The Uptime Wind Energy Podcast
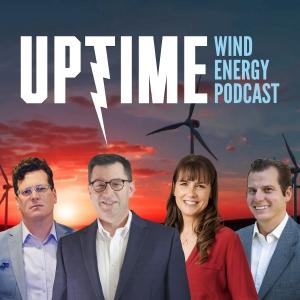
NSK’s Super-TF Main Bearing Solution
You may have missed this fantastic with Loren Walton from NSK, so we’re sharing it again. He discusses the challenges of main shaft bearing failures in wind turbines and NSK’s Super-TF bearing technology as a durable solution. Loren also covers the limitations of previous diamond-like carbon coatings and how NSK’s advanced heat-treated steel can improve turbine longevity.
Fill out our Uptime listener survey and enter to win an Uptime mug!
Sign up now for Uptime Tech News, our weekly email update on all things wind technology. This episode is sponsored by Weather Guard Lightning Tech. Learn more about Weather Guard’s StrikeTape Wind Turbine LPS retrofit. Follow the show on Facebook, YouTube, Twitter, Linkedin and visit Weather Guard on the web. And subscribe to Rosemary Barnes’ YouTube channel here. Have a question we can answer on the show? Email us!
Allen Hall: With modern wind turbines growing larger and main shaft bearings failing prematurely. The industry needs innovative solutions rather than relying on yesterday’s technology. This week we speak with Loren Walton, manager of corporate accounts at NSK. NSK has developed super tough bearing technology, a special heat treated steel that creates a significantly harder surface without coatings delivering long lifespans and eliminating catastrophic failures in today’s larger wind turbines.
Welcome to Uptime Spotlight, shining Light on Wind. Energy’s brightest innovators. This is the progress powering tomorrow.
Allen Hall: Loren, welcome to the show. Thanks for having me. Appreciate your time today. Loren, we brought you in the program because you’re an expert in bearings. You’re with NSK, A lot of knowledge, a lot of history there. First, I want to ask a real simple question because we’ve run into operators all across the United States and the world.
Generally speaking, we just got back from Australia who are having problems with main shaft bearings. And maybe the first thing to do here is to describe what some of the problems are that operators are facing with the traditional main shaft bearings. Yeah. So
Loren Walton: traditionally what we were saying was a whole lot of, I guess I’ll say combined loading, right? So it’s a, radio load that is, up and down and some axial thrust that’s coming in from the wind shear, right? So combining the weight of the main shaft, which is you’re taking up from that radio load with that wind shear. So then you end up having some combined loading where.
The downed wind row is seeing a little bit more of load share than the upwind row. That’s getting through the lubricant regime, which is then creating some micro welding and shearing, any amount of metal, any steel. When it’s created, it’s going to have some disparities. I use my fingers as the disparities, right?
So your roller, your raceway, or your raceway, your roller. There’s gonna be some welding and shearing that happens when that is under high pressure. And so your lubricant is supposed to create a little bit of a gap between those. When you don’t have that gap you end up with the welding and shearing, you end up with what we call peeling damage, and then that peeling basically goes over and over again, and you start having high levels of debris.
Inside of the system. And then once that debris starts going all bets are off, right? ’cause you can’t really even model debris very linearly. It just goes into additional sping and then you end up, if you keep letting it run, you end up with a through crack inside of one of your components, which is typically your inner ring.
’cause it’s press fit on the shaft.
Joel Saxum: And a important concept here as well is because main bearings are basically a sealed lubricant system. There isn’t filters on these, right? So like when you start to get debris moving around in the system, it stays there. It just, it’s not oh, let’s go change oil on this thing.
And we remove the debris, we put a new filter on it, we’re good to go. It’s not, it’s just, it’s in that system now. If it, because it’s a closed loop basically, right? Correct. Yeah. So the grease shift is in there,
Loren Walton: there is an opportunity for you to have, replenishment, right? So you can put new grease in so that old grease comes out.
But even then, you’re reliant on gravity and whatever you can get out of the system. You’re hoping that as you put new grease in, old grease comes out. But depending on how long you’ve been running, it is very possible too that you might end up putting new grease in and new grease out, right?
Because the old grease is so stuck in there. Is now hard to move. It’s very difficult to get that old grease to actually come out. So depending on, if you have maybe a auto lube system or something like that, it might be, you might be running that grease a little bit more consistently.
Otherwise, yeah. You’re stuck with what you’re stuck with once that debris gets going.
Allen Hall: So what you’re saying is as the weight of the shaft and the rotors, everything has gone up on basically two and a half megawatts seems to be that critical area. And above that, depending upon the bearing design, the coatings or the finishes combined with the lubricants, you can actually, or what is happening is we’re micro welding the bearings together because of the weight and the, just the the friction that’s between those two things that.
I don’t think anybody from the technical side realizes it’s happening. It’s not something you think about in a bearing. That gets me into the next question of obviously the bearing manufacturers try to treat the bearings some way to prevent that from happening. It seems like diamond, like carbon coatings were the solution a couple of years ago.
Why was that chosen? Why did that thought process happen? Is that something that was successful previously on smaller turbines and was this implemented on the larger turbines or what was the engineering behind that?
Loren Walton: Yeah, so I started my career in the when generation space in bearings somewhere around 2011.
And at that time, that was when. We were moving from the kilowatt class to the megawatt class turbines. And that was when we first started seeing a whole lot of main shaft bearing problems. And it is all the stuff that I just described, right? The micro welding the micro welding, macro micro pitting, leading the macro pitting, leading the sping, all that stuff, right?
So that was something that was very prominent once you started going from that kilowatt class to that megawatt class and to combat that. DLC was introduced and the thought there was you have a dissimilar material. So what I just described is that, again, I’ll bring my disparities back that micro welding happening, that welding and shearing.
That only happens because you have two of the same like materials. That doesn’t happen if you have a dissimilar material. So DLC di like carving. So what you have is an amorphous tsin carbide that you adhere to the surface of one of those components. So in this case, the roller is what you adhere, the amorphous tsin carbide too.
So that was a game changer. That was huge, right? We went from a few years of life, maybe on average three to five. To I remember seeing a report where A DOC bearing came out after 10 years and still looked beautiful. It was, sorry I like bearing, so I use terminology like beautiful, right?
That I don’t know if that I caught myself after I said the word beautiful for bearing, but that’s just, bear with me. So when we were doing inspections on some turbines that were greater than two megawatt we found. Some abnormalities, we’ll say, in some of our inspections, we didn’t expect to see certain things that we started to see.
We started to see more issues on the inner ring instead of the outer ring, we started to see more issues on rollers than we had seen before. And these were on coating rollers, right? So somebody had already gone to the solution of DLC because it had worked before. And in this case, the customer we were working with.
They actually shortened their life. They went from four years of operation to two years of operation on average when they were using a product that had the coating on it. So again, an abnormality, something that we weren’t used to seeing. So we did all of our investigations, all of the inspections that we normally run through.
We saw that there was actually damage to the DLC. There was the DOC was being harmed. We saw that there was also subsurface wide edge area, wide edge cracking that was also in, in the inner ring and in the rollers. So then we saw that when you compare the uncoated to the coated, the once the DOC was harmed, now you have actually an accelerant to failure.
It. It wasn’t that the DOC was wrong, there was nothing wrong with the DOC. But once it was harmed, you had an accelerant to failure. So instead of it lasting about four years, you’re saying it lasted two years.
Joel Saxum: When you have starting to have a failure with DLC, what are the things that an operator should be looking for, whether it’s a, the DLC ones, because they’re very common right now.
The, in the say the US fleet, there is a ton of DLC coded bearings out there. What are things that an operator should be looking for to see a failure before it turns into a really big problem?
Loren Walton: Yeah, so you’ll primarily see some amount of vibration signatures in your rollers is what I’ve understood from some of the people that I’ve talked to.
It’s really hard to see though, I think. I think that is still getting, like people are still getting better and better at identifying it. Unfortunately, in a lot of cases, what you have to do is see. If you have to look backward on your vibration to see, okay, this was the point because in a number of cases, you might look on Monday, let’s say you see it on vibration, you go do a physical inspection and the rollers look fine.
Finding damage to DOC is not typically something that you can easily catch with the eye. When you’re doing a physical inspection, you’re limited on how many rollers you can check. You’re limited on. What you can actually see. There’s strong limitations there. I don’t fault anyone, if you’re, if you end up with a bearing that blows up because you had a catastrophic roller failure, that isn’t usually something that you can quickly catch unless have learned what the signature looks like from your vibration.
For us, the way we see it is a little, we cheat, right? We have a scanning electron microscope. Where we can see the damage, we can see it almost looks like fractured glass. If you can think of when maybe something hits your windshield and it shatters, right? It looks like that for us under the microscope.
So we can see the damage to the DLC, we can see where there’s maybe some sort of a slit or something like that on the coating. So that’s easy for us to find because we’re. Checking it after it’s already out.
Joel Saxum: There was a certain time, right? It went from the kilowatt class, then we started putting DLC in and then we got a little bit bigger, and then the DLC started to fail.
In between that one and two megawatt class, it worked really well. And maybe that’s the, is it the weight of the rotors or like why did it, why is it starting DLC starting to fail now in these larger rotors, in your opinion?
Loren Walton: For as a bearing manufacturer? We have to adjust to whatever is thrown our way, right?
So I, I don’t get to change anything about the application. I am told this is the application, this is what’s failing. Make it better, please. So that’s the constraint that I’m left. You play the car as you do, right? I can’t ask for a reshow. There’s a lot of investigation that’s happening.
I think that there’s a number of different. Things that are happening. I think people were looking for one smoking gun, but I think we’re more so standing in front of a brigade. I don’t think that there is one. I think there’s a bunch of them. That there’s things like, as the turbine gets larger now, the angles are changing on what is, what was the plane of where the bearing was sitting.
The angles are now changing. You have the aspect of people are seeing that there’s more current that’s going through that, that they weren’t finding before. But even you can’t discount the part of the rotor size today. I think that there is still a multitude of different. Problems that we’re addressing, but the biggest one that I see is that we know that the DLC is being harmed.
So we have to address that because that is the biggest, known right now. I think we have to be willing to change what was the mindset before that. DLC is the solution to everything. And we have to change that to, we have to come up with solutions that are agnostic to the coating that are just.
Able to still combat that peeling damage without needing the coating to be the way to to solve it.
Allen Hall: Yeah, that’s a really interesting way to look at it. At some point you just go, it doesn’t matter why it’s failing. We need to move on to some other technology and. NSK has a lot of bearing knowledge and treatments, and the one I’ve seen for main bearings more recent, most recently is what you guys call super tough.
It’s not a coating, it’s a heat treatment, but it’s unique. Can you describe what that treatment is and why it is so effective in these two megawatt machines?
Loren Walton: So super tough is a medium carbon base steel with varying alloy elements that gives it some different properties and then it’s heat treated.
It’s a cargo nitrite, heat treatment that then leaves the surface significantly hard while having a a mediumly softer core. That’s a bunch of words. I’ll go into a little bit more of what that means. There’s different parts of why that is important, right? So we talked about peeling damage, we talked about the disparity contacts.
We talked about some of that already. The important thing to think through on that is if you look at the matrix of the skin of a steel component, they’re made up of something called carbides. Carbides are basically the hard parts that the bearing runs on. If you have those carbides organized in a very fine and uniform dispersion, you now have uniform wear.
If those are also very hard, they also now I guess push against each other in a stronger way as opposed to. Welding to each other like we described before. So a harder surface is harder to have a welding and shearing than a softer surface. Super tough. It leaves a significantly hard surface, harder than other I’ll call ’em competing.
Technologies, whether it’s a through hard or a case car rise significantly harder than both of those. And we lead with super tough because of the peeling damage that it combats super tough. Was created originally four applications similar to main shaft, where it was slow speed. It was high low.
There was the debris, but typically the debris was coming from the outside in. In the case of main shaft, typically the debris is created by its own bearing. The bearing is eating itself alive, right? It’s from the inside out. And yeah, super tough is got a number of different characteristics that we like.
And to be honest for NSK, for material, that’s one of our core competencies. Super tough wasn’t the only option for us to choose, but it’s the one that made the most sense. We had a few other choices that we could have gone with. We have other materials that we use for slow speeds and high lows and applications like steel making and things like that.
For the size of the shafts. For the operations, it made the most sense to use Super tough.
Joel Saxum: This isn’t something that you engineered for win. This is something that you’ve adapted to win because you have a track record of using it in other places as well. What other, like from an NSK standpoint, what other kind of bearing applications do you use?
Super tough in just to to understand. The track record of it, it was created for,
Loren Walton: Like I said, steel making was one of the big places where we use the NSK as a Japanese company. Steel is manufactured heavily in Japan. Japan is known for steel. Other places where we would use it would be like paper mining, heavy industries basically, where we would use super tough wherever there was a situation where we needed a combination of.
High loading and ability to combat any amount of debris that’s being put into the system. So it was introduced into wind, actually, I wanna say in gearbox because there was some other things that we saw that actually you could combat. Why X area and YX cracking. So actually I should probably take a step back and say from when we were doing our inspections and we saw that the DOC was being harmed, and I mentioned that we also saw a wide edge area and wide edge cracking inside of the inner ring and the rollers.
Another reason that we used super tough as the way to combat was because we had already had success with using super tough to combat wide edge cracking. So when we started seeing it in main shaft, in addition to having the ability to combat the peeling damage. Also when we started seeing why that area in main shaft, another reason that it made sense to go away from just standard through hard, going into the super tough.
And
Allen Hall: as we talk to operators across the United States at the moment that have DLC throughout their turbines farms you get a lot of worried looks and. Until we had talked to you and to Corey MIT lighter, we did not have any suggestions. And now that we’re talking with you here NSK seems like an obvious choice.
How do operators start to implement the super tough design into their turbines? What does that look like? Can they, how fast is a swap out? Do they need to do a lot of engineering ahead of time? What does that process look like?
Loren Walton: Yeah, so the bearings that we’re offering are the same construction, right?
So it’s a. Spherical roller bearing same IDOD. With that, the OEM design had it with it there shouldn’t be any sort of retrofitting or changing of anything required. Honestly, the biggest thing is I think for most people, understanding that we are making changes from the inside out is the biggest thing to understand, right?
Because if we look at one shiny round object and another shiny round object. And one of them has black rollers and you say yeah, that one looks like it’s different. Or one has a change to contact angle. Yeah, that one looks like it’s different. It’s a little bit harder to see, yeah, we make some changes to the internal geometry, but you can’t see it.
Or we made changes to the material and the heat treat, but you can’t see that. So we are, usually having to educate. What you are not seeing is what you’re getting from us, right? It’s all of the information, it’s all of the gathering, it’s all of the inspections. And then knowing that we can combat that with a different approach than what was used previously.
So everything for installation is exactly
Allen Hall: the same. Alright, so if an operator wants to start working with NSK, and it sounds like they probably should start talking to you, Loren, because you’re a wealth of information and you can help them out greatly speed up this process to get the DLC bearings off of their turbines and get running again before they have really big problems.
How do they do that? How do they get ahold of you? You, Loren? How do they get ahold of NSK? Where should they go?
Loren Walton: Yeah, so I guess I hope that they listen to this podcast and then we are visible, right? We attend all of the major events, right? I just came from presenting at the Drivetrain Reliability Collaborative LA this week week after next I’ll be at the operation Maintenance Safety conference for a CP.
I’ll also be at Clean Power in Phoenix. I typically go to all three of those conferences every year. But it’s not just me, right? We also have a team of engineers and segment personnel that work and win. But if you’re specifically looking for me I guess I can give out my email address.
It’s my, my last name Walton, W-A-O-T-O-N, and then my first initial L and that’s at. k.com. So Walton l@nskcorp.com. So you could email me at any time, always looking for the next science fair project to work on, and you need to go
Allen Hall: to nsk.com and check out the website. There is a great deal of information about wind turbine bearing specifically.
Really informative videos to go along with it. You can see the super tough coding and all the details there on the website, and you obviously you can connect with Loren on LinkedIn. He’s available there too, so reach out to Loren. Loren, thank you so much for being on the podcast. Learned a great deal today.
We need you to come back and talk bearing some more.
Loren Walton: Yes. Yes. Appreciate it.