Emerson Automation Experts
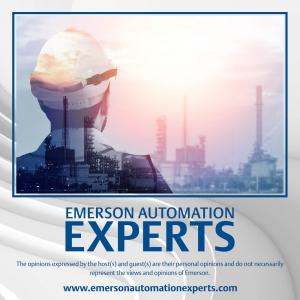
Podcast: How to Approach Energy Management Projects
Emerson's Sam Thiara joined me virtually from the UK for our continuing FIRSTHAND: Operational Certainty Consulting in a Pod podcast series. Sam, whom you may recall from earlier energy management-related posts, is a member of the Operational Certainty Consulting Group speaking with manufacturers about their energy management challenges. In this 10-minute podcast, we discuss the process of planning and executing an energy management project and the importance of getting the benchmarks and baseline performance established early in the planning. These benchmarks and baselines are helpful not only in project justification and return on investment post project, but also help to justify the ongoing support required to maintain the savings over time. https://www.emersonautomationexperts.com/wp-content/uploads/2019/01/Podcast-Sam-Thiara-Energy-Management.mp3 Transcript Jim: Hi, this is Jim Cahill, and welcome to another edition of "FIRSTHAND: Operational Certainty Consulting in a Pod" podcast series. Today, I'm joined by Sam Thiara, and Sam is in our operational certainty consulting team and covers the Europe, Middle East, and Africa regions. And Sam gets involved with improving the performance of manufacturing plants through digital transformation initiatives. Welcome, Sam. Sam: Hello, Jim. Thank you for inviting me back to this energy management podcast. Jim: It's great to speak with you too, Sam. So let's get started. What are common concerns you hear that drive manufacturers to seek help in energy management initiatives? Sam: Customers tell us they have several factors that drive energy management initiatives within their facilities. The need to control operating costs, especially so in energy-intensive industries where energy can often represent up to 50%, if not more, of a site's operating cost, improving energy efficiency goes direct to the company's bottom line, helping their competitiveness, and in many cases, releasing additional capital from lower fuel bills. Equally, we are seeing many plants looking to eliminate or minimize sources of energy wastage, such as excessive steam leaks, and the reuse of processed waste gases. We're also seeing an increasing number of manufacturers adopting energy management standards, such as ISO 50001, placing a systematic focus on plants to become increasingly more energy efficient by bringing people, processes, technology, and best practices together. Jim: So, it sounds like there's concerns around costs, emissions, and standards that are driving this. If a manufacturer or a producer decides to move forward and work with the Emerson energy management consulting team, what are common preparation steps they would take to prepare for the engagement? Sam: Well, this can depend on the customer's experience, capabilities, and the maturity of their energy programs. In some cases, we have been asked to provide plant-wide assessments, helping a site prepare a master plan, and help prioritize improvement opportunities based upon multiple criteria, such as profitability, production, environmental, and safety, and in almost all cases, supporting an economic case for project justification. In cases where a site has undertaken their own assessment, we get called in to help improve the performance of specific assets, such as boilers, process fired heaters, and furnaces, to much larger assets, like powerhouses, distillation units, and steam systems. The typical and most common starting point tends to begin by undertaking a discovery study where we work closely with our customers to investigate and provide solutions to overcome the root cause of an underlying issue that results in poor energy efficiency. Jim: It sounds like getting involved early from the upfront analysis and project justification phase all the way through being able to measure the results and get return on investment is a very effective way to go....