The Uptime Wind Energy Podcast
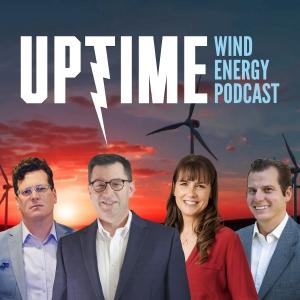
IWTG Consulting Insights: Blades, Bearings, and Big Data
Allen and Joel sit down with Jonathan Zalar, Managing Partner at Independent Wind Turbine Generator Consulting (IWTG). With over a decade of experience at GE Renewable Energy, Jonathan shares invaluable insights on recent wind turbine issues, including blade defects, bearing problems, and the challenges of rapid rotor size increases. This is a must-listen episode for a deep exploration of wind turbine maintenance, data analytics, and the importance of thorough inspections in the ever-evolving wind energy industry.
Sign up now for Uptime Tech News, our weekly email update on all things wind technology. This episode is sponsored by Weather Guard Lightning Tech. Learn more about Weather Guard’s StrikeTape Wind Turbine LPS retrofit. Follow the show on Facebook, YouTube, Twitter, Linkedin and visit Weather Guard on the web. And subscribe to Rosemary Barnes’ YouTube channel here. Have a question we can answer on the show? Email us!
Pardalote Consulting – https://www.pardaloteconsulting.com
Weather Guard Lightning Tech – www.weatherguardwind.com
Intelstor – https://www.intelstor.com
Allen Hall: Welcome to the Uptime Wind Energy Podcast. I’m your host, Alan Hall, joined by my co host, Joel Saxon. Today, we’re joined by Jonathan Zalar, Managing Partner at Independent Wind Turbine Generator Consulting, or IWTG. With over a decade of experience at GE Renewable Energy, including roles in root cause analysis and systems engineering, Jonathan brings a deep industry knowledge to his consulting work.
We’ll discuss recent events that we have seen in the field. Explore how his expertise is helping wind turbine owners optimize their assets and tackle some industry challenges. Jonathan, welcome to the show. Thanks for having me. So you’ve been around looking at blades and turbines for the last several months.
Thanks. Thanks. And we’ve been in contact a little bit about what you’ve been seeing. Maybe just give us a brief description of what’s happened this summer in terms of blades and turbines. A lot of
Jonathan Zalar: customers are starting to realize that there’s some, some bigger issues that are coming to a head. And the need to like, look more is becoming more apparent.
So, just because you have an external crack and you’re about to go repair, it doesn’t mean you shouldn’t. Maybe take a look inside, especially if it’s easy to get to. I have a few customers that are finding, internal cracks and needs to monitor some internal. Issues more and more.
So, relying just on drones is maybe not the best thing anymore.
Allen Hall: Yeah. Let, let’s, let’s talk about that because we’re seeing a lot of internal cracks. It doesn’t, the manufacturer doesn’t seem to be important here. It seems to be universal. the crack situation. Operators don’t really have tools to go do that themselves besides, and they’ve been using drone inspections forever.
So they, are they interpreting drone inspections external once it looks good on the outside is probably good on the inside. And is that the right
Jonathan Zalar: move? In most cases, it probably is, but depending on the type of crack you have and potentially like some history on the particular blades, you might want to start taking a look inside.
And I think More, I think as I don’t know, the industry keeps going with the blade repairs, they’re going to start finding that, some of these might have started on the inside versus the outside. I mean, historically, most of the stuff that’s starting on the outside, I mean, you got a lot of, the coding coming off the small stuff that, cat ones that you can steal with later, but as some, so you can cat fours and fives.
They started somewhere and if you’re not confident it was the outside, spend the extra money, look on the inside.
Joel Saxum: So, someone like yourself who’s got experience like you, you have experience from GEs, right? So you’ve been around the block for most all the, the last ten plus years of GE turbines.
You, you understand them, you know them, you have manufacturing experience, you have the RCA experience. So someone like yourself going to help, One of these operators be that extra bit of bandwidth that they need in engineering. It’s, it’s priceless for them because the knowledge that you bring is huge.
So we’re seeing like, I’m, why I’m highlighting that is it’s important in my mind for some of these operators to not just look to their internal teams to solve problems, right? What does it look like? I mean, for clients coming to you. To solve these problems, is your book full? What does it look like?
Jonathan Zalar: It’s pretty full and some of the problems I do have history with, if they’re on a GE, something I worked on before, but no, there’s new problems that are coming up and that’s kind of the part that’s exciting for me. It’s like, all right, Hey, we got this at, a bunch of turbines. What is it?
I’m like, well. Cool. I don’t know for sure, but this is how I would address it. And then that’s how I help, my customers talk to the OEM and kind of get to the point of like, all right, what’s not so much what the root cause is. It’s like, how big is the LAT list of affected turbines? The goal of the beginning of most RCA is like, how bad is it?
How much bleeding do I need to stop? And, that’s usually where I spend most of my time initially. And then after that, it’s like, all right, why did this happen? What do we need to do about it? What’s the long term solution?
Allen Hall: Are a lot of the turbine issues we’re having today because of the newness of the turbine, or the length of the blades?
There seems to be a lot of problems out there that are not super old, right? They’re a year or two old. What is the driving
Jonathan Zalar: factor
Allen Hall: in that?
Jonathan Zalar: My personal opinion? I think the industry as a whole Went very fast in rotor size. It was, the market was driven for 18 to 24 month rotor size increases.
Right. And the OEMs were like, all right, how many parts can we reuse? Can it handle these more loads? And, maybe got too big, too fast. I mean, that’s not OEM specific or anything, but the industry went very fast in the last 10 years. And I think there’s been multiple articles about all the OEMs slowing down a little bit, right.
Reducing their number of rotors there. They’re applying the field
Allen Hall: now, right? Yeah. They’re, they’re definitely consolidating the number of models, I think, to recover a little bit and get a beat on how to handle these longer blades. So what are you, what are you seeing on these turbines that are less than five years old?
What kind of defects, problems serial defects are out there?
Jonathan Zalar: You the blades ones, I think we’ve talked about, there’s been some issues on different OEMs with the manufacturing. Issues. Not too many huge design issues that I’ve seen. And then, bearings are a big issue too, main bearings and pitch bearings, they’re very expensive, right?
Multiple OEMs are having different bearing issues and, a lot of that could be back to what I said earlier, like how fast are you growing this rotor size and are you actually understanding what these parts are going to be doing,
Joel Saxum: especially long term? Yeah. I mean, I think we’ve talked actually between the three of us just about pitch bearings, right?
So the blades got longer. But the diameter of the root didn’t in some cases. So you have the same kind of forces and pressures on that root diameter, but with further and further basically the fulcrum of that lever arm moves further and further away and puts more and more pressure on that thing. So it’s hard to keep up with the design thing there.
So bearings being a huge one, do you, do you see a, a sweeping fix for some of these bearing issues? Now this is, I’m saying we’ve got pitch bearings. We’ve got yaw bearings. We’ve got main bearings. Main bearing seems to be a big one right now. Is there a fix for this or is we going to be on some of these platforms that are having these issues?
Are we going to be replacing these things every two, three years for their lifetime? I mean, I don’t think it’s going to be as bad as two
Jonathan Zalar: to three years. I think. There are other suppliers that are looking at different answers to these problems, right? The pitch bearings, I think there’s, they’re looking at a third, basically, roller bearing, I believe, on the outside.
The other bearing manufacturers are seeing, okay, hey, these are, these bearings are not working right now. What else can we do, right? And you can’t really increase the size of the bearings because you can’t change the main shaft. You’re not going to change the pillow block or the bed plate. So they’re kind of limited in what they can do.
So it’s going to be a lot of, with strength of materials and different greases too. So there, there will be some fixes that come out. They’re very limited in what they can do just from a real estate perspective. On the current designs,
Allen Hall: the issue comes about in terms of lifetime on bearings and a lot of operators don’t have a way to guess when they would need to replace bearings.
But seeing, besides seeing parts fall out and if I, if I’m going to replace a bearing, what am I going to replace it with?
Jonathan Zalar: Right. Well, and even before that, if you can get an indication that you know, this bearing’s gonna fail and you can derate. And maybe run it for a year and line up the cranes better.
There’s opportunities there too, with analytics. So both I, the greasing is interesting. I’m not heard of that, but that’s definitely an indicator when you start losing coatings as an example. So if you have that indication, you have higher vibration and you have some other analytics that kind of package together a, all right, this bearing’s got 18 months.
So what are you going to do about it? Well, how many more 18 month bearings do I have at site? If I de rate them, I get 24 months. That’s a lever to play,
Joel Saxum: right? Yeah, yeah, for sure. Because, yeah, at some point in time you have to look into the reality of grain availability and how can we put a campaign together and what’s the most cost effective way to do this.
John, you have some
Allen Hall: advanced insights because you’re on the other side, on the OEM side in SCADA data where you had high speed SCADA data and the operators typically do not. And now you’re on the other side of this fence with the low speed SCADA data. How do you leverage that data to your advantage where you can self diagnose what’s happening to a turbine, maybe a little bit earlier than you otherwise would?
Jonathan Zalar: So that’s one of the biggest learnings I’ve had since going out on my own is I thought data would be easier to get from the owners and I’m, I was wrong, very wrong. It could take, it could take weeks or months to get 10 different channels of 10 minute data, if they even have all the channels I’m looking for.
So it’s been a learning curve. And Now, a lot of customers I work with do actually collect higher speed data than I was expecting. A lot of them use Pi, if you guys are familiar with it, and they do have one second, five second, ten second data channels. Now, the number of channels are limited, so I’ve had to be creative in some of the analytics I’m looking at, but especially in issues that have just started, getting that higher speed data, looking at trip logs.
That’s really important and it’s a really good tool to figure out what’s going on. So it, it takes me a longer time to do it than I, than I used to at the OEM, because we had all the data pretty much as fast as we wanted it. But there are still tools available to the owners to get the higher speed data for certain issues.
What are those tools, John? This is definitely G specific. So it’s called G toolbox. It’s what, is running. The software at the site and you can log into a turbine, you can set up a dynamic data recorder and pull high speed data anytime a certain fault happens so you can set stuff up like that to, pull the millisecond data and start looking at it when you’re seeing certain faults over and over again, or you’re trying to hunt an issue down.
Joel Saxum: Because if you just decided to put that on record for a whole, 100 turbine wind farm, you’d have so much data, you wouldn’t even be able to handle it. Right.
Jonathan Zalar: Probably, yeah. If the server would stop working, it’d be terrible.
Allen Hall: Well, are you seeing operators put added systems on to get more data from the turbines?
I’ve heard of operators that are doing that in some instances. Is that becoming more common?
Jonathan Zalar: A lot of it’s OPC tags, right? So the pie basically like scrapes the OPC tags as it’s going through the network. I think a lot of customers are doing that. I mean, some are using genius data as an example or the OEMs version, but it, it does become expensive, right?
Cause you know, If you don’t have an engineering team looking at this data, you’re probably going to stop collecting it when you start getting those big checks or if you have to pay those big checks. But then when you have an issue and you’re like, Oh man, I wish I had that. You’re kind of like, should have kept that going.
Right. So it’s a toss up like the, the bigger owners that have, thousand turbines plus they all seem to have some sort of consistent data recording system. For higher speed than 10 minute.
Joel Saxum: Is that like a, like a base field or power factors or something? Or is that on the other side of things? Is that, are those companies more on the performance analytics side?
Less than SCADA.
Jonathan Zalar: I don’t know for sure. I’m assuming there are. Using something like Pi to pull the data to go do their analysis. I think they’re added on. I don’t think they’re scraping the data, but I could be wrong.
Allen Hall: Is that helping to drive some of these solutions and just having more data? Because it does seem like when you walk up to A wind site and especially if it’s got 100 turbines or more and you talk to technicians, they will rattle off five issues.
No sweat that are like universal across the site. These turbines have X, Y, Z, but they don’t It’ll they have a solution for it and they don’t really have a way to monitor it. They just see the after effect. Like I have to do an MCE on these turbines because of this problem. Are we getting ahead of that now?
Or are there more tools in the toolbox? I know you guys at IWTG have some of that knowledge, but I mean, what do you tell your customers? You’re, you’re, you’re one person doing a really great job for the industry. How do you, how do you help them help
Jonathan Zalar: themselves? Some of the issues do have analytics that like the OEMs provide, there’s some catastrophic blade crack analytics.
There’s, I think some on the root inserts as an example in main bearing, right? Main bearings, they look at temperature and vibration. I mean, I think every OEM does that for main bearings, right? So there are some analytics that, the OEMs want to create because they also have, full service agreements.
So they’re also motivated to do that. But the problems I don’t have them. There are opportunities for people like me. And I have one or two people helping me out that, if given the, given the time and you have enough failures, like there’s definitely analytics that can be developed and, I’ve been working on a couple of things with.
One of my customers, but it’s not something that’s a, all right, you’re going to send me three failures in two weeks of data, I’m going to have an analytic for you and it like, it doesn’t work that fast. So it’s something that you have to be working with somebody over a period of time. And have very accurate data on, failure dates, which blade actually failed, stuff like that.
Allen Hall: Well, let’s talk to the blade insert issue because I hear that one a lot from pretty much every technician I ran into this summer. Blade inserts are loose in some of these blades. They’re sometimes hard to, detect until it’s like really serious. And then they limit who can go up and down the towers.
Even at that point, are there ways to detect that early on? So you can at least evaluate that issue
Jonathan Zalar: from an analytics perspective. My understanding, it’s still in development from the OEM. I first had looked at it a little bit and it’s really tough because you’re trying to catch something that’s moving like this much on a pitch bearing.
Right? Because the interface between the pitch bearer and the blade. That’s going to be tough to do. Now there are third party non destructive testing options that I’ve seen as well, which if you’re worried about population, that’s, that’s. Now, it’s probably a good way to go. I think if the owners are, would continue to work with GE and the OEMs on getting the right data, understanding if it’s a false positive, I think there could be something there over time, but it’s all about getting the false positives back to the right people.
Allen Hall: So there may be a solution coming up in the future, but right now you, the visual inspection is the key to catching it early?
Jonathan Zalar: I think so. I don’t know for sure. It seems. If. I hear, but I don’t hear a lot of Failures that are like confirmed. I hear a lot of people talking about it, but I’m not seeing a lot of actual failures.
Joel
Allen Hall: and I have seen a number of blades with that issue and a lot of complaints coming back from the field about it because it’s, it is hard to detect. I think that’s the issue is the technicians say, Oh, there is pitch bearing grease on the blade. I must have a seal issue. I need, I need to go up and look.
And that’s the real first indicator is Grease on the hub.
Joel Saxum: Yeah. One of the, one of the companies working on is we foresee over in the Netherlands and Ado from Ado Kuipers from over there, he says. When you’re doing inspections of the nacelle or inspections of the blades, if you’re up there, peel back the sealant a bit where the blade root meets the bearing face.
And if you peel that sealant back and there’s a gap there, then more than likely you have an issue. And it could be, look here, look at the top. But if you, if you, if the blade is 90 degrees east west, then you look at the top and see if it’s actually peeling. way and you can see then that if you’ve got, if there’s an air gap there, if you can see through it, then you’ve more than likely have an issue.
Jonathan Zalar: And Meyer saying some of the other inspection techniques, if it does get flagged as a potential failure, it’s takes some time to do. It’s some dial indicators and some movement of the rotor in the blade. So that might have been, Where those technicians were complaining, because I think the term is down for a half day trying to figure it out.
Allen Hall: Yeah, right, exactly. So that, that kind of leads to a little bit of a broader question. It’s Almost fall, right? Or beginning of September, it’s going to get cold and then inspections pretty much stop in the next month or so. What should operators be doing now to carry their turbines through the winter time?
What things should it be looking at? What things should be watching out for? What have you
Jonathan Zalar: seen? Hopefully everyone’s through their I don’t know, second quarter inspections. If not, you better make sure you go do that. And then. I mean, really prioritize the Cat5s, Cat4s be cautious on temporary repairs.
If you’re going to repair it, go repair it. I, I’ve seen some temporary repairs recently that have failed and that just adds to the problem.
Allen Hall: Okay. I’ve seen some of those temporary repairs that looked on. Look to be severe cat five is the one I remember seeing earlier this year. And I thought, wow, is that going to make it?
Joel Saxum: Yeah. I mean, in the, in the Northern environments, Northern climates, people do that just so they can get through the winter time. Right. But sometimes it exacerbates the issue where you might be better off properly repairing it or using, some kind of. I know it’s tough as the winter gets along and you’re looking at what might be like a month long repair or something.
So there’s this, this balance there, but I don’t know. When they get water ingress in and all of a sudden you got to freaking open up, six, eight meters of the blade to get it proper in the springtime. You might be, have been better off to properly repair it and spend a little bit more money that fall.
And,
Jonathan Zalar: I’m, I’m saying this from a technical perspective. I’m not looking at, from an owner’s revenue perspective either. So. Take that with a grain of salt.
Allen Hall: Yeah. And what other things should we be looking at to kind of triage before the wintertime hits? I mean,
Jonathan Zalar: I kind of touched on a little bit about internal inspections.
I feel, I don’t think every blade needs to have a hundred percent internal inspections. I, I think doing some sampling of some Cat5s might not be a bad idea.
Joel Saxum: Yeah. I mean, what we’ve looked at in the past from my wind blade experiences is it’s a good idea to do 10 percent of your fleet, 10 to 20 percent of your fleet.
And then if you start to see something or then, then expand the scope and then look a little bit deeper. Now, there’s other, there’s specific models where we know of issues, right? We know where there’s some cracking issues or some flashover issues in specific ones. And then that, it’s smarter to do, a higher percentage of the fleet or all of the fleet in some cases.
But at a minimum, they should be looking at a small percentage and kind of triaging it after that.
Allen Hall: Well, John, what defects that they’ve stumbled across during the summertime really force them to do a hundred percent inspection? I mean, something
Jonathan Zalar: that’s at a location on the blade that is going to lead to a catastrophic failure.
I mean, if you start seeing something like that, then that’s when you yell, throw the red flag in and be like, all right, we need to make sure. We’re safe here. When it starts becoming a safety risk.
Allen Hall: Well, let me ask the one I’ve seen, because I think you’ve probably seen the same thing, where you see cracks in the hub on some more recent blades.
If that has happened on a site, Is that indicative of there may be a more on the site that have that issue and maybe internal inspections are required sooner? Like a hundred percent? You just cracking
Jonathan Zalar: the hub like you mean the casting?
Allen Hall: Well, not, not, well, the, the hub itself. Yes. I mean, we, we think we’ve seen cracked in husband cracked at the base of the blade that have propagated.
I’ve seen some of that this year, just driving around in the Midwest. And then, then the cracked hub, which is the I think that’s subsequent where they’ve, they’ve Crack the casting of the hub. Does that then drive you into 100 percent inspection because it’s such a severe failure mode?
Jonathan Zalar: I mean, it is a very expensive failure mode.
I believe there is already a standard inspection a few months or whatever. I believe that particular issue is being handled with a routine inspection, is my understanding.
Joel Saxum: But anything blade wise, it’s probably like This is me, this is me pulling a number out, right? If you’re basically from root to max cord and maybe another 30 percent of the blade or 40 percent of the blade length, if there’s something that you’re seeing within there, then you should address it.
Before you let it just sit and run.
Jonathan Zalar: Yeah. Brutamax core. That’s, something cracks there and liberates. Turbine’s going to fall over.
Allen Hall: This is where IWTG comes in because I know there’s a lot of operators that as Joel mentioned, are really understaffed and they don’t have the bodies to throw at some of these problems, especially if they’re unique and to, to, to.
bring you in to take a look at what’s happening on a site so that they can plan ahead. And so I think you’re right, crane operators, power generation, all those factors come into play. And the first piece of information they need is how severe is it? And do I really need, how cautious should I be? That’s where they don’t have an answer for.
And that’s why John, they bring you in.
Jonathan Zalar: Yeah, understanding the risk is very important, and then understanding the LAT, like number of turbines this is on. Those are very important factors.
Allen Hall: Can we talk about serial defects for a minute? Because I think this is, I, I’m seeing what I think are serial defects, and operators Have well, there’s been one operator in particular is screaming serial defect.
Others are sort of following that Parade and just and joining in on it at times Are we seeing more serial defect from the manufacturing side that’s causing everybody to have more work out in the field on? Maintaining the turbines and what is that? What what is your feeling on what’s driving?
Manufacturing issues that sort of plaguing some of the turbines at the minute. Yeah, I
Jonathan Zalar: I’m not too sure about the serial defect part because it’s really tough to, and contracts are very different in what a definition of a serial defect is. And that’s not my expertise. Your other question of like, why are we seeing this now?
I mean, the volume of turbines have increased. The speed of design was increased. Then you had two years of COVID manufacturing, which you can’t put numbers on or calculate the effect. I, I, and DL design tools have been slower than rotor size increases as an example. I think a lot of those things are just kind of coming together for multiple OEMs at some really bad times.
Allen Hall: So then do you look to see what the, when your blade was manufactured, it was March of 2020 through March of 2020. Basically March of 22. Do you then pay more attention to those series of blades?
Jonathan Zalar: The tangular defect, yeah. I mean, like I said earlier, like you really want to reduce the number of turbines by whatever problem you have.
So you, from a blade perspective, you look at manufacturing location, manufacturing dates, serial numbers, mold lines. Core kits, different materials used. I mean, that’s where I mean, it’s hard to get that information. It’s not usually easily available, but that’s where I try to help push my customers is like getting that information and say, all right, I have a 20 turbine problem versus a 200 turbine problem completely changes what you’re going to do.
Allen Hall: Okay, so that’s where a lot of operators do not dig into, in my opinion, they’re not looking at molds. They’re not looking at manufacturing dates, so to speak. They’re looking at blade types and trying to address it as, and coming from different manufacturing facilities. So is there a difference if a Blade is made in Europe versus the factory in the United States.
Are they just not the same thing, and yet we do treat them as the same?
Jonathan Zalar: No, I’m not a materials expert, but there are definitely material restrictions depending on the country. Different resins are approved here, and different balsa suppliers are used in different places. So there is, if you’re coming from five different countries, the blades are not exactly the same.
Allen Hall: Is the arrow shape the same? I’ve seen, I’ve seen a particular OEM that uses multiple manufacturers and the arrow shape is not exactly the same. And the lightning protection system’s not the same, even though the basic fundamental is
Joel Saxum: there. Drain holes in different places, all kinds of stuff.
Jonathan Zalar: So you guys did a built SPAC built to print episode, right?
Walk through the difference between the two. So like in GE’s case, they had a built to SPAC and a built to print blade. So the built to print blade is the one they have manufactured a TPI, for example, But they also haven’t built a spec blade, which was basically the blade needs away this much, needs to have this arrow shape, use this many bolts, be this slide at the root.
And that was what, they used LM for it. Cause LM yelled, this is before G purchased them. Like LM would design the blade themselves and they would meet that arrow shape, number of bolts, stuff like that. So it fit. And then they would have, very similar, similar performance, not exactly the same, two different designs.
And two different materials.
Allen Hall: And when you’re digging into blade issues, as particularly at some of these hundred plus wind turbine farms, you need to know all the way down what that particular blade is, right? When it was made, where it was made, even down to the molds, because that’ll tell you a lot about.
Where this problem may be on other blades in your site, right? Not
Jonathan Zalar: every issue is going to be mold to mold specific, but that’s just an example of getting down to that level of information can help you understand your
Joel Saxum: problem. So it really depends on, it can be the team that was working on it, right.
But we’re diving down into a lot of these details, manufacture, location possible, materials or consumables restrictions down into the shift level. But what that, what that all says to me is. If you have limited bandwidth and engineering, you need to, and you have an issue, you need to grab someone from the outside to help you.
You need to grab a consultant.
Allen Hall: Well, John, it’s been great to connect again, because you’ve been out in the field like us over the summertime. You’ve seen a lot of things and you’re a huge resource to operators that use you in the U S and we’ve, Joel and I have met a number of them and they love having you come in and diagnose their problems.
So how do people get ahold of IWTG?
Jonathan Zalar: They can reach out to me directly with email, jzallar, Z A L L A R, at IWTGconsulting. com. And the website is, www. iwtgconsulting. com.
Allen Hall: Well thanks John for being on the program. Really enjoy having you.
Jonathan Zalar: Thanks for having me. I really enjoyed talking to you guys.