The Uptime Wind Energy Podcast
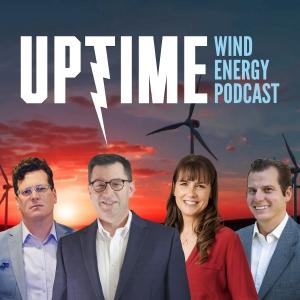
Wind Industry Growing Pains: Recycling, Construction, and Seals
This action-packed episode of the Uptime Wind Energy podcast tackles hot topics like the legal battle over massive piles of unrecycled turbine blades in Texas, construction snafus causing a 2-year delay for a floating wind farm in Japan, a wild new single-blade floating turbine concept inspired by 19th century toys, and ingenious new bearing seals that could solve the chronic lubrication failures plaguing wind farms. The hosts also spotlight the little-known, $700 million Top Crop Wind Farm in Illinois as the wind farm of the week. Grab your headphones and get ready for an energetic dive into the latest happenings in wind.
Sign up now for Uptime Tech News, our weekly email update on all things wind technology. This episode is sponsored by Weather Guard Lightning Tech. Learn more about Weather Guard’s StrikeTape Wind Turbine LPS retrofit. Follow the show on Facebook, YouTube, Twitter, Linkedin and visit Weather Guard on the web. And subscribe to Rosemary Barnes’ YouTube channel here. Have a question we can answer on the show? Email us!
ardalote Consulting – https://www.pardaloteconsulting.com
Weather Guard Lightning Tech – www.weatherguardwind.com
Intelstor – https://www.intelstor.com
Uptime 185
Allen Hall: Well, this week I learned that the word buoy is pronounced boy, and I’ve also learned a number of other Australian words, and I’m not even sure that makes any sense because Rosemary, buoy is a buoy, a boy is a boy, they’re really hard to mix up actually, but in this podcast this week, you went to spar boy, and I was totally confused, I had the dictionary out, I was just thumbing through like spar boy, I, I, I’m sorry, I don’t know what that means.
Rosemary Barnes: Allen, do you say buoyant or booyant? Buoyancy or booyancy? I think you’ll see that it’s Australians that have this one, right?
Joel Saxum: I got to agree, Rosemary. I’m sorry. I agree with you. I’m agreeing with Rosemary.
Allen Hall: Come on. I’ve lost two in a row. I lost the emu and I lost buoy. I’m pretty much out of words at this point.
Rosemary Barnes: You can, you can name whatever, whatever birds are native. To the US you feel free to name them and pronounce them how you would wish, but emus are emus. They’re ours. They’re ours. We’re claiming them.
Allen Hall: Well, see, this is, this is why, you know, it’s good to have a little bit of international flavor on the podcast because us Americans get a little too out of control and Rosemary’s here to rein us back in.
So as you will listen to this episode, that’s exactly what happens multiple times. It’s good to have Rosemary on the podcast.
So down in Sweetwater, Texas, where we were. pretty close to it last week. There, it’s been a big problem down there about the number of wind turbine blades that are just stacked in piles. And Global Fiberglass Solution was trying to recycle them. And those, some of those blades have been there since about 2017.
So they’ve been there a while. And back in roughly 2016, the IRS encouraged wind farms to replace the blades with the tax credits with new blades, right? So there’s a, there were a lot of wind turbine blades that came off the turbines and new ones went on. Well down in Texas, they’re looking for get those blades recycled and nothing has happened yet.
And it’s starting to become a little annoying. And the same sort of situations actually happened in Iowa with the same company in Iowa got really upset and. Forced GE or persuaded GE to take care of the problem in Iowa. So GE is recycling the blades in Iowa now This has led to a lawsuit That was filed this past week between GE and Global Fiberglass solutions and Phil, you want to give us the inside details of what’s going on here.
Philip Totaro: So, basically the, the back of a contract signed in 2017 and then a separate one signed in 2018. Global Fiberglass Solutions had the obligation to start recycling these blades. I think what they were going to do was to shred them and then incorporate some of the the shredded material, including the epoxy, the fiberglass, et cetera, into concrete.
To use as a, you know, a material to kind of strengthen the, the concrete and reduce the amount of rebar that, that would be necessary. So in theory, great idea. Unfortunately, I think that according to the contract, Global Fiberglass Solutions was supposed to at least haul them away and recycle them.
Although, potentially, the contract only said things about hauling them away. At which point, you know, technically, Global Fiberglass Solutions is, I guess, contending that they agreed to do that according to the letter of the contract, but in reality they weren’t necessarily recycling all of the blades that they had suggested they were going to.
So, the question is, was there a reason why they weren’t recyclable, or was something else going on, and they were just pocketing, you know, almost twenty, you know, twenty two and a half, I think, million dollars of GE’s money, and then not really living up to the obligations under the contract, so the, the civil dispute is gonna go on for a while, they just filed this That GE just filed this lawsuit in New York last week.
Heh. Unclear as to what this really means because there was some rather inflammatory language used in that that lawsuit. Where GE was basically suggesting that Global Fiberglass Solutions wasn’t really even capable of recycling anything. They just totally misled GE right from the beginning.
Allen Hall: The GE filing was really loaded with details. Like they had went and pulled presentation packs and emails and all kinds of information. So they had done some homework on global fiberglass solutions to go back and to relive what GE thought was supposed to happen. Obviously there’s been, there’s going to be a disagreement there.
But. Now that these blades are, especially in Texas, are sitting there, I’m not sure what they’re going to do, Rosemary. Is the best solution to try to recycle them? Bring in somebody to recycle them? Like, GE’s talking about doing that? Or is it just better just to bury the things and be done with them?
Rosemary Barnes: It’s such a, such an interesting question.
I mean, it depends what your goals are. I mean, if you really wanted to take those blades and turn them into other products, which I guess is what most people would think of as recycling. Then, you know, they are part of the way there. You know, one of the difficult things with recycling wind turbine blades is just the logistics of getting all the blades down from a wind farm and, you know, collecting them in one place where you can actually.
Processed them. So I guess they have gone partway along the recycling process, but I just think that this this lawsuit is so kind of emblematic of the whole debate around recycling wind turbine blades, because you You know, what does recycling mean and why are you doing it? I think that especially the second question, no one ever talks about that.
If you actually think about what you’re trying to achieve, then you can figure out what is the right thing to do with it. And a lot of those cases, it’s actually contrary to what most people might expect. So, you know, if we assume that by recycling wind turbine blades, we’re trying to minimize their greenhouse gas emissions.
Actually, you’re going to add greenhouse gas emissions to the life cycle of the wind turbine blades if you try and recycle them. The best thing that you could do is to take it off the wind turbine blade and just bury it right there at the bottom of where the wind turbine used to be. So I think in this lawsuit it was mentioned that there was supposed to be grinding them up to make pellets and then turn that into other products.
And I’ve heard you know, putting them into concrete is, is one thing and you can do that. And one of the issues with that with concrete specifically is that, you know, it’s really regulated kind of material because you use it for important structural considerations where you, you, you need to know how strong it’s going to be.
So I don’t think there is a huge, huge market for Just shoving whatever uncontrolled filler into, into concrete, even if, you know, you have had some promising lab results, you have to be able to control the composition really tightly. And one other thing that I think is a bit funny about this lawsuit is that GE has its own research programs into wind turbine blade recycling and has since maybe they didn’t have The program, you know, well and truly kicked off by 2017 when this agreement started, but certainly there are many, many blade experts working for GE who knew very well the state of the the industry and, you know, GE knows that you can’t recycle wind turbine blades in the sense that most people would imagine when you’re recycling, you can’t take the materials that are in an old wind turbine blade and do some process that turns them into a new wind turbine blade, the structural properties just degrade so much with today’s processes that that’s just not a possibility.
So I think that for them to say now, Oh my God, we thought that you were recycling them. It’s just a bit hard to believe that they thought that when their own program showed that that was not, not possible yet.
Allen Hall: Why wouldn’t they recycle, grind up those blades and add them to the concrete they’re going to pour right next door when they put new wind turbines in?
Why wouldn’t they at least do that?
Rosemary Barnes: Because it wouldn’t, it wouldn’t meet the certification standards. You have to, you know, like concrete is really, you know, really important engineering material, it’s strength and durability need to be known. If you just take a random wind turbine blade with whatever resin, whatever balsa wood, whatever, you know, just like rats or rattlesnakes that ended up in it when you, you know, you took it down and left it in a yard for a while, and then think that you’re going to use that for, you know, something as critical as a material that’s going to hold a wind turbine upright for 30 years without falling over.
I mean, it’s, that’s not going to happen.
Joel Saxum: Here’s a thought too, Allen, along that same thing, right? We’ve identified that one of the big issues here is transportation, we know that. All these, there’s a lot of other things that are going to emit more greenhouse gases. So the answer is, the material needs to be used locally.
Okay, building a wind farm down the road. Why not, why not grind it up and use it as the road base for all the roads and pads for that wind farm?
Allen Hall: Absolutely, yeah. I agree with you on that, yeah.
Joel Saxum: Those roads and pads need to be built up above the surrounding fields by a foot or two. That’s all extra dirt.
Why, why bring in all kinds of dirt? Why not put the road, the initial six inches of road base of crushed up fiberglass? Like, we know they can bury them, they’re basically inert, right? So why not use it for that? The tough thing with the whole lawsuit is that there’s a social part to it too, right? There’s a legal part, GE standing in one spot.
There’s a commercial part, GFS standing in another spot. Then there’s the, the, you know, the engineering aspect of it. And the, the actually doing the math and the metrics and looking at it quantitatively versus qualitatively. The other side of the thing is there’s a social impact of this, right? There’s a lot of people, whether you’re for wind or against wind, you’re looking at all these blades stacking up.
You’re saying, hey, this industry has a problem. This is another black eye to the industry. This sucks. We don’t want to, we don’t want to have to be continuously trying to bail ourselves out of these problems when we’re trying to promote wind energy. So the, the whole idea of this, this thing that’s going on, that it’s become a lawsuit between two players out there, it, that’s, that’s a black eye for the industry.
And they need to find a a resolution to it, right? So, in my mind, I know there’s a lot of companies out there that are starting to, you know, get more into the recycling of blade space. Like when GE did the project with Veolia, right? I know a couple of guys that have started companies that are, hey, we’ll recycle your blades.
So they’ll come, they’ll even take them off, they’ll cut them up, and they bring them to Veolia to, to get them recycled. And those guys, I actually talked to one of them about this lawsuit, they said, like, this is giving us all in the industry a bad name. I have, I’m getting vetted so hard by everybody I talk to asking questions.
That should have been asked during this thing, that he’s like, man, it’s like, it should be, these meetings should be a no brainer, and they’re, they’re difficult, they’re tough, because nobody believes that we’re actually going to recycle blades because one guy or one company kind of did the industry wrong.
Lightning is an act of God,
but lightning damage is not. Actually, it’s very predictable and very preventable. Strike Tape is a lightning protection system upgrade for wind turbines made by WeatherGuard. It dramatically improves the effectiveness of the factory LPS, so you can stop worrying about lightning damage.
Visit weatherguardwind. com to learn more, read a case study, and schedule a call today.
Allen Hall: The Goto Floating Wind Farm Consortium delayed the commissioning of the Goto City Offshore Wind Power Generation Project by two years, shifting its initial target date of January 2024 to January 2026. Well, you ask yourself, why did they do that?
Well the delay was prompted by the discovery of defects in the floating structures used for the project during construction. So somebody said, oops, we have something seriously wrong here. And it’s going to set us back two years. Now you know, the, the Toyota Corporation, which is involved in this and they’re in the, in the construction identify the defects and, and it’s going to resolve them, which is absolutely the right way to do it.
And I, and Phil, so when I read this article, like, yeah. They’re going to have defects. It’s something completely new you’re building. And yeah, it’s, it’s super complicated and there’s a defect and they had identified it and they’re going to go fix it, but two years is a long time. So it makes me think it’s something pretty deep into the design that they had to go fix.
And what are the ramifications for other wind projects like in the United States, where it’s really started kicking off something new because it’s so new, there’s going to be delays, right? Has to be.
Philip Totaro: Yeah, there’s, there’s a few aspects of this that are actually fairly interesting, Allen, because first off in Japan, they’ve had many, many years of experience at doing kind of floating, you know, this is a spar buoy technology.
So they, in Japan, they’ve had many years of doing demo projects with. This Sparbuoy architecture including using the basically the same Hitachi 2. 1 megawatt turbines that are supposed to go into this Goto demo project. And so it’s, it’s a bit curious that they’ve run into issues and they weren’t very specific in, in what they publicly released either.
We talked about potentially this could be weld issues, it could be any number of things, it could just be something to do with the design overall. I would think that if it’s a two year delay, there’s some kind of fundamental flaw with the overall design that perhaps wasn’t identified during the the, the demonstration projects that they’ve done, you know, over the past, I want to say, six or seven years.
Over there. So the, the impact of this project, notwithstanding, you know, the spar buoy technology is also something that could be utilized in California. It’s being utilized right now in Norway and off Scotland with the high wind projects. You know, they’re talking about utilizing this type of technology, even elsewhere in Europe, South Korea, et cetera.
So and, and many more floating projects in Japan, by the way. So. Including the, the full scale project that they have, because I think the, the entire Goto project was intended to be something like 800 megawatts or more, I want to say, if memory serves. So the, the point being, I guess there’s, there’s going to be as you said, there’s always going to be issues with developing a new product, but I’m looking at this like it’s not necessarily a new product.
If you’ve been in wind for a long time, you’ve heard about floating forever. I mean, I’ve been in wind energy for 16 years and 16 years ago, we were talking about floating wind. And, you know, it’s taking an awfully long time to get these solutions developed in the first place, which is also a bit of a head scratcher when you consider that things like tension, like platforms are already used in oil and gas.
And what I don’t quite understand is why we’ve decided to design all brand new. You know, offshore wind specific. Certainly there’s a bit of engineering work that needs to go into customizing something that has previously been used, proven in oil and gas. But why aren’t we leveraging more of this oil and gas experience, particularly leveraging tension like platforms or you know, spar buoy technology or something else that has been used for, You know, dozens and dozens of years already has engineering certification, et cetera, et cetera.
So this one’s a bit of a bit of a head scratcher.
Rosemary Barnes: It’s really weird that it’s two years. They’ve got, they’ve only got eight of these. Being spar bouys. We say boy, not buoy in Australia. So sorry, I can’t change that. So yeah, they’ve got eight of these spa boys structures to, to deal with. Three of them are already installed.
They’re going to inspect one of them for damages, but they think that it’s going to take two years. I mean, you can definitely like, whatever it is, you can make eight of them in less than two years. Right. So. To me, it says it’s not actually a problem with the way that they’ve been manufactured or a problem with the materials.
The problem is that they don’t know why. Something’s gone wrong and they don’t know why yet. That, you know, that’s the only thing that can explain a two year time frame to me. And I mean, yeah, that’s just speculation. But if it was just a bad weld, then okay, you remake those three. With good welds and make sure that the other five that haven’t been made yet are also made with good welds and then you move on.
I mean, it’s not going to take you, that’ll take you a few, a few months, maybe a year. And the rest of the project can, you know, still happen as you know, it was originally planned, but I get the impression that they don’t know what’s wrong. They’re going to have to make some sort of design change that they don’t understand yet.
And they don’t understand its impact on all the other parts of the project. So I’ve had to push everything back. That’s kind of my instinctive feel for it. But yeah, I know Joel’s worked a lot with offshore oil and gas. So maybe you can tell me what your, what your gut feel is based on the limited information that we have.
Joel Saxum: I think, Rosemary, you’re, you’re definitely on the same track my mind is, they don’t, somehow they don’t know, right, so you can do FEA modeling and all kinds of grandiose CFD stuff, but your, if your inputs in your software program don’t match reality, which is quite often is reality. Right? Then you may not be able to model something, right?
You may put it into the water and then all of a sudden the, there’s a floating moment or there’s a tipping moment that doesn’t make sense. When you’re dealing with offshore floating wind, you’re dealing with 9 degrees of freedom plus centrifugal motion and all kinds of things. So that’s a really complicated problem.
Another one here to think about is on the economic side of things and the commercial side of things. When you look at the group here, go to or go to Floating Wind Farm Consortium. It’s a lot harder to get things done when you have a group of companies working on them together with the government involved.
So, I also believe that there may be some under promise, over deliver going on here. I would expect these to be, this timeline to actually be shorter than two years. So, in a lot of the offshore like oil and gas projects that I’ve been involved in, you have like one, if you can get with a good EPC, like say a I don’t know, Technipe FMC, or a Baker, or someone like that, or a Saipem, where they’re doing everything in house, they’re doing the design, they’re doing the procurement, they’re doing the construction, they’re doing the install, those projects almost always will go faster and more efficiently than they will if you have company A, B, C, D, X, Y, Z, all doing different parts and having to work together, and I see this as Kind of because this is a you know, it’s a it’s a new thing.
It’s floating wind Japan. They got the government involved They’ve got a bunch of other kind of consortiums involved and some other people I think that that will that’s one of the things that will slow the process down But I’m gonna go right back with Rosemary said I don’t think they know what the problem is yet Because I think that they’re the possibility of modeling things that they didn’t expect is real.
Allen Hall: Hey, Uptime listeners. We know how difficult it is to keep track of the wind industry. That’s why we read PES Wind magazine. PES Wind doesn’t summarize the news. It digs into the tough issues. And PES Wind is written by the experts. So you can get the in depth info you need. Check out the wind industry’s leading trade publication.
PES Wind at PESWind. com
Touchwind is developing a floating wind turbine that It’s anchored to the seabed rather than fixed to the seabed floor. The turbine must, mass bends in low wind and then it’s drawn upright in stronger wind. So what this thing looks like, it’s a single piece blade. It’s like those toy helicopters with, on the stick.
It’s got the blade on top of the stick and you spin it between your palms and it flies in the air. Which is the impetus for the Wright brothers to get involved in flying, by the way, if you didn’t know that. So the, this touch wind is very similar to this design.
Rosemary Barnes: Cutting edge.
Allen Hall: A what?
Rosemary Barnes: It sounds cutting edge if it was the inspiration for the Wright brothers.
Allen Hall: Yeah, the father brought home a toy for Christmas. He was a preacher and he came home, I think it was for Christmas but he brought home a toy from being on the road and that was the toy. And then they got interested in flying and then the rest is history.
Rosemary Barnes: But can we just relate this back to the previous story?
So one of their points is, okay, this is a floating offshore turbine that’s anchored to the seabed rather than fixed in the ground. And Joel, please tell me if I’m crazy, but isn’t that the entire point of floating offshore, that it’s going to be anchored if it was fixed to the ground, then it wouldn’t be, floating, right? It would just be fixed, a fixed spot of offshore wind. Am I, am I crazy? Is that, is that really a selling point for a floating turbine?
Joel Saxum: For me, this one could be because I’d looked at the design of it last week, actually, or two weeks ago, I was looking at this because they had a LinkedIn article.
It makes sense to install these floating in shallow water because of how small they are. There’s how easy they are to transport. Like, like you can do, you can do there’s a vessel that’s known as an A. H. T. It’s an anchor, anchor handling tugboat. So basically it’s really powerful like a tugboat. 30, 000 horsepower type thing.
But it just has a big wide open back deck. And the back deck will have… You can put, it’s made for anchoring things, so it’ll have big chains and loops, you can have a mile of chain on this thing. But you can just put a chain in one of these, drag it behind a boat, flop the chain overboard and be done with it.
Like, there’s no monopile installation, there’s no nothing. You can put these things out in 50 meters of water, no problem. So, I think that one of the ideas behind the Touchwind product here, Is that they could make the L they can lower LCOE of offshore wind by not having to have all of the fixed bottom features, but in shallow water.
Rosemary Barnes: But does it scale? What do you think? Cause you know, they’ve got this one piece blade. So it’s basically like two, two, it’s a two blade rotor, but the two blades are joined in the middle. So you’ve just got one thing. So that sounds nice and simple. And it’s really similar to that. You’d like, there’s a lot of small wind turbines that have that design in particular in the, in the Danish West coast.
They have a lot of farms have this particular two bladed wind turbine, a Gaia wind turbine. I think the company’s gone out of business now, but… Yeah, super popular, it’s just one, one fixed blade and then the, it’s an upwind design as well. So, sorry, I mean downwind and it teeters it’s got a spring in there so that, you know, it automatically kind of, you know, like changes the angle of the rotor depending on the wind.
So that sounds a lot like what Touchwind is claiming and, you know, it’s a good, robust kind of low maintenance design for small wind. But does it, does it scale well, because, you know, it’s really cool to just have, you know, one piece, nice and rigid, less, you know, bolts to worry about, installation would be nice and fast.
But, you know, if you’re thinking about most offshore wind these days you know, if you’re getting up beyond 10 megawatts, their blades are, you know, over a hundred meters long. So if you’ve got two blades in one piece, then now you’re going to have a 250 meter long single blade. How are you going to install that?
It sounds to me like maybe this one will never, never reach those sort of sizes, which is not to say that that’s, that’s bad but you’re not going to get, you know, some of the benefits for offshore of having really big turbines is that you don’t have so many connection points and don’t have to lay so many subsea cables because, you know, you’ve just got fewer, fewer points to connect up.
So yeah, I think it’ll be a slightly different kind of application than what the main direction that we’re seeing offshore wind in these days.
Joel Saxum: Yeah, I’d have to agree with you on the, some of the engineering difficulties there. If you look at Touchwind’s website, they’re claiming in this design, a 200 meter rotor is capable of a 12.
5 megawatt machine. In with their design. And that’s 31 over 31, 000 meters squared surface area. So that’s big. Now, I completely agree with you. It does. Does it scale? Is it are you able to do this? I guess on the, on the backside of things that I need to see more of the, the commercials of it, right?
Because does it make sense to scale it to that big with the structural and the, the structural issues in the O and M issues that you could run into going to that size? Does it make sense to put? 2 to 1 out of 100 meter ones at 6 megawatts, or 3 megawatts. Cause it, there might be a, the economy of scale with this thing might plateau off at a certain level, right?
Or even come back down at a certain level because of the difficulty in manufacturing that rotor. So, I completely understand where you’re coming from, and I think that we’re onto something there. I almost think it’s easier just to put smaller ones out, but more of them for this design.
Allen Hall: I know what Phil’s thinking right now.
There’s no way you’re going to build a port and the infrastructure to do it. It’s going to cost you more to do all the, all the expenses stuff on land than it is to put that out to sea, I think. Right, Phil? I mean, we know we have port problems in the United States right now. I can’t imagine building a port big enough to handle that.
Philip Totaro: Realistically, the other issue is… Getting this thing designed, getting it certified, and then getting it done at scale implies probably about a billion dollar effort. This is a startup company in the Netherlands. They’ve recently gotten investment from Mitsui OSK in, in Japan. Which is good, but they don’t have what they need in place to be able to This is basically just gonna be a demo project for now, and eventually could turn into something.
I could see this potentially displacing what everybody thought was gonna be a big new trend, which was these kites. Which, let’s not go there right now, but, you know, it There’s a reason why the industry has kinda settled on a design, which is a three bladed upwind horizontal axis turbine on either a monopile, a jacket, or a floating foundation or pile cap, whatever.
You know, it’s bankable. There’s a lot of things that are great about this from an engineering standpoint. It’s very clever interesting design. But at the end of the day, insurance companies and banks run the industry, okay? Not the supply chain companies and not even the developers. So, you have to be able to, you know, there are so many solutions out there that fall into this bucket of very, very clever engineering work, very clever technologically.
Yes, you can make it work from an engineering standpoint if you have the right investment, but are you designing something that is bankable? Are you designing something that is insurable? I don’t see that with this. And I don’t know that there’s any scale you’re going to achieve with this. That’s going to meaningfully offset.
I mean, when you’re already talking about the profitability challenges that everybody faces, you’re not going to introduce a radical new technology into a market where we’re already trying to get. You know, the, the conventional technology to work well enough so it can turn a profit for everybody that’s involved in the value chain, from the project developers, to the supply chain companies, to the financiers.
So yeah, I Good, good luck to ’em. But I, I don’t see this being anything more than a science project.
Rosemary Barnes: There’s a lot of, there’s a lot of companies trying though, in in floating offshore. You know, I, I definitely agree with you for. for the most part that that’s probably what’s going to happen. But I do think that you know, the design that evolved to make sense for onshore wind doesn’t necessarily, it’s not necessarily the best technical solution to the floating offshore problem.
So I do think that there is you know, possibility that the best design hasn’t been arrived at yet, but I can kind of see, imagine that what you’d say to that is, you know, like the. What do they call it? The Valley of Death, or I don’t know if that’s really correctly applied here, but the commercial realities of actually getting to that You know, to that better design is so any new emerging technology and something as expensive to develop as an offshore wind turbine really faces a big handicap compared to an existing company that’s already ironed out all of the kinks in their design and just has to, you know, have the few little changes to.
You know, to figure out with floating offshore, whereas this design and all the others that are like it, like the wind catching and the C12 and I don’t know, airborne wind. There’s nothing wrong with any of those concepts and maybe, you know, if wind energy didn’t exist yet at all, that is the direction we’d be going, but they don’t just have to figure out the little quirks of floating offshore.
They have to figure out all of the quirks of just wind in general. So. It is hard to imagine any of them succeeding. As an engineer, I, you know, I love new technology and I don’t, I, you know, I want to see new technologies emerge because that’s, that’s interesting. It’s kind of boring to just, you know, Oh, we figured this out in 1990 and now we’re not going to do anything different.
Joel Saxum: The guy who was pushing this whole thing is originally developed, developed the concept in the 1970s. And now he is focusing on a full time. So that means that the guy who’s pushing this thing that was the inventor is now at least 75 years old. Nothing against old guys. I like old guys. But they might run out of, they might run out of steam sooner than you think as well.
Allen Hall: Thumbed through the new PES Wind Magazine and came across an article from a company called System Seals, and they’re based in Cleveland, Ohio. And they have developed a new kind of seal for main bearings on wind turbines, which is kind of cool, but it’s like a, It’s a, it’s a, it’s got, it’s kind of like a screw to it.
So it’s like a typical seal, but it’s got this, this winding in it sort of, so that the, the fluid gets pushed back into the, to the gearbox into the bearings. So it keeps everything on the outside dry and all the things inside lubricated like it’s supposed to. And it’s a pretty unique thing. So it’s sort of like pumps the fluid or the grease back into the container.
And it has, I guess it’s been used on like 10, 000 turbines at this point. And I, when we were down in Texas at a wind farm. Last week, one of the things you notice when you’re driving through West Texas is there’s oil and grease and stuff on the towers. It’s pretty prevalent in some cases, you think, man, the seals have gone bad.
And I just think, man, the seals are such a big problem, right? It’s such a complicated design and this. System seal Vortex seal makes a lot of sense to me. I’m surprised it’s not being used in more places, actually.
Joel Saxum: Even when you hold a seal of any type, right? Whether it’s a piston seal or a flange seal, face seal, in your hand, that’s like, you know, some, you know, it could be on a skid steer or something, any kind of little industrial equipment, that’s those, even those little seals leak pretty easily.
Now imagine making that seal have to be meters across. If you’re on your main bearing seal and like have not could not have no imperfections cannot have anything any little issues So that’s tough, right? I mean anybody that spent any time in the wind industry has driven through a wind farm that has Grease, oil, anything leaking down out of the tower, you know, from yaw motors, or from the main bearing itself, or from some kind of rotating equipment inside of that machine.
And now that is it’s a, it’s a pain, right? Especially in Texas, all the dust collects on it. It looks bad, but also when you see that, you know that that machine is, is having lubrication problems. Or at some point in time did, right? The last thing you want to do is run them dry. So a, an engineering design that…
Combats some of these issues because it basically creates a almost a analog pump that pumps the fluid backwards in instead of having it rest against the seal, right? So it’s not, they’re not a pump to actually maintain per se, but the design of it lends itself to being a helical pump, taking advantage of the centrifugal motion of the, of the bearing.
So that’s great. The, one of the biggest problems that we have in the wind industry for looking at all these leaks is the simple fact that these things are so big, so remote. And it’s tough to work on, right? So they’re, they’re running up there. The ideally, you know, everybody wants 100 percent uptime.
Well, you know, we know that that number is closer to 40, 35%. So either way, these things, these turbines are out there running 120, 100, 120, 150 days out of the year. And there’s not someone under dedicated to each one to make sure that you see every little thing going on. So a bit of a innovation here from system seals with the, the vortex plus seals is going to be welcome in the industry for sure, especially when you get to these repower projects, as we keep talking that the repower is the time to swap these things out.
Everybody’s doing main bearings when you’re doing repowers.
Allen Hall: Yeah. How does that work? Right. I, does it have to be part of the OEM equipment when you do a repower like that, is that. Or can they upgrade out in the field?
Joel Saxum: Yeah, you can upgrade in the field, but it all depends on how you do your, your repower and who’s doing your repower for you.
Right? So sometimes there is OEM repower programs. You can, if you’ve got GE turbines, you can call GE and say, we want to repower. And they’ll say, okay, one, you know, we’ll take your 1. 5, make it a 1. 6. We’ll put these blades and we’ll put these mean bearings. This will upgrade control systems, yada, yada, yada.
And you can pay for it. Or, you can design your own. If you’re an asset owner, you say, like, well, I want, you know, this Bachmann over here, and I want these main bearings, and I like these blades, and I want to change, you can do all that on your own as well. So you know, the majority of times, when you’re in the field, you’re trying to do things quickly, so.
You’ll drop the whole rotor and then you may swap the main bearing out. And at that point in time, boom, when you put the new main bearing in, change it out in the field, put that new seal in, bang, put it up.
Allen Hall: I’d be shocked if a lot of operators are not doing that on a repower. Because they’ve had so many, especially in the sort of the two megawatt and under turbines, they’ve had so many seals leak.
They’re going to want to upgrade. And you think that system seals could walk right in there and make a pretty easy sale because the proof is in the pudding, right? It’s pretty easy to find them.
Joel Saxum: Yeah, I can’t validate this for sure, but in my mind I’m thinking right now, SystemSeals is a company from Ohio, right?
You’re gonna do a repower, you wanna use American products, qualify for ITC, 30 percent tax break.
Allen Hall: EDPR operates the Top Crop Wind Farm in Northern Illinois. The site consists of 68… GE 1. 5 megawatt SLE machines at top crop one and 132 GE 1. 5 megawatt SLE machines at top crop two. The capital investment on this wind, on these wind farms is crazy.
It’s almost 700 million with over the lifetime of the project, about 33, 34 million being paid to landowners. And about 30 million going to the local governments. They created 20 permanent jobs at the site and about 250 construction jobs. And it is again, one of these massive farms that nobody hears about.
And it’s doing a lot of great things for the local community. And because it has a cool name, the top crop wind farm in Illinois is our wind farm of the week. That’s going to do it for this week’s Uptime Wind Energy podcast. Thanks for listening and please give us a five star rating on your podcast platform and subscribe and then share notes below to our lovely newsletter, Uptime Tech News.
And check out Rosemary’s YouTube channel, Engineering with Rosie, and we’ll see you here next week on the Uptime Wind Energy podcast.