The Uptime Wind Energy Podcast
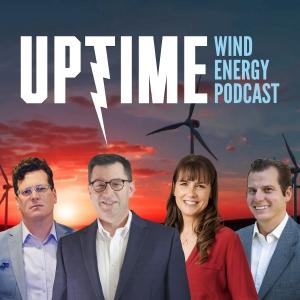
Vestas Offshore Blade Repair, Siemens Gamesa Floating Power Optimization
This week on Uptime Power-Up we discuss Vestas’ offshore blade repair method, Siemens Gamesa’s way of optimizing power production for floating turbines, and a fun way for kid’s to collect their Halloween candy.
ign up now for Uptime Tech News, our weekly email update on all things wind technology. This episode is sponsored by Weather Guard Lightning Tech. Learn more about Weather Guard’s StrikeTape Wind Turbine LPS retrofit. Follow the show on Facebook, YouTube, Twitter, Linkedin and visit Weather Guard on the web. And subscribe to Rosemary Barnes’ YouTube channel here. Have a question we can answer on the show? Email us!
Pardalote Consulting – https://www.pardaloteconsulting.com
Weather Guard Lightning Tech – www.weatherguardwind.com
Intelstor – https://www.intelstor.com
Wind Energy O&M Australia Conference – https://www.windaustralia.com
Allen Hall: Welcome to Power Up, the Uptime Podcast focused on the new hot off the press technology that can change the world. Follow along with me, Allen Hall, and IntelStor’s Phil Totaro, as we discuss the weird, the wild, and the game changing ideas that will charge your energy future.
All right, our first idea is from our friends at Vestas, and it is a a relatively sophisticated system for handling wind turned blades during maintenance, particularly offshore. And if you think about how you try to manipulate a blade offshore to do repair work on it, it’s not, it’s not easy to do that on the deck of a ship.
So the, the concept is you take a crane, get the blade off the turbine, you move it down to the deck of the ship and it sits in these cradles. And they move it from the support cradles to a third device, which allows the blade to rotate. And they could slide it into a shelter that’s built up on deck so you can actually repair the blade without getting wet or, or too hot or too cold, probably, probably too cold in most cases which is a really difficult task to do and Vestas, Phil, has, has come up with a really unique idea on how to manage this.
Philip Totaro: Yeah, this, this one is very Interesting, because we have comparable systems to this onshore, but it’s obviously a lot harder to implement offshore. So, for instance, having the tent, it’s going to sound like the stupidest thing ever, just like having a tent around the blade to be able to, protect the, the area that you’re scarfing out or whatever, if you’re doing that kind of a repair.
That’s, that’s important. That’s an important consideration. And while it’s obviously possible to do that today offshore the fact that you would have to use the crane to, place and pick or use the, um, the fixtures that are attached to the crane to rotate the blade and then lower it into the cradle.
That can be complicated and time consuming and expensive to do with the on board crane on the vessel. So, the fact that you can lower it into this rotating, we’ll call it a rotating, cradle. Or fixture and the fact that, they’ve, they’ve got this capability to be able to put up the, the, tarp or tent to be able to protect the blade to, to do the repairs, it’s, it’s really helpful and, and gives you potentially improved quality in, in the repairs pretty much at the same level that you would get from doing it onshore.
Joel Saxum: Yeah, I like the idea here that we’re basically taking a concept that we know if you’ve seen major blade repairs on the ground, a lot of times a temporary tent is put up so that you can work in the wind, rain, snow, cold, whatever it may be. Doing the same thing here offshore. Important for operations and maintenance for the future as we have to start doing some, larger and larger repairs to these blades.
But a big important part of this is if anybody that’s been involved in lifting operations, you want to minimize the amount of times that you actually touch these blades. When you talk about installing them offshore, you build them in the factory, you move them from the factory to the yard, then you move them from the yard to maybe Keyside.
If the factory’s close to the, to the water, then it goes from keyside, another crane puts it on the boat, and then the vessel might, might be a barge, and then the barge goes out to the working rig, and then they have to pick it up. And every time you pick a blade with a crane or slings or other kind of fixtures.
You have a risk for damaging it. So being able to drop it on deck and move it and manipulate it however you need to, to do repairs without having to re pick, re pick, re pick, especially in a Marine environment is super important. So I like this idea. I think it’ll, you’ll see it in the future, but in specialized cases.
Allen Hall: Yeah, it’s a great idea. Our next is up from Siemens, Gamesa. And this one has to do what they call ride through, right? So the equipment on a wind turbine has to handle the grid voltage fluctuations. In order to do that, a lot of the equipment that is on a wind turbine has to be over designed, have special capabilities to handle grid voltage fluctuations.
And that leads to additional costs and complexity into the equipment. Well, the Siemens idea is to take a transformer, basically a variable transformer, an auxiliary transformer, and have a quote unquote electronic tap, and a transformer converts electricity from one form into another, simply said. It can raise or lower the voltage, same thing with current.
So they’re using semiconductors. So you’ve got a primary and a secondary and a transformer. You can adjust the amount of turns in a primary or a secondary using semiconductors as a switch. So in a voltage fluctuation case, all the auxiliary equipment in the turbine won’t see it because this auxiliary transformer with these semiconductors are going to stabilize the voltage within two AC cycles.
Which is really quick, and that allows you to use much simpler, lower cost equipment in the turbine field. This idea makes infinite sense to me. Depending on what the cost is for this auxiliary transformer with all these semiconductor switches, it could be a lot less expensive.
Philip Totaro: Yeah, and I think the impetus behind this was for larger onshore turbines.
Particularly in markets where you’ve got a need to provide, well, a lot of fluctuation in, in grid voltage and frequency, but also where you may have to be able to provide ancillary services quickly. And so this technology will come in really handy with that, and I, I, it’s funny because every week these, these patents publish and, and we’re reading them at Intel Store to, to extract whatever technology intelligence we can get out of them or just catalog the, the, 60, 000 plus patents that I think we’ve cataloged over the last 14 years now.
There are ones like this that actually stand out a little bit because it, it’s not the most revolutionary patent or technology in the world, but it’s something that’s actually going to potentially impact cost and improve function. of a wind turbine. And so we, we like ideas like this and we want to see more ideas like this.
Joel Saxum: Allen and I talked with R& D test systems regularly and they have shared with us some of the testing mechanisms that they have to basically introduce grid problems backwards into turbines, into generators, into control systems and all this, to make sure that they work. So this is a system that Gets you that certification that gets you to that level.
Then it can handle that. But in like, like Phil said, a more cost effective way. And one of the things I want to focus on here is the speed of which it happens. So when it talks about two AC cycles, okay, if we’re in the United States, usually an AC you’re cycling, it’s, or your power’s at 60 Hertz. So that means two of those 60 Hertz.
So at one 30th of a second, this thing can find the issue. Correct that issue. Or if you’re in the European Union and it’s you’re at 50 hertz, then it’s in 1 25th of a second. That’s how fast these things will operate to make sure that that grid interruption, that grid voltage problem or current problem doesn’t make it back up into the turbine to actually damage something.
So pretty impressive there. And doing it in a way that saves costs. That’s the kind of stuff that we need within the wind industry to make us more competitive, or to make it more competitive versus other forms of energy generation.
Allen Hall: Our last fun idea. Or our last idea of the week is a fun idea regarding Halloween and a Halloween candy container.
And if you’ve just had the kids arrive to your house, usually they have some sort of bag or a bucket that they want you to throw some candy into. Well, this is a novel idea because this is sort of a hands free containment device that is worn on the child’s back. So it’s like a, a clear backpack. But on top of that, there’s a chute that comes from the backpack forward with like a little character with an open end, like a I don’t know, a monkey with his mouth open or an elephant with his mouth open.
So you actually throw the candy into this little animal mouth and it deposits back in the backpack. So the kid is hands free. I don’t know why the kid would have to be hands free to do this, but the concept is, well, they’re carrying a flashlight, they may be holding someone else’s hand. It’s a safety feature device.
Ed, Phil, it’s also fun for the people that get to throw candy at this kid and try to hit the target, I’d
Philip Totaro: assume. Well, hopefully they’re not just chuck chucking it at them, but I don’t think that’s almost as happy.
Allen Hall: It’s all those little tiny ones, not those big full candy bars that you give out, Phil.
Philip Totaro: Are you a full size candy bar household, Phil? Yes, absolutely. If if we’re doing it, we’re not we’re not miniature or anything. I mean, I’m not from Texas, but every, everything is bigger there, and, and, as it should be. I think this
Joel Saxum: thing would work perfect for, I like the idea for berry picking. I do that whenever I’m home up in Wisconsin in the summertime, I’ll bit raspberries, blackberries, blueberries, and if I had this backpack on, it’d just boop, boop.
That would keep me from eating them the whole time out of a bucket.