The Uptime Wind Energy Podcast
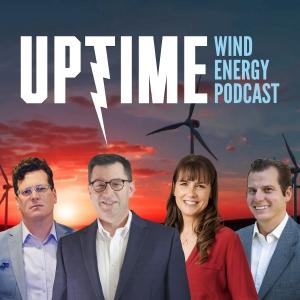
Ørsted Offshore Blade Install, Degradable Epoxy Resin Composite
This week on Power-Up, Ørsted’s offshore blade install method, SWANCOR’s degradable epoxy resin composite, and a precursor to the Google Glass!
Sign up now for Uptime Tech News, our weekly email update on all things wind technology. This episode is sponsored by Weather Guard Lightning Tech. Learn more about Weather Guard’s StrikeTape Wind Turbine LPS retrofit. Follow the show on Facebook, YouTube, Twitter, Linkedin and visit Weather Guard on the web. And subscribe to Rosemary Barnes’ YouTube channel here. Have a question we can answer on the show? Email us!
Pardalote Consulting – https://www.pardaloteconsulting.com
Weather Guard Lightning Tech – www.weatherguardwind.com
Intelstor – https://www.intelstor.com
Join us at The Wind Energy O&M Australia Conference – https://www.windaustralia.com
Allen Hall: Welcome to Power Up, the Uptime Podcast focused on the new, hot off the press technology that can change the world. Follow along with me, Allen Hall, and IntelStor’s Phil Totaro, as we discuss the weird, the wild, and the game changing ideas that will charge your energy future.
First patent idea is from our friends over at Orsted, and they are looking at a really novel approach of installing wind turn blades vertically rather than the horizontally, which is we do today offshore. So if you’ve watched offshore blades being installed, you’ve always seen them placed horizontally and slid towards the hub and everybody tightens them on.
Well, that requires a lot of really tall cranes to, to make that happen. But what Orsted’s thinking about is grabbing the blade kind of by the bottom and lifting it up vertically. In order to do this, you need a pretty rigid frame to hold this crane to keep it from the blade stabilized. So the crane doesn’t move too much.
And it’s, it’s, it’s kind of a complicated mechanical problem. However, it does require a much shorter crane and that is the benefit and getting big cranes out at sea right now is really hard. Phil, so having a short crane with a much stronger crane head, I’ll call it,
Philip Totaro: Does make a lot of sense. It does.
And, and so just for context, we talked a couple of weeks ago about, Equinor getting a patent on, technology around optimization of floating platforms. This is another example of a development and independent power producer company, Orsted, getting a patent. IP themselves that they control on something related to, the, the business that they do on a daily basis.
And the reason I’m bringing this up is it’s, it’s a bit unique in the wind energy sector because most of the, Particularly important patents have been held in the past by the OEMs or other supply chain companies. So for, a company like Orsted to, to even contemplate doing this is, is fascinating.
This is still in the conceptual phase. There’s no rig that they’ve built yet. They’ve probably done some smaller scale bench testing, potentially. They’ve certainly done, plenty of computer modeling on, on this sort of thing. To get it to work. But it is, as Alan mentioned, an interesting concept because, the, the blade’s moment of inertia, when it’s in the vertical position, it, it has the opportunity to potentially flop around or tip over.
But the counter to that is, as Alan mentioned as well, you need a much shorter crane boom. And so, these are some of the technical challenges that, that Orsted is trying to address with introducing this kind of technology. I guess the question maybe for Joel is, is, does this seem practical and, and how attractive is this going to be?
Joel Saxum: I think from an operational standpoint, so for real world value of a patent, and this will happen eventually, and I don’t think it’s limited to offshore. I think it will happen onshore as well. And, and I’m saying this based on the global build out of wind farms, onshore, offshore, floating, you name it, what we’re doing and the goals we have in place.
All of these, do an easy one. Onshore Windfarm has a big, huge crane, a Liebherr 1300, and it’s got a tail picker and all this stuff, you have to mobilize two cranes, even though one’s smaller than the other. The same thing with offshore, you have all these specialized vessels, you have to mobilize this one vessel, it’s the only one that can lift these, 130 meter blades or whatever it may be.
We need ways, innovative ways, to be able to do installations easier. And not only installations, you gotta think about operations and maintenance. So as the lifetime, if we get more and more of these built, yes, construction, but now we’re getting to the point where we have to take and swap blades out, or if there’s an issue or something of that sort.
So, things like this need to happen. Does it make sense for me as an armchair engineer? Of course. Especially sitting here with Phil and Alan, who are Much better engineers than I am talking about moments of inertia. And this is, I’m standing here with my sitting here with my pen and my fingers together trying to figure out how this balance works.
I think it, I think there is a future for something like this. And kudos to Orsted. Maybe they’re gonna get the license it to a bunch of people.
Allen Hall: Our second idea is a degradable wind turbine blade and manufacturing method by Swancor Advanced Materials. And if you’ve been watching in the news about recycling and wind turbine blades, there’s been a lot of discussion about creating resins that you can decompose.
Well, this is one of them. And they, they’re. The idea is to create this resin. There’s a specific chemical compound that they’re creating, but when you break it down, you basically take the blade and drop it into an alkaline environment at somewhere around a hundred degrees Celsius for a period of time.
And the resin separates into its intrinsic parts. You can also recover the fabric that was in the blade. So you basically can start over with all the ingredients. It’s like unbaking a cake in a sense. This is really important because there’s a big movement in Europe to not landfill used wind turbine blades, and I think that movement about not landfilling is going to happen here in the United States.
So, SWAN Corps is really set up here for an opportunity, Phil.
Philip Totaro: Yeah, and just for context for everybody, SWAN Corps is a a partner to a number of the OEMs already including Siemens Gamesa that has developed, recyclable blade, recyclable blade technology utilizing, I don’t know if it’s this specific formulation that they’re describing in this, this patent but it’s probably close.
And they’re actually doing this together in, in the manufacturing facilities in Taiwan. as well for some of the offshore blades for Siemens Gamesa. I believe Squancore is also a supplier to Vestas and certainly some of the Chinese OEMs, Sonoma and Envision Energy. So the fact that this is, again, I’m not sure if they’re using this exact, formulation in their commercially available product.
But like I said, it’s probably pretty close. And, it’s fantastic to see we just talked about another idea from Orsted that’s kind of, technology readiness level, like four or maybe five for those that are familiar with that, well, we track the, the technology readiness levels for all these patents that we catalog at Intel store.
This one’s probably a TRL eight or nine. And so again, this is fantastic to be able to see the progression of technology come into the market.
Joel Saxum: Phil, to, to your point there. A resin much like this one. I don’t know if it’s the exact same one. Like you said, RWE installed 2023 at the Cascasi wind farm offshore.
And there were Siemens Mesa blades. So something like this is being used in the field right now. My fall down on this one is the same conversation that you have whenever you talk about recycling wind turbines blades is what’s the throughput of something like this. Right. So what this patent says is thermal degradation is conducted 60 degrees C to 180 degrees C for 1 to 48 hours.
We don’t know exactly what it is. I’m sure that has to do with agitation in the, in, in the chemicals and these kinds of things, but that’s hugely energy intensive and it’s pretty slow. So when we get to the point where we’re having hundreds and hundreds and thousands of tons of turbine blades to recycle, which we have right now, and it’s only going to grow and grow and grow into the next 10, 20, 25 years, because that’s when, when, by the time these, this resin is into manufacturing, it will be another 25 years until we have to recycle them.
Can a factory or can a mechanism handle this at scale in the real world? Because even as it sits right now, we have people that are having a hard time at scale, grinding these things up to use them in roadbed materials and other things. So, I like that we’re moving forward in this method, and it could be something really cool in the future.
Does it sound like it’s ready for scale? Not to me. But I hope it is.
Allen Hall: Our fun invention is an interesting one this week. Joel, do you know what beer goggles are? I wear them like every Saturday . So this is a relative to beer goggles, and it’s similar to what Google Glass was at the time. It’s a set of glasses and on the lenses they put subliminal messages above the normal sight line, so it’s a stereoscopic effect and so on there it can say, Joel, no beer.
And then they can project that out in front of you on Saturdays so that you can remember what happened on Sunday. But this, this idea, I have not seen this implemented, but it is a very unique idea, just putting something on the edge of your vision all the time that you kind of lose track of. You don’t focus on it because your brain eventually just tries to ignore it.
But some part of your brain may be paying attention to it. And. Could give you
Joel Saxum: some healthy advice. I think there’s, this is, this could be really used in I, I have a lot of uses, I’m thinking marketing campaigns, here’s some free sunglasses to wear and then you never know what you’re actually getting from them or even messages from like maybe parents to kids, like, Hey, clean your room maybe me or maybe me this week, make sure you get my windshield repaired.
If it had something that you could. That you can change in real time on them. That might work really well. I like the idea.
Allen Hall: Come on, Phil, you have a use for this.
Philip Totaro: Well, let’s also give some background on this. This was originally conceived by a couple of Canadian inventors back in 1990. And that’s, they filed it, I think they filed a U.
S. version of the patent in 1991. It issued in 92. This patent is actually cited. As what’s called prior art, so kind of a previous invention to things like the Google Glass and some of these other goggle based technologies that Meta and some of these other companies, Apple have, have actually developed.
So even though this isn’t using or contemplating necessarily augmented reality technology, which was, what a lot of the modern versions of, of these glasses are this was a predecessor to that and, and something that kind of inspired derivative contributions in, in that area.
So this, this is actually kind of a fun and interesting one. I, again, you’re right. I’ve never seen anybody develop this, but it would probably come in handy