The Uptime Wind Energy Podcast
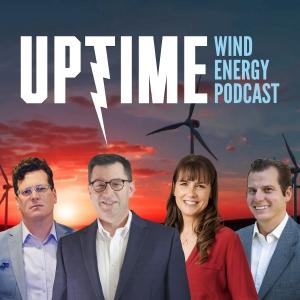
Improving Blade Quality: Challenges and Opportunities with Mohammed Fajar
Rosemary had a great discussion with blade expert Mohammed Fajar about blade defects, the blade design and certification process, and how optimization and automation could improve blade quality. Mohammed provides perspective on recent issues with turbine OEMs like Siemens Gamesa, and expresses optimism about wind power’s future, particularly offshore! With both of their extensive blade knowledge, they explore how human factors in blade manufacturing lead to inconsistencies and why the industry struggles to implement more automation.
Sign up now for Uptime Tech News, our weekly email update on all things wind technology. This episode is sponsored by Weather Guard Lightning Tech. Learn more about Weather Guard’s StrikeTape Wind Turbine LPS retrofit. Follow the show on Facebook, YouTube, Twitter, LinkedIn and visit Weather Guard on the web. And subscribe to Rosemary Barnes’ YouTube channel here. Have a question we can answer on the show? Email us!
Apex Wind – https://www.apexwind.dk
Pardalote Consulting – https://www.pardaloteconsulting.com
Weather Guard Lightning Tech – www.weatherguardwind.com
Intelstor – https://www.intelstor.com
Rosemary: Hello and welcome to a special episode of the Uptime Wind Energy Podcast. I’m Rosie Barnes and today I’m joined by Mohamed Fajar, founder and blade consultant at Apex Wind. We used to be colleagues actually at LM Wind Power when Mohamed was a senior structural design engineer who took five blade designs through the certification process.
So wind turbine blade defects are very topical at the moment with what’s in the news with Siemens Gamesa and also TPI, we’ve talked a lot about that on the podcast. And I thought that Mohammed would be the perfect person to have on to tell us about how the blade design and certification process works, or maybe more accurately how it should work to ensure that blade defects aren’t a problem.
They’re not supposed to be. So thanks heaps for coming on, Mohammed.
Mohammed: Thank you for inviting me.
Rosemary: So I just wanted to start out. Can you tell us a little bit about your background and what you’re doing now at Apex?
Mohammed: I graduated in 2014 as a master in engineering in France about composite structures and materials.
And since then I joined LM Wind Power in Denmark and my journey with blades started. So I started as a structural design engineer. Yeah. As you say, designing blades, for various OEMs, uh, taking them from the conceptual design to the Yeah. Manufacturing and handover to, to the factories. Also worked at yeah, a company called R& D test systems also in Denmark doing test systems for wind.
And then another three and a half years in Vestas in the innovation department. I was working a little bit as the blade owner in the department tech lead in, in all blade related projects. One of them, it’s the, yeah, cable stay drawtor where I also worked on it from the start to almost the end of it.
And then since July 23 I went on my own. I started Apex Wind, as you mentioned, and the goal is, yeah, to have this. It’s a consultancy company, a hundred percent focused on blades. Uh, helping developers, OEMs and startups yeah, to have a blade expert on the side when they need it.
Rosemary: Yeah. It’s good timing to pick a company like that, founding a company like that, because it’s definitely such a need for blade consultants these days, but with yeah, all of the issues that we’re seeing.
Mohammed: Yeah. One of the things that really motivated me to get in, because when it was, for example, on the OEM side, sometimes I feel that there was a struggle finding someone who knows about blades and can help with blades.
Often you end up, even if you want some CAD resources, you end up hiring someone who works with steel or something, and then almost have to teach him how to work with composites. And there was never this full package for people who knows about the whole value chain of blades to know about the design and then the manufacturing, the certification, the testing.
Often I compare it to some other components of let’s just say the nacelle in in, in big companies. You will have the same number of engineers working on the nacelle as working on the blades. And in the place we’ll have all these specialists on lightning on, on foams, on glass and then on liquids and then paint. And that’s why actually sometimes it gets very hard to get that person who can cover all these areas at once.
But yeah, and then the demand is big, but also the issues and the struggles, often they make a lot of noise in the media, but also the cost a lot of money to both, yeah, OEMs, developers and insurances and insurers and so on. And yeah, actually had this. sentence or this mission, when I started, just try to make blades a little bit more reliable again. Because with all I thought, I don’t think there’s a specific person or company to blame, but there is this pressure on costs.
There is these quality issues that keeps coming and then The companies that are trying to fix it, they’re spending money on it, they start maybe spending a little bit of on innovation on new products and so on. And then you just end up just fixing what you have. And sometimes it gets too big that you stop selling some platforms or turbines like what’s happening to Siemens Gamesa at the moment onshore.
Yeah, if I can help a little bit with that, I will be very happy.
Rosemary: Yeah, it’s a timely service that you’re offering. And I think that a lot of manufacturers would be happy to have that resource available. I think maybe it’d be good to start out by giving some background for people that aren’t totally familiar with, what are the issues with blade defects these days?
Can you maybe help just summarize? So I’m talking about Siemens Gamaces their issues with, I think they’ve had some wrinkles and some issues with their bearings as well. Maybe not so specifically blade related. Last time that I checked in, they were up to quite a few billions of dollars in expected cost to remedy that.
And then there’s a little bit from TPI as well, not to the same extent. Is that the issue as you said, or do you have anything to add about what the state of wind turbine blades are these days?
Mohammed: Actually, yeah, there is actually Yeah, a big group of blade defects that happens and some of them happen just during the transport and sometimes they’re just aesthetic.
Majority of them, or like at least the ones that have worse consequences, is the ones that happens often in the factory or even worse during the design. But actually what happens during the design, I have just a feeling that it’s maybe OEMs, they will have a really hard time to admit it. So often outcome of the root cause will come as manufacturing and we all can do, cannot do much except trusting that.
But yeah, in the factories, actually, there is a lot of NDT, non destructive testing that you can do in UT scanning and so on. And you can, again, you find the defect that you find, and then the ones that you don’t find, that’s the one that goes in the turbine.
And that’s the ones that we hear about them a few years later. And yeah, you mentioned wrinkles, wrinkle, it’s actually it’s main and one of very dangerous defects that happens. Yeah, as you said, Siemens Gamers, they also mentioned they had one of these defects in the platforms. They have stopped and they’re actually the physics are easy. Like you have laminate, if half of it is wrinkled, then basically you lose half of the strength. And then once the part that is not wrinkled cracks, then the part that is wrinkled it gets straight and then cracks again. Now actually a lot of days they have these protrusions, carbon protrusions where wrinkles, it’s less of an issue because you can actually control it before placing it on your blade.
But at least let’s say in the root part where you cannot use these protrusions wrinkles yeah, are very present. And sometimes you cannot even find them with this UT methods because if there is just some foam in between the glass, then you cannot get the signal anymore. And let’s say they don’t come from your design and then you have, you design a blade and then mark and then you fix.
You manufacture it in four different locations in Europe and South America and China, you can get three blades that are almost completely different because at one point your design documentation and QMS systems and quality and so on, it has some limitations. And then it ends up at the hands of the people, placing those plies and applying that vacuum and gluing your blade together.
And that’s actually one of the main struggle that people try or OEMs trying to fix, but you do your best, you train people and so on. But there is, yeah, there’s a big turnover in in, in those factories and you end up sadly with, in some cases and actually the CEO of Siemens Games mentioned it in his call last week that he mentioned the Mexico factory. Then it means that Okay, sometimes just one factory can have a lot of defects that some other factories doesn’t have.
And even if your design and all your processes are exactly the same, right? And this also proves or shows how complex is the whole situation because that blade the if it’s designed in, I don’t know, in, in the US or in China, you, it is the same certificate and it’s certified by the same certification body and everything is checked in the same way, but at the end you will manufacture it in two places.
You might get two places that are pretty different actually.
Rosemary: That’s a really good little teaser for the issue that I want to get to at the end. And it raises the whole point of what I wanted to talk to you about, which is how are we supposed to make sure that doesn’t happen. That you just have blades of random quality making it onto wind turbines, which I think is every, wind farm owners biggest nightmare is that, they’ve bought these very expensive wind turbines.
How do they know that they’re not going to the blades aren’t just going to snap off. So I was hoping that you could walk us through step by step, how the process works, so starting off with yeah, how do you even design a blade, a wind turbine blade, and then what is the certification, the manufacturing, the quality checks, how does that work to yeah, supposedly ensure the high quality of all these blades.
And then maybe after you’ve talked about all that, we can go through how it goes wrong and why?
Mohammed: First you will decide that, okay, there is a specific type of turbine that you’re interested in making. Then actually you will have your loads team and aero team and also a little bit the structural team working on defining just the big parameters of this turbine, the exact diameter, the core distribution, the twist, uh, and so on.
And then the outcome of that first step will be an outer geometry of your blade that still might be changed later on during the design phase. But as they say, the big dimensions are fixed and then a good idea about your loads the fatigue loads and then the static loads in the different direction that you will need to design the blade for.
Once you have that, then you will have the structural design engineers starting working. And basically what they will do, they have different tools and then they will start placing almost layer per layer. You can have like thousands of layers sometimes in some blades. Placing that, running your analysis with the loads and then checking the main first failure modes or design drivers, let’s say the strain distribution, the buckling in some panels on the blade. And then iterating, a lot of iterations, adding a little bit of material here, removing from there, checking your load models, making sure that the loads don’t go up too much. Checking some constraints you might have, maybe some tip to tower clearance, maybe some specific ion frequencies that you want to avoid.
And at the end of this first step, then you will have a first kind of conceptual design with the right geometry, the right trailing edge thickness, the right blade circle diameter, root circle diameter. Once you get all that, then actually you go one step further into your design and you start doing some finite elements analysis, which is a little bit some more details analysis on like very small details on your design.
So once you get all that done, then you start involving the certification actually, which is a third party that often the customers will ask for them to certify your product. And then you start sharing with them some of your models. And while they are doing that, you will actually start preparing your full scale testing, because every blade needs to go through a full scale test. And in that phase, you also have some people from the third party certifying your blades coming and doing some audits. Yeah, you manufacture the blade, you ship it for testing. You do full scale tests which take actually many months, the fatigue testing, it’s many millions of cycles.
And then you have to do a static or extreme test before and after that one. And then depending on how much risk you want to take, you can launch the full the serial production before the end of the testing, because often you cannot afford waiting six months or a year for the testing to be completed.
Rosemary: I’m assuming that the team on the certification company is not as big as the team at the manufacturer. So how can they possibly check all of that information in enough detail to be sure that you’ve done it right? Or are they then relying on the fact that you’ve made a test blade didn’t break that means everything’s okay. I just how do they get enough certainty from it?
Mohammed: They check what they can do. They cant rebuild the models, maybe some try to build some the, that finite element modeling and run it. But no matter what they do, they will have to put a lot of trust in what you have done. As I said, there’s many people working on that blade design sometimes can easily go up to 50 or a hundred. And then when you look at the certification parts, two or three people working, for example, on that structural design part, or even less.
They will not certify that this blade is perfect, but it was again, certify that you follow the steps that you have to, and you follow this IEC standard 61400 for lightning or for structural or for testing. And so the system has large limitation and that’s also why, for example, many developers, they have their own qualification system.
Of course. The certification you need to certify, but themselves, they will try to look at some design parameters. They have, they will look again through the, I don’t know, the power generation data. They will go and do some audits in the factories. And even after doing this you catch what you catch and then what you don’t know, you probably never know it.
And some defects, they appear during the lifetime and some they don’t even appear actually because they’re not that problematic. And we learned to live with that. I would say the majority don’t have any problems, but if you are a developer, you don’t want to get those ones that fail so you have to do all these checks.
Rosemary: Okay, so I’ve got a follow up question. I know that you mentioned that you make usually one test blade. It’s one of the first blades that you have made. There’s a high chance that it you know, has a lot of the issues in it that you haven’t figured out yet. I’ve spent a lot of time in wind turbine blade factories, and I know that every blade that comes off the end of a production line is not exactly the same. There’s different defects in every blade and they’re always doing repairs.
So how can you hope to capture the whole range of problems that you might have if you just test a single blade? How does the certification process deal with that or the design and certification process, is a better question to ask.
Mohammed: If you do some lab tests of small composite parts, you really need to test a big population to really be certain of integrity of that part.
In blades it’s a bit different because we talk about blades of 100 meters, it’s a high cost, and it’s also every blade takes many months, so you cannot afford doing seven tests, it will ruin the whole business. One way of dealing with it it’s basically with partial coefficients. So in, in the certification standards, basically because of the, this variation in manufacturing, you will add a factor of, I don’t know, just saying random numbers of 1. 1. Because of this variations in fusion or in, in the uncertainties about your load model and so on. You will keep adding these small partial coefficients and then you end up sometimes depending on your process, you end up with, I don’t know, partial coefficient of, let’s say two.
And that’s already actually means that your blade, it’s actually two times stronger than the nominal one, but it’s because there’s a lot of variations again. And then there is variations in the loads, there is variations in the structure and you don’t want these variations to start overlapping that you will have in some cases a blade that is weak enough because of all these deviations.
And then a load model that is not conservative enough that you will end up with these blades failing. And then you also do overtest actually those blades to some level. In static you will test them 10 percent more and then in fatigue depending on your number of cycles and your strain, you might test it up to 33 percent more.
Rosemary: No matter what your best efforts are sometimes you are going to get, defects that occur occasionally in serial production that didn’t happen in the test blade. Or I guess you do get the occasional unlucky blade where just every single possible parameter you’re at your worst case scenario, and they will all line up like holes in Swiss cheese.
So then you see issues like what we’re seeing in the news today with Siemens Gamesa, TPI, the main ones that I’ve heard of, which you’ve already talked about today. Do you feel like there are more blade defects than normal at the moment?
If you do think that there’s more than the normal amount of defects, what’s your thoughts on why that is and what that means for the future of wind?
Mohammed: Actually, I think there’s much less defects than before.
Because also, actually, there was a lot of progress yeah, but when just the engineering part, there was some, actually now more, much more calculation is done than before. And also in the manufacturing with all these new methods of being lean and then the quality management system and so on. I think they are getting less, but actually the ones that still makes it to the blades, those defects, they have a bigger impact now because we’ll, we became better, I think, as making blades at making less defects, but we also squeezed all the kind of the juice where we really pushing the limits and then going really designing to the limits and so on.
So maybe before you would have 10 small defects because of your manufacturing, but you had a little bit extra capacity in your structure that did want to be a problem. But now maybe let’s say you have just one out of these 10, but because of The very optimized blades, I would say one wrinkle that you don’t catch might be a big problem.
And that’s why having control over your manufacturing, it’s actually, it’s so important if you want to keep innovating, bringing new materials and then having this detailed analysis that you can use. You cannot benefit from that if you’re manufacturing is not like really almost perfect.
And that’s the problem I think blades have. I think almost everybody will agree with me. It’s the manufacturing that is still very like labor intensive. And then when it’s humans making that, it depends on where they are, if they had a bad night, if they have paid well, if they are stressed and all these factors, actually. You can have the best design you want.
You can reduce the number of defects, but yeah, the human factor is so important and then how can that be fixed? Often it will require money. And then again, the business case start suffering. Because you can say that why aren’t we automating all this process some simple ones like placing glue or placing some layers?
But, I worked in some many actually projects trying to add automation into factories. Very often you end up having more expensive blades that nobody will want to buy. And then you end up somehow, I don’t know if it’s intentionally or not admitting to like to have this quality issues than to invest in automation and then remove these quality issues.
Because at the end, even if those blades fails, it’s still actually better business case than a fully automated factory.
Rosemary: Okay. That’s a, yeah, that’s a really good perspective. And maybe we’ll have you back on another time to talk about wind turbine blade manufacturing, because I think that’s a whole huge topic that people don’t necessarily understand that well.
Yeah, particularly how manual the process is and all the quirks of composite materials. Thanks so much for coming on. And can I just ask a parting question? What do you think the future for wind is? Are we going to, make it out of this current crisis? Will we see bankruptcies? Do you think it’s overblown?
What’s your little snapshot of where you think we’re going?
Mohammed: I think there is still a future for wind, also mainly for offshore. Actually, it looks very promising. LCOE, it’s just decreasing and decreasing. And maybe that’s also why we are seeing all these problems. But I think it will stabilize at one point. I hope that will happen.
And then we have this healthy kind of industry where nobody’s taking kind of the losses. If it’s a supplier, OEM, or a developer, or the end customer. I think actually, I’m very positive, I would say. And then I think the solution in all that will often be, yeah, technology and innovation. I know also trying to keep the amount of platforms and product existing in the market very limited so that OEMs can benefit from it.
But only the market can regulate itself. And only the market will regulate the size of turbines. Only the market will regulate the end price. And it has to converse to a good balance point.
Rosemary: Thanks a lot for listening to this episode of the Uptime Wind Energy podcast. Don’t forget to like and subscribe if you’re watching on YouTube. Or if you are listening on a podcast, please leave us a review. It makes a big difference to other people finding the podcast. Yeah, thanks again and we’ll see you in the next episode.