The Uptime Wind Energy Podcast
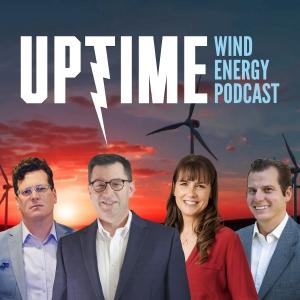
Segmented Turbine Blades, Vestas Acquisition, and Innovative Anti-Icing
The whole Uptime crew is back together this week! They debate the future of segmented wind turbine blades–are they needed anymore? Plus Vestas moves to boost its services business by fully acquiring weather forecasting firm Utopus Insights. Also, Fraunhofer’s development of a drone-sprayed, biodegradable blade coating to prevent icing, and the challenges of mapping offshore wind farm sites and currents using subsea acoustic technology.
Sign up now for Uptime Tech News, our weekly email update on all things wind technology. This episode is sponsored by Weather Guard Lightning Tech. Learn more about Weather Guard’s StrikeTape Wind Turbine LPS retrofit. Follow the show on Facebook, YouTube, Twitter, LinkedIn and visit Weather Guard on the web. And subscribe to Rosemary Barnes’ YouTube channel here. Have a question we can answer on the show? Email us!
Pardalote Consulting – https://www.pardaloteconsulting.com
Weather Guard Lightning Tech – www.weatherguardwind.com
Intelstor – https://www.intelstor.com
Allen Hall: Okay, Rosemary, I was just saw the news article today where the Australian Post is going to stop delivering daily and you’re only going to get your mail occasionally in Australia. And I’m wondering like how the heck that works. If you, when your mom sends you cookies, it’s really important that they actually get there on time.
Now you have to sit there in the post office for a couple of days before they reach your doorstep. I don’t know how that works. That’s one part of a functioning civilization is that the mail arrives on time. Would you like to explain?
Rosemary Barnes: Yeah it’s letters. Letters are going to be delivered every second day now instead of every day.
Yeah, so if your mum cooks you biscuits, then you can still get them delivered promptly. I think it’s, the same trend that you’re seeing in the US, I’m sure, and that everyone’s seeing around the world, is that in terms of delivery, the profits are to be made in the parcel delivery. And letter delivery just is something that they’re forced to do because, you need to have a post system, but everyone’s just losing money on that part.
So they’re trying to, lose less money without reducing the service too much. But how often do you need a letter delivered? It doesn’t matter if it was delivered one day later. That’s what, there’s still express post obviously for that. If you need something delivered.
I’m fine with it. I’m going to, I’m going to be okay with this change.
Joel Saxum: There’s a talking post so I’m back in Houston now and Houston being a big hub in the United States. I ordered something on Amazon today at 2 p. m. and it was here at 4 30. That is just crazy to me.
Like the, how fast, and it was just like some random dude in a car pulled up and ran over and, here’s your super glue. I was like, oh dang, thanks man.
Allen Hall: So Vestas is increasing its expansion of the service business, I think. They’ve announced the acquisition of Utopus Insights. So they had purchased, actually purchased the company back in 2018 for roughly 100 million. Utopus Insights provides weather forecasting for solar and for wind. And that they have a platform which is pretty popular that a lot of the industry uses called Scipher.
And so it has advanced forecasting techniques. And we’ve seen some of these companies around at some of the conferences like ACP. That they’re trying to predict tomorrow’s or next week’s weather. So you know how much energy you’re going to be producing. But because Vestas already owned it, it looks like they’re going to pull it all in house and make it a quote unquote Vestas company now instead of an investment.
This is interesting, Joel, just because as we wandered around Blades Europe and talked to some of the Europeans. Vestas is trying to make a big splash in the service business with the full service agreements and now looks like in some of the weather prediction.
Joel Saxum: Yeah, and Vestas is a company that they don’t when you think about full service agreements, don’t get this wrong.
They don’t just work on Vestas turbines. They will work their multi brand, right? So when they’re saying, Oh, we’re taking this off the market, basically, it’s not just so it works for Vestas and their internal stuff. That gives them a bonus, right? It puts a little another tool in their back pocket, especially when it’s a tool that’s already recognized and utilized by the industry, right?
We call that the lemming effect. Once one or two of them lemmings go, then all the other ones start to follow suit, like just watching, ants go to something sugary on the floor. So when they have this unit, this Utopus Insights Scipher inside, then everybody’s wants to use it.
Everybody, it’s an industry recognized product. So if they bring it in house, then it makes their service options more attractive, and it gives them the upper hand when they’re trying to sign full service agreements, or OEM agreements, or O& M agreements against the competition.
Allen Hall: Phil, I definitely see a Vestas move, now that Siemens Energy is really struggling and limiting where their sales are.
Vestas is trying to become a much bigger player worldwide in all aspects due to really just the lack of GE and Siemens at the moment pushing back. And this seems like another one of those plays where they’re expanding into areas you wouldn’t think Vestas would be into actually.
Philip Totaro: It’s a different kind of vertical integration.
Normally a supply chain company is going to vertically integrate supply chain things. This is an ancillary kind of capability to bolster the services, business and potentially even the project development consulting area, which obviously is an OEM. You do a fair amount of that with the project development company that you’re partnered with if they’re, going to be sourcing your turbines.
But keep in mind as well that Utopus also does data analytics beyond just the weather forecasting. There are also, ever since the initial investment as a stand alone company, Vestas has actually been feeding Utopus some asset level SCADA data and other CMS data, etc., that Vestas has, and that they were trying to analyze internally.
They’ve been working in conjunction with Utopus to build a more robust analytical platform. So bringing Utopus in house potentially also helps facilitate that. Keep in mind that Vestas had launched, a spare parts business and things that were ancillary to their services business a while ago, and then they pulled the plug on it. I get the sense that they’re trying to regroup on some of those things now and develop something more robust leveraging more robust datasets, analytics, et cetera. That’s actually going to allow them to introduce more capabilities in the future.
Joel Saxum: To add on to that, Phil, either way, we’re seeing Vestas make moves right now to capitalize on the absence of those Siemens in the market, like you were saying, Allen. Like just this last week I saw Vestas announced it was like 193 gigawatt or gigawatt, 193 megawatt order. And then there was another announcement, 200 megawatt order.
So they’re getting orders, they’re capitalizing on that little bit of gap in the space to grab a foothold.
Allen Hall: It’s really. Interesting development. The wind players right now are battling. It’s quiet. It’s weirdly quiet. You don’t hear a lot of news about it, but you see these acquisitions and these moves and Vestas is definitely trying to conquer the chessboard at the moment.
Rosemary, we went to, Joel and I went to Amsterdam to see the Blades Europe Forum. And, so the whole time I’m watching some of these discussions about Blades and man if Rosemary was here, she’d give them a piece of her mind about, about, about some of the, just the kind of the more outlandish approaches to the blades and how blades are built, how blades are assembled, what the future of blades actually looks like.
Now, what I want to talk to you about is the segmented blade concept, right? So there’s a real discussion in Europe, like blades are being built outside of Europe and why can’t we bring it back into Europe? How do we do that? We need to lower the cost. We need to make things simpler. And the concept is to build these segmented blades, uh, where the shell and the internal structure is Lego y and so a blade, let’s say a hundred meter blade is going to have 25, 30 pieces.
Where they can all fit inside of a standard conics box and be put on a ship. So they would build these subcomponents and then put it on a ship to where it was going to go. Then they assemble it on site. Now, my first thought was like, wow, that’s like super complicated. And Rosemary is going to tell me the structurally, it’s going to be very difficult to do.
Now that we’re here all together, finally, what do you think of these segmented blades and the concept of building segmented blades? I think you were involved in at least one segmented blade previously.
Rosemary Barnes: Yeah, the two piece blade for the Cyprus turbine and GE Cyprus turbine, I worked on that project.
That was the last blade that I was working on. I think before I left LM. Big challenges involved in making a blade in pieces. And that’s just, yeah, that’s just two pieces and that blade as well. It’s not like you don’t split it in half. It’s like a big blade section of about, I don’t know, 60 ish meters.
And then the tip of about, 10, 15, 20 meters. It’s the split comes towards the tip. And the reason for that is because it is really challenging structurally. Wind turbine blades, they’re just attached at the root and then there’s this really long cantilever structure just sticking out there with a lot of, Big, big forces trying to, bend it and break it.
And the way that a wind turbine blade deals with that is through the use of composite materials and in a fiber reinforced composite material, like fiberglass or carbon fiber you get a lot of strength and stiffness for a low weight because you can put the fibers. Running in the direction that you need the strength and stiffness, right?
So the blades are very strong in that one direction along the length of the blade, and they’re not as strong in the other directions that they don’t need to be. And so you really target your properties where you need them. And so you get something that’s very light. But the problem is that when you want to make a two piece blade, then you’re going to obviously cut at some point along the blades band, you’ve got to cut, and there’s not going to be any fibers running all the way across that cut. So if there’s no fiber continuously running across the join, then you don’t transfer the loads from one side to the other easily. It has to go through a pin or some bolts or, a patch or however you choose to put your blade together.
That’s the basic challenge you’re going with. There’s some other materials challenges as well, most or all utility scale wind turbine blades currently use thermosetting resins, which don’t, that’s the, the plastic that holds all the fibers together. And that kind of plastic, it doesn’t melt.
You can’t melt it. You can’t weld it. You have to, the way that, you put a blade together, you make it in one piece because once the resin is set, you can’t do anything to it after that. It’s a rigid component that’s going to be exactly in that way for the rest of its lifetime. So if you want to do a repair or if you want to, assemble multiple pieces of a blade that’s made out of a thermoset resin, then you’re going to have to do a complicated repair where you yeah, you stack up layers of glass to try and, make up for that issue that I mentioned where you’ve got cut fibers that can’t transfer loads, you got to end up putting in a whole lot more layers over the top to get the load transferring.
And also to get the resin of the new piece to stick to the old structure. So one way that you can overcome that is by using thermoplastics, which do melt. But the problem with them and the reason why no one uses them yet is that they’re not usually not as strong or as stiff as the thermosets.
So a lot of the work in multi piece blades is about changing the structure so that it can use these thermoset plastics. And then you would be able to, bring a shipping container worth of blade pieces to site, put them together, and then maybe use heat welding to assemble them. And you should be able to, have some layers that can stack up and instead of just, like Lego bricks, instead of just putting two bricks next to each other, you probably put another one over the top so that, it’s got some sort of strength and bending as well.
And weld it all up that way. I think it’s a good concept. And definitely worth pursuing. I do think it’s complicated. And if you were able to transport a blade in one piece to site, then that is always going to be a lighter, cheaper, easier, faster way to do it. I think if you look at that blade that I mentioned from GE the cypress blade that was made in two pieces, they had this whole big thing about, oh, this is going to open up so much more so many more locations, two longer blades than what they’ve been able to deal with so far.
We’ll be the only people that can sell a turbine in these locations of this size because everyone else is limited in, what they can transport there. But instead they found that people. They solved all of those logistical problems, and in fact, there isn’t, I don’t think there’s many, if Any, maybe none locations where you can only put in a Cypress wind turbine.
I think that they figured out a way to be able to get longer blades onto site. And, some of those technologies like you, you’ve seen those trucks where they will tilt the blade up to get around a winding corner. Yeah it’s always a risk with when you’ve got a, you’ve got a technology that you’re developing to solve a problem.
You’re not the only person that’s trying to solve that problem. And it’s not, it’s always going to be a bunch of different ways that you can solve it. And it’s not, it’s not really obvious. Okay. I’m designing a two piece blade, but my competition is actually a different kind of truck. That would probably a bit of a bit of a weird competitor to, to foresee, but I don’t think that the two piece blade has definitely not taken the world by storm. And so I think it’ll remain to be seen whether we do need to move to a, a really segmented. I really segmented kind of blade design.
Do we need bigger wind turbines on shore? I don’t know. I think people are losing appetite for really huge wind turbines these days. Yeah, there’s a lot of other good reasons to move to a modular system. Thermoplastics are better for recycling and repairs might be easier. Yeah. So it’s something to keep an eye on.
Philip Totaro: The whole reason why segmented blades were believed to be necessary in the industry in the first place was because of transportation and logistics constraints, bridges and tunnels that have, like your 4. 3 meter height restriction. And so that was the impetus for Gamesa doing that segmented blade design on their, the G128.
And other companies to have investigated the technology, but Rosemary just said. If you’re doing a segmented blade, it’s not always the most desirable thing to do, so you’re not necessarily competing with other companies that have segmented blades, you’re competing with, the logistics companies that already have a vested interest in ensuring that they can continue to, meet the demand that they’ve that they’ve already been serving with single piece blades in the first place.
It’s, The insurance companies don’t like the two piece blades. To be honest, there’s they are more expensive. They’re not necessarily more accident prone because the joint does tend to get overbuilt. The companies that we’ve worked with in the past, Neverwind and others that have investigated this type of technology it’s, it’s a pretty robust thing if you’re going to use it so they haven’t had terribly many failures or anything with it.
It’s not the world’s most desirable thing to, to do. It’s one of those things it’s technologically feasible, but the commercial viability of this kind of solution was not what the industry really wanted.
Allen Hall: So the market’s essentially moved on? Is that it? And that blade manufacturing is just going to occur in lower cost countries?
Is that the outcome?
Philip Totaro: It’s, it’s a combination of. Rosemary also said, there’s a finite limit between social acceptance, physical constraints and limitations, et cetera, to the size that you’re going to have of onshore turbines. Yes, you can do, a 10 megawatt onshore wind turbine or a 12 megawatt onshore wind turbine in the outback in Australia or the middle of nowhere in, Finland or Norway, because there aren’t any bridges and tunnels.
That you have to go under anyway you might be traversing over a fjord once in a while. But you have the ability to be able to transport a single piece blade that would be You know, whatever, 85, 90 meters long plus to a project site if you wanted to be able to do that. But the problem with it is there’s a finite, there’s a finite kind of market demand and market appetite for Turbines that large.
Most countries still have, setback distance restrictions tip height restrictions, et cetera, et cetera, that preclude onshore turbines from really getting that big. So it’s a niche technology. That has been developed for a segment of the market that never really evolved, because, again, like we’ve been talking about, if you’re going to build a project site, it’s got to be someplace that’s accessible anyway.
You need to be able to have roads where you can do any kind of the transportation and logistics, regardless of whether it’s a segmented blade or not. And just because, you might have good wind at the top of a ridge, some place, if there’s no transmission there, you’re not going to build. If there’s, no kind of regional demand if your substation is, hundreds of miles away you’re not going to build in places where you would necessarily need the segmented blade. Or, similarly, we’ve talked before on the show about things like, on site spiral welded towers, or other technologies where you’ve got the self erecting tower. It’s all clever and great technology, but there’s just no market appetite for that sort of stuff.
Lightning is an act of God, but lightning damage is not. Actually, it’s very predictable and very preventable. Strike Tape is a lightning protection system upgrade for wind turbines made by Weatherguard. It dramatically improves the effectiveness of the factory LPS, so you can stop worrying about lightning damage.
Visit weatherguardwind. com to learn more, read a case study, and schedule a call today.
Joel Saxum: Okay, so when we were in Amsterdam this past week at Blades Europe, we actually had some of the new PES Wind magazines on our booth. And some people flipping through them really enjoyed some of the content. One of the curious things was that there was actually a bunch of companies there that had articles in them.
Aerones was there we were there, of course, and there was a couple of others. Oh, hey, I know these people. Oh, hey, I know a little bit about this. So that was neat. One of the things that tripped the trigger for me and the PES Wind the magazine For this quarter is an article about Nortek.
The reason it was, to me, Nortek is part of my old life, right? Nortek’s a Norwegian company that creates some subsea technology in a lot of different ways. But their big claim to fame is, fame to, is ADCPs, which is It’s a long way of, or it’s a short way of saying Acoustic Doppler Current Profiler.
Okay, so now that seems crazy, but what an Acoustic Doppler Current Profiler is it’s basically a way of measuring water subsea. Measuring water movement and flow. And there’s a lot of reasons to do this. The article goes into some of them. The ADCPs, of course, Nortec makes a bunch of different ones.
They make some flat ones that go underneath vessels to track actual vessel movement. Like in a, on an airplane, you have a pitot tube that tells you what your actual airspeed is. But that’s different than the ground speed, because airspeed takes into consideration the wind that’s flowing with you or against you or, at a whatever angle to the plane to get the actual effect that the wind is having on the aircraft.
So you can and then that you compare that to your speed over ground that you might get with a GPS and there can be vastly different. If you’re like, oh, we have a great tailwind. The plane might think it’s going 500 miles an hour because of the wind coming at its back. But you might be actually going 600 miles an hour on the ground.
So an ADCP is actually that same kind of technology, but for vessels in the water. So it will actually, it shoots down like there’s, it’s a little kind of complicated and maybe we can go into that about how it works, but it’s measuring the current and flow of the water. If you have one underneath your vessel, it’s under the vessel.
So you may be sitting still in the, in a river but the ADCP will tell you that you’re actually fighting a three knot current. Even though your GPS tells you’re going zero and the motors are on and you’re moving or you’re moving water so that you’re fighting against that current. So how does this fit into what we talk about here in renewables?
Of course, offshore wind. So an offshore wind, we’ve talked about it before, all the site characterization that needs to be done before any kind of development can go in the water, you need to know, What meta ocean data, so what kind of currents are out there, what kind of wave heights are you getting, all of those kind of things, right?
Directions, speed, flow, and then you need to map the subsurface so know exactly, what what depth the water is, and if there’s rocks down there, if it’s mud or silt, and what the topography basically, what you look at on the surface of the earth, what that looks like on the seafloor.
But then also because we’re driving piles or suction caissons below the mudline, you need to know what is below the mudline. So you need to know the first 5 to 40 meters of surface to be able to do geotechnical investigation on it to see if your Structure is actually going to hold up or be able to be installed or cables are going to be able to be trenched in Or whatnot.
So there’s a ton of work that needs to go offshore The difficulty of offshore work though, and this is where the ADCPs from Nortec come into play Positioning is very hard. You cannot use GPS on subsea instrumentation because GPS doesn’t go through water. If you want to, if you want to test this theory I don’t know, hold your, put your phone underneath the pool and see what happens to the GPS.
It’s just not going to work. That’s maybe a crude way of testing it, but…
Philip Totaro: Hopefully it’s waterproof.
Joel Saxum: Yeah. Yeah, exactly. So to get proper measurements, you need to combine a lot of sources to get a good X, Y, Z location of your instrumentation and orientation of it. Some of this comes in you can have GPS on the boat.
You may know how long your tow line is and the direction you’re going. So if you’re towing an instrument behind you say echo sounder to give you depth and map the sea floor. Great. So you know where your vessel is and where your tow line is, say it’s 40 meters behind you and you’re heading this way.
However, you may have a current coming against the vessel this way. So that’s moving that off to the side. You don’t know what’s moving it though, because You can’t see it in the GPS, can’t see it back there. So now you’re relying on adding an ADCP and acoustic Doppler current profiler to tend to tell you where it’s moving sub C and you may have to add other things like a USB, like a short baseline acoustic sensor to be able to ping back and forth.
And there’s a very sophisticated software that will tie all these instruments together and give you good positioning. So you’re, it’s you can’t make chicken soup out of chicken poop, if you’ve ever heard that before.
Allen Hall: That’s a Wisconsin term. Has to be.
Joel Saxum: It’s termed a little bit different when we say it in Wisconsin, but same concept.
So you have to have good data in to get good data out, right? So if you’re out there dragging these instruments around the in the ocean and you don’t have good measurements on where the data actually came from, then your analysis is going to be, flawed from the beginning. Adding all these tools on, like the Nortec or ADCPs or DVLs, Doppler Velocity Logs, will make the actual analysis of the seafloor and site characterization more accurate.
It’s not just boats driving around and in grids out there, there’s actually highly trained highly trained personnel running extremely, Customized software with very expensive instrumentation to be able to do these things correctly.
Allen Hall: So how does this affect the one thing I’m really interested in, and we need to have them on the podcast, the Ridgway Rock Bag Group?
Does, if, they have to know what the current flow is to place those bags properly, right? They just don’t start dumping rocks randomly.
Joel Saxum: Yeah, so ADCPs sometimes depending on where you’re dumping things, you may put those out on the seafloor. So you can actually put these things on tripods. Out on the sea floor in regular areas, and then you’ll know the current and direction of the current live feedback to the vessel.
So you can tether them or you can, get information back and forth from USVL communications. But when they’re doing big projects in, like in the North Sea, there’s always issues with scour being when currents flow past monopiles or flow over rock dumps, they create this.
This basically, The water flow creates a scoop. It creates turbulence and it might move some sediment in the wrong direction. Because they have two and three knot currents regularly subsea in the North Sea. That’s not an abnormal thing. You think that of the ocean as a big stable place, but the ocean is constantly moving at all depths, the water is.
If it’s Ridgeway Rockbags and you’re out there and the deeper of the water you’re in, the more the current can play with you, right? So if you’re on the surface and you’re on a dynamic position hold and you’re a big barge with the, the crane off the side is holding there the position on the tip of the crane, you thinking that it’s going to go straight down the crane wire to where it’s dumping, By the time you get down there, that rock bag is big.
It’s getting pushed by the water. You might be a couple of meters off, and if you’re a couple of meters off of the cable that you’re trying to land on, then you’re not going to land on it. And all of a sudden, a year later, or you do a post dump inspection with an ROV, you go hey, those rock bags missed, man.
And that’s a big problem, because now you’ve got to go back and remobilize the vessel and get them back in the correct places.
Allen Hall: Okay, this is really complicated. I would assume that. They’d have to sample the ocean floor over a long period of time. It seems like the currents move around a little bit, seasonally, right?
Joel Saxum: Yeah, that’s gonna be like a MedOcean campaign, right? So that’s where Nortek makes, they make stuff for everything, right? Nortek makes things to put on the bottom of your boat. They make things to put on survey instrumentation. They make things to have standalone MedOcean data collection. They make all kinds of stuff, but, yeah, if you’re talking MedOcean data there’s a company TGS is a Norwegian company.
They specialized for a long time in oil and gas data. So they had seismic data all over the world, onshore and offshore, based on spec, right? So if you were an oil company and you were looking in this block, you could just call up TGS and say, Hey, can you give me what you have for 2D seismic lines in this area?
And they’ll be able to tell you what they have and sell it to you at a premium. What they did a few years ago as a pivot. TGS is very smart company. They, to get into renewables, they purchased 4C offshore. 4C offshore was in the process of developing kind of spec data on but MedOcean data.
Seafloor currents wind resource topside, weather conditions. And not only seafloor currents, but mid level currents, sea surface currents, surface temperatures, salinity, all these crazy measurements that you need to have. 4C Offshore was developing a big database globally for all of those. They started focusing on all the areas where renewable energy would be installed. So if there’s an, if there’s an area where there’s a lot of oil and gas activity, yeah, most of that data exists, but now you’re starting to see renewables branch out where there is no oil and gas activity, say East Coast U. S. So there’s companies out there collecting that data over large long campaigns, year two, three, four, five to get higher resolution data rather than just whatever you can, download from NOAA online.
Allen Hall: Okay. This is really cool. I know I read through that article about Nortek. And It was a lot to absorb because it’s a very technical article, but it is interesting how much work goes into the sighting on offshore wind turbines and just knowing what the sea is doing is a major part of that. So if you’re interested in offshore wind or onshore wind, you need to pick up the latest PES wind.
Magazine. You can just get it online at P E S win. com.
Hey, uptime listeners. We know how difficult it is to keep track of the wind industry. That’s why we read PES Wind magazine PES Wind doesn’t summarize the news, it digs into the tough issues aPESE S wind is written by the experts. So you can get the in depth info you need. Check out the wind industries, leading trade publication, PES Wind at peswind.com.
Well, Fraunhofer has been working on a drum based ice protection method for wind turbine blades. And this one’s a little different than anything I think you’ve seen in the past. Some of the criteria, at least one of the criteria was that it needs to be whatever chemical they were going to apply to the blade had to be neutral, right?
No impact on the environment. So they came up with a really interesting coating. It’s a combination of wax and urea that they can spray on the winter blades and it’s environmentally friendly. It sticks to the blades, but it helps prevent ice buildup on the blades. And if you’ve ever, like in Massachusetts, when it’s icy outside, if you take some fertilizer, which is basically urea, We throw, if we throw that out on the ice it’ll melt the ice.
So I think the concept is urea in a waxy film will help prevent ice on blades now. The way to apply it, obviously, the way to do this easily is with a drone. And that just brought flashbacks to Aerone’s first attempt at this years ago. It’s probably five, six, seven years ago. If everybody remembers, there’s actually a YouTube video of them de icing a wind turbine blade.
And I think that was a a hot glycol solution probably at the time. That they’re using as a demo and we saw that drone last week, Joel, on the wall. It’s huge. Yeah, it’s a big, it’s a big drone. Yeah. So it’s interesting that Fraunhofer’s back onto this type of approach and Rosemary, being our resident blade expert and anti icing expert, I assume that you have been playing around with urea and wax for a long time, is that something that you studied in college to figure out how to keep blades clean, or is this a good approach, or what?
Philip Totaro: Where are you going with this, Allen?
Allen Hall: I don’t know, it’s a very odd, it’s a very odd approach, I’ll have to say that. When I saw it, I was like Really? It’s like an old farmer’s technique and maybe that’s why they picked it up. It’s an old farmer’s technique.
Rosemary Barnes: I think that the approach makes sense.
So I haven’t dealt with that particular mix of materials before, but. When I was working on de icing yeah, back in my days as the, I was in that role in charge of blade heating systems at LM Wind Power, definitely there were plenty of kinds of ice phobic or anti icing coatings that people wanted to sell us as being, the solution to the icing and wind turbine blades, because the only method that works currently is to heat the blades up and to melt the ice off that way.
And of course you need to know ahead of time that you’re going to have a blade that’s going to ice a lot in order to be able to do that. It adds quite a lot of costs to a blade. And it also adds just so much baff to the turbine operation and maintenance as well. So I think everybody would always prefer that you could have a passive system and not have to install any kind of, electrical heating mats all the way down a blade and deal with all the issues with, potentially overheating the structure or attracting lightning or anything like that.
Yeah, the blade coating for passive ice removal or yeah, ice prevention is an obvious approach. Heaps of people were involved in it. And what I think is interesting in this project is that they have bypassed the biggest weakness of that approach in the past. Because a lot of these coatings they work in the lab you can, code a piece of material and put it in an icing wind tunnel and say, Oh, look at, it works. But it’s very different to how they work in reality because once you’ve got a coating on a blade in the field and then, they’re probably, it’s not going to be in its perfect condition by the time an icing event comes along, you’ve got a leading edge erosion, you’ve got bugs that are going to stick to it and coatings degrade and every material that I looked at during my time it didn’t work in the field that, they just didn’t last well enough.
And a lot of the time, probably even maybe most of the time, the coatings, when they were worn a little bit actually were worse for attracting ice than a blade without the coating. So it’s just a really hard problem. So Fraunhofer seemed to have. sidestepped that by not expecting the coding to last for a long time.
So what they’re doing is saying, okay, this is a coding. It needs to last for a few weeks, but then we can just keep on reapplying it over and over during the winter. So that makes a lot of sense to me. However, what I’m missing from the, I’ve just read a couple of articles about it. I’m just missing actual demonstrated use in the field.
I still feel like they’ve got a lot of computer simulations. They’ve tried their drone out on a piece of blade. They’ve done icing wind tunnel tests, but where’s the actual test on, it’s not that hard once you’ve got a drone, you turbine, spray your coating on it, and then. Measure it, see if it’s, see if it’s working.
I’m missing that. So it’s like impossible to say anything more than this is an interesting idea at this point. I just don’t know why people make these announcements. Just a bit early, and I guess it’s just coming up to winter in Europe now So they probably haven’t had you know, they’ve been working on this for the last six months then They wouldn’t have had I guess an icing event Likely, maybe they’re ready to go.
But I don’t know if I was a communications department. I’d just wait Till March or April and say how did this work over your first you know icing season campaign and then be able to say more than Cool idea. Nice work, guys.
Joel Saxum: My take on it, though, is that the biggest problem I see, technically, cool, whether the chemical compound works or not, that’s not my concern right now.
My concern is, operationally, you’re going to be sitting in the O& M office on Monday morning and see a forecast and say oh, Wednesday, it might Ice up. Okay, we’re gonna get a drone out and now we’re gonna go and now, wind farms in Germany are much smaller than in North America, so even if it’s 25 turbines, 40 turbines, you’re gonna say, we’re gonna go out there with this drone, we’re gonna go and fly these 25 turbines, 75 blades, we’re gonna coat them all with this stuff, before Wednesday, and hope it doesn’t, or hope it works.
I just, That, to me, is asinine to even think that it could possibly work in a real life situation.
Rosemary Barnes: I agree with you, except that the headache that a wind farm owner operator in a site that is affected by icing, they have just the hugest incentive to, you wouldn’t believe the lengths that some of these these guys go to, the WiseTech system, which is a retrofitable electric heating mat.
They’ve had projects where they took down every single blade on a wind farm installed a temporary factory on site and got every single blade through there to wrap a heating blanket around the blade taped a electrical cable to the, to run down the length of the blade and put it back in place.
Now that’s a pain and the, I’ve seen them present at conferences and from all reports that wind farm owner is happy with the result of that, that was worth it to them because they were just experiencing so much pain. So I think you’re right that it’s not ideal, but yeah, a wind farm owner that has ended up with an icing problem that they weren’t expecting is like really in dire straits.
Yeah. It’s a pretty common problem actually because, when you’re doing a site assessment for a new wind farm there’s a lot of pressure to have your icing assessment come back as saying it’s not a big problem. You get these assessments that say, Oh yeah, you’ll probably have AEP losses of 2, 3, 4%.
It’s not really worth installing an icing system. And then you see a lot of the time. It’s actually 6, 7, 8 percent and that, that means that, that’s a significant loss and they should have installed a blades with heating, but it’s too late after the fact. And yeah, I think that there is, it’s not like a majority of wind farms, obviously it’s, it’s a niche application.
It’s. The niche is maybe small, but the people in that niche are just absolutely desperate. So I think that there would be quite a market for this kind of technology, even with the extra pain that’s involved operationally.
Joel Saxum: So I think I’ve got it solved, Rosemary. This is how we’re going to do it.
It’s going to be a fire hose, right? But the fire hose is going to be connectable in the base of the tower, and the fire hose is going to be already run up the tower, and there’ll be a little fire hose reel on the top. You roll up with the big pump truck full of eurea. You hook up the, you hook up the pump truck on the bottom and the guy climbs up to the top, pops the top off the nelle and sprays the blades down from up on the nelle.
Allen Hall: That guy is gonna smell horrible.
Joel Saxum: Yeah. . Yeah. Yeah. Urea and urea’s not cheap I run a diesel truck. So DEF that you put in diesel pickups right now because of the crisis in Ukraine. DEF prices went through the roof, which is just urea and water, like there’s nothing else in it.
It went from being able to get this stuff at 7 to 9 a gallon to right now it’s 18 a gallon for this stuff to put in my pickup. So if they’re spraying the same, if they’re spraying the same kind of stuff, that’s going to be expensive.
Allen Hall: I have a question, and this has to do with the way we do it on airplanes.
On airplanes, we have something called a weeping wing. Have you ever seen this, Rosemary? You take the leading edge of the wing, and they drill a bunch of laser holes in it, and then they pump a fluid through it, usually a glycol solution, and that just runs back and removes the ice. Is this a similar application?
You could actually pump this stuff up, up into the leading edge, and just let it run out, and De-ice ice a blade?
Rosemary Barnes: Yeah, I mean, you, it’s going to be complicated to deal with the rotation of the of the rotor. If you’re pumping something from the ground, you’ve got, I don’t know, maybe you run the turbine a hundred rotations and then.
Shut down for a couple of minutes to run it backwards to unspool your hose again uh, yeah, possibly or you can use Joel’s method of, mounting some sort of that guide on the tower and spray a hose that’s connected on the ground. Honestly, I don’t see that is so wild compared to a drone, except obviously it is a bit of a
a retrofit needed, but yeah, no, I think that the drone system does sound pretty versatile.
Joel Saxum: Yeah, the, yeah, The trouble with drone is once, as soon as you get up in the air, that big of a drone and you’re, you have to hoist all of that, that fluid up as well. So there’s a ton of weight and that thing’s weighted down.
And then once you start spraying and you’re spraying at, I don’t know what the PSI is, even if you’re spraying it. 200 PSI, that much that you’re going to coat a blade, that thing gets so hard to control up there that I don’t know. I just think you’re asking for trouble with the drone.
Rosemary Barnes: I think though, that this Fraunhofer approach where they’re not trying to spray like something to remove ice.
It’s not like it, it’s a coating, right? A very thin coating. So presumably there’s a lot less volume that they’re going to have to spray compared to if you’re just trying to. Yeah, I don’t know, spray, spray antifreeze all over a blade. Yeah. And it, they say it’s only needs to be done every few weeks.
So I guess, if you’ve got a long range weather forecast, you can say it’s okay, it’s going to get. It’s going to get cold in 10 days, we’ll start spraying, but it is hard to see how, you can get it done quickly enough to, make it worthwhile.
Allen Hall: So Rosemary says there’s a chance.
Rosemary Barnes: Yeah, no, this is when I used to work. When I used to work in de-icing and that was my job every single day for four or five years and I definitely used to get tracked down in the canteen or at conferences or wherever everyone has a, a bright idea along the lines of Joel’s one, many of them much more crazy than that.
And like I’ve probably got a bank of 50 or a hundred ideas that I’ve heard before, and this one would be, like in the top couple of percent of those ideas, so I I don’t think this is a bad idea at all. I think it’s an area where there’s only bad ideas, like everything, like this current system is bad.
But it’s just the least bad of all the ones that we’ve got. That’s what we’re going with. I don’t think there’s anyone that’s working on. On de icing of wind turbine blades. And it’s Oh no, this system is so good that we don’t need to change it. Like that, no one thinks that it’s just full of headaches and and pain and costs.
And, like it’s a reason why I got out of that role, like it’s only so long that you can deal with all that. I’m the first to, to wish for improvements in this field. And when it comes, I’m sure it is eventually going to be in the form of a coding of some sort, but whether that’s, like a magic coding that.
It just repels all ice and stays on there for the life of the blade. That’s obviously the holy grail. Maybe something like this is a step towards that. And they’ll, incrementally improve until you don’t need to spray it every two, three weeks. You can do it, twice a season and then maybe once a season.
And, if it was once a season, then that would be something that would, obviously be able to fit into any wind turbines maintenance plan. I think. There’s a high chance that this is a step on the eventual direction, but like I said, without actually having, they’ve never used it, they’ve just, they’ve got a little, five meter or two meter piece of blade tip that they have sprayed the coating on.
And that’s them saying, yeah, we’ve tested a prototype. I’m like okay. Yeah. Like you’ve tested a prototype of your drone, but you haven’t tested that it does what it’s supposed to do. They’ve got a long way to go before we, we know this is the path to pursue.
Allen Hall: That’s going to do it for this week’s Uptime Wind Energy Podcast.
Thanks for listening. Please give us a five star rating on your podcast platform and subscribe in the show notes below to Uptime Tech News, our weekly newsletter, and also give a five star rating to Rosemary’s YouTube channel, Engineering with Rosie, if you haven’t done that already. And we’ll see you here next week on the Uptime Wind Energy Podcast.