Product Mastery Now for Product Managers, Leaders, and Innovators
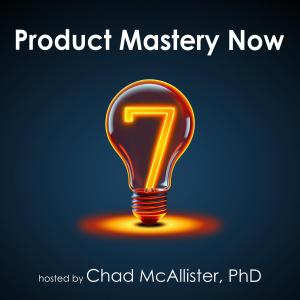
509: Prototyping mastery for product managers – with Matthew Wettergreen, PhD
Watch on YouTube
TLDR
- The value of starting with simple, low-fidelity prototypes
- The importance of focusing on the problem before jumping to solutions
- The need for making well-supported decisions throughout product development
- Real-world examples of how prototyping leads to innovative solutions
Introduction
In this episode of Product Mastery Now, I’m talking with Dr. Matthew Wettergreen, Associate Teaching Professor at the Oshman Engineering Design Kitchen (OEDK) at Rice University. We discuss the benefits of low-fidelity prototyping, the engineering design process, and how to use prototypes effectively to solve problems and validate ideas. The episode also covers potential pitfalls in prototyping and best practices for product managers.
The Power of Prototyping in Product Management
The Oshman Engineering Design Kitchen at Rice University is an academic makerspaces where students learn innovation and product development skills. This 20,000 square foot facility has top-notch machines for digital and 3D prototyping, allowing students to create products that look like store-bought items.
Prototyping is a key tool for product managers who want to create value for customers. Matthew explains that prototypes help product managers confidently develop solutions that make customers happy. By using prototypes wisely, product teams can figure out what truly meets customer needs and test solutions before launching them in the market.
The Value of Low-Fidelity Prototyping
Matthew has discovered that in many parts of the world, people build things with no budget at all, not just a low budget. He saw this resourcefulness in places like Ethiopia, where everyday items are reused in clever ways. For example, highway dividers made from cut-up palm oil containers show how people can create solutions with limited resources.
In the OEDK, students have access to high-tech equipment, but they won’t always have the OEDK available to them. At the ODEK, students always start with no budget and prototype using readily available materials.
This approach, called low-fidelity prototyping, has several benefits:
- Causes students to produce more prototypes
- Results in higher fidelity and resolution in the final product
- Only require practical ingenuity and creative problem-solving to produce
- Encourages quick iteration
- Allows for fast and cheap testing of ideas
- Makes it easier for people to work together and share ideas
Types of Prototypes and Their Fidelity
Prototyping is a method of problem-solving that creates physical or digital objects, called artifacts.
Prototype Fidelity
Characteristics
Best Use
Low-Fidelity
Meets few design goals, not at the right scale, made from analogical materials
Early brainstorming, fast testing of ideas
Medium-Fidelity
Meets some design goals, close to actual scale, made from mostly suitable materials
User testing, gathering detailed feedback
High-Fidelity
Meets most design goals, at the correct scale, made from the best available materials
Final testing, showing to stakeholders

The Engineering Design Process
Matthew introduces the seven-step Engineering Design Process used at the OEDK:
This approach begins with understanding the problem before jumping to solutions. Fifty-one percent of the design experience should be spent in the prototyping, testing, and iterating phase.
- Clarify the team assignment
- Develop a Design Context Review
- Set design objectives and constraints
- Develop solution options
- Evaluate solutions
- Prototype and test iteratively
- Iterate based on feedback

Overcoming Challenges in the Design Process
One of the main challenges in product development is the tendency to rush into solutions without fully exploring the problem. Matthew offers several strategies to overcome this:
- Use the “freezer” concept: Put initial ideas on hold to allow for deeper problem exploration
- Collect extensive information about the topic before brainstorming then marinate on that information and allow your subconscious to form connections
- Collaborate with diverse teams to bring in different perspectives
Matthew also addresses the myth of the lone innovator: People who seem like lone innovators, like Steve Jobs or Thomas Edison, actually represent an immense number of humans who supported their accomplishments. Successful innovation is almost always a team effort. Matthew tells his students, “Work with people who are smarter than you and work with people who think differently from you. You will be better as a result of that.”
Case Studies from the OEDK
To show how prototyping works in real-world scenarios, Matthew shares two interesting case studies from the OEDK:
1. Giraffe Enrichment Project for Houston Zoo
The challenge was to extend the feeding time for giraffes in captivity to better match their natural eating habits. This project shows how prototyping often involves multiple attempts:
- First attempt: Giraffes didn’t interact with the prototype
- Second attempt: Didn’t hold enough hay
- Third attempt: Used dangerous materials (wire)
- Fourth attempt: Successfully created a hay-shaped box with safe materials
The final prototype has been used at the Houston Zoo for nearly a decade and has been adopted by other zoos.
2. Apollo BVM Ventilator during COVID-19
During the early stages of the COVID-19 pandemic, the OEDK team quickly developed a bridge ventilator called the Apollo BVM. This project highlights the power of rapid prototyping and iteration:
- Intense development period of one month
- Collaboration with respiratory therapists and pulmonologists
- Parallel prototyping of individual components and the whole system
- Resulted in a functional product that was licensed for use during the ventilator shortage
Potential Pitfalls in Prototyping
Prototypes can be used in a misleading way, such as presenting a beautiful prototype to convince stakeholders that it’s a good solution, rather than collecting feedback. It is acceptable to produce an ugly prototype, but it is less acceptable to produce a beautiful prototype that lacks all functionality in order to mislead people.
Matthew recommends that his students prepare focused questions for client conversations about prototypes and share assumptions built into the prototype’s design with the client. This allows clients to give suggestions for revising these assumptions.
Best Practices in Prototyping for Product Managers
- Fall in love with the problem, not the solution
- Whenever possible, allow stakeholders to physically handle prototypes, as this often leads to different insights than just viewing images or videos.
- Overcome the “I’m not good at prototyping” mindset: Encourage team members to build to learn.
Conclusion
Key takeaways from this episode include the value of starting with simple prototypes, the importance of focusing on the problem before rushing to solutions, and the need for well-supported decision-making throughout the product development process. By applying these insights to their work, product managers can drive innovation and create more value for their customers and organizations.
Useful links:
- Learn more about the Oshman Engineering Design Kitchen
- Check out the Global Medical Innovation Master of Bioengineering that Matthew runs
- Connect with Matthew on LinkedIn
Innovation Quote
“Make defensible decisions.” – Matthew Wettergreen
Application Questions
- How can you incorporate more low-fidelity prototyping into your early-stage product development process?
- In what ways can you improve your process for gathering and incorporating user feedback on prototypes?
- How can you help foster a culture that values “falling in love with the problem” rather than becoming too attached to specific solutions?
- Where might you be rushing to solutions without fully exploring the problem?
- How can you use prototyping to improve collaboration across different teams and departments in your organization?
Bio
Matthew Wettergreen is Director of the Global Medical Innovation Master of Bioengineering program and the Program Director of the NSF-funded I-ACED Scholar Program at Rice University. He is also an Associate Teaching Professor at the award-winning Oshman Engineering Design Kitchen (OEDK) at Rice University, recruited as the first full-time faculty hire in 2013. At the OEDK he co-developed the engineering design curriculum, including the flagship first-year engineering design course and the Prototyping and Fabrication course. Wettergreen is the co-author of the textbook Introduction to Engineering Design. Over nearly fifteen years of developing client-based engineering design courses and with a deep interest in engineering education, Dr. Wettergreen has deployed engineering design curriculum and helped to support the development of makerspaces on five continents. His design work has been featured on the cover of NASA Tech Briefs, in the Wall Street Journal, The Atlantic, Make Magazine, and Texas Monthly.
Thanks!
Thank you for taking the journey to product mastery and learning with me from the successes and failures of product innovators, managers, and developers. If you enjoyed the discussion, help out a fellow product manager by sharing it using the social media buttons you see below.