The Uptime Wind Energy Podcast
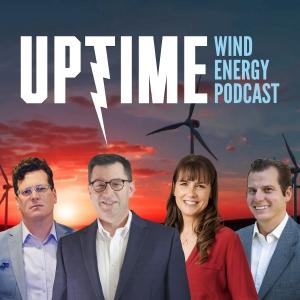
Drone Delivered LEP Robot, Vibration and Acoustic Sensor System
This week on Power-Up, Allen and Phil discuss Bachmann’s turbine monitoring system that combines vibration and acoustic sensing, Blade Robot’s innovative drone delivered LEP robot, and a vest that allows you to carry your pets with you.
Sign up now for Uptime Tech News, our weekly email update on all things wind technology. This episode is sponsored by Weather Guard Lightning Tech. Learn more about Weather Guard’s StrikeTape Wind Turbine LPS retrofit. Follow the show on Facebook, YouTube, Twitter, Linkedin and visit Weather Guard on the web. And subscribe to Rosemary Barnes’ YouTube channel here. Have a question we can answer on the show? Email us!
Pardalote Consulting – https://www.pardaloteconsulting.com
Weather Guard Lightning Tech – www.weatherguardwind.com
Intelstor – https://www.intelstor.com
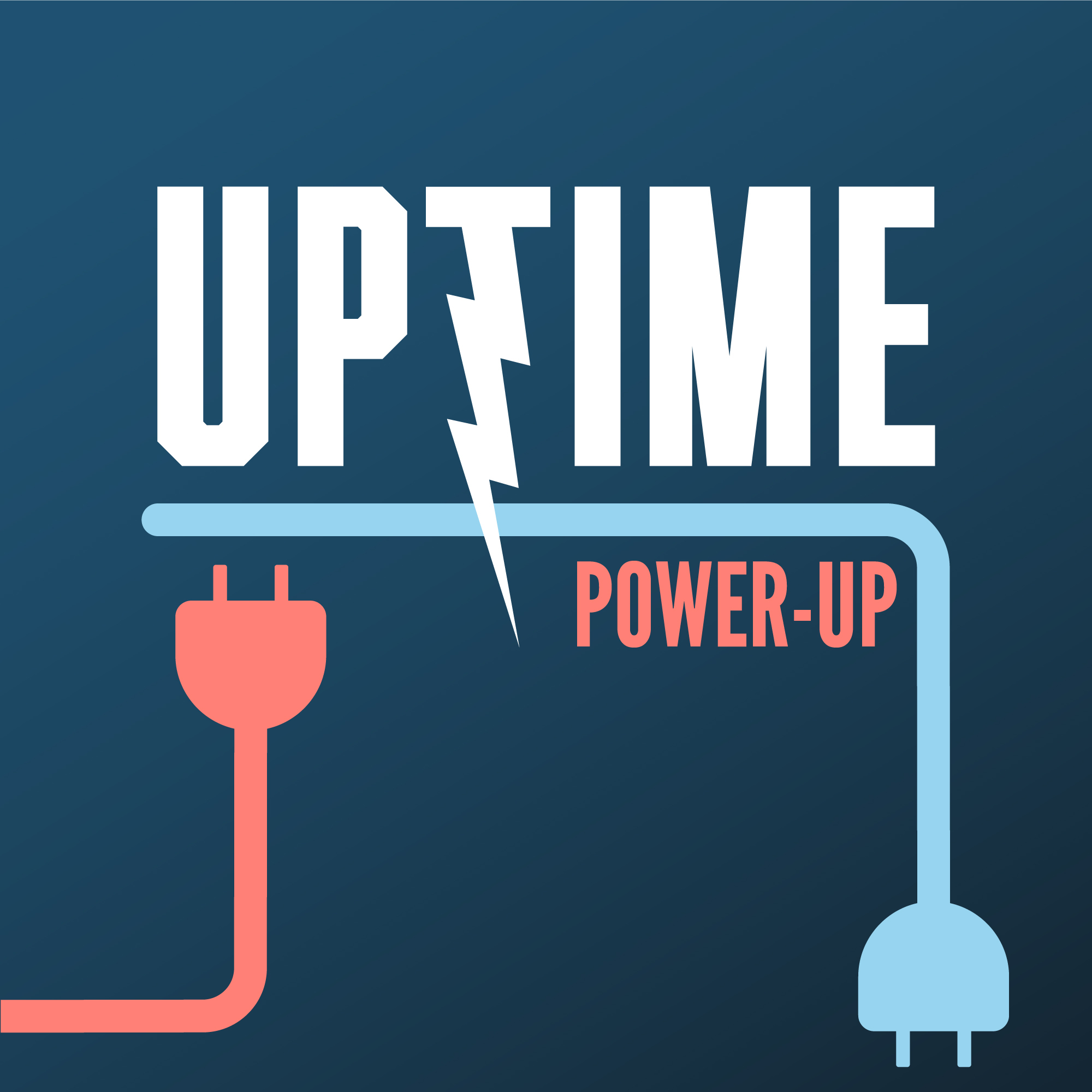
Allen Hall: Welcome to Power Up, the Uptime podcast focused on the new, hot off the press technology that can change the world. Follow along with me, Alan Hall, and idasaur’s Phil Totaro, as we discuss the weird, the wild, and the game changing ideas that will charge your energy future. All right, Phil, our First idea is called a method and device for monitoring a machine state of a machine system, in particular a wind power plant.
Now that’s a lot of words for what is relatively a simple concept from Bachmann, and their idea is a means of monitoring for natural vibration patterns, which is kind of what they do already. So this falls right into their Their skill set, where they’re looking for natural vibration frequencies of a wind turbine over time, and the, the beauty of this system is as the wind turbine ages and vibrations start to change a little more erratically, they can point out that something is off.
Not necessarily be able to pinpoint it without having more data, but to say, Hey, this wind turbine has been altered. Let’s go take a look at it. Bachmann does a lot of updated control systems for a number of turbines. This could be rather
Phil Totaro: interesting if applied. And here’s the really cool thing about this.
I think if you’re familiar with like motor racing, for example Formula One racing, they actually have. People who spend all day listening to their own car and their competitor’s car to try and get the acoustic signature of the engine and see whether they’re running it at full power, whether they’re de-rating it, or whether or not there’s like a, some kind of a mechanical issue during the course of the practice sessions, qualifying or the race.
And, and that’s kind of what Bachmann’s adopting, is that same type of philosophy, to not only do the, the vibration monitoring, but combining that with the acoustic sensors that will allow you to determine if the pitch of your gearbox has changed a little bit through mechanical wear. A lot of just the vibration monitoring can throw up a lot of false positives.
So combining the acoustic detection capability with the vibration monitoring actually, hopefully, improves the quality of detecting positive, well, we’re calling it a positive, but detecting an issue. In the in the mechanical systems. So, kudos to, to Bachmann for, for coming up with something quite innovative.
And, and I think that this is something that they are if they’re not already using it, they are going to be using it commercially soon.
Allen Hall: Well, in the area of leading edge erosion, there’s been a lot of work from a number of companies and Blade Robots, which is an outgrowth of Festus. Has a new concept, which I, I think I’ve seen, Phil, where they have their leading edge robot, and if you’ve been at any of the international conferences, you may have seen this robot where the blade is sitting horizontally on the turbine, so everything’s uptower, and the robot sits on the blade and then starts sanding and grinding and applying a new coating, As it moves towards the root, pretty slick.
The, the issue with this whole approach though, is how do you get this robot on the blade? Well, they’re, they’re identifying UAVs as the means to lift and to mount this robot, and at the same time once the robot starts, it’s moving. leading into erosion cleanup process, the UAV remains attached.
So that’s always a concern from operators. I have this robot up there. Does it fall off? Well, in this particular case, no, because the UAV is hanging around to make sure everything goes okay. This is a, this is really a different approach, Phil, than other means of doing leading edge repair from technicians on ropes to other robotic means.
Placing a UAV with a large robot to fix leading edge repair is
Phil Totaro: It is, and it’s, it’s really about time and cost efficiency, because normally, even the first generation blade robots approach, it was kind of a crane pick and crane delivered solution, where you’d have the blade in a horizontal position and then you would use a crane pick to get this thing up, Blade, which again involved kind of a precision, control and precision lowering of this thing so that it, it got onto the blade and in just the right way and wasn’t going to further damage the blade with this crane pick.
But then, you’d run this leading edge repair system along the length of the blade. And when it was done, you had to kind of crane pick it back down. So as we all know, cranes are expensive. And when you start talking about, hub heights of 120 plus meters, a crane pick for this kind of a leading edge repair technology can get expensive.
So. Drones are actually a really great way to not only deliver this, but significantly reduce the cost. Again, I think they’re still in the testing phase, as far as we know with the, the drone delivered solution. I believe they’re actually looking at this right now in, in Denmark and, and perhaps in Germany.
But at the moment, if they can make this work, this can be a huge time saver and cost saver for not only fixing the leading edge erosion and, and any other leading edge repairs that need to be done, but also getting this, this autonomous repair platform up there and, and doing its job in, in, in a time and cost efficient manner.
I think this is, this is fantastic.
Allen Hall: Fun Patent of the Week is by Bryce Belisle, and he has come up with a unique device. It is clothing with transparent, enclosed passageways for small pets. The garment, which can be a vest or belt of some type, allows pets like hamsters and mice to be viewed as they move across the wearer’s body.
And The little passageways are integral to the clothing and terminate in pocket like chambers for feeding and retrieval. Now, the patent images, Phil, are really fascinating because they show these pets, I guess, I don’t, wouldn’t have a mouse as a pet, but people do, in their natural habitat. So the, the vest has got all these colorful things on it, so the, the mouse feels like it’s at home, I guess, running through these passageways.
Now, I, Phil, I haven’t seen this before. I’ve been around a lot, a lot of the world. I’ve never seen anyone use this. I’ve been to California, which I thought was where I would see this. I’ve never seen it
Phil Totaro: there. This has to be, I mean, look, we’ve had the bird diaper on the show. We’ve had The method for swinging on a swing sideways.
We’ve had spackling a hole in the wall. We’ve had the motorized ice cream cone. I gotta be honest, this one takes the cake for me, because from the perspective of, like, things that are totally impractical yet rather entertaining, this has gotta be At the top of the list, like, why would you ever, I mean, okay, the fact that you might have like a gerbil or mouse or animal maze on your vest.
But why would you need to carry your animals with you? I mean, maybe if you’re really that passionate about animals, this is a great invention for you, and it’s maybe sad that nobody ever bothered to commercialize this, but I don’t know what is going on with this thing. I certainly would not be carrying small animals with me in this manner.
This is for the true animal lover, Phil.
Allen Hall: You gotta be dedicated to carry your pet around in tubes on your body.