The Uptime Wind Energy Podcast
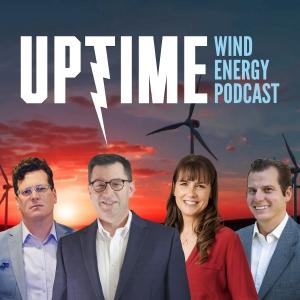
Main Bearing Failures: Detection, Coatings, and Solutions with Malloy Wind
Allen Hall and Joel Saxum talk with Cory Mittleider from Malloy Wind about the complex world of wind turbine main bearings. Cory breaks down why traditional bearing coatings are failing in newer turbine models and explores how electrical discharge, material choices, and monitoring systems play crucial roles in solving these costly failures. Dive into the technical challenges of detecting problems in these massive, slow-moving components and learn what operators should do during warranty periods to prepare for long-term maintenance.
Sign up now for Uptime Tech News, our weekly email update on all things wind technology. This episode is sponsored by Weather Guard Lightning Tech. Learn more about Weather Guard’s StrikeTape Wind Turbine LPS retrofit. Follow the show on Facebook, YouTube, Twitter, Linkedin and visit Weather Guard on the web. And subscribe to Rosemary Barnes’ YouTube channel here. Have a question we can answer on the show? Email us!
Pardalote Consulting – https://www.pardaloteconsulting.com
Weather Guard Lightning Tech – www.weatherguardwind.com
Intelstor – https://www.intelstor.com
Wind Energy O&M Australia Conference – https://www.windaustralia.com
Joel Saxum: Welcome to Uptime Spotlight, shining light on wind energy’s brightest innovators.
Allen Hall: This is the progress powering tomorrow. I’m your host, Allen Hall, joined by my co host, Joel Saxum. Today, we’re tackling a critical issue that’s affecting wind farm operators across the industry, main bearing failures and the evolving solutions to combat them.
Joining us is Cory Mittleider business unit manager at Malloy Wind, who brings over 15 years of hands on experience in power transmission and bearing technology. Cory has built his career at Malloy Electric where he’s become their go to expert for complex bearing challenges. His journey from technical sales support engineer to wind business unit manager has given him a unique perspective on the evolution of bearing technology and the real world challenges faced by wind farm operators.
Malloy Wind, based in Sioux Falls, South Dakota, has been at the forefront of developing solutions for wind turbine bearing issues, particularly focusing on advanced materials. and designs to combat common failure modes like peeling damage and premature wear. Cory, welcome to the Uptime Wind Energy Podcast Spotlight.
Thanks for having me. You are our go to guy for Anything bearing related. And as Joel and I travel around the United States this summer, we ran into a lot of people with bearing issues and now main bearing issues. And we’ve seen quite a bit in the press this summer about main bearings and coatings on main bearings and what is the right kind of main bearing to use and a lot of operators looking at different solutions at the minute, and we figured.
Cory will know. So let’s just ask Cory what his thoughts were on main bearings and try to get a sense of what can be done.
Cory Mittleider: Yeah. We’ve definitely spent a lot of time looking into main bearings, main bearing failures.
Joel Saxum: So let’s dive into this, Cory, then what is the. Just for our users or users, for our listeners can you give us the rundown basically of what the main bearing is, where it sits in the turbine and what it does?
Cory Mittleider: On the wind turbine drivetrain, you’ve got the blades and the rotor hanging out front, and then ultimately that’s connected to a shaft. Which then connects it to the gearbox and the generator. And on that shaft, that’s what we’ll call the main shaft. On that shaft, there is a really big pillow block.
And it’s got the main bearing inside. So we’ll call it the main bearing, the main shaft bearing, a couple of different nomenclatures there. But that’s what helps support that load of this very heavy drive train, but also connect it and allow the rotation to generate the power from the turbine. Some turbines do have two.
main bearings on this main shaft. And most of them installed in the U. S. have one. That’s what we’d call a three point suspension. The two main bearing ones we call four point suspension. There are some other designs some direct drives and stuff like that, but very small install, install base in the U.
S. So we’re really talking about this type of configuration where we’re talking about main bearings most of the time.
Joel Saxum: Okay. So I’ll ask you another really basic and simple question for people like myself. There’s a lot of people in the wind industry that have never been uptower and have never seen these things, so they may not know exactly what size and what kind we’re looking at, but, you’ve been in the wind industry for a while, Cory, so you’ve seen some small ones, and now we’re growing in from that one megawatt, sometimes 500 you’re in.
South Dakota. So you’ve got some Zahn Z50s and stuff out your door.
Cory Mittleider: Yeah, we’ve got some 750s out here.
Joel Saxum: So there’s, there are a lot smaller in the main bearing size, but now we’re getting all the way up to the point where we’re actually hearing of, like right now, GE is one, one 6. 1 megawatt, 158s are being installed in Wyoming.
So we’re getting to that larger size. What is the size of these things look like?
Cory Mittleider: Yeah, it’s been fun to see the trajectory on size. I remember one of the first main bearings I saw in person was a shaft size. That’s 12 inches. And coming from the industrial bearing space, where a good size bearing is 4, maybe 5 inches.
That thing was huge, right? I’m like, wow, look at that big thing. Over the last 10, 11, 12 years now we’re talking that mid two megawatt range, we’re talking 700 800 millimeter shaft sizes that’s about 30 inches. Shaft diameter. It’s really tremendous to see the size grow from another point of information, that shaft size bearing weighs in at about 2, 500lbs.
So 30 inch shaft size, 2, 500lbs, call it 50 inch on the OD about. So
Joel Saxum: putting this
Cory Mittleider: into
Joel Saxum: scale, right? Like I, I drive a three quarter ton diesel truck. That truck on the hoof weighs like 7, 700 pounds, 7, 800 pounds. So just three of these bearings weighs as much as that three quarter ton truck sitting out there in the park, in my driveway.
That’s insane, right? Just to put that into scale. The scale, but I will, in the wind industry, you get that conversation quite a bit. Like people don’t realize how big turbines are until you’ve stood underneath one. You can drive by on the highway. Drive up I 35 in Iowa and you look out and you’re like, wow, they’re cool looking.
That’s big. But then you stand on the pad underneath one and you’re like, whoa, this is a different story. Because when we talk about this, that main bearing supports a lot of weight, right? So you have blades, you have that hub sitting out there. And these blades can be 20, 30, 40, 000 pounds.
Each, right? So you’re talking, this bearing, the weight that’s hanging out over the front of it easily can surpass a hundred thousand, 150, 000 pounds that it’s supporting. So they become a massively critical element in the drivetrain. Like they’re very important to the whole mechanism. If these things start to fail, which we’ve, Alan and I have been hearing in the field, right?
Oh, we’ve got main bearing problems. We’ve got main bearing problems. This is not a trivial piece of kit to change out.
Cory Mittleider: No, and that’s a really good point. You look at the complexity of the system, the fact that to your point, this system, when you drive down the interstate a little ways away, it’s like, Oh, that’s big, but.
Once you put your hands on this stuff, you really start to appreciate just how big it is. And so one of the the mid two megawatt main shaft bearings is a 750 millimeter shaft size. This is the size of a roller from that main bearing. There’s maybe 60 of these.
Joel Saxum: So if you’re listening online, rather than watching the YouTube version of this, you can see Cory was, Cory, you can’t see, but Cory was holding up a roller bearing that is the size of, it’s a larger than even a Coke can of just, and this is just one of these elements.
Cory Mittleider: Yeah. Yeah. And there’s quite a few inside. The other interesting thing is there’s a curvature to it, so it’s not just like a Coke can, but it’s actually bulged in the middle. And, there’s a lot of different bearing types. Used just in any industry. And the thing that makes this this main shaft bearing special is it’s, they used in the design primarily, but are called double row spherical roller bearings.
And those have been around for a long time. They were invented in 1919. Very well defined from an envelope point of view. But the benefit of this bearing type is that curvature of the roller and the corresponding curvature of the raceway allows. for some deformation and it’ll accommodate what we call misalignment.
So you imagine you’ve got this a hundred plus thousand pound drive train on the up in the air, it’s 80, 90, a hundred meters in the air on top of a stick in a cornfield, right? The environment is changing constantly. Temperature, wind, weather, all this stuff. The ability of that system to move a little bit is why you pick a double row spherical type bearing.
So that allows. confidence that it will still carry the load effectively while still potentially being able to move. So that’s why the vast majority of mainshaft bearings are in fact, this double row spherical type as well.
Allen Hall: So if you have different OEMs you’ll see different manufacturers for those same bearing types, right?
That they’re not uniform. I haven’t seen. Two manufacturers of bearings produce really the same bearing. Everybody has their own particular flavor that they add to it.
Cory Mittleider: Yeah, that’s true. Every bearing manufacturer, tries to and they do a good job of setting themselves apart from one another, defining what what they think is important.
For applications for just the bearing generally. And although the envelope dimensions to your point are defined they’re ISO defined dimensions. Each manufacturer does their own things, right? Um, material differences steel alloy differences, cleanliness roller shapes, coatings as applied, right?
There are some coatings that are proprietary and some coatings that are Industry known, right? Maybe there’s their own formulation, but they fall into a category that’s similar.
Allen Hall: So when an OEM picks a main bearing, it has a general spec, from what I’ve seen. There’s a lot of mechanical features to it.
One of them tends to be lifetime, that they want to try to get a certain amount of lifetime. Out of the bearing where it happens. So all the manufacturers of these bearings come forward with their particular solution. What do those solutions look like? How do they vary between the bearing
Cory Mittleider: manufacturers?
Any OEM, they want to have multiple suppliers, right? So they want to define an envelope and make sure that they can have a supply chain to, To build all the farms that need to be built without constraints in their supply chain. As far as what it looks like in the aftermarket, right? That’s cause that’s where I live is completely in the aftermarket.
We get to look at things after they failed and investigate the fine tune differences between them.
Allen Hall: What I’m trying to understand is if I buy a particular turbine and I pick a hundred of these things. The main bearings will not be from the same manufacturer on all 100 turbans. They are choosing two or three different manufacturers to provide those main bearings.
And even though the mechanical spec and even the lifetime spec and even the coding spec may be the same, the bearing itself is different from turban to turban. Why is that? And what does it matter?
Cory Mittleider: The biggest change, depending on how much is specified to your point some designs are build to print.
I think we talked about that on the blade bearings actually, right? Where a turbine manufacturer will take the full responsibility for geometries and hardnesses and finish surface finishes and material, the whole ball of wax and others are more meet the spec, have this material meet this surface hardness and, meet this fatigue life type of thing.
So depending on the Sarah, historically it’s been the latter, right? Here’s our lifetime goals. Here’s here’s our loading. Give us something that fits and achieves the lifetime. Yeah, to your point though Materials can be used differently from different manufacturers coatings on the raceways, on the rollers.
And this is something we actually saw a while ago on gearbox bearings as well. Gearboxes had an evolution of materials and coatings. And we’re starting to see some of that with main bearings. And true in most industries is that the OEMs tend to learn from the aftermarket as well, right? Learn some of those options because ultimately they want to buy the lowest cost product that meets the needs, the design requirements.
But it’s not until you get it out in the field to understand the things that outside of just the design requirements, but the real world effects of what’s going on. And some of those things are then fed back into the OEM cycle that yes, this change is worth a little bit of a cost premium when you buy the turbine.
So that you can have long term operational confidence.
Joel Saxum: We talked with R& D test systems not too long ago about this actually, basically testing bearings and how these large size bearings are one of the most difficult components to test because they are, the failure modes are so Like it takes so much force and so much effort to get to that failure mode that to make it happen in a lab setting is almost impossible.
So they’re getting to the stage where they’re doing some like hybrid testing where it’s yes, it’s on a bench, but we’re also involving some AI and machine learning algorithms from other things to try to get to that accelerated life test. What the reality is, because earlier in the conversation here, we’re talking about A 2, 500 pound bearing and all this steel.
That’s hard. If I have this one on my chair, right? So if I’m testing the one on my chair, I just put some weight in it and spin it around a bunch. And eventually I can get it to come apart. But with a, something like that, like it would take years of testing. So what ends up happening, like you say, is they have to wait for a little bit of runtime in the field and some feedback from SMEs like yourself to say, Hey, this is the things that we should fix for the next generation of turbines.
The difficult thing here is, the OEMs are learning lessons all through, they’ve been learning it forever. So take a OEM XYZ, they’ve, they’re on, model 58 of turbines by now. Hopefully they have some things figured out and which they do, but the difficult is as we continue to scale and rotor size so quickly these bearing sizes and the designs and the loads on them are all changing very rapidly.
I guess a question here for you guys is, you’re in the field you’re getting calls from operators. Hey, I’ve got this problem. Come and dissect it and tell me what I can do next. What are some of the fixes that you guys are working on for main bearings at Malloy?
Cory Mittleider: In the past, let’s say 12 years, there’s been a couple iterations of different attempts to fix the problems in the field.
And to your point the OEMs they do a good job, I think, of the sizing of the bearings. I wouldn’t suggest that the size is necessarily wrong because their core goal is to achieve a runtime. And that, that formula, that calculation to understand, here’s the applied loads, here’s how many revolutions it’s going to accrue here’s what the fatigue life looks like, raceway rolling contact fatigue life look like is pretty straightforward.
The thing that we learned from the field and is even really hard to learn on a test bench, is what are the other things? What’s happening in the real world, right? Because even the test bench, you still need to set up your test. If you’re setting up your test for rolling contact fatigue, you’re probably going to fall right in line with the calculations.
But you need to test these other things, environmental different loading than expected. Is there some feedback from the field that it’s different than what was thought to be? Are there other conditions? As we talk about main bearings. There’s some investigation going on right now around electrical discharge happening in main bearings.
Yes. They’re not solved today, right? These problems are where we live in the aftermarket. It’s where the operators that, that are taking control and self operating their turbines have opportunity. To learn and adapt. And that’s where the OEMs are taking feedback from the aftermarket as well.
Not in the real world installed, not just test benches.
Allen Hall: So how do you know you have main bearing problems? What’s the first indication? I’d like to ask
Cory Mittleider: people that when they tell me that they have failed the main brain. So it’s interesting. Main bearings are really slow, right? We’re talking RPM on some of these as the turbines get bigger.
So your traditional vibration. Signature it’s not impossible to see with condition monitoring tools like Vibration, but it doesn’t jump out as much as high speed bearings in a gearbox or generator, for example. Another thing that we do hear reports of is temperature as another feedback loop.
Unfortunately, temperature indication, if you’re generating a lot of heat, In a failing main burn, it’s probably pretty late stage.
Allen Hall: I thought a lot of times the key was just technicians hearing some grinding noises, but you’re saying you can actually detect it way earlier. If you’re looking
Cory Mittleider: for it, you might be able to.
You’re right. I’ve heard a lot of stories of the technician said it was growling type of thing or banging. But that’s, they have to be up there for that, right? That’s that personal exposure that doesn’t happen every day, every week even. Unfortunately, we’ve also heard reports of the turbine went offline because of an alarm.
And when the technicians do go up, the rollers have fallen out of the bearing. I’ve seen some of those pictures. So they aren’t, as well monitored or easy to detect early. And to Joel’s point, there is a huge load applied to them, right? The nice thing about the high speed bearings or gen bearings although they’re moving fast and it can be monitored with vibration tools.
They have a lot smaller load. They don’t have that a hundred plus thousand, a hundred thousand plus pound rotor assembly,
Joel Saxum: right? So if you’re to monitor a main bearing, would you look for. Rather than vibration or something because you know a lot of things they’re running at 6 to 10 RPMs or so 6 to 12 maybe on a smaller one.
Would you look for deformation? Or would you look for vibration?
Cory Mittleider: I think that’s what the operators are and service companies, the the condition monitoring service companies are improving. I understand that some of the CMS tools do have some, I don’t know what the right word is, machine learning type stuff some things that are helping them learn more with more data points, which is going to be really helpful for those operators.
From my position as a bearing person, not. Living in the monitoring world there’s things that an operator can’t control. Looking at it to your point is it a platform where we know there’s an extreme failure rate? Make sure that when you’re up there for your biannual maintenance is.
That you’re looking at it. Grease sampling is another idea, right? It does have its own challenges in providing consistent results. Grease sampling, bore scoping, both tools available. They do require that personal attention though. It’s not the remote monitoring. The remote monitoring is some have figured out the clues on their turbines that trigger.
The in person visit. I think both go hand in hand as far as monitoring goes.
Joel Saxum: Yeah. Cause from the vibe, from a vibration monitoring standpoint, like high speed, it’s a lot easier to pick up. You get that higher frequency and you can sense that, but the list will slower, lower thing. One of the solutions that comes to my mind, Alan, who I’ve talked with you about this one, is that sensing 360, they have the fiber optic sensing that will go right basically around the raceway.
And if that raceway starts to deform or move at all, You’d be able to see it or pick up on it. Now you’re going to have some natural movement in it, right? But you’re looking for that difference or the anomalies. Yeah, exactly that delta between what the baseline was and then what may be happening because I think at the end of the day, That’s what we’re starting to hear in the market is everybody wants a, they want a CMS solution for everything.
If they could be remote, if they could remotely have eyes and ears in that turbine, right? The less people they have to send up tower to climb, the better off the operations are more efficient operations are.
Cory Mittleider: And they can focus on the stuff that they’re there to do. PMs and address the problems that are qualified.
Joel Saxum: Yeah, fix the problems instead of just having to
Allen Hall: go up and look for them. So I want to get to the coding issue, and the one that has been discussed the most recently is the diamond like carbon coding. I understand what that is, generally speaking, but exactly what is it and why would I want to use that coating on my main bearing?
Cory Mittleider: Sure. Yeah. So we look back at the history of main bearing failures to 10, 12 years ago where DLC started to become popular. A lot of the main bearing failures had, excessive wear in the raceway, peeling damage specifically, I would call it. And that can be caused with poor lubrication environments, right?
The wind industry. It took advice from other industries. They didn’t, this DLC technology was not necessarily invented for wind it’s technology that existed before and was used successfully in other industries for similar failure modes. So it’s a tool in the toolbox and it was launched in wind and it’s done a pretty good job on a lot of applications really, right?
Now DLC. As far as what it is, it’s it’s a coating that’s applied to the roller. And this coating is actually extremely thin, right? It’s, we’re talking 2 3 microns, 2 3 thousandths of a millimeter. It’s really thin coating. You’re not gonna, you’re not gonna see the edge and feel it. It’s very thin coating.
It’s applied after the roller is produced, right? And then it’s assembled into this mainbrain. And the idea is that it’s really hard and it’s a different material than the steel of the raceways. So the dissimilar material and the high hardness are, where it has merit in trying to prevent that peeling damage in a poor lubrication environment.
That’s what it was used for in other industries. And that’s why it was used in wind.
Joel Saxum: So if we’re going to equate this to something that the everyday person can understand, is it like a, Like in your pots and pans, like a Teflon coating. Is it cause Teflon’s what’s slippery though.
That’s different. I guess it’s not the hardness. Is it more like anodizing in a sense as
Cory Mittleider: conversion coating? I’m glad you asked that question. So we talk about coatings in gearbox bearings too. And you said exactly right, Alan. Anodizing is converting a base material. Black oxide, as we look at gearbox burns, is converting a base material.
And that’s actually where DLC is different. No, it’s actually applied afterwards. So it’s put into this environment and in a, highly controlled environment in an oven and it’s deposited onto the roller surface. So it relies on a bond strength to attach it to that roller surface. So that’s where it is different when we talk about some other coatings in wind, for example, in black oxide.
Although we use the same terminology,
Allen Hall: there’s a functional difference there. And if you’re applying a material to an existing piece of steel, which is what you’re doing, in that case, the prep you perform on the steel and the cycle you put it through to apply that coating become. really critical, generally speaking.
Is that where that coding starts to have issues is in the application processes, or is it more in terms of the operational side? We’re just applying too much load to it. Sure. So you’re absolutely
Cory Mittleider: Prep process control. Because remember, this is the size of one roller. There’s all this surface area.
It’s five inches long. It’s a three inches diameter. There’s a ton of surface area on just one roller. Okay. There’s 60 of these. And all of them have to have really good adhesion of that coding for it to stay in place. Now what you’re asking is a really good question, right? Is what’s the.
Why isn’t it working anymore? I think is maybe is maybe part of the question, right? Because it did work really well. And I would continue to argue that it still does work in some applications. But we’ve learned in the last four or five years, I would say that some applications, it doesn’t offer the same solution that it has on other applications or other platforms.
So I, As much as we have explored alternate tools I by no means want to give the impression that I believe that DLC is bad or completely inadequate. So just so we’re clear, but no we’re actually not seeing a ton of problem with I’ll say the DLC necessarily coming off.
We don’t view the DLC on the rollers. To be the root cause of the failure. We see it to be how the failure manifests. So we’re seeing artifacts of other things and to be fair, since this is relatively young, there’s still some exploring going on on what that root cause is. There’s some operators, certainly the turbine manufacturers and bearing manufacturers that are investigating some of those root causes.
Now, at the same time as we have to investigate the root cause Bearings still need to be replaced. And if the bearing that’s being taken out now had certain characteristics, whether it’s DLC coding this cage guidance method, whatever it is, those are the variables that we have to look at changing to try.
and see what works, right? And that’s where we spend our time in the aftermarket. About five years ago now, there was one application that was failing main bearings pretty young. And then over some time, DLC was applied as a typical aftermarket solution. And what we’ve learned there is That’s one of the Turbine models that just putting DLC on didn’t offer the solution that it did on some of the previous platforms.
So we’ve looked into, what else can we do? And one of the tools in our toolbox, in Win specifically, is different materials. Alloys, heat treatments, both. Those are two independent things, alloys and heat treatments, as well as process control, cleanliness, quality control and that’s where we’ve turned to develop new tools as we collaborate with our customers and our manufacturers.
Allen Hall: Let me just dive into this for a minute. Cause I’ve, this is fascinating for an electrical engineer when we start talking about metals and how things pick all these loads. So we’ve got this really thin coating. It’s secondary applied. It is. As it’s been described to me, flaking off, and that gets into the grease, and then you have this basically diamond hard coating in the grease, which then just runs everywhere and starts to attack the bearing surface itself, and then it just cascades into bigger problems.
But we don’t really understand what drives that failure at the moment. We’re still trying to understand look at what the variables are. I know the one that I hear the most is, Electrical currents or lightning currents passing through the bearings. Now, electrical currents would make a lot of sense to me because that coding is non conductive.
Dam light coatings tend to be non conductive ish. And if you start pushing current through it or breaking that coding down electrically. I’ve seen it on airplane parts. It doesn’t go well for that coating, but there’s probably 50 other reasons why this coating could go bad.
Cory Mittleider: Yeah. Yeah. You’re, and you’re exactly right.
You’re you presented a couple of the pieces on some of the working theories that I’ve been a part of as well. Any bearing, no, no bearings like electricity. Let’s be honest, right? We learned this 15 years ago in the generator. We see in the gearbox in certain cases, we think that’s in the main bearing.
We’re probably not terribly surprised to see that may play a factor. Now to your point one of the things that we have seen and I know is being explored is if the DLC is damaged not even saying that it were to be inadequate in the first place, but just say it got damaged.
from some hard particle debris or environmental or whatever. Now maybe if there is electricity, it’s now even more concentrated in this spot. This is one of the conversations that we’ve been having. So does that lead to some of the domino effect? Where more of it is coming off. And is it where, is it flaking?
There may be some nomenclature disagreement depending on who you’re talking about but you’re also, you also bring up a really good point. Regardless, if it is coming off from damage, electrical, any reason whatsoever, if it’s coming off, you now have what is, remember the point was it’s high hardness.
Now you have this high hardness debris. in your grease and it can accelerate the wear when in fact it was supposed to reduce the wear rate.
Allen Hall: That just really makes me wonder what the solution has been over the last couple of months. I’ve heard differing opinions about it. Some of the operators are installing essentially the same bearing back into those turbines or choosing the other manufacturer for those bearings in the same turbine.
And occasionally you hear them talking about putting what I call bonding straps, electrical straps around to tie all the equipment in the cell together electrically to reduce the amount of impact it would have on the main bearings just as a bandage. I don’t know if there’s any, I have not seen any hard data on any of this, but it feels like there’s been a lot of ideas being thrown against the wall at the minute.
But we’re still trying to understand what the core issue is. Is that where you feel we
Cory Mittleider: are at? Yeah, I would agree. I’ve heard a lot of the same, and I’m going to tell you as a Bering guy, whatever you can do to stop electricity going through the Bering. Yeah, do that. Give it a desirable path. Don’t let it go through this undesirable path, right?
Let’s eliminate variables like that. That’s a great idea. But yeah there’s been a lot of talk about that. There’s minor differences between bearing manufacturers, which you hit on earlier, that maybe this bearing manufacturer had a little bit lower failure rates.
We have a better chance. Using that bearing manufacturer. And that’s what I alluded to earlier. Right now, we have a choice of, wait for people to test this, which could be a year, it could be three years or install a bearing in your turbine and run it. And that’s largely where we’re living right now is we know we have history on certain things.
We’ve learned quite well on certain things. This is what we feel we can do from a bearing technology point of view, but continue, we’re encouraging the operators to continue to explore this because if they need to work on grounding if that’s lightning, if that’s static, is it a induced current from other electrical systems in the turbine?
Keep exploring. Don’t think for a second that you’re going to put something in, walk away, and never come back.
Joel Saxum: Keep exploring. Cory, a question about you on this exploration part, and basically, because WeatherGuard here, we’re in the same boat, right? We’re always trying to get as much data as we can to put together to, because answers are driven from data, right?
We can have anecdotal thoughts about what’s happening, but as soon as we start to, Really build a track record of a certain L, like for us, it’s a certain LPS system versus a, geography and environment operates in these kinds of things. We can start to get some really good insights of what’s happening in the field.
Are you guys, so at Malloy, do you guys keep like a database of, these are the ones that we see that are good. This is what’s the failure modes we see.
Cory Mittleider: So on a per platform basis our team has a pretty good knowledge of this platform, fails from this method failure mode rather. Early failure life might be X years, average failure life might be this, we hear some scuttlebutt about if there’s acknowledged technical issues, publications from an OEM type of thing which Alan alluded to earlier, of course. So from an app a turbine model point of view. We have a pretty good idea. And I like what you said, Joel. One thing that we like to encourage operators to do as we talk to them and we’re launching new solutions is validation.
Validation is the most important part of this evolution. And you put in a new bearing, generator, gearbox, blade, main, all of it. Or all the other problems that operators are trying to solve. Whatever you install for a fix, it’s always based around really good ideas. And we generally agree on the scientific idea on why we think it should work, but you got to go validate, right?
And that’s not a light task. I get it, right? There’s a time commitment. There’s a labor commitment. There’s just plain a desk time commitment to trending that data, understanding that data. But that’s how. Those operators are going to be able to come out of that successful and there’s it is a hard task, admittedly and some are really dedicated to doing it and it shows that they do really well.
Joel Saxum: Yeah, I think that the, it’s a heavy lift, but as an industry, No matter what you’re dealing with, whether it’s bearings, lightning, blade problems, gearbox issues, whatever it may be. If we’re not doing that as a collective team, then we’re not moving the industry forward.
Cory Mittleider: And that’s where our role is.
I feel at Malloy, is working with multiple operators. Across multiple platforms and accumulating this knowledge across 12 plus years now on these failure modes on the different applications. And one of the things I touched on it already is we’ve had a lot of success for 15 years on gearbox bearing failures.
And. The way that those were solved were not actually with a coating applied to the rollers. It was actually applied a lot of the solutions that we have developed are based on material changes, right? So that’s alloys, that’s process cleanliness that, Does some manufacturers have higher standards than just what ISO sets out for manufacturing standards and heat treatments to boot, and a combination of all those things are important.
So when we looked at this main bearing problem, for example five years ago, although coatings on the roller was widely accepted in the industry, we wanted to look at some other solutions. And how can we inject some of these other tools. Because even at the time, this first one we looked at five years ago.
It looked a little different than the historical main bearing failures. So we said we should treat it differently, right? So we took this different material and different heat treatment that was very successful in, in, WEC problems and debris initiated issues in gearbox, high speeds, planetaries, intermediate bearings and said, what we’re seeing, this might be a really good fit for main bearings as well.
Allen Hall: If I’m a operator with a warranty and I’m trying to figure this out and I know generally that I probably have this issue, what should I be doing right now in the warranty period? So when I come off warranty, I have some sort of track record.
Cory Mittleider: Yeah, that’s a great question. Cause you don’t have too much control probably in that warranty period.
Other people are in control. Now, as I understand it, you have access. to go get what you want. So I think getting informed both on your situation because unfortunately we have heard that a warranty ends and operators have no idea what the history was. Failure rate, the failure mode, whether it was replaced at all or once or twice.
So Collection of information on your fleet is probably a really good piece. Reach out, give us a call, talk to us about what our experience has been. Being prepared to make that decision, I think is the other side of that coin, right? Not just waiting until warranty’s up.
Now we gotta, now we gotta go explore the options. Adjusting, anybody would do that but reiterating the importance of being prepared. All right, we can talk about what’s available, what our experiences are and ultimately we’re always learning more from the next operator that’s talking to us as well.
So I view our role as a bit aggregating in the operator’s experiences, the service provider’s experiences to inform how we’re, Launching new barracks to solve those problems.
Allen Hall: Can Malloy help develop that plan? Just because you have all that deep knowledge of other operators. Is that something that you can assist an operator with?
Is here’s the plan you should be taking. This is the ones that have had success.
Cory Mittleider: Ultimately we would probably give some recommendations. Look for this. Look at your bore scopes. This is what it, this is what you can look for from what the picture would look like maybe some response.
I can’t say we’ve developed comprehensive step by step plans by any means, but a good conversation on what to watch for I think is the first step in developing that plan.
Allen Hall: I think a lot of operators are in that boat at the minute. They don’t know what to look for and they don’t have any plan to attack it.
They’ve seen the cranes on site. They’ve seen some main bearings being replaced. under warranty, they don’t have all the details, and yet, in a year or so, they’re probably going to own all those assets, and how do they start tracking it now? If you’re out there, you better get a hold of Cory at Malloy Win, because that’s where the answers lie.
Cory, this has been a fascinating discussion. I love Talking Bearings with you because you’re just so deep into it. I love that it’s almost like a mystery. It always has to be solved. It’s a complicated problem. It’s probably one of the most complicated problems in WIND at the moment. And if someone wants to reach out to you, how do they connect with you?
Cory Mittleider: I’m active on LinkedIn. My, my phone numbers is on the website, but it’s 605 357 1076. Don’t hesitate to call and ask about any bearings. I like talking about bearings with everyone. We have our say general inbox, which is wind@malloyelectric.com. That’s a good entry point as well, because it’s not just me.
And I got to emphasize that, we’ve got folks in the field that are out collecting some of this information as it happens. Basically learning more about it every single day, we’ve got an inside team of product champions that really know those applications down to the detail that I work with we all work together, obviously on a daily basis.
So there’s several of us. That depending on your, the operator’s situation today, what they know, what they don’t know, that could help guide for, what is the next step? Is it main bearings? Is it what your bore scopes look like? Is it gearbox bearing? Can we start with a nameplate picture to understand what that application is exactly to support you in that way?
Allen Hall: Everybody out there listening go to malloywind.com. And look at all the information they have there. They have terrific online resources about main bearings, gearbox bearings, pitch bearings, it’s all there. All the failure modes are shown on there. They have great color photos and a description of what has happened to them.
Tremendous resource. Cory, thank you so much for being on the podcast and we’re going to have you back again because there’s so many Gearbox problems. I want to get to gearbox bearings next on my list. So we got to invite you back.
Cory Mittleider: Yeah, absolutely I’d love to talk about gearbox bearings, there’s definitely a lot of activity around blade bearing and main bearing failure, but it doesn’t mean the gearbox bearings have gone away, right?
There’s still some of the existing fleet out there that can be addressed and there’s always new stuff to learn there as well. So yeah, I’d love to. Thanks for having me.