The Uptime Wind Energy Podcast
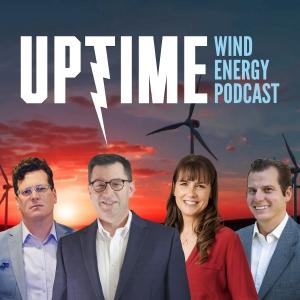
Helicoid: Strengthening the Leading Edge
Allen Hall speaks with Helicoid Industries’ Dr. Lorenzo Mencattelli about their groundbreaking wind turbine blade LEP technology, which uses a biomimetic fiber pattern inspired by mantis shrimp. Their solution reduces erosion damage by 70% and can work with existing materials and manufacturing processes.
Sign up now for Uptime Tech News, our weekly email update on all things wind technology. This episode is sponsored by Weather Guard Lightning Tech. Learn more about Weather Guard’s StrikeTape Wind Turbine LPS retrofit. Follow the show on Facebook, YouTube, Twitter, Linkedin and visit Weather Guard on the web. And subscribe to Rosemary Barnes’ YouTube channel here. Have a question we can answer on the show? Email us!
Pardalote Consulting – https://www.pardaloteconsulting.com
Weather Guard Lightning Tech – www.weatherguardwind.com
Intelstor – https://www.intelstor.com
Join us at The Wind Energy O&M Australia Conference – https://www.windaustralia.com
Welcome to Uptime Spotlight, shining light on wind energy’s brightest innovators. This is the progress powering tomorrow.
Allen Hall: Welcome to the Uptime Wind Energy Podcast. I’m your host, Alan Hall, and today we’re discussing one of the most persistent challenges in the wind energy industry, beating edge erosion on the wind turbine blades. To discuss an innovative solution to this problem, we’re joined by Dr. Lorenzo Micatelli, the Managing Director of Tech and Ops at Helicoid Industries.
At Helicoid Industries, Lorenzo is spearheading the development of a groundbreaking technology that could significantly reduce leading edge erosion damage on wind turbine blades. Lorenzo. Welcome to the Uptime Wind Energy Podcast.
Lorenzo Mencattelli: Thank you very much, Allen for having me.
Allen Hall: So leading edge erosion is one of those top issues, and I first ran across your company at DTU, at the Leading Edge Erosion Conference, and all the experts all around the world were there.
I think it was in February or March earlier this year. And I sat through all the presentations and then Helichord came up and gave a presentation, and I was astounded because I hadn’t seen anything like this technology before. But first I want to talk about how big of a problem this is, and I think during that DTU conference we realized it’s a couple percentage points of power loss for a lot of operators, and it’s structural damage when leading edge erosion penetrates through the shell of a winter blade.
That’s a huge problem.
Lorenzo Mencattelli: Yeah, exactly. So the, the, the small percentage power loss is often acceptable if you want, because it doesn’t really force the operator to, to stop the blade and, and perform maintenance and repair. But when the erosion gets to the composite substrate and therefore the structural integrity of the blade is compromised, then it carries a whole lot of other issues.
And, and then operations need to stop.
Allen Hall: Yeah, and that’s where you see all the repair work going on, particularly in the United States, in the middle of the United States, where leading edge erosion has penetrated to the shell, and the amount of time and effort of independent people. service providers going and fixing blades, leading edge erosion is a, is an industry upon its own.
And it’s a little shocking actually that your technology hasn’t been used yet. I want to just describe it here in a second because the, right now in order to prevent leading edge erosion out of the OEMs, the manufacturer’s equipment, you have to apply Plastic, basically plastic shells or rubberized plastic shells or put some sort of thick coating on to the blades, which is somewhat effective.
I would say it’s going to give you a couple of years of life, but there really hasn’t been a true fix.
Lorenzo Mencattelli: Yeah, so the, the focus indeed has been mainly on developing new solutions for the coating, right? That is applied on the, on the leading edge, while there is no be any engineering on the composite substrate underneath.
And the reality of things is is that the operator, you know, spin their blades way beyond the erosion of the coating. So initially when we deployed. When we thought of this solution, we wanted to find something that would work together with the coating. So initially, we are not considering replacing entirely the coating with our fiber architecture.
But the idea is to give the operator an extra margin of safety once the coating has been eroded to keep their blade spinning, produce energy and not worry about having issues of structural integrity because now the composite substrate has the strength to endure that erosion.
Allen Hall: Yeah, and the failure mode on the structural side as it was described in your presentation, was the resin.
Basically, the plastic that holds everything together, right? That the fibers go typically at 090 if you’re biaxial, and then you have these, these little pockets that are resin, and unsupported resin, has trouble in rain erosion. So it wants to be eaten away. And once you start to break that resin down, you get through one layer, then the next layer, the next layer.
Pretty soon your, your fiber doesn’t have any support structure. It gets eroded away. And then you’re through the blade. Now Your solution is really unique in the sense that you’ve thought about the way lineage erosion happens, but you’ve also sort of tied it to the animal world. I want you to describe that for a second.
Like, how did this idea come up and, and sort of describe how that animal world translates into materials?
Lorenzo Mencattelli: Yeah, so this is actually part of a discipline called biomimicry, where we take inspiration from features and some aspects of creatures and plants that can be found in nature. And trying to understand the relationship between the features that we observe and their function and then translate that into engineering principle and apply to material systems and so on.
So in this case, we we got inspiration from this specific microstructure that can be found actually in a wide range of creatures, including the mantis shrimp which is our mascot, if you want. And the shrimp uses it’s club to strike praise. It feeds on, it deploys underwater at very high speed caliber bullet speed, and it, it manages to crack shells of creatures which are considered to be quite tough themselves.
So if you look inside the club, you will see that this is in fact, a fiber reinforced composite structures is made out of unidirectional layers, which are slightly rotated one to respect to each other. to form this helicoidal distribution of fibers. So we are mimicking that and we initially deployed that solution for improving impact performance of of a wide range of applications from aerospace, automotive and so forth.
And then we started thinking whether The same architecture could have been beneficial. So, so for, for rain erosion, because eventually the, the rain, the rain droplet is a low mass, high frequency, high speed type of impact that happens in an area of the, of the blade. And by orienting and redistributing into an helicoidal way, the fibers in the composite substrate, we are able to better redistribute stresses.
That follows from the from the high velocity impact of the rain droplet, and therefore the structure is able to endure more impacts without an early on onset of erosion.
Allen Hall: So, if you go to Helicoid’s website, which is helicoidind. com, you will see this mantis shrimp hammer, and the sort of microscopic images of it, and it, it is a series of fibers.
It looks like a composite structure. It’s very interesting, by the way, so everybody should go look at that. But you’re right, it, the, the mantis shrimp has this helicoid pattern. type of arrangement of the fiber, which is much more tightly packed. So instead of zero 90 or plus or minus 45, how we typically do things in composite world, it’s, it’s every 15 degrees, maybe every 10 degrees, it’s the, the pattern starts to rotate.
So it’s, it makes a much more Dents, fiber composite structure, and as you mentioned, composite structures are not forgiving on impacts. In the airplane world, which I’ve worked for a long time, that thing about composites around landing gear is any kind of rock that gets thrown up makes a dent and it damages it immediately.
It’s a constant problem. It’s a constant repair problem, much like in wind turbines. This layering of the fabric and at different orientations then does create this little bit of a different structure. What happens when you put this structure, and I want to put a little framework around this, using existing materials, existing resin systems, existing fibers, I reorient those fibers in a much more prescribed way.
What happens when you take it to rain erosion testing? What do you see?
Lorenzo Mencattelli: Well, what it happens is you don’t see erosion for quite a few a few hours of testing. So we have we have done extensive rain erosion testing comparing a conventional substrate, as you mentioned, a plus minus 45 zero degree fiber, fiber orientation substrate, and we use the exact same fiber, the exact same resin, the exact same manufacturing process, but with our helicoid design leading edge.
To show that instead of getting larger chips of material being removed very quickly as the erosion progresses in our case, we have a very smooth and slow erosion of the substrate. So, for once, you reduce by more than 70 percent the eroded mass under the same testing conditions. And for second, you also get a smoother erosion, which decreases the loss in performance, aerodynamic performance, and also allows for easier and faster repairs.
Because now you can probably do a light sanding to recover the the shape of the profile instead of having to do a big cutoff and repatches of the of, of the leading edge.
Allen Hall: Yeah, it’s a different kind of wear effect, right? It’s not, I wouldn’t really call it erosion. I mean, in the top level sense, it is erosion, but when you see your plus or minus 45s in a rain erosion testing, you see the resin pockets start to fail first and you get this little grid like pattern, of course, and then you wear that away and it becomes very uneven very quickly.
And your material, it looks like someone has taken some sandpaper to it. That’s what it appears like, just worn it away instead of Pocketed and trying to bore through it. That’s a huge advantage like you mentioned. You don’t lose the aerodynamics with your
Lorenzo Mencattelli: material. Exactly. And, and as you said, this you know, the, the technology is really material raw material agnostic, right?
So it can be used with with conventional glass fiber and conventional resins used for wing blade manufacturing, but you can be also very creative and and start playing with with fiber type and resin system to, to Create a layering of performance enhancement into the leading edge. Wow.
Allen Hall: Okay. On your website, you do talk about flax fiber.
Obviously, the industry is trying to get to more natural fibers. That, that even putting flax fiber in for like 80 percent of the fibers and 20 percent glass fiber, you still roughly get the same result.
Lorenzo Mencattelli: Yeah, exactly. Yeah. So we have we have a big effort at the moment of leveraging our technology and natural fibers for automotive applications.
And with the idea of using the technology to enhance the performance of a material that is known to be less performant than conventional glass fiber or carbon fiber, so that you can effectively replace a glass fiber component with a natural fiber component. Achieving the same performance, but now having a big offset in terms of carbon footprint, because you, you, you’re moving the use of rheumatoid to, to a lower embodied energy one.
Allen Hall: Well, this makes really good sense. And seeing that presentation at DTU, it was eye opening because it just seemed like, wow, okay, this makes sense. It does seem to work. You have data behind it. You’ve done some testing on it. You’ve been in different industries, so you’re going to get a sense of different kinds of impacts.
The one thing that I didn’t realize at the time was that the area in which your material would be applied is actually relatively limited. Very similar to, you know, How you would apply a leading edge coating.
Lorenzo Mencattelli: Yeah, that’s correct. So we don’t plan to use the fabric to change the entire skin of the blade because that will have a major impact on the elastic response of the blade itself, right?
So we, it would be an issue of design of the entire blade at that point. The solution is is really a locally applied at the leading edge. to serve the function of leading edge protection. And that opens a possibility of implementing the technology in either at the manufacturing stage of the blade.
Because again, it’s just a, an, another couple of pieces of fabric that you place in the mold before infusion, or it could be used and applied as a repair patch for a blade that have already gone into some extensive erosion. So we are looking both at the manufacturing stage of the blade as aftermarket solution.
Allen Hall: Sure. And how does the different orientation of the fiber work? Handle infusion in a manufacturing sense
Lorenzo Mencattelli: very well. We have been building components in various thicknesses for especially for the automotive industry using Vartam. So basic infusion technique, RTM process it, liquid composite molding.
So various processing technologies using different type of fiber, carbon, glass, and different resins, and never been an issue, the infusion and processing of these fabrics. So virtually really they, they be, they behave in terms of processing and manufacturing. Exactly the same as a conventional fabric, but now with the advantage of gaining considerable performance.
Allen Hall: And then in the repair scenario, I assume like if you’re out in a blade in the middle of Texas where there’s a lot of leading edge erosion, you were thinking about like a pre preg that would just be applied to the leading edge and come on like a kit form. What’s your thoughts there?
Lorenzo Mencattelli: It could be both. So we have proven that the technology delivers its benefits even with just two layers of fabric on top of a conventional substrate.
So we don’t need to replace the entire thickness of the leading edge with our technology. You can too, if you want. and extend that benefit of erosion resistance, but it can be just a couple of layers applied on top of a substrate. So it could come into a preformed format very easily. I think the solution that we have right now, if you think of a prepreg format, would be a single Piece of fabric of about 1, 200 grams per square meter.
So very lightweight as well. Or it could be used as a conventional multi axial NCF patch. So dry format that is applied and then it’s infused with the rest of the of, of the components for the repair.
Allen Hall: So how wide would this piece be for, you know, most of leading edge erosion happens, you know, on the outer third of the blade.
How wide of a piece are you talking about? Are we talking, I’m going to talk in feet here, but are we talking about like one foot, a two foot, or two foot wide kind of pieces just to cover the leading edge and that’s it?
Lorenzo Mencattelli: Yeah, exactly. It could be it can be adapted to, to any size for any leading edge opportunity.
It, it can be produced in very wide rolls as well. So as I said, using conventional multi axial non cream fabric technology so we can be very flexible to serve a specific subset of the wind industry and enable them to use the technology.
Allen Hall: And in the resin system, obviously every blade manufacturer has their own specific polyester, epoxy resins, there’s a lot of variables there.
Can your system be infused with any of those resin systems to match?
Lorenzo Mencattelli: Yes, yes. It can be used using this exactly the same resin system. Again, the, the, the key of the technology is the orientation of the fibers into the fabric. That’s That’s what our technology is all about. Then it can integrate any combination of fiber and resin type.
Allen Hall: So, where are you seeing the most action on this, or reaction to it, I suppose? In the United States, where the service life of a winter blade is roughly 10 years, in Europe and other places, it tends to be much longer. It would seem like if you started off with the helicoid material on your blade out of the factory, in the United States, you may not do any leading edge repairs at all over 10 years.
Does that make sense?
Lorenzo Mencattelli: Yeah, of course it does make sense. So we see from our collaborators that we that, you know, severe stages of erosion, so where the structural integrity of the blade is compromised are achieved within four or five years. Of lifetime of the blade, so we could potentially extend that interval and hopefully double that interval in, in a way that the blade, at least the substrate of the blade doesn’t need to be serviced again.
So that, that’s the overall selling point of the technology. Giving an extra safety margin safety margin to the blade operator to perform the maintenance and delay as much as possible the intervation and the downtime of the blade.
Allen Hall: So what’s left to do in the qualification of your material?
Because when, when I saw you put it in. Several months ago now, eight, ten months ago, it looked like it was pretty well developed. That you had the data, that was shocking by the way, and congratulations for doing that because that really opens up a lot of doors for operators. What’s left to do? Is it just implementation, making sure the operators know about it?
Where are you at?
Lorenzo Mencattelli: Correct. So we have developed the fabric in collaboration with Sartex. Major supplier of the wind industry. So it’s been fully validated in terms of manufacturability and scalability. So for production at volume we have done the rain erosion tests at third party labs. that they test for the OEMs.
And right now we are looking at putting it on a blade in the field and and see effectively in real life how how it performs. But based on the process that we have been following for the qualification of the product we have no doubt that also in field it will delivers what we observe in in the lab.
Allen Hall: That is truly amazing. If any operator, or OEM for that matter, is interested in learning more about the Helicoid system and getting a hold of you, how do they do that?
Lorenzo Mencattelli: They can reach out to through our website. We have an info at helicoidin. com. Or you can reach out to me Lorenzo Mincatelli over LinkedIn.
Or over my email address lorenzom at elicoidin. com. And we would be happy to, you know, discuss, understand your needs and, and see how we could deploy and test the solution.
Allen Hall: Yeah, this is a really great technology and it needs to be out in service. So go visit the website which is spelled H E L I C O I D I N D dot com.
Lorenzo, thank you so much for being on the program. Great technology. Hopefully we’ll see it in service next year because it will change the blade industry. Thank you
Lorenzo Mencattelli: very much, Adam, for having me. Been a pleasure.