Swarfcast
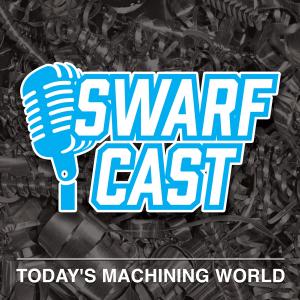
Tracking Your Shop’s Performance, with Lauren Dunford—EP. 147
Our guest on today’s podcast is Lauren Dunford, CEO and cofounder of Guidewheel. Guidewheel produces a sensor that clips onto a machine tool’s power supply to collect data while it runs. The data helps manufacturers understand what processes on the shop floor need to be improved and guides them toward solutions.
Scroll down to read more and listen to the podcast. Or listen on your phone with Google Podcasts, Apple Podcasts, Spotify, or your favorite app.
Find us on Social:
Facebook: https://www.facebook.com/swarfcast
Instagram: https://www.instagram.com/swarfcast/
LinkedIn: https://www.linkedin.com/company/todays-machining-world/
Twitter: https://twitter.com/tmwswarfblog
Main Points
Guidewheel’s sensor is a current transformer that clips around the first phase of the 3-phase electrical connection to a machine. This means it can be configured for use with virtually any type of machine tool, no matter how sophisticated. It monitors the electricity draw recording when the machine is running on load, idle, or off. The live data is transferred to the cloud where a software platform sends alerts to shops to inform them if the machine is functioning correctly. The software also analyzes the data in the context of what’s happening on the shop floor, layering in metrics such as production, quality and speed. This helps management understand which processes need to be improved upon.
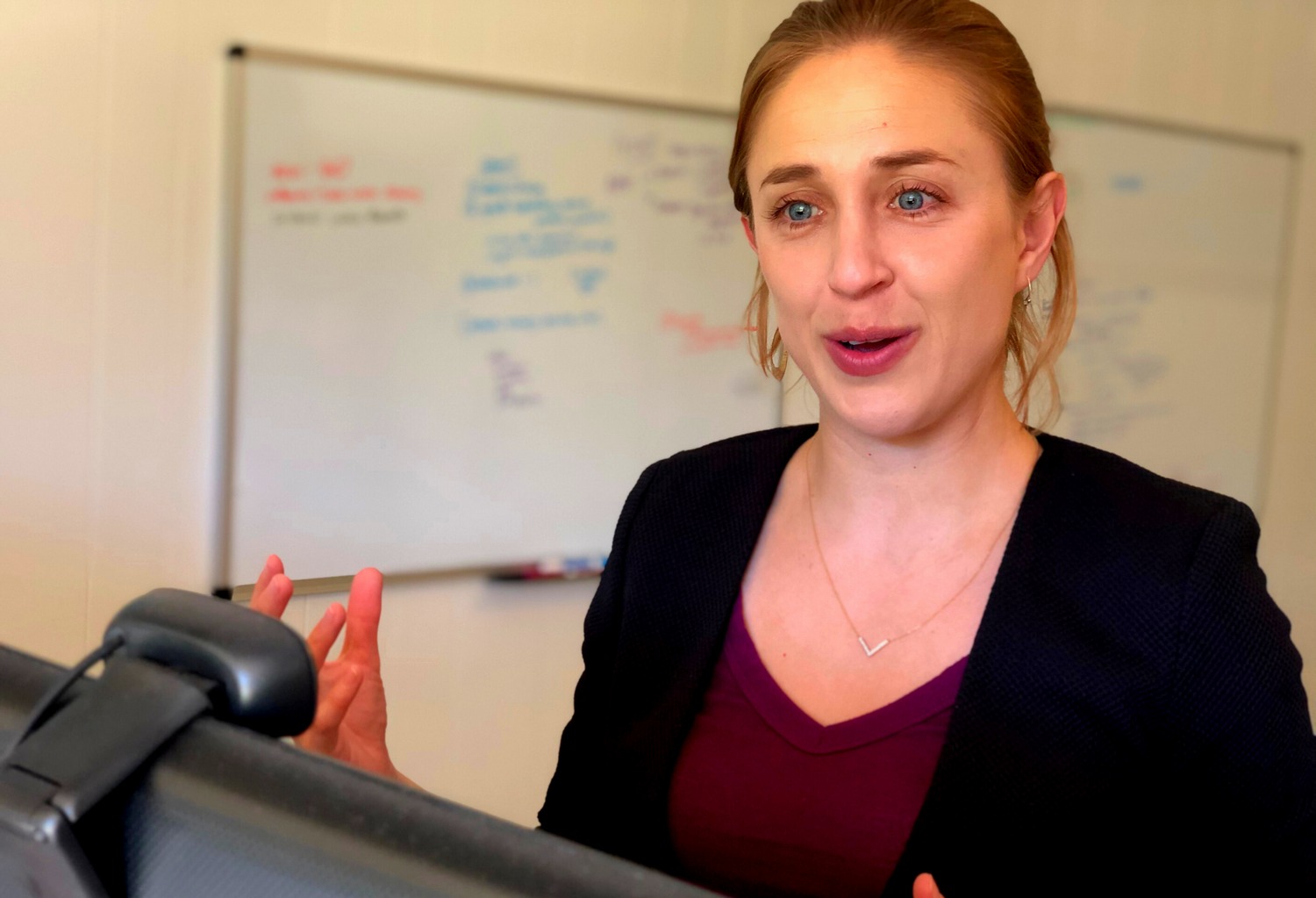
Lauren Dunford, CEO and Co-Founder of Guidewheel
Guidewheel’s data might reveal that various shifts differ in production output, pointing out inefficiencies of certain personnel. It could also reveal that some machines are poorly maintained or not well suited for certain tasks. Guidewheel’s sensors often show that machine changeover and setup are processes that could significantly be improved. When the sensors record that one worker averages 3 hours to change over a machine while another worker takes 30 minutes, a company can then observe both people working and compare their processes.
Companies often find that the culprit for slow setup or changeover time is that necessary tools for the job aren’t already next to a machine. When workers have to leave their machines to obtain the tools they need, they may have to walk across the shop floor where they could be held up by fellow employees or sidetracked by other distractions.
Guidewheel’s data helps companies cope with labor shortages by boosting their efficiency. Sometimes it produces data revealing that more employees are needed, justifying the cost of additional staff.
Lauren says typically a manufacturing company’s perceived utilization for its equipment is much higher than its actual utilization. For example, she sees high volume shops targeting 85% utilization while having actual utilization of 60-65%. She says low volume shops often have actual utilization of 30-40% or even lower.
I asked Lauren at the end of the interview if the increased efficiency was enabling people to work fewer hours. Her first reaction was that people are still working the same amount but output is being increased. However, she added that Guidewheel’s monitoring tools have enabled supervisors to spend less time at their shops because they don’t have to stand around watching employees and troubleshooting problems.
Questions:
What are the most inefficient processes in your work?
When are you least efficient in your daily life?
The post Tracking Your Shop’s Performance, with Lauren Dunford—EP. 147 first appeared on Today’s Machining World.