The Uptime Wind Energy Podcast
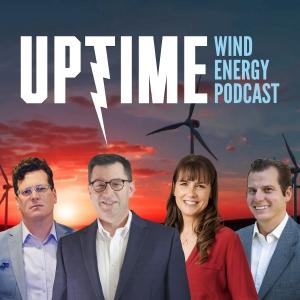
The Global Blade Group Builds Industry Blade Knowledge
Allen and Joel speak with Birgit Junker, co-founder of the Global Blade Group, a forum created to share knowledge and innovation around wind turbine blades. For over ten years, the group has been making blade information more accessible and approachable. For more information on joining the Global Blade Group, email tgbg@statkraft.com.
Fill out our Uptime listener survey and enter to win an Uptime mug!
Sign up now for Uptime Tech News, our weekly email update on all things wind technology. This episode is sponsored by Weather Guard Lightning Tech. Learn more about Weather Guard’s StrikeTape Wind Turbine LPS retrofit. Follow the show on Facebook, YouTube, Twitter, Linkedin and visit Weather Guard on the web. And subscribe to Rosemary Barnes’ YouTube channel here. Have a question we can answer on the show? Email us!
Allen Hall: Welcome to the Uptime Wind Energy Podcast Spotlight. I’m your host, Allen Hall, along with my co host, Joel Saxum. Today, I’m delighted to welcome Birgit Junker, a true pioneer in wind energy blade technology and the co founder of the Global Blade Group. This organization has become the premier forum for the wind turbine blade experts to collaborate, share knowledge, and drive innovation in areas like structural design, Lightning protection and blade inspection technologies.
Welcome to Uptime Spotlight. Shining light on wind energy’s brightest innovators. This is the progress powering tomorrow.
Allen Hall: Birgit, welcome to the Uptime Wind Energy Podcast Spotlight.
Birgit Junker: Thank you very much and thanks for having me.
Allen Hall: I want to start off by looking back a little bit into 2013. What were some of the challenges that when farm owners were facing with Blade technology and maintenance that led you to create the global Blade group?
Birgit Junker: To start with Rege from Vattenfall and I, we were relatively new on the owner operator side. And we both found that when we were speaking to our colleagues, they, their eyes just glazed over every single time we said Blade. Cause nobody knew anything about blade. When I was hired at Eon I came from from Siemens.
I was hired at Eon. I was told that they didn’t have blade issues. So I should expect to work about 80%, 75 percent on blades. And the rest of the time I should be spending on a drivetrain. 10 years later, when I left, there were 10 blade people. And I never ever had to look at a drivetrain. That was the attitude then.
Blades were not a problem. We didn’t have blade problems. Blades were like that black box that you had. You just went out there and counted that they were all there. And you listened just to make sure that there wasn’t anything strange going on. And about, you 99. 9 percent of the time, nothing happened.
There was nothing wrong. We even had contracts that said that blades were maintenance free. But then Reg and I started on the owner operator side. We came, we both came from OEMs. I’ve done catastrophic failure investigation. I’ve done field failures. I’ve done all sorts of things for what, 10 years before that.
And knew that we did have blade problems. Ian just hadn’t found out yet. So when I started, Reg and I, we decided that we needed to talk to one another because we couldn’t talk to colleagues.
Joel Saxum: Birgit, from experiences in the field I would, I want to follow up with that as a hard second. Because so many people Don’t understand even today what’s going on in the with blades.
Like I’ll give you an anecdotal problem. I was in a field doing an RCA and out there with a site supervisor who was in charge of 120 odd turbines, big wind farms in the States, right? And he was looking up. He said, yeah, those blades, he’s they’re just, big plastic wings in the skies.
And I was like, they’re not actually plastic. And he goes what do you mean? I said it’s it’s like fiberglass and this and that. He’s wait a second. So you mean to tell me that thing’s like a, it’s built like a boat. Like it’s like a fiberglass boat up in the sky. And I said, yeah.
And I was like, I was like, that’s more in line of Ben, a plastic wing. And he goes, Oh, he’s I never really knew that. And I said, Oh, further conversations with this this gentleman, he’d been in wind for 15 years and it was running wind farms and didn’t know that the blades were made out of fiberglass.
So I think that when you came in, what you’re talking about, it’s the origination story of Global Blade Group here. That could be echoed all over the world. There’s so many people that don’t know. What it really is. You and Reketpale from Vattenfall, so you guys got together, you understood that, Hey, we could talk to each other about these things and try to fix these problems.
Did the next conversation go, let’s bring more along? Let’s bring some others along?
Birgit Junker: Our initial goal was to increase the knowledge about blades in the industry. And I am still now after 22 years in the industry, I’m still asked, are blades hollow? So that goes along with your your guy in the U S asking if, glass fiber, really?
But but yeah, the initial goal was to increase the knowledge, but also. And to have a common front towards OEMs and other interesting parties, the first meeting we had was actually with DNV and GL about the the guideline for blade design. And while we were sitting at the table, one of the managers looked at us and said, very discreetly, I’ve actually never spoken to an end user before.
And these are the people doing the guideline for blade design that all blades are type approved type approved from. And with my normal way of speaking, sometimes I speak without thinking. I just looked at him and said, I guess that was about bloody time.
Allen Hall: It leads to a good point, Birgit.
So what is all this, when you have all this fragmenting knowledge running around from different organizations, how does that affect the performance and maintenance of blades out in the field? If you don’t understand some of the fundamentals, what are the consequences of that?
Birgit Junker: You got two two very extreme consequences and then something in the middle.
The. The worst consequence is that people look at them like a black box. Like Joel’s American site manager and don’t do anything. Especially if they have one of the really old contracts where it says that blades are maintenance free. And then you have the they don’t do anything. They run them and suddenly they fail and they get shocked and they’re like, Oh my God, something happened.
I don’t know what to do. And then you have the other extreme. Where a company will have an independent service provider on blade repairs servicing their blades or the OEM servicing the blade, and they will do repairs that aren’t necessary because they are being over eager. They want to make sure that the blades are perfect all the time.
And you don’t need that. You need something in the middle. You need to maintain your blades in such a way that they don’t fail and you get the expected AEP. But that doesn’t mean that you have to repair them every single year. It just means that you need to keep an eye on them, make sure that they don’t crack that they don’t have cracks in structural areas, that they don’t have open leading edges or open tips, that they don’t have lightning damages that are severe.
And if you do that, you can cut down on your maintenance. And have a turbine that operates really well.
Joel Saxum: I liken some of this, and this is not just this comet is not just blades, it’s drive, train, gearbox, bearings, all these things and wind. So if you have say, we talk about a fleet wide problem.
You have a, we’re in the States, a Ford truck. Okay? A Ford truck. There’s millions and millions of these things out there. In the hands of all kinds of people. And so when there’s an issue with something, there is a tribal knowledge that’s so deep that you can reach out in every direction and find an answer.
Everybody has an answer to how to fix this carburetor or whatever it may be on this vehicle. In wind, we have such a small size of a fleet, right? So if you’re, say you’re a XYZ wind operator and you’re a decent size, you have a thousand megawatts of wind production. You may only have 50 of one kind of turbine and 60 of one kind of turbine 80 of one kind of turbine So that’s not a very big like statistical fleet to pull information from because failures happen at different rates and different things and different blade Manufacturers then we get deeper and we get into this one was manufactured at this plant versus that and we have this model But they have those blades and so it creates an inherently tough problem for the industry And the answer to it is the same answer that we, or in my opinion, the answer to it is the same answer that we hear at almost every conference, trade show, industry get together.
We hear collaboration and transparency. However, it’s hard to make that happen, but that’s what you guys have done here. That’s what the global blade group is based on is collaboration and transparency, because if you’re one operator and now all of a sudden you have, Eight friends that are operators and they can share information from their fleets with you.
Now you have this collective piece of info or collective batch of information that can give you so much more insight into what may be happening on your own fleet. You guys have taken on a lot of projects in this manner. What, what does that look like for collaboration?
Birgit Junker: To start with, we we were on a much lower level.
We were just like, we want to function as small own operators, a back office support. We had companies that were part of the initial, we started being the blade group and then there was the. Scandinavian Blake group or Nordic Blake group. And then it became the European Blake group.
And now it’s the global Blake group. But to start with, we had small owned operators that were part of it. And they would call us, some of us, one of us and say, my OEM says this. What is he actually saying? Or in one case, it was like, can I actually believe this? And we could then go in and translate what was being said to make them understand it a bit better.
And that’s what I mean by we wanted to raise the awareness and the knowledge with, within the industry, especially the small owned operators, because a lot of those people, they were appointed blade specialists with actually never really seeing a blade. But that was just their area of responsibility in in the company.
And they were just trying their best and and that’s fine too, but we wanted them to have a bit more knowledge when they said yes or no to to an OEM. Primary goal was to increase the knowledge. Secondary goal increase the matureness of the industry and increase the Communication between OEMs, ISPs, and OWN operators.
Allen Hall: And that’s a different approach than other organizations take on BLADEs in particular. I’m not going to name them, but there are several organizations that are trying to do something similar. But I always feel like they’re very rigorous in the documentation phase, creating of standards, whatever that is.
But they don’t have the requisite engineering at the table to help explain these things. Is that what the global Blake group really brings to the offering?
Birgit Junker: We we’ve actually requested not to have any kind of commercial people present. We want it to be an open technical discussion. Of course we honor everything, which is, NDAs and all that sort of stuff is on it, but it’s critical.
Communication of a technical nature between owner operators and and sometimes it’s also helping somebody to decipher what they’ve been told in connection with a failure or a new kind of blade, all that sort of stuff. And it’s just, um, because it’s free and because we only have own operators because of GDPR, which is the European rule set for communication and and data.
We are able to speak relatively free, relatively freely without having to have lawyers present. And because we don’t have commercial people, and we don’t talk about projects if they haven’t been signed yet. We don’t talk about a lot of things where we would, you know, Require lawyers or commercial people.
It’s technical stuff. And very often we don’t know what site people are asking us questions about. We don’t know. We know what turbine type because we don’t need to know what blade type, but we very often don’t know what country it’s in what area it’s in. We know if it’s onshore or offshore and whether it’s in a lightning area or not.
If we’re talking about lightning, that kind of stuff.
Allen Hall: Let’s focus on one particular problem, which I think is universal, which is lead, leading edge protection, leading edge damage. And I know you’ve been vocal in that area and I talked to you at Sandia a couple of months ago about this and I got an earful, which is fantastic by the way, because I like hearing your opinion about this, but how does that work in terms of the global Blake group?
If you’re looking at a particular problem, how’s it sussed out among the members?
Birgit Junker: We create what is called a JIP, which stands for joint industry project. Right now we actually have a JIP on leading edge erosion where seven own operators in Europe and the U S have decided to put some LEPs on turbines.
And for most of them, I think it’s seven the seven own operators that are part of it. Six of them have put the same material on at least one turbine in the test. And then they have put two or three different LEPs on different turbines so that we all have the same one. So we have some, a reference point and then we have all the other ones and we we got some assistance from a third party in the UK, they get access to all the data from our inspections.
They put everything together and we can now see five years down the line, which LEPs are better than others. Which ones fail first, which ones fail last. And because we all put the same LEP on as a reference point, that is the one that everything is compared to. And we can see that some of the LEPs fare really well, some of them not so much.
And we can also see that some of them should have been put on from platform but weren’t and some have have been really easy to put on. And we’ve also seen a difference between the different LEPs in the sense that some tapes work better than other tapes. Some precasts are better than other precasts and within paints there are differences as well.
And we got everything from a three layers LEP to a single layer paint LEP. Yeah, we do joint industry projects and it’s voluntary for the ones that want to be part of it. They pay what they do. And each company, each individual company pays for their part. So there’s nothing between us financially.
Allen Hall: Yeah. So there’s no money coming to the table just to belong to the group. But if you want to participate in the testing program, like on this leading edge protection effort, you’re going to put some coatings on your blades. You’re going to donate that time and effort to go do that. But the return on that investment is a hundred X because you can’t find good information on leading edge protection from real world turbines.
That is the hardest part. And then to tie it together with the engineering knowledge, And history of blades that the global blade group brings to the table. That’s not anywhere else on the planet right now. Is this just one of several projects that you’re working on at the minute? What are the other projects that you’re working on?
Birgit Junker: We focused very much on the LEP because when we started this project we were three companies to start with Stattgart, Vattenfall and and Eon. And we tested 20 LEP projects. On a rain erosion test and chose the ones that behave the best. And then we made this JIP where we invited the rest of the Blake group to participate.
And we ended up being seven own operators. And we’ve been, that has been running now for five years. We’re actually at the moment talking about starting two new JIPs, one on on databases and inspections and how we can deal with those because we we get information and very many different kinds of data.
Formats and quality and stuff like that. Try and make something where we can do added benefit from the data that we get, and we’re also looking into the last one is that beginning, beginner stage. We want to test some some CMS data or CMS systems. But it’s like having a project that’s seven times as large as the one that you can do yourself individually in your company, And and you’re only paying for your own part.
So it’s, you get a lot for nothing or a lot for a little.
Joel Saxum: How do we add a fourth one for lightning protection upgrades? How can we do that?
Birgit Junker: You ask kindly.
Joel Saxum: I can get down on, I can get down on a knee. I think it’s a fantastic idea, right? Because you’re not only are you getting different I think the installation part is a big one.
You’re testing the LAPs. Yes. But you’re testing how they were put on the ambient conditions. They were put on all that stuff is great. But the big part here for me is It’s being tested in varied geographies, right? Because you can put LEP on one wind farm in one spot and you’ll get a certain amount of tests.
But if you spread that test from different corners of the world, different corners, closer to the ocean, maybe offshore, maybe onshore, maybe up in a mountainous range, maybe in Spain, maybe in Canada, wherever. And you add all of those together, you start to get a much better picture of the overall qualities of whatever this product is.
So in that project, you had seven owners involved. What does a normal meeting look like? How many people, how many different operators are involved in a normal meeting?
Birgit Junker: We don’t have a lot of meetings because we have a third party that does all the the analysis. The JIP was actually started by EDF.
And they sent a project proposal to all the own operators and said anybody want to be part of this, you want increased knowledge. And the only way we can get it is by going out and doing it. And if we should do it ourselves, it’s going to be humongous. But if we do it together with the rest of you we can get more for less.
And so EDF is running it. But we have a third party doing all the analysis and the reports. And if you come to the DTU event on leading edges in February, I think it is you will actually hear about the five year report. And we are also looking into extending it because there are at least three new LEPs that we haven’t trialed.
And so we are right now discussing whether we can extend it or whether we should start a new one and and how we can do that.
Joel Saxum: Bjerken, let me ask you a question, cause this is one that I have quite often and Alan, earlier in the show or in this little recording, you had mentioned different groups.
In those different groups, and so this is, this may be a point of contention here, in those different groups, they want operators, and that’s great because they don’t want outside influence changing how they are. However, in my opinion, I think that at some of those meetings, they should have, or some of those conferences, some of those meetings, some of those get togethers, some of those white papers that are written, I believe that they should bring in subject matter experts in individual subjects.
Like I’m talking, if you’re talking aerodynamics and you have a bunch of blatant people, that’s fantastic. But, in my mind, I would bring in Nicholas Goddard as an aerodynamic subject matter expert to supplement that conversation. It’s the same thing I talk, like, when we see people talking operators talking lightning.
Alan and I live lightning all day, every day. That’s all we do for our day job, is we have to eat. When I believe that, in some of those conversations, that, that bit of knowledge could be very beneficial to that group. Do you guys bring that in, or is it all just operators and nobody else is allowed?
Birgit Junker: Because of the confidentiality and GDPR and all that, we can’t bring in ISPs or subcontractors on specific areas, especially not if they’re suppliers. One of the main parts is that we’re not allowed to talk about the cost of using these subcontractors or suppliers. Because that would be a competition issue.
But what we’ve done is that we’ve made working groups right now Bladina has a working group on stock on structural damages. So on the team site, which is the new place where we’re going to store all the data Bladina has access to the group the working group called structural damages and talking about Nick from PowerCurve After New Year he will actually be heading up a new group called Aerodynamics.
And and Politech has yet said yes to head up a working group called Lightning. There will be webinars. There will be sharing of information. We will perhaps be making some kind of inspection reports together so that we are talking the same language. That’s one of the things that started the whole I think it was you, Alan, that mentioned it earlier.
The Blade Handbook. The Blade Handbook was actually written by one of the owners. And it was like four pages. It was an information for employees. And then Vladina helped them make it. And and after agreement with this owner Vladina said, when we do these projects because they do a project very, very often they do projects for us we could add more data.
We could add more knowledge, we could add words, we should have a common language. So that’s actually how the Blade Handbook started. It was it was an attempt for us to speak the same language, use the same words, understand what everybody was going on about. And it’s it’s now a very comprehensive book with lots of terminology.
And that was the common goal was a terminology. So everybody understood what we were talking about. Whether it was, leading edge or trailing edge, the abbreviation for it, whether it was pressure side or suction side the abbreviation of it, but also the different ways that blades are built up.
You’ve got the box bar, you’ve got the integral blades, you’ve got the web blades, you’ve got carbon, you’ve got a glass fiber, you’ve got balsa, you’ve got pine, you’ve got PVC, you’ve got PET, you’ve got all of that is in that blade handbook. to make sure that we speak the same language.
Allen Hall: We’re going to put the link to the Winter and Blaze handbook in the show notes, because if you don’t have that as a reference on your laptop, your desktop, or printed out next to you on your desk, you need to do that because a lot of the knowledge that comes from the industry and all the experts that are from around the world when they put that into a condensed volume, that is explanatory.
The average human can understand what’s happening. Those things are invaluable. And you need to go find that. We’ll include that in the show notes, Birgit, because it’s a really important document for the industry to continue to grow and understand what is happening. And I know we, Joel and I had talked to a number of operators and engineers that are interested in joining the Global Blade Group.
How do they do that? What’s the process?
Birgit Junker: They send an email.
Allen Hall: It’s that easy?
Birgit Junker: It’s that easy. If you’re an owner operator. And you send an email to the email that you will share on the screen at some point, Alan. I will be on the other end and I will send you an email specifying exactly what you have to do.
And it’s all based on teams. So you have to join a team’s site and you’ll have to put your name in a membership list. That’s how easy it is. There are also bylaws because more and more owners didn’t want to join unless there were bylaws. Before COVID we were 52 owner operators. There are quite a few people that have left their jobs.
So we need to reestablish the contact with some of these companies, but we’re we’re getting up there. And and the whole idea is to increase the knowledge. and have a common area where people can share information and ask questions and also ask the stupid questions. Personally, I don’t think there are stupid questions, just stupid answers, and they’re usually supplied by me.
But if you don’t know what the leading edge of a blade is, you should have somewhere where you can ask that question. Because a lot of the people that actually work with blades. Don’t have the introduction to what a blade actually is.
Allen Hall: Yes, that is so true. And if you want to join the global blade group and get connected with Burgett, the email address is tgbg@Statkraft.com.
So tgbg@statkraft. com. Birgit, thank you so much for being on the podcast. We’ve wanted to have you on for a long time. We need to have you back more often because there’s so much information and you’re. Tremendous help to industry. So thank you for being on the Uptime Podcast.
Birgit Junker: You are more than welcome.