Swarfcast
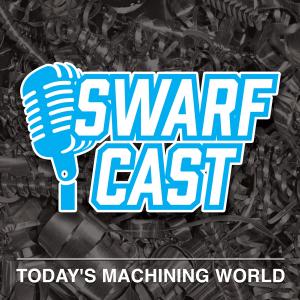
Ep. 88 – Collaborative Robots on Haas Mills with Timo Lunceford
Today’s guest on the show is Timo Lunceford, general manager of Swiss Productions, a 25,000-square-foot Swiss CNC shop in Ventura, California, that specializes in fluidic medical components. Recently Swiss Productions introduced two 7-axis collaborative robots to work in tandem with two Haas CNC mills. Timo says the robots increase the production on each machine by the equivalent of 30-40 hours per week. Scroll down to listen to the podcast. Or listen on your phone on Apple Podcasts and Google Podcasts. Main Points (3:00) Timo discusses his background. He Joined Swiss Productions at age 20 when he married the owner’s daughter. He has worked his way up from the very bottom to Vice President and General Manager. (6:00) Timo describes how Swiss Productions grew from an 8,000-square-foot shop with just 12 machines to a 25,000-square-foot facility with over 50 machines. He says 70% of the company’s business is making medical device fluidic components. It also manufactures parts for irrigation, automotive, and aerospace industries. (7:55) Timo speaks about the company’s unique experience manufacturing parts for the medical industry. He says a major part of growing in that sector is networking and developing relationships around the world. (10:40) Timo talks about introducing collaborative robots to the machine shop. The company recently purchased two OB7 cobots from Productive Robotics. Timo says he chose this brand because it seemed to be very user friendly and feature 7-axis models. (12:20) Timo says that at first employees were suspicious about the role of the robots in the shop. However, soon they realized that their jobs were not at risk and that the robots handled tedious labor that freed them up to complete more interesting tasks. (12:50) Timo describes how the OB7 robots help make valves for syringe pumps working in tandem with Haas mills. The robot picks up the unfinished valve, opens up the door of the machine, blows out the collet inside the machine and puts the unfinished part in the machine. Then, it opens a collet holding a finished part, takes the part out and drops it into a bucket. The robot then closes the collet, closes the machine’s door, and hits the start button on the machine. The robots can run lights out. (14:40) Timo discusses the uniqueness of the OB7 model and how it is programmed through demonstration. (15:45) Timo speaks about how the shop has increased the productivity of their two Haas mills by 30-35% using collaborative robots. He estimates the shop saves 30-40 production hours a week on each machine. (16:20) Timo says that time is the most precious commodity for both the business and its employees. For the last 10 years, employees at Swiss Productions have enjoyed a 4-day workweek (10 hour days). He says that automation is playing a part to save the company money and give employees more time with their families. (19:30) Timo says that Swiss Productions has remained operational throughout the COVID-19 pandemic because it is considered an essential business.