Bluefield 30 in 30
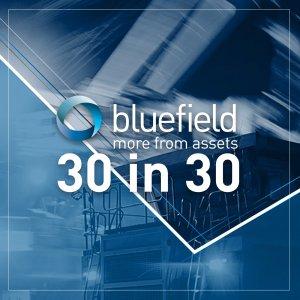
Taking a Systematic Approach to Ouput Improvement with Dick Pettigrew
Our guest today has been at the forefront of operational reliability improvement in various industries around the world for many years. Dick Pettigrew joins us today, sharing from his extensive experience as we discuss his integrated approach to design, maintenance and operations.
With a degree in Chemical Engineering and a love for machinery, Dick started out working in process engineering support. As he progressed into design and project management, Dick began to observe fundamental issues surrounding the approach to reliability improvement and maintenance operations. In this episode, Dick shares about his career journey, some of the major learnings of his experience thus far and his holistic approach to problem solving on site, not just within maintenance reliability.
We discuss how output improvement is more valuable than maintenance cost reductions, how there’s a difference between the problem and the cause and that taking a broadened approach from reliability improvement into total manufacturing improvement is what will create sustainable improvements.
Dick talks us through some of his experiences improving outcomes and how the assessment process itself isn’t as important as the commitment from the leadership team and people on site to implement the improvements. We discuss the importance of establishing a good culture and how working with people directly on the floor brings the plant up to standard and restores pride in the operation.
Dick has spent a lot of time creating measurement systems and writing books to take a systematic approach to output improvement. He discusses his asset utilisation model and how combining this with the theory of constraints enabled him to improve the output of many plants he’s been involved in.
We discuss using RCM not as a project but as a way of thinking about plant reliability and how it can make a real difference when utilised this way. Dick shares his advice to aspiring maintenance and operational managers, honing in on the vital component of the human aspect.
TOPICS DISCUSSED AND WHERE TO FIND THEM
[2:00]: How Dick started out as a chemical engineer and worked in process engineering support, moving into design and project management
[3:30]: How Dick became frustrated by the fact that the chemical plants he built weren’t being operated and maintained in the way they were intended to and that they needed an integrated approach to design, maintenance and operations
[4:30]: As he moved into maintenance management, Dick discovered there wasn’t a logical approach or codified practises as there were in design
[6:00]: How Dick was asked by the vice president of a large plant to discover ways to improve the maintenance and how they hired a maintenance consultant, wrote a book, developed a bench-marking process and performed many assessments on their plants
[8:00]: How all problems flow down to maintenance but they developed a measurement system and philosophy that went back to the source of the problem.
[10:30]: Combining the asset utilization model with the theory of constraints enabled them to start improving the output of their plants
[11:20]: How output improvement is 5-10 times more valuable than maintenance cost reductions
[12:30]: The opportunities that exist within the unscheduled operational downtime
[14:00]: How Dick retired from the chemical business in 2003 and established his own consulting business which led him to work with an Australian mining company. He rewrote the chemical plant assessment book into mining terms.
[16:45]: How they implemented a successful process where the site took ownership for the outcomes of the assessment
[18:50]: Relialitics Equipment Condition Supervisor software
[21:00]: The assessment process itself isn’t as important as the commitment from the leadership team and people on site to implement the improvement
[22:16]: How any errors should be classed as unscheduled downtime, regardless of the source of the problem because there’s a difference between the problem and the cause.
[23:00]: How often maintenance and operations are at odds but working together is essential
[25:00]: A successful plant that changed to become much more reliable, largely due to the local management and their focus on teamwork.
[27:15]: How the state and size of the storeroom is a good indicator of the success of the plant
[28:30]: How the commitment from local management and the people on site is what really makes change possible
[32:00]: How senior managers understand how difficult improvement can be and have been more understanding of the process than Dick himself
[34:20]: How the culture of a place with the right people, attitudes and standards create sustainability
[39:00]: Working directly on the floor in clean and tag operations brings the plant up to standard and restores pride in the operation
[42:10]: planning and scheduling is there to improve the efficiency of scheduled maintenance downtime but doesn’t actually improve reliability if the quality of the work isn’t there
[43:30]: Dick’s advice to aspiring maintenance and operational managers - the human aspect has to be at the forefront of your thinking and the technical aspects of RCM, importantly addressing functional requirements not the machine itself
How you think about failures and manage them through the RCM mentality
BOOKS MENTIONED:
The Goal by Eliyahu M. Goldratt
Reliability-Centered Management by John Moubray
Website: https://www.bluefield.com.au/en/