The Uptime Wind Energy Podcast
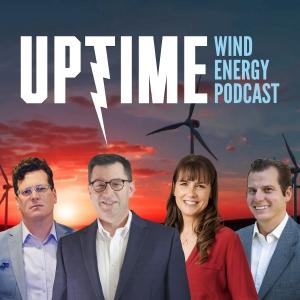
Transforming Wind Turbine Inspections with Voliro’s Contact-Enabled Drones
Allen and Joel talk to Laurent Zimmerli, Vice President of Customer Experience at Voliro. Voliro is a Swiss company that creates drones and robotics to transform the industrial inspection and maintenance processes. Their flagship “Voliro T” drone is designed for stable and controlled contact with surfaces, enabling efficient inspection of wind turbines including non-destructive testing and lightning protection system testing. Visit https://voliro.com/ for more!
Sign up now for Uptime Tech News, our weekly email update on all things wind technology. This episode is sponsored by Weather Guard Lightning Tech. Learn more about Weather Guard’s StrikeTape Wind Turbine LPS retrofit. Follow the show on Facebook, YouTube, Twitter, Linkedin and visit Weather Guard on the web. And subscribe to Rosemary Barnes’ YouTube channel here. Have a question we can answer on the show? Email us!
Pardalote Consulting – https://www.pardaloteconsulting.com
Weather Guard Lightning Tech – www.weatherguardwind.com
Intelstor – https://www.intelstor.com
Allen Hall: Welcome to the special edition of the Uptime Wind Energy Podcast. I’m your host, Allen Hall, along with my co host, Joel Saxum. Today, we have the pleasure of speaking with Laurent Zimmerli, Vice President of Customer Experience at Voliro. And Voliro is a pioneering Swiss company applying drones and robotics to transform inspection and maintenance processes.
Founded in 2016 out of ETH Zurich’s Autonomous Systems Lab, Voliro has quickly become a leader in industrial inspections and non destructive. Testing their flagship offering is the Voliro T drone known for its stability and reliability in confined spaces. Thanks to its omni directional control. We’re all welcome to the program.
Laurent Zimmerli: Thanks Allen. Thanks for having me. It’s great to be on the show today.
Joel Saxum: We had this conversation. Okay. We’re fresh off of OMS and blades and people talking. Lightning protection has been. Huge. Everybody’s talking about it. Lightning protectionist. Weather Guard lightning tech, that’s what we do, right?
We’re talking StrikeTape to people all the time. The first thing we ask them is, when was the last time you got your lightning protection systems tested? And a lot of times we get this glassy eyed look. Do we do that? They look at someone else and pull their phone out Do we do that? This is, this, and this is one of the reasons we want to talk to you.
We want to touch on Voliro and all of the offerings you guys offer, because I know you’re working on NDT things. You’re working on a lot of cool stuff, because you’ve solved a base root problem. So let’s jump into that. The base root problem of flying drones and being in contact with surfaces.
Laurent Zimmerli: Yeah, that’s exactly, that’s actually how it started back in 2016 at ETH Zurich as a research project.
So we definitely didn’t think about testing lightning protection systems of wind turn turbines back then, because it was mainly about what you just explained. It was how can we create a drone that can establish contact in a stable and controlled way with a surface or an object? If you’re looking at a, like a conventional multi copter drone, whenever it moves sideways or forwards or backwards, the whole drone tilts in the direction of the movement.
That’s basically how it works. The, like the back prop spin, spin harder and then it tilts and then it moves, which completely, which is the perfect way of moving. That’s how a helicopter works as well, right? Now, if you’re in motion it’s not a problem in terms of stability because you’re in motion.
However. If you want to push against the surface, or if you want to apply force against an object, the vehicle will not move. And if it tilts, it becomes unstable. And at some point, if you push too hard, it just basically falls over.
Joel Saxum: It’ll flip over.
Laurent Zimmerli: Yeah, yeah. So basically the question back then is, was how can we redesign the airframe, that the vehicle the drone, the, So that it can actually remain stable when it gets into combat.
And that’s how it started back in 2016 in the research lab.
Allen Hall: So the tilt is the problem, right? That any sort of other drone has to have tilt to apply any force. And that’s why we don’t see a lot of drone applications on LPS systems, on wind turbines. And that is the key, right? So I, one of the problems with any LPS resistance measurement, even with technicians, if you watch, is that it does require a good bit of force to push these probes into the receptors to get an accurate reading, because a lot of the resistance is actually in the contact between the probe and the receptor.
So you have to apply force. That’s not easy for a standard drone to do. For a human, sometimes they don’t apply enough force. If you look at resistance measurements. Sometimes you see they’re a little erratic because they’re not applying a proper force to get through like oxidation levels and on the surface of the receptor and all these other minute things that matter.
So then the technique for Voliro then is to have basically be able to rotate. Is that the solution here?
Laurent Zimmerli: That’s exactly the solution. So the big difference is that. Instead of tilting the vehicle to move or push forward, we’re tilting the rotors. So it’s the propellers that can actually tilt forward.
They can tilt backwards and sidewards. And they can do it in, independent of each other. So they don’t have to tilt in the same direction. So if you have a perfect day, zero wind, perfect conditions, of course you only need to push forward and it’s all good. But that’s like probably happening one once in a hundred years.
We build wind farms in windy areas for a reason, right? That’s exactly it. So you ever, you always have a little bit of wind. There’s always a gust surprising you at some point. And while you’re pushing, you need to be prepared for that. And for that’s why the independent tilting of the rotors can not only apply pressure, but it can actually also counteract external forces like wind, like gusts, everything like that.
And that’s actually not, just basically to to come back to something Joe mentioned before, it’s not just a case for the LPS testing. It’s for any work at heights that you do where you need to apply force. So you were quickly mentioning NDT, non destructive testing. So where you push sensors against steel structures, for example.
You also need to have a constant force. You also need to have a stable interaction. And you also have these kind of conditions because it’s not just the general weather conditions. It’s also the fact that we’re close to structures. Per definition, we’re flying close to structures. That scares people.
It scares people. And also it makes it harder because there’s, there can be different kinds of winds and turbulences because there are structures, right? So that’s basically a key of the solution to work. It’s not just the lab kind of conditions to apply the 30 Newton of force or how much you need, but it’s also to be able to keep that.
While the situation or the conditions around the drone are changing, exactly.
Joel Saxum: When you talk about the drone, I’m immediately, I’ve seen it, right? I’ve watched YouTube videos, I know what the solution looks like. But for people that may not, think about the movie Avatar. A lot of people have seen this, right?
Those flying vehicles, where the, like the helicopter things that they fly around in? where they can individually pitch and I think they can pitch and roll them too. That’s what the system looks like.
Laurent Zimmerli: Absolutely. Yeah. As you mentioned the name of the of the drone, we call it Voliro T for a reason, because it’s a, it’s a T shape.
You have the two rotors in the front that are like for any kind of multi, a multi copter, but then instead of have another two in the back. You have a straight tail going back again in a T shape, which has another rotor, which then helps also to stabilize the system. And one thing I actually haven’t mentioned and that’s not necessarily important for LPS, but for many other applications, we’re not just able to apply this pressure horizontally and, but we can actually tilt the whole drone upwards and downwards and then apply the force in any angle.
We can also do a bottom up or a top down. arbitrary angle and then apply the force in the direction of the sensors. And that’s all thanks to the rotating, the tilting rotors. And the the system, which is really designed for this.
Joel Saxum: I’m sitting in my office right now. There’s a wall a meter away from me.
If I had a yardstick or a meter stick, and I was pushing it on the wall. That’s what we’re trying to do, because that becomes basically a fulcrum and a vertex, right? So that point where I want to touch the wall, I need to have good contact with that all the time. And if I take the yardstick and I push straight onto it with my thumb on the back, I can maintain that position fairly easily.
But if I start leaning the yardstick up and that’s what a normal drone, say a DJI phantom four M three hundred, whatever that may be. When you try to put pressure forward, you watch it fly. It has to do this, right? It has to lift the tail and go forward. So if I start lifting the tail, I can’t keep that yardstick on the wall there.
It’s very difficult, but if I’m able to keep the, basically The vector of force going straight at it, which is what your drone does by tilting the rotors themselves and pushing at it. Then I can keep that thing on point.
Laurent Zimmerli: In general in the industry, in the robotics industry because pragmatic people have been impatient, which is absolutely understandable and which makes total sense, but the problem is that then they try stuff and then those videos are online where you see these drones crash and then people just lose confidence.
Into this and faith into this kind of technology.
Joel Saxum: So right now you guys have a commercialized system. You’re rolling it out worldwide. You’ve had, I think the last time we talked to you had done around, was it 700 LPS tests in the field?
Laurent Zimmerli: It was 700 in 2023. And we’ve already done a bunch this year.
I don’t know how many, to be honest, but 700 last year and about 200 the year before when we started using it.
Joel Saxum: So we’re over a thousand more, more than likely that you guys have actually deployed in the field and most of these in the EU, or have you broken it out in the U S or where are you working at for LPS?
Laurent Zimmerli: It’s probably about 50, 50. We’ve done the, so the early adoption program in 2022, we’ve done a few campaigns with our customers in Europe, Northern Germany, for example. But now our customers who are the inspection providers. So just to be, maybe to add this so we are providing the technology, but we’re not doing the service because our customers usually are service providers who use drones doing inspections in some cases, it’s also turbine manufacturers who do their inspections themselves.
It depends a little bit, but most of the time it’s an inspection provider. And, but what we do and what we especially did during early adoption, obviously, is we went out together with our customers. To do the inspections and that was mainly, again, early adoption was mainly around Europe, but now our customers that we managed to get last year and who are using the system, that’s actually more happening in North America.
So we have campaigns being flown in, in, in the U. S. We have a customer that’s going to do a campaigning in Canada later this year. And then we do have a bunch in Europe as well, but the focus started shifting towards North America.
Joel Saxum: It’s needed over here. This is from the people dealing with lightning protection upgrades.
It’s needed over here big time. We don’t have the, I know that it’s Germany and I think France. They also, they have statutory laws where it’s one year, two years, you must inspect your, that’s great because it’s a, that’s a safety thing, right? And over here, we just. The U S doesn’t like to be told what to do.
So everybody’s left to their own devices.
Laurent Zimmerli: No, but I guess, so what we hear it’s in, because I was just talking to a customer today who is operate not only, but they are also operating in the U S and and what they hear or what they feel from their customers is that one of the reasons why they would start increasing inspections on lightning protection systems is that they were also scared of, Basically of the contracts they have with the grid.
So they need to deliver a certain amount of energy electricity to the grid. And if they have damaged turbines and they cannot deliver, it’s going to become super expensive because they have to buy it from a different provider. The other provider knows it. They ask for, I don’t know, fantasy prices. So it’s going to be super tough for them.
And if they can basically do more regular checks and be sure that this is The risk is decreased or eliminated that’s in terms of risk management, a huge factor.
Joel Saxum: So let’s talk this way then. Okay. So we’ve got listeners listening right now. Maybe they want some LPS inspections on the website.
I see three and a half megawatt turbine completed an LPS inspection in 40 minutes. Now, the reason that this is important and super important really for a mass rollout of LPS inspections is that. Traditionally, these are people on ropes or people in man baskets or people in trucks. And you might get one or two turbines done a day because you’re rigging and moving and all this good stuff.
So that those, they become really expensive. Now, if you can do 40 minutes per turbine, all of a sudden, you might be able to get eight, 10, 12 of these done a day. And then you’re changing the game as far as value add for bringing LPS inspections on site. Walk me through the process. Technician shows up at the base of the turbine.
To walk, to walking away from the turbine. What does it look like when they’re doing the test?
Laurent Zimmerli: In the end, it depends a little bit, but the best, let me start with the best case, because the best case is there’s no spark gap, so nobody needs to close the spark gap and there’s a remote controlled shutdown of the turbine as possible, so no technicians need to actually need to be on site because they inspect the inspection provider can be there.
It’s a one man operation. So the person who is piloting the drone can take the measurements on the remote and see the results. So they can fly the drone, take the measurements, save the measurements and basically make sure and store all the results and create a report from all these results. So best case and that’s actually, I don’t know how, probably about 50 percent of the cases, it’s a one man operation.
No technician needed whatsoever. Unless of course there’s a damage that then later needs to be repaired. But for the inspection as such, it’s a single person operation. Now you, some of the turbines have the spark gap. So what you would have to do is close the spark gap because we’re doing a full circuit measurement.
So we need the whole circuit to be closed. And so that’s something that, that you will require. And then depending on the turbine, some of them also need to be stopped on site. So somebody should just be there to stop the turbine. And then talking about stopping the turbine. So what we unfortunately cannot do is measuring a spinning turbine.
So we’re working on that, but that’s not working yet. But what we can do is we can measure, we can perform the measurement in any orientation of the blades. So you don’t have to be at six o’clock for example, you could even have a one, you could even do a one stop inspection of the, of all three blades of the turbine.
Joel Saxum: Yeah, that’s huge. Especially if you’re out flying where there’s like a low wind conditions, because I’ve been there before. Where you’re trying to get that thing to spin and you’re just like, come on. Everybody’s watching it. Alright. Hit the brake , okay, so you’re gonna walk up to the turbine.
You’re more than likely gonna hook the bottom lead of the tether to a bolt one of the, one of the bolts on the flange on the base of the foundation. And then the other part of it is going to be, it’s going to be tethered to the drone’s gonna go up. You’re gonna find the receptors, you’re gonna make contact and you’re gonna check test.
Every receptor in the blade. So if you’re looking at a V 110, that’s got eight receptors and a solid metal tip, you’re going to want to test every one of them to see if there’s an open circuit in any one of them.
Laurent Zimmerli: Exactly. So the procedure is exactly as you described. You have a, you, you ground it to the base of the turbine.
There’s an ohm meter on the ground, which is doing the actual resistivity measurement, and then you have a long tether who connects to the drone. The tether is 300 meters long. So we can fly up to 250 meters. And then it’s a super thin cable, basically, just to minimize the weight, the payload weight, and then it pulls up the cable, and then we have a needle probe which consists of four needles, and then basically the pilot has a tablet with a first person view of the drone.
So there’s two cameras on the drone. One is a wide angle shot, and one is a basically a close up. So they can see, basically aim at the receptor. There’s assistant systems that help the pilot to aim. And then, once we are about a foot, one or two, two foot away from the receptor, there is an interaction switch on the remote.
So the actual interaction is done autonomously by the drone. So the pilot then doesn’t touch the sticks and just flips the switch. And then the drone approaches the blade and pushes like at the constant force until the pilot says it’s okay. And pulls back because then basically the attention of the pilot becomes like the attention of the inspector, the attention of the, to the inspection.
And they can check, okay, what’s the value? Is there a proper reading? If yes. Save the measurement and then pull it back and go to the next one.
Joel Saxum: Okay. So then I’m going to ask another question here. I don’t, I know it’s different country by country, but because you’re care, technically carrying a payload, is there any FAA drone flight rules that, that you guys have to circumvent, or is it basically, Hey, you’re just flying a drone.
You’re good to go.
Laurent Zimmerli: We’re basically more or less. It’s the latter. It’s where we’re good to go because the overall weight of the drone is quite is Okay. Six kilograms, which is about 10 to 12 pounds.
Joel Saxum: You’re under the limit. Yeah.
Laurent Zimmerli: Yeah, absolutely. So there is no special permissions required in the US to fly the drone as such.
Of course, the regulations around the piloting and the registration for remote ID, etc. That’s the same. But there is no special permission required for the drone as such.
Allen Hall: Laurent, what’s the business model here? Is the drone available for purchase or to rent or lease? If I’m an operator and I have, in the United States, several thousand turbines that I probably need to inspect over time, do I just lease the drone and then I have my own technicians that can fly it?
Do I? You have to have a special person brought in to fly the drone. What’s the approach here?
Laurent Zimmerli: I usually say we’re a technology provider. So we’re providing the technology to the inspectors. And what we, how we do that is in terms of a robot as a service subscription, which is a quite a new model in the robotics or drones world.
At least that’s what a lot of people tell us. So what we do is for an annual subscription fee, we provide our customers with the drone, The payloads. So for the LPS, there’s an LPS testing payloads for the NDT. There is an NDT bundle. So depending on what you’re doing, you’re getting the right payloads.
And part of that subscription is not just the technology as such. It’s also the training. So to make sure that your pilots are are basically learning yeah, that they learn how to use the system also in on ideal conditions, obviously, and they learn the procedures and all of that. So that’s included in the subscription.
Usually what we always do or will also do or try to do always is after to, we try to schedule the training close to their first actual inspection work. And then we basically go on site with them. And then we wouldn’t do the inspection ourselves, but we would just be there. To give them more confidence.
If there’s any like emergency situations that we will be there. So just to boost the confidence basically. And so that’s how we do that. But from then on our customers are using the technology themselves. But then what we also provide as part of the subscription is all the updates. It’s a first generation product.
So there’s quite frequent iterations, especially on the software side, sometimes on the hardware side. So that all of that is part of the subscription. We also have a crash insurance part of the subscription. So if there is a crash…
Allen Hall: I think Joel would need that for sure.
Joel Saxum: I’ve crashed a few drones and some expensive ones too.
Laurent Zimmerli: I crashed a few drones before, but I knock on wood. I haven’t crashed one of ours. So yeah, that’s part of the subscription as well, because as we discussed before, there’s so many factors here. We’re close to procedures. Even the best pilots might have a bad day because there’s environmental influence or whatever, so things can happen.
And after all it’s a fine piece of high tech. So it’s things can happen. So that’s why you make that part of the subscription. So that we can replace that, especially if people are, if our customers are on campaigns, that’s super helpful for them because then they are like in a limited timeframe where they need to get a job done.
So that’s something that they appreciate a lot. And all the support basically in general is part of the subscriptions, there are spare parts. There is software updates. Again, I mentioned those any kind of troubleshooting. And then after a year. When the, basically when you decide to extend the subscription and do another year, instead of just doing common maintenance, we would just basically provide you with a new drone.
So you have the latest and greatest technology, and then we will refurbish the old and bring it back into the cycle. Basically.
Joel Saxum: That’s huge. That’s big time because. Drones, if you look at say the flyability drone, those motors operate at super high RPM, 10, 000 RPM crazy, but they have a really limited hour bandwidth on them, where they say Hey, at this many hours, you have to replace these motors no matter what, otherwise, if you crash, not our problem. And that, That is actually pretty common with a lot of drones and people just don’t realize it. So getting a brand new kit, that’s huge. That’s important.
Allen Hall: Laurent where does all the data go from the Voliro drone?
When is there an online cloud that the data is uploaded to that the customer has access to? How does that work?
Laurent Zimmerli: So if you go back to the procedures, what happens is, so the pilot goes up, does some, it takes some measurements and then like first they’re stored on the drone. So all the data is on the drone basically.
And, but then once the job is done and the pilot is going back to to, to their office or hotel room or whatever, they can connect to wifi and upload the data automatically to the cloud. And from the cloud, they can download a a report, the PDF report that basically reports all the details of the measurements.
And PDF is one that’s usually the most common format that customers ask for. However, what we also provide is raw data. So if they have a system, a software system that consumes this kind of data. Then we can also provide raw data and insert that into existing software systems.
Allen Hall: Does that data consist of images and resistance measurements?
Because I know, in the lightning business, we see a lot of damage around the receptors. So does that, do you include those images? So if they had some damage, they would see that in the report?
Laurent Zimmerli: Absolutely. As I mentioned earlier, we have two cameras, so we have the closeup and the wide angle. And whenever a measurement is triggered both cameras take a picture.
And they there’s a measurement, a timestamp, the geolocation. The pictures and all of that is automatically and pops up in the report.
Allen Hall: That’s impressive technology. I’m really interested in this and it’s, this is going to be a busy season for you from what Joel and I have seen over lightning strikes last year.
And it already starting in 2024, it’s going to be an insane year for LPS measurements. So Voliro is well positioned to do some work this year.
Laurent Zimmerli: We’re prepared.
Allen Hall: All right. It’s been great to have you on the program. How do people reach out to Voliro? Where can they find you?
Laurent Zimmerli: So the easiest way is definitely our website.
There’s a contact form and an email address or on LinkedIn. So that’s definitely the easiest way to reach out. And then we are more than happy to arrange a call or a demo for anybody who’s interested.
Allen Hall: This has been great. Laurent, thank you so much for being on the program.
Laurent Zimmerli: Thank you, Allen. Thanks, Joel.
It was great to be on the show.