The Uptime Wind Energy Podcast
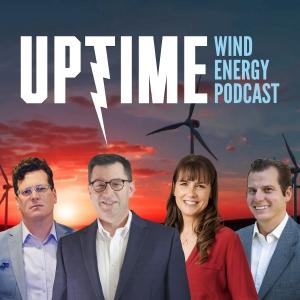
DTU and R&D Test Systems Open Cutting-Edge Rain Erosion Facility
Allen Hall interviews Nicolai Johansen and Jesper Dal Hasager at DTU’s brand new R&D Rain Erosion Facility for testing leading edge erosion on wind turbine blades. They discuss the unique features and capabilities that make this one of the most sophisticated erosion testing rigs in the world. Visit https://wind.dtu.dk/facilities/leading-edge-erosion-test-facility for more info!
Sign up now for Uptime Tech News, our weekly email update on all things wind technology. This episode is sponsored by Weather Guard Lightning Tech. Learn more about Weather Guard’s StrikeTape Wind Turbine LPS retrofit. Follow the show on Facebook, YouTube, Twitter, Linkedin and visit Weather Guard on the web. And subscribe to Rosemary Barnes’ YouTube channel here. Have a question we can answer on the show? Email us!
Pardalote Consulting – https://www.pardaloteconsulting.com
Weather Guard Lightning Tech – www.weatherguardwind.com
Intelstor – https://www.intelstor.com
Allen Hall: Welcome to the special edition of the Uptime Wind Energy Podcast. I’m your host, Allen Hall, and I am in Roskilde, Denmark, with the folks from DTU and R&D Test Systems, because we have a brand new rain erosion facility. And I’ve just been attending the 5th Symposium on Leading Edge Erosion this week, and there’s been a tremendous amount of new technical knowledge and test results and computational efforts going on across the world.
And it’s time to talk about the real issues. rubber hit the road part, which is the rain erosion testing. And I have here today, Nicolai Johansen with DTU the Risø campus, which is the wind energy and energy system. Energy systems department. Yes, we just had a magnificent tour of the facility, and there’s some amazing pieces here.
I didn’t realize what kind of technology DTU has. It’s astounding. It’s quite nice. It’s better than anything I’ve seen in the United States. You should be proud of it. It’s really nice. And this is one of those new facilities that has been built by Jesper Dal Hasager, who is with R&D Test Systems.
So welcome to the podcast. Thank you. Thank you. This is impressive. So I, we have talked to R&D Test Systems in the past about a lot of different things, one of them, rain erosion test facilities, that this is a kind of a standard thing that R&D Test Systems does. because there’s such a big demand for it.
Jesper Dal Hasager: Exactly.
Allen Hall: And I haven’t seen this up close, but seeing it up here now, this is amazing. This is a really nice setup. Thought out. And this setup is the most advanced one in the world at the moment. Exactly. So you want to describe what makes this the most advanced main erosion test facility?
Jesper Dal Hasager: Yeah, first of all the test chamber is larger than normal. One belt. It’s we normally either we deliver the system within two containers.
Allen Hall: Okay.
Jesper Dal Hasager: Two 20 feet containers, high cube containers. Or we can deliver it into a building so we can integrate it in a customer building Sure. Solution if they want to have a building instead of this modular.
But then we have thought of a lot of these containers. It’s not, that’s nice to look at this container, but still a building is very expensive for It’s yes. For our customer to build themselves. Sure. So we designed a middle way in this one. Where we have this steel structure that we have welded in our workshop in Hinderup and, yeah.
And then we have mounted these sandwich panels with 80 millimeters insulation.
Allen Hall: Yes, it’s quite warm in here. Yeah, exactly. It feels good. It’s because it’s cold outside.
Jesper Dal Hasager: Yeah, exactly. So that should both cope for the temperature and for sound dampening. Yes. Because it’s a very loud machine when it’s beginning to turn around.
Allen Hall: That’s very smart design because I think a lot of people wouldn’t think about those design details of just the day to day operation. I’ve been to some of these facilities and they are tremendously loud. Yeah. It’s going to make sense.
Jesper Dal Hasager: And one of the reasons we did it is because we have our own Rain erosion tester at our facility.
And it’s very loud. So it’s okay, we have an issue here. We have to solve it.
Allen Hall: So Nikolai got the quiet one. He has the most quiet one. We’re going to find out.
Nicolai Johansen: There is a certain budget for sound mitigation, because one of the main concerns we have, of course, like we are in a, Officially zoned industrial.
Yeah. So we are allowed to make noise, but of course we shouldn’t both be noisy to our neighbors, but also more importantly, the wind tunnel just next door is designed to be an acoustic wind tunnel. So for sure we will make sure that we’re not disturbing whatever measurement is going on over there for measuring noise on aerodynamic profiles.
But, and yeah, again the building was also one of the things we settled on relatively early in the process. So I can. Way back when we, like two years ago, when me and Jakob Illstedt were back we went around literally scouting the old buildings and research is there any of these old buildings we could fit in a machine?
But then quite quickly Modifying and overbuilding to house this quickly turned out to be much more expensive than going something where we can control all the factors.
Allen Hall: Yeah, it’s very modular and it’s really easy to set up. How long have you been on site to actually start assembling this?
Jesper Dal Hasager: We started I think it was one week before Christmas.
We were here one week to, to set up the test chamber. It came in four walls and two floor sections. Okay. And two ceiling set section. Okay. So we put that up also The, this huge concrete block in here. Three tons. Tons of concrete. Three tons of concrete, yeah. Okay. To ensure this data and the road.
Okay. So we put that up windy and cold december day. I was in the office, but I was, thank you very much to, I was out here all day and the, and outside installation crew. So they put that up. Then they left it came back after after New Year, we had a blizzard we had to cope for so we got a little delayed.
And then they begin to build up all the steel structure and outside we have a heat pump for temperature regulation inside the test chamber.
Allen Hall: So it’s a three piece kit, so there’s a little bit outside, there’s actually two sub buildings outside.
Jesper Dal Hasager: The two sub buildings, that’s also one thing, usually we only Deliver one control facility but of course, new line wanted another one or did you,
Allen Hall: uh, that’s okay because I think you’re going to need it with customers coming in and the base.
Nicolai Johansen: The normal option does work, but you’re setting it a little bit of a shoebox. Let’s find out. Be honest, .
Allen Hall: So for the control room, that’s exactly what you need though. And I think because it’s DTU and you have a lot of people coming from the outside to it, you need a separate place where the engineers can huddle up.
Nicolai Johansen: And I typically I think large, the landscape facility, that’s just the next door. They, I think they managed 70 tours last year. Wow. Okay. So like the amount of public flow through is quite large. So it’s worth considering that whenever you do anything here Sure. And then again, like the one, the unique thing in in, in the erosion test here is that it’s really the first one that’s in a pure university setting of the R&D Of course there’s the old machines from the cold, all the cold era machines.
They exist in some universities. Sure. But so far all the R&D test have been in commercial settings. Exactly. To one extent. There’s the one in Japan that’s semi open and then of course there’s all catapults machine.
Allen Hall: So we’re talking in the beginning of February. So it’s literally taking a little over 30 days to get the work.
You’re going to be up and running in around
Jesper Dal Hasager: two, two, two weeks. I think,
Allen Hall: wow.
Jesper Dal Hasager: When we have it all the hardware installed and the wiring then we have a lot of running of the machine. We need to be sure that this is this is running as we expect and that the test result is repo repeatability.
Sure. That’s the key. So we can repeat the results, right? And to ensure that we run eight calibration tests. And these calibration tests we run for ten hours each.
Allen Hall: Ten hours? Continuous?
Jesper Dal Hasager: Yeah, continuous. To make sure that the calibration is correct.
Allen Hall: Okay. And in the calibration, we’ll talk about the calibration in a minute, because I think that’s part of the details about this particular unit, which is unique in the way that it can, one, control temperature, two, the amount of water it can pump through it, three, it has two different sets of needles that actually make droplets, and that’s just what I visually see.
I assume there’s some other bells and whistles that are in this machine that make it unique.
Nicolai Johansen: Yeah, for sure. Again, we’ve had a lot of inputs and what the design we wanted in it. And one of the main things is the droplet generation system, as you say, because it goes back to two studies we’ve done.
And also R&D has been partnering projects there where we looked at various drop size and flow rates and amount of water. And one of the things we pinpointed is, yes, you can accelerate the test by going faster, but it seems to provoke failure modes that we don’t necessarily want. But there seemed to be leeway in adding more water into the tester, or at least that’s something we wanted to look at.
And that’s where we beefed up a lot, both with, then we have one set of normal manifolds, that’s 600 individual needles that sit around and drop. And then we added the second extended manifolds, that’s 20 needles per manifold for an additional 1200 needles. So We go from 600 to 800, 1800 needles.
Allen Hall: 1800 needles that are dropping water.
Jesper Dal Hasager: And Nikolai has to change them each week. No, not each week. That’s a lot of needles.
Nicolai Johansen: That would be a master student job.
Allen Hall: No. I think it leads to the point of the reason that this level of machine is needed today is because we still have trouble in service with leading edge erosion. It is one of the most universal problems that wind turbine owners and operators have today.
Everywhere I’ve traveled in the United States, every wind turbine has some level. We saw some presentations today from Brazil. Yeah. Yeah. It looked like next level erosion. It is a major problem. And the issue is not having enough test equipment for the companies that make protective coatings to go test and to look at what the variables are, because I think there’s, being at the symposium this week, that’s one of the discussions is what variables are the variables that we need to focus on.
And we don’t have enough machines to go do that. And this machine is going to help eliminate some of those things that we’ve been talking about and get to some real data, I think.
Nicolai Johansen: And at the level that there is, I guess we say this will be the machine number 15. So there’s a lot of these now in the wild, but as I say, they are within companies that they run more or less 24 seven, most of the machines I know, but they can qualify.
But for a university setting that becomes limiting in what’s. If they already run it, everyone runs at the standard conditions, then we never really get outside the box and figure out the really the core driving things.
Allen Hall: It’s the research part of this, which is the bonus you guys have is that you can expand that envelope.
Whereas a lot of the testing, Nikolai, you’re a hundred percent right. The, if you go from R&D test system to R&D test system units, they’re very consistent. That’s why everybody loves those systems because they do this focus thing. But as we are learning this week there are. There’s a, it’s a big world out there, and the raindrops aren’t all the same, and South America is different than North America, and Europe’s a little bit different, so everybody needs to have their own understanding of what’s happening, and we need to have the brains at DTU going to figure this out.
Where else you gonna do this? Exactly. Yeah, it’s here. And in, in terms of what this system does I think we ought to take a step back here, because if you’re new to leading edge erosion, That’s right. And you’ve never seen one of these machines before it is Nikolai, maybe you want to describe what it is, what it does, how it works and the magic of this system.
Nicolai Johansen: Yeah. So I can bring a prop in. So this is an example of an uncoated specimen. We would put that would go into the, to the tester and with all the needles going around and the blade where you can imagine there’s a higher tip speed at the tip and a lower speed towards the middle. Yeah.
And as the test runs the asbestos sample is inspected at certain intervals, and you’ll see if it was well behaving and erosion front progressing from the tip going towards the root. But in many cases like that might not be. But again we broke it at certain stage and we observe main, the main observation method will is through the camera system that will soon be mounted over here.
That’s the key. Yeah. And. And that’s also things that we might expand on. But as it erodes, then we can track the erosion and we can measure the amount of water in the rain that impinged the blade, right? That got to that failure mode. And with that data, we can then go use a climate model, a rain model of, for an actual turbine site.
And get to an estimate of lifetime for the side. We know there’s, even though this aims to replicate as much as the real conditions as possible, there’s still. A significant jump from what happens in here to what happens
Allen Hall: And this is a three blade system, so you could put three samples on simultaneously.
Would you do three of the exact same coding at the same time, or do they vary that?
Nicolai Johansen: Typically, we would always go with three of the same. One thing is, if it erodes evenly, then the rotor remains more balanced. Oh, sure. And also, it’s again, duplication and replication of results, so you get a minimum three replicants of each material tested.
And that’s one of the things that’s from my point of view the biggest difference in, in historical rain erosion test is also whirling arm test that says that often there was short sample or coupon. So you’re only really get testing one speed at one time. So you imagine if you’re building a plot with velocity, a number of impacts to failure, you would have to do repeat experiments for each time.
Sure. Whereas with the longer specimen and the way the rain field is configured here, we get. Proportionately more impacts towards the root, but actually for one sweep around, each part of the blade sees the same amount of droplet impacts. But that means that you get a slightly more even erosion. Over. So you get more out of your samples.
One sample can sometimes cover a 30 meters a second range from the tip to the root. So then you are like halfway to your to a usable curve. So you cut down significant on the time, but there’s a bit more analysis on. on the back end.
Allen Hall: So this, a lot of the rain roof rain erosion facilities in the United States are older, right?
And there are two blade systems. So the three blade makes a lot of sense in terms of samples and running the samples and trying to get the most data you can for the time, right? There is a time element to this because some of these samples run for hours before anything noticeable happens. I don’t know what the typical length is.
What’s a typical length you run it for a coding today? What does that look like now?
Nicolai Johansen: It’s varied a lot. Like when I started looking at this, I said for you, then it was only like half an hour.
Allen Hall: Yeah, we were running things in minutes.
Nicolai Johansen: Yeah, we were running it at full speed and then it dropped down and now there are things that run for 300 hours.
We saw some of the, we also had some of our own. Liquid LEPs and the Dual Edge project, there was one of them we had to give up on because after everybody’s tested for 400 hours like this, we don’t have budget to run it for anybody.
But yeah so they’ve become longer and longer tests.
Allen Hall: And that’s the point, right? Is that we’re trying to build more durable coding so that we have less issues out in the field, but that also lends itself to R&D Test Systems. If you’re going to run 400 hours for one set of samples, and you’re going to do that repeatedly, this thing has to run because my guess is that the line of customers that are going to be in here is, it’s going to be busy.
Exactly. This machine can’t be down. No. Yeah. And it looks like you’ve over designed this thing in a sense. What’s the motor size that’s actually spinning this?
Jesper Dal Hasager: The motor size is if it’s running at 50 hertz, yeah, it’s 37 kilowatts. Whoa, so that’s a huge motor. That’s what we have seen Sometimes when we run it in things are going fast and we had sometimes Forgetting to put in the samples and then we can’t understand why it can’t run, above 1200 Rpms.
Yeah, and we said come on. Come on. Come on, but it’s actually just the drag of the wind
Allen Hall: Really?
Jesper Dal Hasager: Yeah that’s holding it back as soon as we then go in and put in the samples You Then we can spin up to the aerospace version with the same motor. We can spin up to 1, 790 RPM.
Allen Hall: What’s that in kilometers per hour?
Jesper Dal Hasager: That’s 800 kilometers per hour at tip speed. At tip speed. Okay, so that’s for aerospace industry.
Allen Hall: And what is the tip speed of this particular unit?
Jesper Dal Hasager: It goes to 173 meters per second.
Allen Hall: So that’s about 350 miles an hour or so, roughly.
Nicolai Johansen: Yeah, so it’s 540 kilometers an hour. Kilometers an hour.
Allen Hall: That sounds about right.
Nicolai Johansen: All the conversions.
Allen Hall: Sorry, that’s America. Yeah, we use strange units. But that, that, that speed though is needed because of the speed, but we’re also finding that maybe we don’t want to run as fast because that maybe causes some unnatural things.
Nicolai Johansen: Yeah, that’s been, I think, the trend we have. I’ve been with the, dealing with some of the radio test data since 2016 and we see more and more people want to go lower and lower in velocity. And we’ve also gone down to realistic speeds. But again, it’s on a power curve with an exponent of minus five or eight or something. So going a little bit down in speed drastically, it goes up in time.
Allen Hall: Sure. But there’s reasons to do that. And then you have to have a reliable system in order to be able to do that.
And I do, if I’m a coating developer. At some point, I want to run it at regular tip speed maybe plus 10%, maybe plus 20%, and see how long it goes before I notice anything. I think it’s a valuable thing for customers of those materials. So yeah, that makes a lot of sense. Now, the, the complexity and the ability to add on to this, we’re talking about cameras, it has lights, right?
So it has lights to take photographs. I assume that the lights are to take photographs as the blade passes through.
Jesper Dal Hasager: When it passes through, you can set up the test for a certain amount of time, so you can put it up. I want to have it analyzed each 30 minutes. So it will run at the setting speed for 30 minutes with water dripping.
The water will stop dripping, and then it will dry the blades, and it will spin down to around 6 RPM. And then we’ll, it will take the images, the light will come on and it will take images. So it’ll do the photographs without taking the leading edge off to actually Yeah, exactly. Wow. So that’s one of the things that make it, it fast.
Of course, you don’t get all the details, but you can get an idea of where are we. And the operator can sit from remote distance at a screen. Yeah, look. Okay. Now the next picture has come in. Okay. Not enough erosion yet. We run it for an hour more. Keep going. Yeah, keep going. And suddenly, oh, now we’re there.
Then they can go out and make a better analyze and further analyze it. Maybe take it out. Sure. Scan it or something.
Allen Hall: Wow. Yeah. And if you want to learn about the material, it’s just going to weigh it, that’s the other thing. Material loss, which can be done a DTU , right? Yeah.
Nicolai Johansen: Of course we can do, but I would say.
For these, that’s the downside of the long specimen because you get erosion over a longer range and you do get material loss and you can measure it, but you’re, you never, you’ll never know at which velocity the material loss happened. So that’s the downside to going a long distributed impact compared to, to, to the short sample.
Allen Hall: Let me ask you this general question here, because this is. There’s different kinds of randomization facilities. When it’s dripping water, are the water droplets timed or are they just randomly happening? Because I’ve seen both.
Jesper Dal Hasager: They happen when they want to.
Allen Hall: Okay, that’s what I prefer.
Jesper Dal Hasager: That depends on the surface tension of what water is coming in.
Allen Hall: And can you vary the water a little bit that goes through the needles? Is there a little bit of
Jesper Dal Hasager: We can change the size of the needle and we can change the flow rate. So we can put the flow rate up and down and adjust the needles depending on which droplet size you want.
Nicolai Johansen: And the basic science to controlling it is that it’s a semi stable hanging pendant drop.
And a hanging pendant, the size of a drop there is defined by the outer circumference of the needle. So that’s the balance between the surface contact forces that says how big the droplet can be. So if you put in a bigger needle, you have a longer circumference and you get a bigger droplet. But of course, this is this, that would be in perfect steady state.
This is not in a steady state, but it still defines the needle to a larger extent. But what we might also want to look into is another mode of operation. That’s where you, instead of having the drop, we let them spray. That makes the distribution wider. But it might actually from when we talk with our metrologist, or that’s another department of the, another section of the department, the metrologist, they say these 2.
4 millimeter droplets, that’s way too large. The most of droplets in nature that we see in rain are much smaller. So it’s one of the directions we will look into.
Allen Hall: That’s why the machine is here. So you can do those adjustments. And that’s why, you call R&D Test Systems to make this thing because it is adaptable.
And if you, if. There’s a lot of needles that have to be replaced still. I only see a couple of them hanging down. So is that a routine piece that has to be replaced every once in a while? It seems like they’re heavily used.
Jesper Dal Hasager: Some customers are having like a service maintenance interval that they change needle one, needle two, needle three at each manifold.
And then over. a year, they have changed it all. Maybe.
Allen Hall: Oh, they change them over the cycle.
Jesper Dal Hasager: So they’re not changing every needle each day but or each time. You could also do just to look at them, verify, okay, now it’s not dripping as we like it. And we can change that needle or we can change the other one.
Okay. But what we have seen the most important is like an old diesel car, you need to get it running all the time. You need to run. Yeah. Then you don’t need to change that much. And that’s why we have one of the thing that you as requested here is to get a water recycling system for this one.
So we implemented this also to get the water recycled. We are using as less water as possible
Allen Hall: because this system can use a lot of water.
Nicolai Johansen: Yeah. So the maximum flow rate is 400 liters an hour of the system. And in a traditional machine that would all go to the drain, of course, while the machine is running a significant part is going to go out of ventilation because a significant amount of the droplets turn to mist.
But again, there are these considerations, both with the heat pump and water reclaiming it’s, let’s be honest, it’s not financial It’s not a viable option if you just look at the money, but I still, as a university, we have to take these considerations in if you look at the cost of everything and what they, what influences the cost of running a test, it’s insignificant, but I, we have a responsibility to choose an option that minimizes the elements.
Allen Hall: That makes total sense. I think it’s a responsible thing to do. And let’s talk about it from a customer’s perspective, right? If I’m a coding developer or I have some new great idea about leading edge protection, I guess I’m calling DTU . That’s the first thing I’m doing. And then what are the steps?
What are the next steps I need to do? How do I get these samples made? These leading edges? Is that something I have to talk to you about? Do I make them myself? Is it a, yeah
Nicolai Johansen: It’s a process we’re getting into. So our plan is to, to up our own capabilities. Sure. Both have. The traditional way you would buy your shells from the main manufacturer right now is Olsen Wings.
But we’re also having molds made to, to be able to make our own because there are some, sometimes an operator is concerned about what is the effect of the layout on the erosion. We’re also moving into the realm of biocomposites. And I, we’ve done some preliminary work with a student in Bergen looking at Flex composites for impact position and they seem to be quite good.
So there could be something there. Yeah. Wow. More testing to do. Okay. Yeah. But then again it, that will be one of the things we will focus in on over the next year. To get the kils, you have to make our own for the mid majority of samples. We’ll probably buy them externally and then we’ll figure out how to coat them something.
We’ll coat here, but we also have a. A collaboration with found over from to join forces on some of the coating works. So again, it’s a big it’s a big community. I think that’s one of the slightly unique things are things about rain erosion that it’s. More open and shareable than I think a lot of sort of industry driven technical fields.
Allen Hall: It is. Right now it is because everybody’s trying to find a solution. There’s so many variables.
Nicolai Johansen: And also like it, it was not the universities that started off the work on erosion. It was the OEMs and two cross and then two. Joined industry projects, the Cobra and Biceps project.
Was I think biceps predated our entry into rate erosion and COBRA came afterwards. But like it’s been interesting to see like from a university that the, that you can get both Siemens Vestas and LM to sit in the same room and agree to share data, I think was
Allen Hall: Sure. Sure.
That’s not their core
business. No. Their core business is making wind turbines and making them run a long time. And this is a problem that needed. needed researchers and R&D Test Systems to get in the mix here, to get the test equipment where it needed to be and to just do what we just did in this symposium and get all the smart people together in a room and let’s figure this thing out.
So if I’m a customer and I get this leading edge and I put my new magic coding on, it’s going to solve all problems. I come over to Nikolai and I say, All right, Nikolai, what happens? We install them on this on the test rig. And I tell you, just go test it. Is there a standard that’s used in the world today to go test?
Nicolai Johansen: So the, also one of the reasons for this machine is it’s covered by like two two industry recommended practices. They’re not quite standards yet, but I know there’s something on the way. So DNVDL has the two recommended practices. One describes the tester and one describes how to use the data from the tester to go to the field.
And I say that’s the jumping off point. We have some, we have more that we’ve developed on over the years working with it. So we would probably recommend that we start also looking at some of the dynamical mechanical properties with DMA testers, which we also have invested in before, before the erosion.
Allen Hall: I just walked through that facility the materials facility. It’s fantastic. So that would make. That’s why you’re at a research institute like DTU , is that you can hop over to the materials lab, check out the material before it even gets on to the whirling arm here.
Nicolai Johansen: Yeah, and again, it’s what we’re tied into.
The condition that happens in radio erosion is so different from all the other kind of mechanical tests we have, because it happens in like a split second. When you look at the times, the peak stress has happened two microseconds after the droplet touches the surface. Yes. And even if you have the slightest amount of deformation, anything that happens in two microseconds means that you have both high strain and high strain rates.
Yes. And those two things are very difficult to test in any conventional means. They are. Our best approach now seems to be like dynamical mechanical analysis and some of the impact testing we’ve done. But that’s our jumping off point now, but a lot more is going on to get deeper into the materials.
Allen Hall: So if I get my material on, we get to the, we get to the materials test and we get it onto the rain erosion rig, it’s going to run for how long?
Nicolai Johansen: Until until the machine says it’s vibrating too much. I don’t. That’s a good indicator. And then there’s different, I think the general recommendation is if it started eroding too much into the laminate, you should stop.
Okay. I’ve seen there are some operators that are a little bit more brave and they continue until it’s eroded all the way through. But that’s with the risk of of losing a blade, which is why there’s a one inch blade.
Allen Hall: Is it one inch steel? What is that?
Jesper Dal Hasager: It’s 20 centimeters. 20 centimeters.
So I’ve been there. I don’t know. Try to be exactly. Wow. Yeah. Yeah. So even though
Allen Hall: Does this get used in some of the testing? Yeah. Parts come off and sidewall?
Jesper Dal Hasager: It hits the wall, take off the initial power of it and forces. And then it bounce back and sometimes it takes off some hoses and then, and of course we have a package for that you can run.
So you just say, Nikolai, when you do that, we are ready to come to ask you with our service to fix it. The service contract.
Allen Hall: You’re going to need it. If it’s used the way it should be, you’re going to need service on it. And that’s a good thing because R&D Test Systems is right there to come over and help you.
Jesper Dal Hasager: It’s to ensure that the safety is always up to date and that the machine is running as we expect. So we will check the rotor each year and the bearings and. All bolts and nuts if we go all through that to ensure that the are tightened and that it works.
Allen Hall: Yeah, that’s what the test phase is going to do before you really go live.
And yeah, it makes sense that R&D test system, obviously everybody knows, right? That company makes incredible machines that are unheard of in the world.
Jesper Dal Hasager: So we use the same procedure in this quite, for us, for R&D testing, this is a small machine, but we use the same procedures to ensure the safety.
So even though we make these large scale test system for the industry then we use the same procedure here.
Allen Hall: Just looking at it, it’s magnificent. And I know we run across a lot of operators in the United States that are thinking about different kinds of coatings. And one of the, one of the questions is how long is it going to last?
And do I need to go do some testing on my own? I don’t necessarily trust the manufacturer of coating and I get it. And that’s a common theme today, but they don’t know where to go. And especially in the United States, there’s a lot of large operators, 10, 000 turbines or more, right? They need to come someplace and do some testing.
And they have engineers, they have bright people, but they just don’t have the facilities to come to. You need to get on an airplane, get over here to Roskilde, and run some testing. Because I think that’s the way that they’re going to convince themselves that they have a solution for their particular situation, their particular rain, their particular temperature extremes, their particular tip velocities.
This is where you would go to do that work. And this whole facility is magnificent. And I’m so lucky to be here at this moment to see it before it goes live. And congratulations. This is a lot of hard work to come into this. This has been how many years of your life that you’ve been around?
Jesper Dal Hasager: I’ve been for R&D for two years, but I know my, what’s called processor. Yes. Yeah. was there for also five years, I think. And Nikolaj has been there for most of the time, supporting us. The unofficial R&D employee. Exactly.
Allen Hall: So Nikolai, do you get a set of keys when it comes? Does he get like a new car? Or do you get some
Nicolai Johansen: There was a weird key hanging over one of the containers that I stole.
I’ve changed the lock.
Allen Hall: It’s gonna make you feel proud. This is another thing that DTU does extremely well and it just adds to the abilities of this research facility and it’s amazing. Congratulations! Yeah, you’re the elected recipient of a brand new Rain Erosion facility.
Nicolai Johansen: Again, It’s it, the team effort and like I, I took over the last part, but it’s been like the entire department coming together and agreeing, starting it up and then through the entire management, getting it up and push it because like we did this investment on internal funds, which is also it’s a big ask to say, okay we’ll take our own money. It’s part of the department has, it’s quite good at making its own money at time, but often it goes straight back to main campus. But then that allows us from time to do these investments that of course you can do this and find, try to look for funding, but then the process goes from our total process was maybe two years, but a lot of it was just where we were waiting. Yeah. If you’re going the funding way, then maybe you are spending five, 10 years trying to. Slow the last bit of money out to, to do it.
Allen Hall: It’s wonderful to made a decision. I think it’s very smart decision. It’s a long-term investment into the wind energy community and I think it’s gonna, it’s really gonna pay off.
And if any operator or owner OEM is interested in getting up to DTU to do some testing, how do they find you on the web?
Nicolai Johansen: So if you’re tired, search for the Risø leading Edge erosion facility, you should hit our homepage. Okay. Otherwise, the. The wind energy systems that you guys to go in and look under our system.
So I guess there’ll also be a link or something.
And then get in contact with me or whoever, then we’ll set up the process. We are still learning how the real workflow is going to be but we have a large part of the department’s business is commercial testing. So it’s not that commercial testing is anything new for us.
Sure. Yeah. I think there’s about 400 commercial jobs going through the labs every year wow.
Allen Hall: Okay.
Nicolai Johansen: There’s a workflow for it. It’ll just be a little different for this than than some of your other tests.
Allen Hall: We’ll put the, in the website, in the show notes, and I think there’s a LinkedIn page also that people can connect to.
And we’ll get all that information out so everybody can find you because this is the place to go. And Jesper congratulations on this facility. It is magnificent. Nicolai, you’re the luckiest person in Denmark at the moment. So congratulations and thanks for being on the podcast. This has been wonderful.