The Content Strategy Experts - Scriptorium
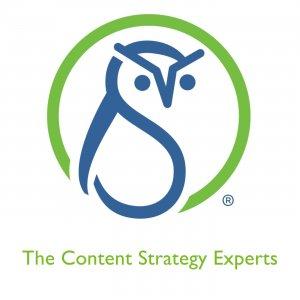
Industry 4.0 (podcast)
In episode 126 of The Content Strategy Experts podcast, Sarah O’Keefe and Stefan Gentz of Adobe discuss Industry 4.0.
Related links:
Twitter handles:
Transcript:
Sarah O’Keefe: Welcome to the Content Strategy Experts podcast brought to you by Scriptorium. Since 1997, Scriptorium has helped companies manage, structure, organize, and distribute content in an efficient way. In this episode, we’ll talk about Industry 4.0 with Stefan Gentz of Adobe. Hi, I’m Sarah O’Keefe. Stephan, welcome tell us a little bit about yourself and your job at Adobe.
Stefan Gentz: Hi Sarah. Yeah, I’m Stefan Gentz and I’m the Senior Worldwide Evangelist for Technical Communication at Adobe. I’m working for Adobe like six years, six and a half years now, almost seven years. And it has been a great journey and it’s a great company to work for. So, I’m happy to look into these topics like Industry 4.0 to drive that forward and help our teams also to get a better understanding for that and develop solutions that the Industry actually needs.
SO: The Technical Communication portfolio at Adobe includes, I’m going to list a few and then I’m going to forget some things and you’ll fill in the rest, right? But it includes FrameMaker RoboHelp, AEM guides which did a CCMS AEM product and what did I forget?
SG: For the Technical Communication part that’s mostly it, RoboHelp is brand new product since 2019, where we completely revamped it. And of course, with the good old workhorse FrameMaker that you can use for structured content and XML editing and DITA authoring, et cetera. And yes, for a couple of years now we have our own DITA CCMS Component Content Management System, which sits in as you said Adobe Experience Manager it’s called Adobe Experience Manager Guides, formerly XML Documentation for Adobe Experience Manager, which was a very long name.
SO: It was.
SG: Yeah.
SO: So, I wanted to ask you about Industry 4.0, it’s a term that I hear a lot in the European market and it seems to be used more there perhaps, especially in Germany, because Germany has so much heavy industry, so much machinery, that kind of thing but when somebody talks to you about Industry 4.0, how do you define Industry 4.0?
SG: Yeah. I mean, these two terms around there’s IoT, the Internet of Things, which is more a north American thing and industry 4.0, which is something that roots deeply in the German industry. And it’s actually not a new term goes back until I think even 2011 when that started. And in 2013, the platform Industry 4.0 was founded by German Industry Associations like Bitcom, VDMA, and ZVEI. And they were coming together to develop further and implement the industry 4.0 idea as part of the high tech strategy of the German government. So, the German government in 2011 was inventing that term industry 4.0 as a future initiative to drive digitalization in the German industry and that what was picked up by these industry associations and then companies like German Telecom, Robert Bosch, Siemens, Festo, SAP, and others joint that platform Industry 4.0 and started to create a framework for that.
And that’s all happening on the platform Industry 4.0, which is indeed very German and very rooted in the German classic manufacturing industry. And that is probably the reason why that term Industry 4.0 is usually heard more in Europe than in North America where the industry is talking more about internet of things but in some way, the same idea and roots into the same concepts, but Industry 4.0 is more about classic manufacturing industries and production processes and what we call the smart factory. And it refers to intelligent networking of machines and processes in the industry with the help of information and communication technology. That’s more an industry thing while IoT is very often also about the end consumer Smart Home and things like that. And that is Smart Home and things like that are not so much in the focus of Industry 4.0 there we really talk about things like smart factories, smart machines that can communicate with each other and where content and data is used in new ways.
SO: Right. So basically, I mean, it sounds as though, Smart Home is internet of things more or less and smart factory, the industrial equivalent is Industry 4.0 to terribly oversimplify.
SG: Yeah. Very simple set. We could put it like that. Yeah.
SO: Yeah. Okay. So, we make a smart factory where we’re going to wave our hands and make a smart factory where everything starts to be interconnected and have some intelligence in terms of what’s going on with all the machines, talking to each other. What does that then mean for? You and I both live in the content world. What does that mean for us? What do, what are the implications of Industry 4.0 of a smart factory for content people?
SG: Well, I recently talked to someone and he said, or actually she said data and content are the new raw material in the Industry. Of course, well in the future also have other raw materials to turn them into products but one important factor that is basically a deciding factor for success or failure is data and content. And when we think about the use of data, data on the production process and the condition of a machine and the product are combined and evaluated by algorithms, by software and data analyzes provides information on how a product can be manufactured more efficiently, like you’re monitoring the production process and then trying to optimize it. But more importantly, it is also the basis for completely new business models and services. For example, let’s think of elevator manufacturer, they can offer their customers. Things like predictive maintenance based on content and data.
The data is maybe produced by the machine, by the motor of the elevator, for example. But that data itself is not useful. It needs to have some context and that context is something that is coming from engineers. And for example, technical writers or engineers, let’s think of a classic manual for an elevator where you have some part about maintenance. And then there’s a table of how often does this elevator need to be maintained and maybe the software needs to be updated, whatever. And this is content that usually is created by human beings. And that is something changing where in the future… For example, elevators can be equipped with sensors that continuously send data about their condition and what to do with that information. That is something that we as human beings, as tech technical writers, for example, put somewhere and classically it’s put in a user manual or in the maintenance manual.
And that then there’s a disconnect between the data and the content and the idea of Industry 4.0 is also to bring this together and have a new way of consuming and using technical content like stuff that is a content that is in a maintenance manual and use that the machine can use that. And there are already examples for that in the German industry. Like there’s a big company that produces big machines for a wood processing. On the one end, you put in a big tree and on the other end of the machine window frame comes out of that machine simply said, and how often this machine needs to be maintained, the machine is actually pulling that data life through an API, from the system where the data content is hosted and the maintenance data is created as XML as data and there’s a maintenance table and in index in one topic and the machine can pull out the information, when is my next maintenance cycle from the data topic that is created by a technical writer.
And that means we also need to think about how we create content and how we offer that content and how we make that content accessible. And if you think about it from a technical writing perspective, traditionally, the idea of technical writing was to explain a complex product or a complex process for a human reader so that the human reader understands how to use the machine or how to use the software or how to use the elevator or whatever, or a service engineer who has to maintain such a machine or product. So, the target audience of content created by technical writers was usually a human being. And in that Industry 4.0 context, and also in the IoT context, we need to think about content, new ways.
We need to create content in ways that it’s consumable by both human beings and machines and that is something where we need to not only from the words and phrasing and how we explain content, but also in terms of attributing content and say, ‘This is content that is for a human reader, one paragraph for the human reader and one paragraph or one table of data for the machine that is going to consume that content to pull out, for example, maintenance cycle data.” And that means we need to approach technical writing in a new way in the future and already today actually, and also need to use technologies that make it possible to implement what we as technical writers produce to implement that into an Industry 4.0 or IoT scenario. Yeah, it’s a complete new way of what we need to do with content that we produce and how we store it, et cetera,
SO: I’m terrified of your wood machine. So I’m going to go back to the elevator cause. So what you’re saying is that you have an elevator and in the Non-industry 4.0 world, you have an elevator and the elevator goes up and down. And after every, let’s say 100 hours of operation, there’s a particular maintenance procedure. You need to go in and lubricate some things or check a belt for wear or something. And by the way, no idea how elevators actually work, so-
SG: Neither…
SO: Yeah, okay. So we have an elevator every 100 hours, there’s something that you should be doing. And so, the implication of Industry 4.0 is that the elevator itself has sensors which count operational time, right? So it would measure, Hey, I’ve hit 100 hours. Yeah. And at the point, and it knows that, or it has what amounts to a clock or a counter inside the system, inside the elevator.
Okay. So it hits a 100 hours and normally at a 100 hours, the dumb elevator, right? It has the sensor, but the dumb elevator just turns on a red light and says, “Hey, hi, you need to do my maintenance.” Right?
SG: Exactly.
SO: And then the maintenance technician shows up and says, “Oh, the red light is on. I have error code 57. Let me go see what that is. Oh, that means I need to go pour oil on this thing over here.” Fine. And presumably they looked up error 57 in the documentation, some horrible PDF that’s like 100 of pages long. And it has error codes for days. And they go in there and under 57 on page 685, they eventually find something about machine oil, but in Industry 4.0, it kicks off that message or that error that says, “I’ve hit a 100 hours. It’s time to do some things.”
And then essentially it has access to the documentation, right? It’s like contact sensitive, help. It just says, “Hey, Stephan, my friend, the mechanic, you need to do this procedure.” Right. You don’t have to look it up. You don’t have to provide that connectivity between the system, the error code or the maintenance code. And then the documentation that explains what that maintenance code is. Now, somebody did the work, right? I mean, to your point, some human being created the content and presumably some other human being built the framework that connects all those error codes to the relevant information.
And then somewhere along the way, we have to display that content in a human readable form so that the service technician can do the procedure. Now, to your point, that doesn’t get into the question of what about automated procedures or the machine automatically going into service mode and I guess servicing itself in some way. So, when I think about this and we look at what we’ve been doing for the past 15, 20 years with topic based content, that seems like the first step in this direction, right? That we have to have individualized units of content that cover these specific procedures so that when the machine says, “I need this service, we can connect. I need this service X, Y, and Z to the relevant instructions.”
SG: Yeah. And Sarah, we can think it even a little bit further. Imagine that it’s not about oil in the elevator, but about a certain part of that elevator that needs to replace every hundred hours of operation time. As you said, classically red light would light up and someone looks at that red light and needs to call the elevator company. You need to send someone there’s a strange red light. And then the service technician comes, sees, “Oh, that’s this red light with this arrow code. Okay. I need to replace that part.” Good. That don’t have that part with me. I need to go drive back into the company and order it in SAP or wherever. After a couple of weeks, it comes back. The part is delivered. He again, needs to go to the elevator, replace the part, et cetera. So it’s a very time consuming and cumbersome process where maybe even the elevator will not be available for a certain amount of time.
And people need to walk the stairs, which could be healthy, but could also be that. And the idea of Industry 4.0 here is that the elevator can look up. For example, by being connected through the internet with the central data center of the elevator company can look up what that error code actually means. And in a list of error codes or whatever could send, for example, a short message or an email or something to the service technician, informing the service technician that this part will needs to be replaced in 20 hours of operation time, predictive maintenance, and when the 100 hours are actually achieved, then the survey technician can already see, “Okay, based on data. So many hours per day, the elevator running probably on August 15, this part will fail and needs to be replaced.”
And then he can also already come to the elevator with the right part and replace it and he already knows, or she already knows that how to replace that part, because that information is already there. It’s already pulled from the technical documentation coming maybe to the iPhone or Android phone or whatever or smart pet that this is the part that you need to re replace. It’s maybe already automatically ordered from the supplier of the replacement part, along with the information, how to replace that part. So when the service technician arrives at the elevator, he or she already knows what to do and what to replace and doesn’t need to go forth and back and then order and then wait for the part to come, et cetera. And that makes the whole process much more efficient and makes it much more stable for the people who use the elevator because the elevator company can take care of such replacements and maintenance things before in German, we say before [foreign language] fallen into the-
SO: Well-
SG: Yeah.
SO: Oh, there’s a terrible lassie joke in there, but we’ll let that slide. So, okay. So let’s say that I work for some an industrial company producing service and maintenance documentation. Now, if my organization has already started an initiative like this, then this is all not new information, but let’s say what about for the people that are in these organizations that at this point are still producing dumb PDFs. I mean, good maintenance instructions potentially, but just in locked up in PDF or locked up in a way that is not interconnected with the systems.
What would be your advice to those people? What are the first steps to start thinking about this? If I’m the tech writer and I know that my company is moving in this direction, doing more service management, predictive maintenance, trying to add some intelligence into my products, then what are the implications for me as a content creator? And what kinds of steps should I be taking proactively to make sure that I’m ready when eventually the director or the VP of something shows up on my doorstep and says, “Guess what? We’re doing Internet of Things, we’re doing Industry 4.0, and we need your content to be ready.” What do I do?
SG: Well, you will not go very far with traditional ways of producing content in Microsoft Word as a long Microsoft word document so what do we basically need is what do we call intelligent content and intelligent content basically is something like structured content XML based where you can add metadata, where you can attributes to the strengths of content that is readable so to say. So you could have attributes on a certain table with maintenance data, like the audience is the technician, or the audience is the machine, and then attribute the rows in the table to certain, to these two certain audiences. And this is something that this additional intelligence on top of the text strings themselves, this is this additional layer of intelligence that you can attach to the content. This is only possible today with XML and this is why Industry 4.0 Scenarios or IOT scenarios are always based on content that is produced in XML.
And one great language to produce XML based content is of course DITA, the Darwin Information Typing Architecture, this language makes it possible to put that in additional intelligence into the content or on top of the content or attached to the content. This is one thing. So, structure content is there’s no discussion about that. If you want to be future ready, if you want to be Industry 4.0 already with your content, you need to work with XML preferably with DITA. And then, you need to also host that content somewhere so that it can be centrally managed, but also centrally consumed and centrally delivered. And that is something where you need a CCMS. You will not be able to achieve that with only RoboHelp or only FrameMaker, but you need a component content management system. And that CCMS also needs to have APIs so that external content consumers can access the content through an API and pull out the information that they need.
And from that CCMS on the other end, you can also deliver that content to what you say, call Omnichannel. So basically the good old PDF yeah still very relevant, but you can also produce push that content into other systems, like let’s say Salesforce or Zendesk or your own help portal or support portal or [inaudible]-
SO: Service management system. Yeah.
SG: Or in some other management system or some machine system where can inject certain informations from the CSMs side. But APIs are a crucial part there with system, without APIs that are accessible from the outside. You will not achieve a lot without APIs. So basically, XML plus CCMS and the CCMS with APIs. These are the things that you definitely need to have as a technology stack to be Industry 4.0 already. And then of course, you need to think about how to create that content, how to write content, how to migrate content legacy data, because you don’t want to start from the scratch with everything, right? You want to migrate that content and have a content suggestion engine where you can push your existing unstructured, non examine content into a CCMS like Adobe Experience Manager Guides and get it migrated into XML and transformed into XML, and then enrich it with these new possibilities that such system offers like attribution of content, metadata, taxonomy, et cetera.
SO: And, we talk about the world being more and more interconnected and more and more interdependent and really, it seems like what you’re describing is a world where the content is an integral part of not just the product talking to it, but the product operations in the sense of the maintenance tech, the service people, all these different people who actually are looking at both the product, our elevator, and also the maintenance and connecting those together in ways that make them better, make the product better, make the product safer in that we have, as you said, predictive maintenance rather than after the fact maintenance and potentially more efficient, right? Because, well, let’s just replace it 98 hours instead of a hundred, instead of waiting for it to stop.
SG: Yeah. And it’s also the personalization of that content. If you think of a car, let’s say you’re a car manufacturer and you have a model of your car, but this model is in hundreds if not thousands of variants in the market with this seen on light or with this other light, or with all kinds of parts in the car that you can customize as a customer. But when you buy that car, traditionally, you get that super big bot manual where all possible variants are described.
And of course not only that’s raise of paper and not good for the environment. It’s also very unfriendly for the customer who wants to access information because the customer doesn’t care about all the variants. The customer cares about that one configuration that he or she has bought this kind of configuration and having a personalized bot manual for your car in two variants, even one in the screen, in the car, and one in the human machine interface there, and one in the maybe printed manual for security, backup reasons, and this kind of personalization of content and maybe even having two different ways of representing the content, maybe in the technical manual that is shipped with the car, it’s legally approved proper content.
And maybe in the onscreen, in the human machine interface, in the car, in the display, it’s a completely different content. Maybe it’s like, “Hey, Sarah, the oil in your car needs to re be replaced or whatever.” And this, this, this kind of personalization of content for that you also need a CCMS. And to put that a step further, personally, I think in the future, we will approach content in a new way from delivering content to hosting content. In the past, we were always thinking about the output channels. We were always thinking about how can we create a nice looking PDF or how can we create nice looking web help portals and you also talked a little bit about that in your presentation at DITAWORLD, about content as a service.
I think in the future, companies will much stronger focus on having a central place for their content a CCMS and then from there, the content is just pulled or delivered as necessary and needed by the different scenarios where their products are used in, and this idea of not thinking about the output, but thinking about how to host the content and in which format to host the content, et cetera, that is some a new way of thinking about content. And I think this is where the future is going to that companies are more and more focusing on centralizing that content in a platform that can be used by all kinds of content consumers.
SO: And we’re already seeing some of this in the projects that we’re doing exactly that model and in a really interesting move away from focusing on delivery endpoints and rather focusing on, I guess, enablement and making content available but not necessarily being a 100% focused on where it might be going. I mean, of course delivery is important, but it’s more the idea that we want to make sure this content is set up in such a way that it can accommodate today’s requirements, but other requirements, the requirements we don’t know about, you know the future stuff. That’s a really interesting, I think, challenge to the people that are listening. And so, I think I’m going to wrap it up there’s an enormous amount of, I think, food for thought in here. So, Stefan, thank you so much for coming in and sharing all this wisdom with us and all these exciting new possibilities for our content.
SG: You’re welcome.
SO: And with that, thank you for listening to the Content Strategy Experts podcast brought to you by Scriptorium. For more information, visit scriptorium.com or check the show notes for relevant links.
The post Industry 4.0 (podcast) appeared first on Scriptorium.