The Uptime Wind Energy Podcast
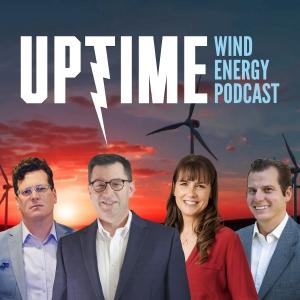
Stopping the Data Chaos: The Million-Dollar Challenge SkySpecs is Solving
In this episode, Allen and Joel speak with Tom Brady, CTO of SkySpecs, to discuss the challenges and solutions in managing multiple data sources in wind farm operations. Brady explores how SkySpecs is revolutionizing wind turbine maintenance through integrated data analytics, advanced drone technology, and AI-driven decision-making tools, while sharing a glimpse into exciting R&D developments that promise to transform the industry’s approach to predictive maintenance.
Sign up now for Uptime Tech News, our weekly email update on all things wind technology. This episode is sponsored by Weather Guard Lightning Tech. Learn more about Weather Guard’s StrikeTape Wind Turbine LPS retrofit. Follow the show on Facebook, YouTube, Twitter, Linkedin and visit Weather Guard on the web. And subscribe to Rosemary Barnes’ YouTube channel here. Have a question we can answer on the show? Email us!
Pardalote Consulting – https://www.pardaloteconsulting.com
Weather Guard Lightning Tech – www.weatherguardwind.com
Intelstor – https://www.intelstor.com
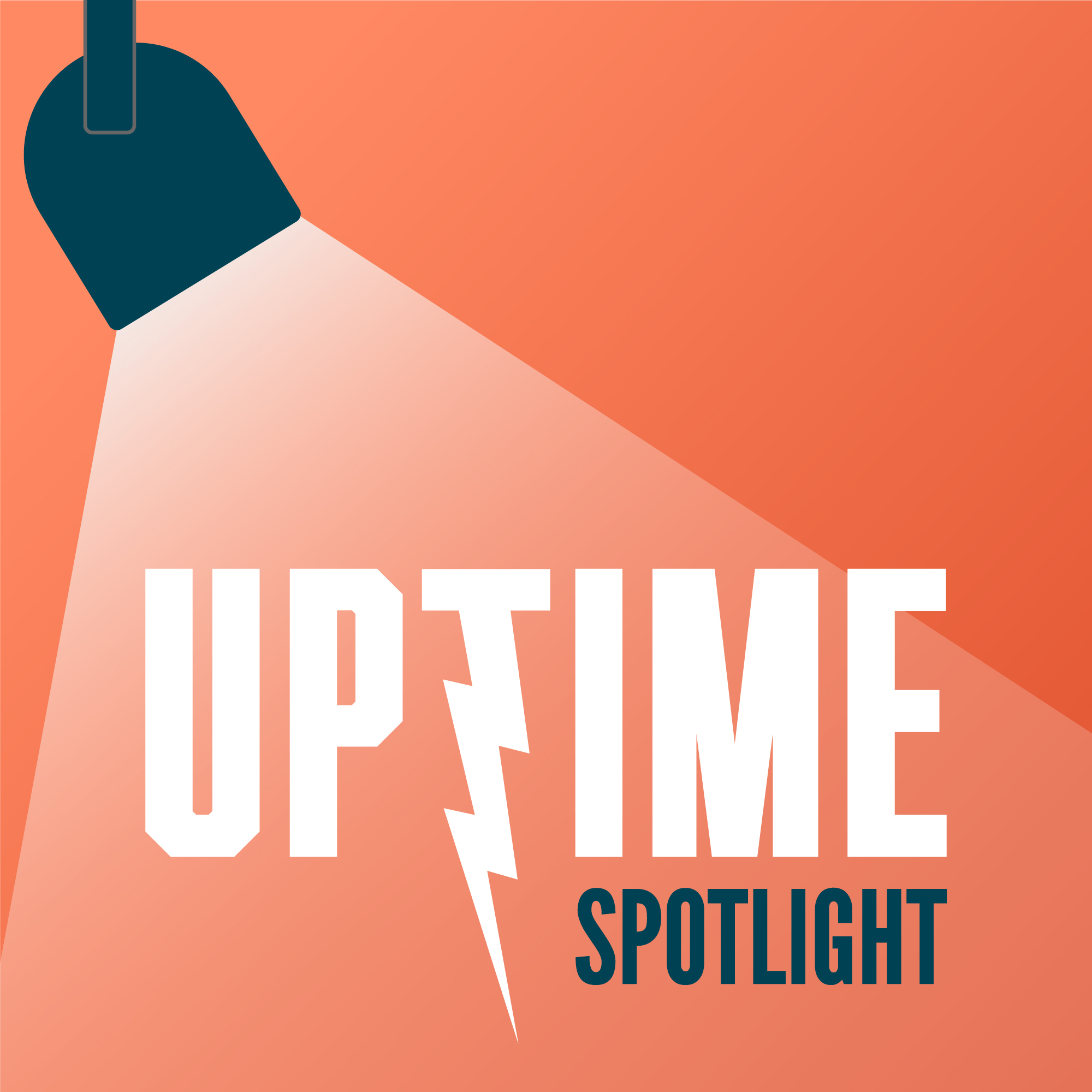
Welcome to Uptime Spotlight. Shining light on wind energy’s brightest innovators. This is the progress powering tomorrow.
Allen Hall: Welcome to the Uptime Wind Energy Podcast. I’m your host, Allen Hall, along with my co host, Joel Saxum. We’re going to discuss a challenge that’s becoming increasingly critical in our data driven world, managing and integrating data from multiple sources in wind farm operations. In the age of smart turbines and lot sensors, wind farm operators are awash in data.
But here’s the catch. According to a recent industry survey, a staggering 54 percent of operators find managing multiple data sources to be difficult or very difficult. It’s like trying to conduct an orchestra where every instrument is playing from a different sheet of music. In today’s episode, we’ll be diving into this data dilemma.
We’ll explore why integrating data from various sources is so challenging, how it impacts decision making and operational efficiency, And, most importantly, what innovative solutions are emerging to tackle this issue. But that’s not all. We are also pulling back the curtain on some exciting R& D projects at SkySpecs that promise to revolutionize how we handle data in the wind energy sectors.
From advanced analytics to machine learning, we’ll get a glimpse of the future of wind farm data management. Our guest is Tom Brady, the CTO at SkySpecs. And Tom leads the technology vision and development at SkySpecs, overseeing the creation of innovative solutions for the wind energy industry. His expertise in managing complex data systems and R& D initiatives is crucial to addressing the challenges of multi source data management in wind farms.
Tom, welcome to the program.
Tom Brady: Glad to be here. Thank you for having me.
Allen Hall: So we have a lot to discuss actually. So we just got the grand tour of the Sky Specs R& D facility. Both facilities. This is true. We were in the offices also this morning and, we meet with operators all the time. And one of the things they’ll tell us is, or especially if he asked them for data, they go, yeah, we have it, but I don’t know how to access it.
Or I’m not sure what system it’s in. Let me go figure it out. Let me call somebody see if they can figure out where the data is. Or I have too many logins. Oh, absolutely. That’s a common one. Yeah. So what is happening right now? Is it just because we’re just getting so much information? We just lost track of it.
We don’t have any place to put it. We’re using Google Drive still. Some of the operators are using Google Drive, which is insane to me. Is that where we are in the wind industry?
Tom Brady: I would say all of the above. Winding back a little bit to when we got started in the industry back in 2016, we launched our autonomous drone inspection or blade inspection product.
And prior to us being on the scenes we did our typical market discovery, customer discovery, learning a little bit about the market that we were about to try to enter and something that we saw was common across the board was exactly as you say, I’ve got folder folders in Google drive folders in box.
And, maybe I’ve got I’ve got something like maybe I’m organizing by site, turbine, inspection date, blade, and then, radial distance. That might be how I’m organizing my inspection data. We, a couple of times, tried to ask our customers, Okay, can you show me the data from last year versus this year?
Has anything gotten any worse? And, I’m like, It wasn’t even a question that anyone was thinking about, at least at the time. There’s also this backdrop of increasing blade issues and blades becoming an even more important operations and maintenance concern. But I would say it wasn’t even a thing back then to try to answer those kinds of questions.
So I think that is one part of it. There weren’t, without now we’re seeing more of these modern data systems that can actually relate. And answer those questions in different ways that customers want to ask them. So that’s a big part of it. And I think the other big part of it, which we probably don’t talk enough about is that it’s really hard to compare apples to apples when I’m talking about, maybe it’s a drive train related issue or a blade related issue or performance related issue.
So all of these systems exist in these different silos. And you talked about the, I have too many logins. Like I’m thinking about who is that asset manager? Who is that person that cares about, All of the issues, not just the blades, not just the drivetrains, not just the performance, but all of it holistically and I personally can’t imagine what that must be like for them because there is no, there’s not a there’s not a common way of speaking about maintenance issues or asset health risks that is common among all of those different data sources or main components.
So I think that, that’s a big one for me and that’s one that. Drives a lot of our strategy, especially as it relates to our acquisition strategy. You may have seen in the last three years, we’ve acquired, a CMS company. We’ve acquired a finance class management company and a performance company.
And that’s what we have our eye on is how can we actually tell a cohesive story and drive that insight to action across all of these different main component areas?
Joel Saxum: At the simplest level let’s dive down and do just a blade problem because I’ve seen this before, right? At the simplest level and internal damage.
And an external damage many times are related. Absolutely. But unless you have a decent data set, that is a, catalog data set, you can’t do that. You can’t look at them because what you’re saying about the, how you guys got into, the blade inspections with autonomous drones, that was really the first, really good data structured inspections where you could call up on, Hey, I would like to look at this radius on the leading edge of these blades.
Okay, so you guys started that as a cascade and everybody else has followed suit and now it’s become normal in the industry and that’s fantastic. But now even two years ago, internal inspections, people were not looking as it was more of there’s technicians in there, they have a camera and they’re pulling a tape measure and they think they’re about four, 14 meters in the blade and they got a picture.
Am I looking at the trailing edge or what bond line is that? But now you see that how those things could be related. So when we talk about large data sets, Now you’re talking, you’re getting even more in depth saying there may be a way where we can tie CMS data to blade damage data or something of that sort.
Absolutely. But you need to be speaking the same language. This is a thing I always go back to language wise is what people don’t understand, they say the Wi Fi. Actually, Wi Fi is a common language. And that’s why everything can speak in it. And that’s something that we see every day, but not a lot of people realize if you could put that together for data, which is what you guys are starting to do to amalgamate all these different data sources and data types into one system, you can really get a holistic view of what could be happening to your blades or anything else for that matter.
Tom Brady: Yeah. I think there’s a lot of work to be done in that, at the intersection of data, exactly. As you say I’m particularly interested in some of the work that’s ongoing both. Projects that we’re working on, but also out in the industry on things like blade sensing. So what can we do to actually drive the increased frequency or the the capability of continuously monitoring blades, I think is really exciting.
Overlaying blade issues with SCADA issues, or excuse me, overlaying blade issues with SCADA data. Yeah. I’m very curious to say, or to see what kind of information we can derive about, Why blade damages propagate? Can we say something about how blades are loaded and therefore how they propagate?
I think we’re starting to see glimpses of that in some of our research and development, but there’s a lot of work to do. I think that’s a really exciting area for future devs.
Allen Hall: So what are those things that you’re finding right now? Just by, for just a top level look at connecting data sources together, are you realizing, yeah, there is a connection between this gearbox and that blade having a problem?
Are those sort of Concepts and ideas and problems starting to rise to the top a little bit more. It’s an integrated system more than just individual components.
Tom Brady: I would say right now we’re at more of the stage of having the data backing to support the things that some experts probably already had intuitions about.
We don’t need to get into specific makes and models and the serial issues that are prevalent among them, but I We have a number of blade engineers on our staff and they act as consultants, both internally and for our customers at times, just to advise on their maintenance strategy.
And they know from their experience that, a certain blade maker or a certain blade model is, if you see an issue at this spot, you better fix that thing very quickly. We’re now seeing in data what happens if you don’t, which is really, I think, really exciting because now it’s not only that that tribal knowledge or that, that expertise that they’ve built up, but there’s, we also have data to, to back it up and say, with a 10 percent probability, we’ve seen this thing that you’re calling a Cat 4 now turn into a Cat 5 the following year.
And that is extremely powerful in terms of helping owners start to inform their maintenance strategy. When you can say. Okay, I have this set of issues. Yes, they’re very serious right now, but also I only have budget to fix the top 10. So maybe I can use that to say what I prioritize first and what I can let run.
Joel Saxum: At the end of the day, an operator wants to be told they would rather not look at inspections. They want to be told what to do, right? And if you can back that up with analytics and data, then that’s huge, right? Like I’ve seen post mortem studies, I say post mortem blade failures. Yeah. Where you can see a crack propagate.
At the time of failure with a pitch walk off, right? Where if you have because that blade is trying to stay in line with pitching to the other blades, then that crack develops. It has to pitch more and more as that blade is failing. And so that can be done, right? But that’s in an extreme case, if we can get closer and closer to doing that.
And it’s it’s in minutia, right? There’s so many small little details, small, something that you could find in some of the SCADA data or some other CMS data to show this. But. What it’s really going to take is someone to tackle that project. And I don’t think that we’ve seen, we, we, Alan and I keep pretty close tabs on what’s going on at DTU and NREL and Sandia and Oak Ridge and all these other laboratories and universities across the world.
I haven’t seen anybody academically taking that project on yet. But I think it could be very powerful. Like you say, for lowering the cost of energy across the board. Absolutely.
Allen Hall: How much money do you think is on the table for a particular operator, a midsize operator in the States?
How much money do you think they’re losing from not connecting those data sources together?
Tom Brady: Oh, that’s a great question. I guess let’s think in terms of, orders of magnitude for typical blade budgets. I’ve seen that for a medium to large size operator, you might see a blade budget in the realm of call it.
I don’t know, a few million up to ten million dollars in a year not more. How many failures is that typical owner experiencing in a given year? Again, on the order of ones to around 10, you’re not seeing tens of failures in a year. So how expensive is a failure when you break it down to when you break it down to how much production is lost and how much and how much that, that replacement cost is, not to mention the reputational damage whenever that occurs.
And insurance premiums in the future. Yeah. I think you’re talking millions of dollars just when looking at blade failures. And that’s for every owner that is experiencing these. I think there’s a lot more to be done, both in terms of predicting blade failures, and I think that’s where the intersection of data particularly with SCADA or with in blade sensing, I think there’s a lot we can do on that front.
I think when it comes to CMS and we, within our CMS business, it’s a lot it’s a lot better understood. It’s CMS and, vibration monitoring as a practice has been around for a very long time, not just in wind, but in other industries as well. And so I think there’s a, it’s a lot more prescriptive from that perspective.
So we, what we see within the drivetrain world in our CMS product is, we have we’ve used machine learning and AI to train on this, the CMS signals that basically the early indicators of a fault. And we’re able to tell owners with some degree of confidence, again Similarly to how an expert in the field might comment on the issue and how fast it can evolve, we can tell them with some degree of certainty how much time is left on that drivetrain before that liability turns into something much more like a risk of cascading failures and so on,
Allen Hall: so how are the SkySpecs connecting that data together? What are you, obviously everybody knows Horizon, that’s ubiquitous at this point. Is it? Horizon Plus, what is this software data set? Please tell me it’s with OneLogin.
Tom Brady: Oh yeah we’re working on it. I won’t say we’ve nailed it yet.
Not especially not the OneLogin thing. And yeah, exactly as you highlight we’ve brought together a number of companies under one roof in the last two years and there’s that constant push and pull of, do we spend that next engineering dollar on bringing these products together and making it so you have that OneLogin or is it on something that’s more like a A feature for one of the point solutions, right?
So we’re constantly looking at those trade offs. The way I see it in the future where this is heading, I think we will start to see, like I said, that common language used to talk about risk and liability, like really distilling that blade issue. Like we need to stop talking about, in my view, category 4 and 5.
That needs to be distilled to something that is Comparable and understandable by someone like an asset manager who what they really care about at the end of the day is how much is this turbine going to produce. So we have to get to a point where we can say this this blade damage is likely to lead to this amount of propagation in the coming year that affects repair costs in this way.
And it it may lead to failure, which would lead to production loss in this way. So I think we’re in the early stages of Defining that language of starting to build that product that pulls together those different data sources. I think it, it’s important to note too that SkySpecs can’t solve all the problems.
I wish we could. But there’s a number of really exciting tech companies and sensing companies and analytics companies out there that we need to find a way to answer that question of not just how do we bring the SkySpecs data together in one place, but also How do we allow that insight to action to take place for all of those other different really powerful sensing methods?
So that comes to us being more of a an open platform such that we can bring in that data and we need to take it’s on us to create those connectors, to create those APIs in order to help our industry partners. Pull that data together as well.
Allen Hall: So what you’re looking at going forward then is an ability to predict lifetimes, but also energy produced in terms of revenue and say, all right, if you let this damage go, it’s going to cost you a hundred grand over the lifetime.
And you may be able to live with that and maybe that’s totally fine versus the cost of repairing it. That may be a win situation. But right now, Those calculations are not done, or if they’re done at the engineering level. The engineer tries to pencil that out, and I’m not sure that’s always the right approach, because they don’t know a lot of the financial details about the wind farm in particular, like how this thing’s financed, and couldn’t agree more.
Yeah, so there’s a lot of unknown boxes in the engineering equation and I think this is really the first time the industry is really starting to address levelized costume. Energy. That they’re, the engineering groups are starting to focus on it. And obviously SkySight expects this has to be part of that solution because you have the data and now because you’ve acquired a couple more companies that have the ability to put, yeah, to put some context on it instead of just providing pictures, which are great.
But what does it mean to me? Because that’s the question Joel and I get asked all the time.
Joel Saxum: Yeah. What does it mean? What you’re looking to do is basically. At a highly granulated level, assign a floating ROI value to every action you would take.
Tom Brady: Yeah. I think that in the future we’ll see that there, there is a right answer in terms of what your next best maintenance dollar is spent on.
Yeah. We’re nowhere close.
Joel Saxum: Yeah. I think that’s
Tom Brady: where we’re heading.
Joel Saxum: Of course. I think, but I think that, I think that most industry, We’re in the wind industry. But most industries would love to have that. Yeah. It’s a very, that is a, that’s a precipice That would be fantastic to reach.
’cause it would be, it’s difficult right. To know which ones, because right now, like you said, a lot of people are just going we’re gonna try to re repair our cat four and cat fives. What does that mean? What did, do you need to repair now? Do you, if you repaired it in June versus repairing it in August, what is that gonna mean for the bottom dollar?
Is that’s a, it’s a difficult question to ask, but if you had. Basically, because at the end of the day, Alan, like what you were getting at, I think is when we talk to operators, they want to be told what to do. They want to know what the best decision to make is today on this asset. So if you’ve got a wind farm with a hundred turbines in it and you’ve got half a million dollars right now, these are the things that you should do that will add up to that 450 with some 50 over for change.
And then the next chunk of money, this is what you need to do. So getting to that point where it’s. It’s algorithmic, it’s modeled, it’s understood, it’s data driven but the decisions can be made that can show real value.
Tom Brady: Yeah.
Joel Saxum: That’s huge.
Tom Brady: One of the ways that we’ve operationalized that that goal, at least within, within our blade world is that many of our customers have different ways of thinking about risk.
And it. not just across customers, but also across individual sites within a given portfolio. Yeah, for sure. You, you mentioned, maybe this one is up for, maybe this one’s up for repower. And so therefore maybe I have more of a run until failure mentality. This one is on an FSA. And so I want to know about everything mentality.
And so I one of the ways that we tackle that is with a some, a method broadly we call rules. So when we finish an inspection, For our own benefit we’d analyze all of our inspections with one schema, one methodology, one set of, think of it like a big lookup table where we say, damages that look like this, we are always going to label as a crack and maybe we’ll label it with this severity.
Very early on, we saw that not all of our customers agreed with the way that we were tackling that, the way that we were labeling. And so we started getting these questions around, okay, hey you. Will you label things that look like this instead as a L E 1? And will you label these instead as a 2 instead of a 3?
And with our volume that we were doing, with the number of customers that we had acquired at that point, it was not practical. We couldn’t train our team on all of those different ways of approaching it. So we created rules. And essentially what that is, is at the moment that our analysis finishes, there are a set of it’s an engine that runs on every single inspection that we deliver, and the Customers can essentially codify down to this site or this turbine or this make and model.
When you see something that looks like this, perhaps it’s one of those serial issues that we were talking about before, I can say, alright, immediately tag that as a severity 5 because that’s a very, that’s a very risky issue. And also while you’re at it, create a task for me to follow up on this. So we’re connecting the output of our inspections directly to decisions that are, Individual, at the individual customer level and respecting all of that context that’s required in order to actually make the decision that is the right one.
Allen Hall: Let’s talk about that rule based decision making because I think that’s a unique way of looking at particular assets as the asset owner wants to look at them. You do see unique approaches across the, particularly the United States in the wind industry, about how they deal with those problems. But the overriding factor in all of that is that there’s only so many staff to look at them.
Amen. Yeah. So if you talk to Blade engineers on some of these larger operators, what do you do all day? I look at pictures. I’m looking at pictures. Yeah. That seems like a tremendous waste of resources to do that. Yeah. So with this rule based system then, you can apply some logic to it so that It’s like a pre filter.
Are doing less of that now? Is that the goal? So that you can
Tom Brady: actually use it more productively? Exactly right. And I think what, I think that the result is that for customers that are very engaged with the way that we think about rules and and using Horizon to its fullest extent, we’re seeing that they have less to review because they can set aside, okay, I.
I don’t need to go hunting for those things that I know might be problems. I don’t need to be filtering to the 10 to 20 meter mark on this make and model in order to make sure that SkySpecs didn’t screw up. Because it’s transparent. I know that when a damage comes through or an observation comes through with this set of characteristics, I’m going to be flagged immediately and I trust that the system will let me know.
So I think they can, I think they can spend more of their time on what really matters rather than hunting for What might be a problem for them next year?
Allen Hall: I’d be remiss to let you go without talking about some of the R& D aspects that are happening. Joel and I took a quick tour of things that are not for public consumption, I would say.
However, there is some really cool technology going on in the evolution of drones, hardware, electronics, storage, capability. Cameras, lenses, optics, all that are changing so fast in a couple of years. You want to describe what’s coming up for the following season? What everybody’s to expect from the R& D side?
Tom Brady: Yeah, absolutely. I think that the big thing for us for right now is in 2020, Wait, gosh, what year is it? In 2024, excuse me. 2024 we we scaled up our next iteration, next generation hardware platform for inspections. We call it Foresight. That’s what we’re looking at here.
And so throughout this season doing now over 50, 000 inspections in the year. We’re, we’ve had this sort of heterogeneous fleet. We’ve been doing some inspections with the old, some inspections with the new. And I think as we look ahead to next year, a big thing is going to be Concluding that rollout and making sure that our, all of our customers are getting the benefits of this new tech as compared to of the, as compared to the old some of the things that I think are really exciting about this new tech.
First of all it’s a lot more productive than our old tech, and that’s not just a good thing for us. It means that we can get through more inspections faster, but it also means our customers are experiencing lower downtime. And I think that, That theme, especially as we see inspections, excuse me, turbines that are much bigger, we need to continue to focus on driving down downtime because what used to be a, Oh, it’s an inspection.
So it’s cost me 20 because it’s half an hour, like not a big deal. In an offshore context, when that turbine’s off for half an hour, you’re talking about hundreds of dollars. And when you apply that across a whole fleet. It does matter, right? It starts to actually matter. And we’re constantly looking at ways that we can drive up the productivity.
We’re looking at ways that we can do inspections without turning the turbine off at all. I think these are really exciting future methods for us to do inspections. We also have some things in the works with sensing. Let’s call it just leave behind type sensing capabilities. So We’re really excited about using, whether it’s cameras or in blade stress and strain type technologies both from, also from our partners, right?
We’re not trying to build all of this stuff. All we’re trying to do is make use of it and help our customers benefit from it. Without naming specific names of the companies that are doing this kind of thing there’s a number of providers that are in that space. Yeah, just, wow.
Allen Hall: That’s a good explanation because there’s so much more yet to come. Or
Tom Brady: yet to come.
Allen Hall: Yes, absolutely. A lot of people working hard here at Sky Specs, building the next generation of sensing technology, CMS, optics, drones, you name it, you guys are involved in it. And that’s you should.
Congratulate yourself a little bit. I know it’s hard to do that in the wind industry because there’s never any down time. Amen. Yeah. It’s all the time. It’s a 24 hour
Joel Saxum: a day kind of business. Everybody thinks of the shoulder season, you start to slow down, but in this world, that’s when the dev picks up.
Exactly.
Tom Brady: That’s it. That’s exactly it. There’s about four months a year where things are in like a low season and that’s when everything has to, if there’s going to be change, do it now. Yeah, exactly.
Allen Hall: Tom, it’s been great to have you on the podcast. Really appreciate all the insight. We appreciate the tour and understanding.
Where all this data is going it’s an amazing journey. Thanks. It’s been my pleasure. Nice to speak with you guys.