The Uptime Wind Energy Podcast
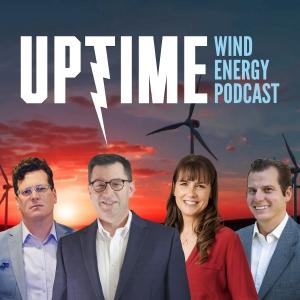
PelaStar: Revolutionizing Floating Offshore Wind with Tension Leg Platforms
We talk with Ben Ackers, CEO of PelaStar, a company revolutionizing the industry with their tension leg platform design. PelaStar’s innovative technology provides stability for large wind turbines in deep water conditions, paving the way for cost-effective and efficient floating wind farms at scale. Visit https://pelastar.com/ for more info!
Sign up now for Uptime Tech News, our weekly email update on all things wind technology. This episode is sponsored by Weather Guard Lightning Tech. Learn more about Weather Guard’s StrikeTape Wind Turbine LPS retrofit. Follow the show on Facebook, YouTube, Twitter, Linkedin and visit Weather Guard on the web. And subscribe to Rosemary Barnes’ YouTube channel here. Have a question we can answer on the show? Email us!
Pardalote Consulting – https://www.pardaloteconsulting.com
Weather Guard Lightning Tech – www.weatherguardwind.com
Intelstor – https://www.intelstor.com
Allen Hall: Welcome to the special edition of the Uptime Wind Energy Podcast. I’m your host, Allen Hall, along with my co host, Joel Saxum. With the increasing demand for clean energy, offshore wind has become a crucial component in the global energy mix. However, many of the world’s best wind resources are located in deep waters where traditional fixed bottom foundations are not feasible.
And this is where PelaStar comes in. PelaStar is changing the floating offshore wind industry with their 10 leg platform design, which provides stability for large wind turbines in deep water conditions. Our guest today is Ben Ackers Chief Executive Officer at PelaStar. Ben brings a wealth of experience in the maritime industry to lead PelaStar’s efforts in making floating offshore wind a reality on a large scale.
Ben, welcome to the show. Thanks for having me. There’s a lot to talk about because with the recent auctions or the outlines of some offshore wind sites off the coast of Maine, and then obviously off the coast of California, floating wind is going to be huge in the United States, and it’s already becoming something of an item over in Europe.
You at PelaStar have been trying to answer some of the problems that we have with floating offshore wind and maybe you can just give us a little bit of background on PelaStar and what you’re working on right now.
Ben Ackers: Absolutely. First of all, PelaStar is, as you said, a tension leg platform which sets it apart from a lot of the platform technologies that you’ll see that have been deployed in demonstration and pilot projects. We’re really the next generation of technology that the industry needs to bring down the cost of energy for utility scale floating wind farms. We started developing PelaStar around 2009. The idea comes out of our parent company, Glosten, which is a naval architecture, marine engineering consulting firm headquartered in Seattle.
We’ve been around for over 65 years. And as our engineers were looking at the challenge of how do we put turbines offshore? We evaluated the different archetypes of the time. Semi submersible spars. And ultimately landed on tension leg platform is what we thought would be the best way to bring down the price of energy in the long run by developing platforms that have the lowest mass and the least amount of motion to drive down capex and operating costs.
Joel Saxum: So a quick question then there, we’ll dive right into it is you highlighted what you believe the Or what in, it’s physics, right? But what the tension leg platform has advantages over some of the other technologies that are out there, because like we, we talked about a little bit off air there’s a lot of options and ideas and demonstrators and stuff, but nobody has really taken that the front runner, the pole position in the race for what’s going to be built at scale in offshore floating.
So that’s The tension leg platform idea. What are the advantages of it over some of the others?
Ben Ackers: Principally, the classic advantages of a tension leg platform are that you can design a platform, a hull with the lowest mass of any of the systems because we’re not using the platform itself to provide stability to the turbine.
We simply need less mass. steel or as others might use concrete to provide that stability. And then we’re stabilizing the platform with tendons that are vertically stiff so that we have very little vertical motion and very little rotation of the system because it’s basically a rid, effectively a rigid structure in the vertical direction.
Now it does, it is soft in the horizontal direction, so there is some movement back and forth. But ultimately. By restraining that motion, we provide the turbine with an ideal environment for operation. So we keep motions down low enough so that turbine is producing power and with an efficiency equivalent to if you’d put that turbine on a monopile.
Joel Saxum: That that’s hugely important, right? Because we’re, you mentioned CapEx in, a couple of minutes ago, but OpEx, because Allen and I, we were always talking, we’re all engineers at heart and thinking, you got this turbine up there and now you’ve introduced a few more degrees of freedom with some of the floaters, right?
We’re talking Highwind Scotland and stuff like that, where now you used to have the monopile and you have a little bit of movement in it, but now you have this and all kinds of rotation and all those things. So you’re actually it’s possible in my mind that you guys are taking out some of the future O& M costs by possibly saving on bearings or rotating equipment by lowering some of that movement.
Ben Ackers: That’s absolutely what we’ll leave, but it goes beyond just reducing wear and tear on the turbine, which is obviously really important, but it’s also about accessibility and workability, right? Because in the conditions in which we’re maintaining offshore wind turbines today even in shallow water, where we’re using SOVs with walk to work gangways, CTVs, daughter craft to board the platforms, our platform is not moving.
And with our central column design, we present as a monopile. So you just translate all of those things that have already been matured in offshore wind today. And we can use those same systems, same procedures, same equipment to get people on and off the platform. Whereas other platforms that have more motion, that becomes a greater challenge.
So we’re either those platforms are, you’re either going to have to limit. The times that you can actually access the platform because of that motion, or you need to build more robust equipment to deal with the relative motions between the platform itself and the vessels you’re using to access it.
And that’s all going to cost money. And then once you get people on the platform if the platform’s moving, they can simply just get less done. They’re less efficient versus being on a stable platform to get their work done.
Allen Hall: So the basic PelaStar design I’ve seen on your website, and your website is fantastic by the way, people should go there, check it out, just go to PelaStar, I think, PelaStar. com, and you can see all the details there’s basically a monopile type tower, and there’s five steel legs coming off to the side, like spider, and then there’s tension lines going all the way down to the bottom of the ocean. It’s that simple. And the one of the unique features I thought was the ability to transfer the components to the assembly site, like everything can be barged up.
So you don’t have, you can make the system pretty much anywhere, put it on a ship, haul it to the site and assemble it right at the coast line, I assume at a dock and then just tug it out to where you need to be. So you’ve thought about this from a lot of different aspects. It’s really simple. But it does a very difficult task at the same time.
There’s always that fine line. Where’s all the magic in all this? Is, there’s always that real, that piece that makes it all tie together. Is it the tension lines? Is it the anchors that make all this possible?
Ben Ackers: First of all, simplicity is The the cornerstone of our design philosophy that in order to take advantage of the TLP, this low mass structure, our goal is to leave as little complexity in the water as possible.
And a lot of times people will say, it looks too simple. There’s gotta be, there’s gotta be something more to it. And there is a lot to it. So first of all, there, there are so many factors to consider in design that you already know how hard it is to design for turbines, either even on land or Fixed offshore turbines the interaction with the environment and the complexity of the turbine, its loads, the wind loads, the control system, all of that requires a lot of work and a lot of fine tuning.
And you can’t just go to a clean sheet of paper, draw a platform and see if that works. It, it takes a lot of iteration, a lot of optimization to bring this all together. Now there’s certainly complexities to address a platform like PelaStar that’s designed for excellent operation and low construction cost is one that is also harder to install.
And so our some of where that secret sauce is, how do we get that platform that when the, those arms go underwater. It loses stability. How do we get it installed? So we’ve developed an installation system called crawl down installation where we float the platform out to the site. And then we deploy tendons with the platform and those tendons are extra long, longer than they have to be.
So that we can grab onto those with tools we call jacking tools and actually pull the platform down to its installed draft. And then we can remove those excess lengths of the tendon, remove all the special tooling that is that, that is complex, get that off the platform so it doesn’t stay at sea.
So we don’t have to buy 500 copies of that equipment, take it to the next platform. reuse it for installation. But I, you asked what about the tendons? The tendons are also incredibly important. If you were to have just carbon copied oil and gas technology into offshore wind, we’d all be using tendons that were either steel bar or steel pipe.
And while that works great in oil and gas when you’re deploying one platform and you can wait a long time pipe is hard to deploy. And so we looked very early on, we decided that we wanted to pursue synthetic fiber tendons. The reason being that they’re far easier to deploy. Literally you have them on a spool and you unspool them into the water.
And they have Excellent performance properties. We actually get damping out of the synthetic fibers that you don’t get in a steel tendon and that improves system performance, reduces fatigue loads, makes the controller easier to design and they’re very cost effective. It’s required a lot of new technology development.
And that’s something we’ve been working on with our partners, FiberMax and Dyneema for over a decade now to get the performance that we’re targeting and the technology qualified so we can deploy on real platforms.
Joel Saxum: So this is where I want to make sure that we don’t miss this because I made a mistake a few episodes ago, talking about the depths.
So I’m not going to make this mistake again. So we want to, I want you to be clear, Ben, on where you guys can install. And if you do have some limitations if there’s certain soil subsurface you can’t anchor into or basically if you can do anything and what, Depths and what this looks like, right?
Ben Ackers: We actually have a great range of site conditions that we can install. And I would say in terms of bottom conditions really the only difficult substrate would be a mud. And you can use a suction pile anchors in those conditions. It’s a, it’s already been done by oil and gas, but it is pretty expensive.
So we’d like to see our preferred seabed would be a sand gravel clay mixture. We have excellent cost effective anchor options there, but also if you start to introduce hard rock seabeds with either some overburden or just clear rock, there are good anchor solutions for that too. So that covers most of the seabed conditions that we’re going to find.
Now as far as depth goes we actually can deliver cost effective solutions for modern turbines in the 15 range down to about 70 meter water depth. And that is, that’s it. On the shallow end of a lot of people’s expectations. We’ve worked hard to optimize the design to make that happen.
But actually we’re finding that that’s a pretty compelling case to developers who actually, who have a hard time getting some of these immersibles even to work in those depths, because it’s actually very challenging to design catenary and top mooring systems that work in that depth range as well.
Yeah. That’s shallow. Yeah. Yeah. Then on the deep end as you get deeper we do get into arguably a soft sweet spot in the a hundred to 300 meter range. In terms of overall cost performance, but we can keep going from there. It’s just a matter of lengthening tendons in our system.
So we’re working closely right now, focused on the water depths that we’re going to find in the California lease areas between 750 and 1300 meters. That 1300 meter is going to be a pretty much a hard cutoff in the U S for some time now based on what Boehm is going to cite for lease areas And so we’re working on solutions there.
There are a lot of technical challenge going that deep. However, oil and gas has conquered the, this depth territory. It’s not a technical feasibility issue. It’s a techno economic issue. How do we produce the most cost effective mooring solutions when you have to simply buy more tendon? And that’s an area of That’s our primary area of research and development focus right now is how best to do that cost effectively and what kind of design trade offs are we going to make to make what we call ultra deep water more economically feasible.
Allen Hall: Does the tendons. Are there tendon changes based on the water depth? I know Dyneema is a magical material. We use it. I’m an electrical engineer and we use it for electrical things. It has great electrical properties, by the way, but also has wonderful mechanical properties. You see it in sailing all the time.
Are there any design, changes that are relative to where the wind turbine is going to be installed?
Ben Ackers: I would say that’s really only a function of depth. We we’ve Dyneema as our core load bearing fiber works great from that 70 meters out through a few hundred meters. As we get into ultra deep water, it’s not I know we have to ask ourselves, this is a a very high performance fiber and you do pay for that performance and you need to ask yourself if you need to pay for that performance over the length of the entire tendon.
We always find value of having that those properties somewhere in what I’ll call the tendon stack, but it’s not clear that we need that for the whole length. So we might be looking at other materials through the tendon stack for a more efficient tendon design.
Joel Saxum: Yeah, so I’m thinking I’m on the construction side again, because now we’re talking about differences in length and differences in materials in the tendon stacks and going back to what you said, where we can, this thing can be built case side and then basically brought to site rolled over or rolled over, but install the onsite.
So if you were to say, I know that the water depth thing is a little bit different there, but if you were to say, giving equal, A monopile installation versus this installation with the PelaStar system. Time wise, is it half the time to install PelaStar? Is it double the time to install PelaStar if you were to put them on site?
Ben Ackers: That’s interesting because we don’t do a lot of direct comparisons with the timeframe of fixed fixed pile installation. But I can tell you that we can typically get anchors installed in it, it does depend on the anchor type in the seabed conditions, but that, that operation we’re focusing on anchors that are being specifically developed for floating offshore wind. So we’re not using a lot of the traditional anchor types that are technically feasible, but are quite expensive. Some of the innovative anchor developers are using their own proprietary subsea installation. methods that decouple installation from vessels that drives down the vessel size we need for installation.
And then they’re using Subsea Robotics to automate the installation process. So we can get a, an anchor spread of our five anchors installed in 24 hours. And then When we bring the platform out, it takes a couple of days to get the tendons deployed, hooked up to the platform with the platform crawled down and the cable connected.
So that’s about a three day evolution offshore.
Joel Saxum: That’s cruising. So immediately comes to mind. This is from my oil and gas background. The company subsea micropiles. And the cellular robotics team that’s just up the street from you in Burnaby B. C. that builds that robot. It’s, if you haven’t ever seen this thing before, I have an offshore world, it’s really cool.
It’s it started life as a geotechnical, drilling, seafloor geotechnical drilling rig. So instead of having to do geotechnical from a boat, you put this thing over, it’s an ROV, it goes to the bottom and it auto, it will, can do CPT coring and in all kinds of things. But now they’ve adopted it. Subsea micropiles has adopted it to actually do in not even in situ tests, but actually geotechnical drilling tests.
And then at the same time, they can install the subsea micropiles in the subsurface, drill them down, and then they hook them up as anchors, leave a buoy on them, move on to the next one. And then you guys can come right behind them and just hook up to the anchors. That’s fricking slick, man.
Ben Ackers: Exactly. And their anchor is good for a lot of rocky seabed conditions.
There are for the softer sediments we’re we work closely with a company called Triton Anchor in Massachusetts, and they’re developing a helical group pile system that is excellent actually. And then Schottel Maritime Technologies also has a groutless mechanical toggle rock anchor system, very similar to subsea micropiles, but they don’t need to grout, but then they need a harder rock material for their system.
Yeah, mostly we’re looking at grouped anchor solutions to get away from the heavy drilling that you would expect for a more classical rock anchor.
Joel Saxum: Another question for installation and O and M the in, in farm collection, power cables, and the main export lines and stuff like that. So now the main export lines, you’re going to have.
A little bit of a navigation to do to make sure that of course the anchors and stuff are not in the same pathways. But what is the hookup for comms and power, import, export, all that stuff look like with the PelaStar platform?
Ben Ackers: It looks like a lot of other platforms. The fact is that with our lower motion.
It’s actually a little bit easier to design the dynamic cable that connects the platform to the inner array cables just because we’re not moving that much, it’s straightforward. One cable with all the export power and data that cable is generally prelaid on the seabed a couple of days before we come out with the platform.
And then we send once the platform is installed and locked off on the tendons, we send down a messenger line through an I tube that goes up the center column of the platform. An ROV makes the connection to that dynamic cable. And then we pull that cable up through. Our eye tube a bend stiffener will lock itself off at the base of the platform and then the the cable will come up and we’re looking at some kind of cool, innovative new systems that they will auto latch in place And we can do that entire operation without putting anybody on the platform.
And then but with it held in place temporarily, then we can get all of our temporary installation equipment off the vessel and wait then for an SOV to come out with a crew that actually secures the final hang off joint and terminates the cable into the switchboard.
Allen Hall: PelaStar was invited to participate with the Department of Energy in the Floating Offshore Wind Readiness prize and it, there was a, that’s been going on for about a year, I think, or so. What, where is that at right now? And what’s the next phase of that?
Ben Ackers: FLOWin is a three phase competition. The first phase was completed a little bit over a year ago. And in phase one, there were 43 teams all led by platform technology that competed to Demonstrate to the Department of Energy that we had technologies that were mature enough to justify moving on to the next step of industrialization and planning for cereal production.
So we completed our submissions for phase one in January of 2023. And of those 43 teams nine were awarded phase one prizes and we were among one of those 19 among those nine teams. So that came with a cash prize and a voucher to get some work out of National Labs as well. And then, but what it really brought with it was an invitation to participate in the phase two round.
We completed our submission for phase two. And on March 1st, so just very recently. And now we’re all waiting patiently to hear the results. What I’m expecting to hear those in mid May, I think, and we’re, we expect five teams to be awarded phase two prizes. And what we had to do in phase two was to show that we have a, that we are developing real plans with real suppliers to manufacture these platforms at scale, at the pace of one a week to deploy gigawatt scale farms in one to two years on a regular pace, one a week.
That’s a lot to ask. It’s actually one of the, I think our biggest takeaways from really digging into this in phase one and looking at our production throughput from the steel showing up at a fabrication facility to locking off the platform on its tendons, looking at that entire chain we actually found that it was pretty achievable to get to that level as long as you have a fabrication facility that is built around hitting that production target. And we were able to do that working with a partner here Pacific Northwest Everett Floating Structures that has ambitions to be one of those fabricators. And with some help from some European industrial engineering companies to design a manufacturing facility to with. with two assembly lines essentially to fabricate all of the modules we need to assemble a full platform and do that at a rate of one a week. And then we, and then as you were commenting earlier the general plan is that we develop those facilities in our target regions, whether they be U. S.
West Coast, U. S. East Coast, Scotland, Eastern Australia, and then then we ship those modules to an assembly and integration facility that would be local to the wind farm itself. And there we can complete final hull assembly and integrate the platform with the tower and the turbine. And we had to also end up with two assembly lines at that facility to hit that one a week target.
Allen Hall: Okay. That’s impressive. So what, when can we expect to see a Palastar project? platform in the water probably off California first. I’d assume that’d be the first place to go.
Ben Ackers: We’d like that to happen. We’d like to see something like a pilot project, maybe proceed to these utility scale deployments and see that maybe something like 2028 with any luck, and then then we would start seeing the real deployments probably in the 2032 to 2034 timeline.
But hopefully we’ll see PelaStars popping up before then in other parts of the world.
Allen Hall: See, that’s a realistic timeline, Joel. That’s one thing that we don’t get a lot of at Offshore Wind is a reasonable amount of time because there isn’t a lot of infrastructure that needs to be built up before you can do one a week.
It takes a little time, yeah.
Ben Ackers: And a lot of money, right? And workforce training. training the men and women that we’re going to need to build and operate these platforms is a huge heavy lift in addition to the investment in these facilities.
Joel Saxum: What I’m hearing here is that you guys cause we’ve been talking with We talk with everybody in the industry, right?
And floating offshore wind, it’s at such a early stage in most places. I’m over here in Bilbao, right? We’re right on the coast and there’s a couple of demonstrators out in the water here, some people taking tours to them on the show floor this week I saw a couple of different types of platforms, but it just doesn’t seem like.
Anybody’s as far along with as much support and as much proper planning and engineering complete as you guys are from this conversation we’re having right here.
Ben Ackers: Indeed. There are a lot, there’s a lot of competition out there. We often joke every year, I feel like we had another 20 concepts that people are developing with.
Let’s say there’s about 120 out there and we’ll say, there’s probably 30 real competitors and there are definitely, obviously platforms that are already out in the water that are competitors. have successfully deployed. So I don’t want to take away from the, from their engineering accomplishments they’re great.
And they’re and a few of them are doing the same thing, planning through this whole production throughput and serial production plan. They know that’s, what’s important to, because the reality is as good as our technology is, if we can’t do, if we can’t deliver it. developers can’t buy it.
So certainly there is an upper echelon of technologies that are carrying things through this far because if They don’t have a product to sell. But I appreciate the head nod. It’s been a lot of hard work and we see the importance of all of this.
Allen Hall: Obviously, PelaStar is doing a lot of wonderful things.
How do people connect with PelaStar? How do they see this Tension Lake platform? How do they connect with you?
Ben Ackers: They can give me a call, send me an email. I’ll be in Sacramento in the middle of May and that’s actually around when we expect DOE to announce that phase two prize winners.
And yeah, so send me an email. Happy to talk.
Allen Hall: And this has been fantastic. We have to stay in touch as this effort grows and it would be great to see In California and close to me in Maine at some point and yeah, Palastar is going to be helping lead that way. So I really appreciate you being on the program.
I’ve learned a ton. Thanks so much.
Ben Ackers: You bet. Thanks for having me.