The Uptime Wind Energy Podcast
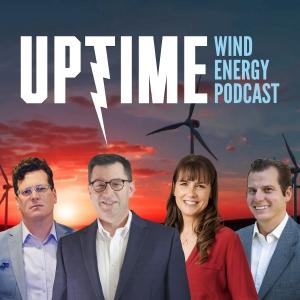
Bonus: EchoBolt – A Revolution in Bolt Upkeep
In this bonus episode of the Uptime Wind Energy Podcast, hosts Allen Hall and Joel Saxum delve into the complexities of bolt connections in the wind industry with Pete Andrews, the Managing Director of the UK-based company EchoBolt. With bolted connections being a key area undergoing significant changes in terms of efficiency and cost-effectiveness, EchoBolt has introduced a new approach to bolt inspections that is faster and more accurate, transforming the way the wind industry thinks about bolts. The discussion covers the common issues facing bolted connections and how EchoBolt helps customers focus on problem joints.
Visit Pardalote Consulting at https://www.pardaloteconsulting.com
Wind Power Lab – https://windpowerlab.com
Weather Guard Lightning Tech – www.weatherguardwind.com
Intelstor – https://www.intelstor.com
EchoBolt – https://www.echobolt.co.uk
Sign up now for Uptime Tech News, our weekly email update on all things wind technology. This episode is sponsored by Weather Guard Lightning Tech. Learn more about Weather Guard’s StrikeTape Wind Turbine LPS retrofit. Follow the show on Facebook, YouTube, Twitter, Linkedin and visit Weather Guard on the web. And subscribe to Rosemary Barnes’ YouTube channel here. Have a question we can answer on the show? Email us!
EchoBolt
Allen Hall: Welcome to an exciting bonus edition of the Uptime Wind Energy Podcast, where we explore the latest innovations in the wind industry. I’m your host Allen Hall, along with my co-host Joel Saxum, and today we have a game changing topic that’s sure to spark your interest. As we know, the wind industry is relentlessly striving for greater efficiency and cost effectiveness, and one of the key areas that is undergoing significant changes is the bolted connections.
Today we have the pleasure of hosting Pete Andrews, managing director at EchoBolt, the UK based company that is revolutionizing bolt inspections instead of traditional re-tensioning methods. Echobolt has introduced a faster and more accurate approach that has the potential to transform the way the wind industry thinks about bolts.
So join us as we delve deeper into the complexities of bolted connections in in wind, and discover the cutting edge technology that EchoBolt is bringing to the. Pete, welcome to the program
Pete Andrews: Hi, Allen. Thank you very much. It’s good to be here.
Allen Hall: So one of the, the concerns out in the industry at the moment is what is happening with all these bolted connections and some of the problems we’re seeing in bolted connections, in particular in the United States.
We’re seeing a lot of issues with blade bolts and foundation bolts. Are you seeing some of the same things over in Europe?
Pete Andrews: Yeah, I think so. I think it’s really a story of two halves with bolted connections on wind turbines. Either your bolts are, are behaving in a static manner and a fine, and you can almost leave them alone for the life of the asset, or you have persistent problems and it’s exactly the same story for us.
It’s blade to blade bearing connections. Sometimes foundations where. Degradation of concrete, et cetera. And so we are really helping customers focus in on those problem joints and hopefully engineer ways and investigate and. Help ’em solve the issues that they’re having. A question for you, Pete.
Joel Saxum: So when we talk bolted connections, right on the wind turbine, we’re ma mainly talking tower to foundation.
We’re talking tower section to tower section and usually tower to bolts, or I mean tower to blades. Sorry, tower to bolts. Is, is, yeah, that’s gonna happen. But to the blades. So do you run it, when you talk about, like, there, it’s a dichotomy, right? It’s either you’re having problems or you’re just beautiful and everything chugs along in its business as usual.
When you guys are out there and you don’t have to name any, cuz we don’t want to, we don’t want to drag anybody through the mud. Too bad, but are there certain. Kind of like, so we deal with blades and there’s certain models of blades that we know like, oh, if someone calls me and says they have a lightning issue, like, ooh, what kind of blades you got?
You know, and, and we kind of know, or hey, we’re having, you know, root cracks, what kind of blades you got? Ooh, yeah. We know. So is there certain tower section models and, and, you know, foundation designs or Blade, you know, root sections that you guys know like, oh, if someone calls and says, Hey, we’ve got this, oh yeah, we’ve seen that problem before.
EchoBolt to the rescue, we’ve got a solution for that.
Pete Andrews: It’s often the case that when you are, you’ve got issues in the operations phase. The root cause stems from the construction and installation and, and very often it’s when joints have been toed in a relatively uncontrolled manner that the. Bolt to bolt variability and the initial preload wasn’t where the design intended.
The kind of rule of bolted connections is whatever you think your tension or preload is, you’ve got less, and that’s just the way it is, particularly if you’ve talked the joints. So where we’ve got long, thin blade studs that have been torque tightened instead of stretch tensioned. Often they haven’t achieved the preload, that that would’ve been desirable during installation.
And the same is true with the foundation. So early on in the offshore industry in Europe, a lot of the mono pile to transition piece foundation connections were talked and they’re very large M 72 bolts. And. We’ve seen multiple times that those joints haven’t achieved the preload and have therefore been problematic in the operational phase.
So I think if, if you came to me and said, I’m having issues with my With a particular connection. The first thing would be, what are your installation QA records? How, how was it installed? And probably, let’s say 90% of the time, that’s where your, your issue lies. Okay.
Joel Saxum: That makes sense. Yeah. So, and, and I guess in that, man, if you had a, now I’m thinking I’m putting on like, My construction hat.
So if I was on a site and I had a hundred towers and I had an issue with one of ’em right away, and I looked at QA records and I would say like, okay, give me the QA records from that team or that team lead who was working on these, and let’s go check all of those within this wind farm, because that might be somewhere where you could.
You know, as an ar, as as a armchair root cause analysis study. Say like, all right, if we’re having some issues with this one, we maybe be having issues with other ones that are done by the same, the same group of people.
Pete Andrews: It’s certainly the case that you could end it with uncalibrated equipment so you get a incorrect hydraulic pressure, for example.
Or corners can be cut where you have multi-stage processes. You know, you’re supposed to say, talk to 50%, 75%, a hundred. And people just bypass that. But the, the main thing I’d say is if you’re thinking about when you’re installing turbines, do a percentage where you, you prove the preload from your installation process, prove to yourself that the process you’re following will deliver the correct output and it, it, it only need.
You are on a large site, let’s say a hundred turbines, five or 10%, you just check and verify. But I’d say it’s, it’s more the procedure more often than an individual team or piece of equipment that that’s. Could be improved.
Allen Hall: So peak bolts stretch when they’re tightened. That’s the whole point, right?
Is that we, they go through a process of the 50%, 75%, a hundred percent on tensioning, because the bolts actually physically stretch, and that’s where echo bolts steps in. Because, and I, I want you to walk through your technology here, but essentially you’re relying on the fact that as bolts are tensioned, they get longer.
So can you walk us through what Echo Bolt does with that knowledge? Yeah.
Pete Andrews: So perhaps if I just take a step back to say, what does the industry currently do in order to maintain the integrity of these bolted joints? And it’s typically a, a check tightening approach, so, Technicians would go out and maybe reti 10% of the bolts on each turbine each year or a hundred percent every five years, and see effectively if the nut moves, if it, and if it doesn’t, the bolts deemed.
Okay. There are a couple of issues with that approach. First off is it takes a long time and it’s a lot of heavy hydraulic equipment, a lot of manual handling, a lot of. Technician time and turbine downtime. So it costs a lot of money. Our sort of rule of thumb is that in Europe it probably costs you something in the region of a million euros per installed, gigawatts per year just to go and routinely tighten bolts.
It’s a really significant cost. It’s probably the, the single biggest maintenance activity that’s done in wind. So obviously that’s a problem. The second issue is you aren’t proving the load in the bolt. You are just validating if the nut tighten if the nut turns and if the nut seized that it’s not gonna turn whether or not the bolt is tight.
And so we’ve seen operators who have been operating wind turbines tighten the bolts in this way. Thinking everything’s fine, but actually the nu just corroded to the bolt and they don’t have the load that they had. So there are some really fundamental flaws in what we’re doing as a status quo. And you’re absolutely right, Allen.
So what we do at Echo Bolt is, is look to validate the stretch or the elongation of the bolt. So we try and prove that the bolt has got the load in. Directly rather than infer through a amount of turn. And we use primarily use ultrasonic measurement techniques. So it’s really an extension of a non-destructive testing method where traditionally you might use it for thickness checking on the boiler plate.
It’s that sort of Sending out a, a pulse of energy. Measuring the time for it to return to, to measure the thickness of a material is what we’re using on bolts. And it can be extremely accurate. So we can sort of weak can measure to, let’s say half the width of a hair in terms of our level of. The bolts on the wind turbines are really, can be very significant, so the bolts can be half a meter long and we’ll stretch by over a, over a millimeter so we can be very accurate in determining whether or not bolts of lost load or and are operating at the load they should be.
The major advantage of this is that you can, you can monitor a sample of the site. You, you don’t have to go and measure every single bolt. If you can prove that 10 or 15% of your turbines are healthy with a good margin, then that finding is, you can extrapolate that finding across the whole park. So rather than revisiting every turbine every year to.
Do 10% of the bolts, you can really be far more targeted and treat this as a condition-based inspection technique and only widen the sample if, if you start seeing issues.
Allen Hall: So instead of basically pulling on bolts to tension them to usually 90% as the number I hear quite a bit, you can actually. Put one of your sensors on there and say, yes, this bolt is, is intentioned because we know
Pete Andrews: how long it is.
Yeah, that’s exactly right. So it, it’s just a small handheld device very quick to deploy. We sort of probably in the order of 10 seconds per bolt to do a measurement. So it’s kind of you’re carrying around something that almost fits in your pocket rather than trying to lift lots of equipment, hydraulic hoses, pump.
Tensioners, et cetera, all over the turbines. So it’s, yeah, it’s a really really efficient way of achieving a, a good inspection result. Yeah,
Joel Saxum: man, I’m thinking especially for guys going up tower, like it’s easy to, it’s easy to back a truck up to the foundation of the tur turbine and checks and bolts.
But when you gotta start in up tower and you’re haul hauling hydraulic hoses, equipment kits, pumps all this stuff up, that sucks. So if you can go up there with just a, a little handheld device and, you know, strapped on in the nice carabiner clip so you, you’re not dropping, you know, you’re avoiding. The dropped object syndrome, like, man, that’s, that’s great.
That’s that’s a, a game changer for the industry.
Pete Andrews: Particularly when you start to get into looking at blade blade bolts and you need to access the hub and you’re kind of often on the smaller onshore machines, it might be an external access, so you’re over the nose cone trying to get. Each time you need to turn the shaft, pitch the blades, you’re in and out and in and out.
It can be a very laborious process and sort of anything that can, that you can do to streamline that really pays dividends in terms of the turbine downtime.
Allen Hall: So you’re, you’re saving about 90% of the time. At least 90% of the time, if you’re checking blade bolts, tower bolts, it’s, that has to be a relatively fast process com compared to retentioning, all those bolts and all, and like Joel was saying, all the equipment hauled up and down the tower.
That’s a huge financial savings.
Pete Andrews: Yeah. I mean it, it’s a much quicker inspection and in general, we’re inspecting far fewer turbines, so you’re absolutely right. We would say we would expect. Take the turban off for less than 10% of the time of your kind of status quo. And it’s fewer technician days. So, you know, can be a really substantial saving for For operators of wind assets.
So walk
Allen Hall: us through what this echo Bolt solution looks like. If I’m a customer and I have, I’m in Oklahoma, I have a hundred turbines out there, and I, I know it’s been a couple of years, I know I have some bolting issues. I call you. What does that look like? Walk me through that process.
Pete Andrews: So, I suppose the first thing is to understand whether or not you are having problems or you suspect that you have a, a problem joint.
If the answer is no, then you are into sort of, okay, what can we do to replace our scheduled retarding activity? And the alt offering there is either we come and deliver a service for you, we send our technicians to inspect your site, or we train up your team. Training course would typically be two days.
And we could lease or sell you the kit. And what we would do is then put in place with you a kind of recommendation how many turbines we should inspect. So let’s say you’ve got a hundred turbines, we’re gonna inspect 15% and do 15. We typically aim to, to complete a turbine a day. So, For most onshore turbines, it’s probably two technicians can expect the whole, all the bolts in a turbine in a day.
It’s probably one in the hub, one doing everything else. So we would then aim for your hundred turbine sites. To have inspected all the bolts in 15 turbines in 15 days. A set a baseline that we can monitor from going forward, and then year on year, inspect those same 15 turbines. As I said at the start, for the majority of joints in wind, they’re really stable.
They aren’t losing load, and you’ll find very quickly that you build up a trend and can be confident that the. Preload is maintained and you’re not gonna have any problems. The flip side is if you do have a problem connection, like a blade to blade bearing where you’re finding failed studs and you are having to periodically go in and replace and repair, damage, et cetera, what we would do there is something a bit more investigative.
So we would go with you and look at what’s the existing preload. What’s the maximum load we could put in the bolt safely? What’s your installation method? Can we improve your tightening process to add preload to the joint safely? Cuz the majority of failures are fatigue failures where you, you don’t have enough load.
The connection is opening and the bolts seeing far greater dynamic load than it’s designed for, so it fails prematurely. So the kind of number one remedy is to try and raise the preload in the joint to try and guard against that fatigue failure. So it’s slightly different if, if you have a, a problem that you’re trying to engineer out, we end up in a bit more of an investigative.
Mode, but for let’s say 90, 95% of the connections out there, we would just replace your annual. I’m gonna Reid one in every 10 bolts to we’ll re, we’ll ultrasonically, inspect all the bolts on 10%
Joel Saxum: of the site. One of the use cases I’m seeing here, Pete, is that we’re starting to see a lot of acquisitions, mergers, and acquisitions in the us.
Company X, Y, Z is buying company ABS assets. And it’s, and it’s like every time we turn around it’s like, oh, so-and-so sold. And some of ’em are huge, right? Some so-and-so sold 4 billion in assets. Oh, this wind farm was bought by these people. This wind farm was bought by these people. So when you have this, this juggle of record keeping and who’s responsible in o and m activities, right?
Because it might. Commissioning day, installation contractor hands over to oem even though an asset owner owns it. So OEM might maintain it for five years or 10 years or whatever, but then that might pass to. The asset owner now doing the, the o and m activities themselves. And then two years after that, they might sell the whole thing to someone else.
So now there’s like, the chain of custody is three, four different companies long that may not have involved in the project for 10 years. So as a asset as the purchaser of that asset, it’s like, how do, how do you trust the record keeping and all these things that come in. So it might be, it might be really smart for someone that’s acquiring a wind farm to say, you know, Let’s get echo bolt in here.
Let’s check all these to make sure that we are, you know, we’re running this risk free, or, you know, controlling a risk as, as good as we can. Because you just never know what could happen because you, you know, you can look through the records all you want, but you might find you’re, you’re going to find gaps.
I know that because we’re requesting records all the time for, for cases, and you just don’t get stuff. So I think that that’s a huge use case that anybody out there buying a wind. I should look into this. In, in, in my mind, that’s the smart thing to do, right? It’s like going over a car when you first buy a used car and checking all the lug nuts,
Pete Andrews: you’re absolutely right that there are some sort of high value or high high benefits moments of time in an asset’s life.
There’s obviously installation. We’ve spoken about that. Using this as an installation QA tool can be really valuable. There’s the period where your OEM is probably servicing your turbine and you’ve got a warranty, so before your warranty ends is another high value time. Make sure you kind of can, can prove that you don’t have serial defects, et cetera out there in your.
Any of those changes in ownership as you said. But then the other one that we’re increasingly seeing in Europe is life extension. So we’re getting to year 20, year 25 operators are thinking, how do I, how do I give myself confidence that these assets are safe to continue to operate? And one of the ways we can do that is help them in the few.
Prior to build up a trend to say, okay, we know these joints have been operating in a good envelope and that they’re stable. And so the design conservatism that was built in on day one, we are happy that, that that can be reduced. And it’s, you know, a similar way to how people might do structural fatigue.
Monitoring over time to try and prove that they can extend that asset’s life. We can do the same thing with the bolts. And so, you know, there are these key interventions that you can make at strategic points in, in the life of the site. And what I’d always say is that a few years trend is so much more valuable than a single data point.
So you can get a data point and say, yes, we know the load in this bolt, but if you know that it’s going down versus. Stable or going up, which is unlikely. That’s a more useful piece of information. So you always wanna think two or three years out from these key moments and sort of plan how you’re going to address them.
Allen Hall: Pete, one of the things we like to talk about is the customer experience. And I, I imagine the customer experience with Ebot has been really good because you’re actually saving them. A bunch of time and money, but also giving them peace of mind.
Pete Andrews: Yeah, it’s been an interesting journey for us because obviously we’re quite a new company.
I guess there is some nervousness about trialing a new technology with a relatively unknown entity. So I suppose our, our customer journey has often been to pilot the technology. At a small scale, but I think almost every pilot we’ve done has led to a, a wider sitewide or fleet wide deployment. So it’s sort of really good feedback for us that customers are coming back.
So that’s, that’s the first thing. But yeah, the sort of typical interaction, as I sort of said, it’s, it, it’s one of two things. We’re either investigating a problem and then it’s a bit. Organic we’re, look, we’re looking at different solutions and different technologies and sort of coming together to find a way forward, or we’re just doing a direct replacement of a check tightening philosophy.
I think in that latter case, we’ve been able to show customers year on year. Bulk preload isn’t changing. They’ve been able to make decisions to drop. Bulk re tightening campaigns. So say probably the first customer we did was an offshore foundation connection. They’ve got over five years of ultrasonic measurement data, but in year five, they had to do a hun They would’ve had to do a hundred percent Reid of all of the joints.
So it’s a over a hundred turbines. These are confined space entry. Big attention. As you know, the attention at tool weighs over a hundred kilos, so it’s a huge effort. It, it would’ve been millions of euros of cost to do a hundred percent of those bolts re tightening. But with five years of data, we were able to show there’s been no change in preload, then there’s nothing to gain by re tightening those bolts and they’ve eliminated that.
That step and save that cost. And that’s sort of the story we’re seeing. Increasingly as we do different joints, different areas of the turbine, the, you know, the vast majority of cases, you can save over 90% of that. Million euros per gigawatt that you are currently spending. So hopefully in general, our, our customers are quite pleased to have engaged us.
Yeah,
Allen Hall: I, I bet they are really pleased to, because it’s all about controlling costs right now and making sure your turbines are operating at peak efficiency. The Echo Bolt story is really amazing, Pete. So Pete, how, how do people contact you? How do they reach out to Echo Bolt? Yes,
Pete Andrews: there’s a few ways. We are active on LinkedIn and you can find me direct and my colleagues probably the simplest ways.
Our website, which is ww dot echo bolt.co. And from the website you can get some case studies, see what we’re about, and there’s links to get in touch on there. But yeah, I’d just say if your audience is interested in the topic, would like to learn more or like to understand what’s involved in doing this sort of inspection.
Please reach out and we are always happy to speak to people. Yeah. Pete, it’s
Allen Hall: been great having you on the podcast. I’ve wanted to talk to you and learn about ult for at least the last year, so I’m finally glad to have you on the podcast. So Pete, thanks so much for being on. We look forward to hearing
Pete Andrews: more from Ult.
Thanks, Allen. Thanks, Joel. It’s good meeting you both.