The Uptime Wind Energy Podcast
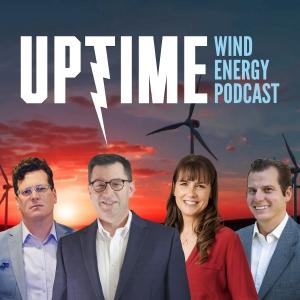
Siemens Gamesa Blade Closeout Plates, Vestas & ZF Plastic Torque Tube
This week on Power-Up, we discuss Siemens Gamesa’s method for stabilizing wind turbine blades by installing closeout plates. Then Vestas and ZF’s idea to replace the metal torque tube in the gearbox with a plastic piece, protecting from current. And finally, an Enercon patent for painting blades in an ombre pattern to lessen visual disturbances.
Sign up now for Uptime Tech News, our weekly email update on all things wind technology. This episode is sponsored by Weather Guard Lightning Tech. Learn more about Weather Guard’s StrikeTape Wind Turbine LPS retrofit. Follow the show on Facebook, YouTube, Twitter, Linkedin and visit Weather Guard on the web. And subscribe to Rosemary Barnes’ YouTube channel here. Have a question we can answer on the show? Email us!
Pardalote Consulting – https://www.pardaloteconsulting.com
Weather Guard Lightning Tech – www.weatherguardwind.com
Intelstor – https://www.intelstor.com
Wind Energy O&M Australia Conference – https://www.windaustralia.com
Allen Hall: Welcome to Power Up, the uptime podcast focused on the new, hot off the press technology that can change the world. Follow along with me, Allen Hall, and IntelStor’s Phil Totaro, as we discuss the weird, the wild, and the game changing ideas that will charge your energy future.
All right guys, our first idea is what’s turbine blades, and it’s an idea from Siemens Gamesa, and it In patent form, as they describe it here, it’s what they call a novel approach to stabilizing wind turbine blades without the need for traditional trailing edge beam designs. But what they’re really doing is they’re installing closeout plates on the, between the aft spar and the trailing edge.
So, This idea is pretty much making a wind turbine blade look a lot like an airplane wing, Phil.
Philip Totaro: Yeah, especially like an older style airplane wing. So those that aren’t familiar with the closeout plate, it’s like a rib design that has this, vertical element at different longitudinal locations throughout the Kind of the, the max cord section and in inner portion with the exception of like the, the immediate root section of the blade.
But it’s, it’s interesting to me, besides just the, the general concept here, the timing of this was fascinating to me because they filed for this patent back in April of 2024. And the patent has now published in October and the question Is, is this a potential fix to a problem?
Is this what’s this really doing?
Allen Hall: Well, it’s stopping torsion is what it’s doing, Phil. It’s preventing the blade from twisting too much, which makes me think of a couple of blades that I’m familiar with that have torsion problems. Joel?
Joel Saxum: Well, if you look at the image here, so I’ve crawled around in quite a few blades doing RCA’s and failures, and you’re always looking for failure modes, so you start getting into a different mindset of when you’re crawling around in them.
But In multiple blades that I’ve been in, there’s an, what looks like an extra shear web in the, in some of like the max cord region and stuff like that, just to make sure that you keep that part of the shell supported and then that structure rigid there. And in this design, they’re removing that extra shear web and putting these closeout plates in there.
And it is exactly like you guys say, the design looks like an airplane wing with a bunch of ribs in it. And to me, in my mind I’m, I’m not a, trained structural engineer, but from engineering principles and just kind of physics and forces and a little bit of knowledge there, this to me looks like it could solve some, some pretty big issues.
However, in maintenance, that makes things a little bit more difficult because maintenance and construction, because it’s harder to place these things in construction, of course, and to get them right. We already sometimes have a hard enough time placing shear webs and getting those right. Now you’re adding perpendicular components and multiple of them.
So that makes that a little bit more difficult. And then, you’re checking more glue, glue lines and bond lines and these kinds of things. But then, of course, what we’ve seen in the last two to four years and wind and the explosion of internal inspections. The only way you’re going to do an internal inspection on one of these blades is, from a structured standpoint, is with like an Elios drone or something like that, if they can fit through the holes in the closeout panels.
But you’re not going to do it with a crawler anymore. So there’s some like manufacturing things, some trade offs with O& M. However, to me, it looks like if you could get this right, you might end up with some more structurally rigid blades. That could, could alleviate some of these cracking and, and blade failure issues we have.
Allen Hall: Our next idea is from Zedaph Windpower and Vestas Wind. And it has to do with gearboxes and preventing electrical Currents, stray electrical currents from damaging the gearboxes, the drivetrain, and causing havoc and warranty claims and all kinds of other things. As you, as you pass through a gearbox, there’s usually a tube that sits in the middle of this where you can put hydraulics or electrical signals or whatever you want through them.
However, when you put a piece of metal in this, in this drivetrain, it provides a pathway for stray currents to flow and thereby causing Damage to the gears and the bearings. And this idea from ZF Investus, takes that tube and makes it out of plastic. Seems like a really simple change, Phil.
Philip Totaro: It is, but what’s interesting about it is a couple of things.
First, not only that, that kind of physical interpretation of this idea to just have a, a portion of what would otherwise be a, a metallic but non structural component just changed over to plastic, it might seem like a really simple, stupid idea. But I gotta be honest, like, a lot of times, those are the things that A, are gonna help you with maintenance or otherwise solve a problem that’s being caused by the fact that you were using the metal in the first place.
The other aspect of this is the fact that, because this is a joint, patent application between ZF and Vestas. This is potentially technology that’s already being used on the large onshore machines. We’re talking about the V162, V172 kind of product families or the large offshore machines like the V236 and, and above.
So, the fact that we know that there’s a commercial tie in between ZF and Vestas on those those gearboxes means that we hope to be able to see this kind of technology used in real life applications soon.
Joel Saxum: Yeah, Allen and I being part of the lightning world, and of course, Allen being an electrical engineer, we hear about a lot of problems within turbines with stray voltage, whether it’s static buildup or stray voltage coming from the turbine itself, and disregard the idea of even lightning moving around.
They can wreak havoc on electronics. They can throw alarms that you don’t want to see. They can ruin coatings. They can do all kinds of things. So Vestas and ZF looking at, Fixing this problem. Maybe it’s something that they’ve learned and lesson learned from or something that they’re foreseeing good on them.
And it’s good to see innovations like this making their way into the market.
Allen Hall: All right. Our next patent idea is on a rotor blade and, and painting the rotor blade, different colors to reduce the visual impact. Now this is really fascinating. So the concept goes like this. You, you take, you paint a part near the hub, a lighter color.
color. And then as you move out towards the tip, you paint that a darker color, like the color of the sky. So it’s blue or maybe even the color of the ground, green or brown to, to match the landscape. So when the rotor is spinning, this color gradation creates an optical illusion that makes the overall rotor diameter appear about 10 to 20 percent smaller than its actual size.
Now, the only thing I can compare this to, Phil, is when you walk into a home and they have Two differently painted colored walls and the shape of the room changes. It’s an optical illusion of sorts. It sounds like that’s what they’re headed for in this painting scheme for wind turbine blades.
Philip Totaro: It is. And this, so for those that aren’t familiar, this is a patent from Enercon.
This was originally filed in Germany in October 20th, 1999. So we’re certainly talking about what is now an expired patent. So if other companies wanted to be able to use this technology, they could. What’s interesting about this and the other Enercon patent about, they, they literally patented painting the wind turbine tower different shades of green, and you may have seen this if you’ve seen, some of the wind farms in Germany or Austria or elsewhere in, in Europe where they’ve actually implemented this technology it was part of being a social acceptance of wind turbines.
And that’s, that’s originally what the, the concept was behind it. Why they patented it is something I still kind of question to this day. And the reason we’re talking about something that’s an expired patent in the first place is, we, we have the luxury to be able to, look back and say over the last, 20 plus years has this really been a competitive differentiator for a company like Enercon selling their wind turbines?
I’d have to say no. So the, the question of whether or not you want to spend, and, and companies will do this, they’ll spend upwards of 400, 000 on a single patent over the lifetime of the patent for all the countries that you could potentially go file your patent in. We’re talking about, major international markets where you’re going to sell wind turbines.
That’s the U S throughout the EU jurisdictions like Brazil, Japan, China, Australia, et cetera. Canada, that, other major markets where you’re, you’re gonna sell your wind turbines, you’re gonna spend 400 grand over the lifetime of the patent to get a patent. So, was this 400 grand well spent?
I’d probably have to say maybe not because while it may have helped in a handful of cases with social acceptance, I, it hasn’t really served as a significant competitive differentiator for for this company.
Joel Saxum: I would say if they got this, if it took cost of 400 grand and they got to install one more turbine from it, it was worth it.
However, I have never seen one that’s painted like this and I don’t believe anybody I know has ever seen one painted like this. So I don’t think it’s like exactly like you say, Phil, it caught on or it made any value. The interesting thing in this patent, I’m looking at a section of it and I’m going to read it right from the patent so you can all listen.
That it says it goes sentence, sentence, sentence. That is to be achieved in particular in respect of installations with large rotor diameters. And in parentheses, large rotor diameters in 2000 or 99 when this thing was filed was larger than 40
Philip Totaro: meters. Well, considering the fact that we now have the, the Chinese have literally just last week at their China wind power event just proposed a 25 megawatt offshore wind turbine with a 304 meter rotor.
So, I think we’re, we’re beyond the need for painting the tips.