Emerson Automation Experts
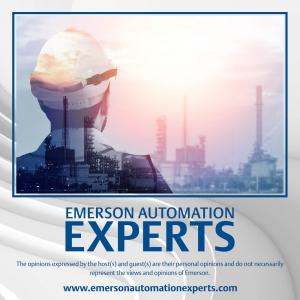
Adopting New Tailings Standards for Mine Sustainability Podcast
Miners have always faced the challenge of how best to safely and sustainably manage the vast amounts of uneconomic material left over from the mining process, known as tailings. A new global standard charts a path for the industry to further improve its management practices.
In this podcast, Emerson’s Steve Brewer joins me to discuss some of the challenges in adopting the new standard and the role of valve technology in managing tailings successfully.
Give the podcast a listen and be sure to visit the application pages on Emerson.com for tailings pipeline & spigot isolation and tailings pump isolation. Here, you will find more information on the solutions engineered specifically to support more sustainable tailings management.
TranscriptJim: Hi, everyone. I’m Jim Cahill with another Emerson Automation Experts podcast. Today, we’ll be discussing tailings in mining operations. What they are, what miners’ challenges are in dealing with them, and what are some ways these challenges are being solved.
I’m joined today by Steve Brewer to discuss all these topics and more.
Welcome to the podcast, Steve.
Steve: Thank you. Thank you, Jim. Thanks for hosting.
Jim: Well, we’re glad to have you here today to get a lot smarter about tailings. So, let’s begin by asking you to introduce yourself and share some of your background with our listeners.
Steve: Okay. Right. Well, my name’s Steve Brewer, and I’m a business development manager for Emerson. I cover North American mining. So, I’ve been working with the mining industry for 25 years, and specifically with the Clarkson slurry gate valves and knife gate valve products. I’ve been involved in a variety of roles, regional product sales manager, export sales manager, and, like I said, now business development for North American mining.
Jim: Well, that’s great background for our discussion. Let’s start. Can you give us a brief overview of what tailings are and their role in the mining process?
Steve: Sure. So, tailings are basically a byproduct, or a waste material generated by the mining processes. So, simple way that this would work, miners extract ore from the ground, and they provide that ore to the mill. The mill goes through the processes of extracting the metals or minerals that they want, and everything left over is waste product, or tailings. And that tailings has to be moved or transported from the mill to a tailings storage facility.
The vast majority of the ore going into the mill will end up as waste material. So, for example, a typical copper mine might have a 1% recovery rate, meaning that they’re recovering 1% copper, and 99% of the material that entered the mill will end up in the tailings storage facility.
Jim: Well, that sounds like the majority of everything is this tailings in there. So, why is the management of tailings so critical to both the productivity and sustainability of a mine?
Steve: Right. So, again, you have so much of the material going into the mill that ends up as waste product. If you don’t have a way to dispose of the waste, or if you can’t move the waste from the mill, production stops. So, that’s the first part.
I mean, you have to be able to get rid of the waste material to continue production. Environmentally sound and cost-effective disposal of the waste material is just critical to the operations. It’s something we work on every day, right?
Jim: Yeah. It sounds like, with those percentages of what you’re trying to get and what you need to dispose of, that, yeah, if you’re not doing that right, everything grinds to a halt.
Steve: And nobody likes to stop production.
Jim: Yeah, I know how that goes. So, can you explain the challenges associated with the transportation of tailings through pipelines and the role of valves in the process?
Steve: You bet. So, we’re typically dealing with what we call slurry. So, it’s going to be solids material in a liquid, water in this case. And some of the difficulties, of course, your tailings, you’re going to have water and rocks, dirt, sand, you know, whatever is in that material.
The tailings part of this process, it’s typically high solids content and very abrasive, transported often a long distance from the mill. So, abrasion and erosion resistance is critical for long service life and reduced maintenance intervals of the pipeline and the valves and the pumps. So, maintenance is a really big part of this process for the mills.
Valves themselves provide control or isolation. In our case with Emerson, we’re doing mostly isolation for slurry valves. And valves are typically used for tailings isolation, tank isolation, pipeline isolation, pump isolation.
And, again, it’s critical that these valves last a long time. That’s what customers are always looking for. And so, we designed these valves not only for long service life, but also ease of repairability, because these valves, when you buy a slurry gate valve, you’re buying a capital asset, and, basically, you’re able to repair or rebuild these valves over time because they are going to show wear.
And customers are very aware of this slurry being abrasive. They’re very familiar with the wear issues, with pipelines and pumps and valves, of course. And so, that’s where we come in, providing those valves that are going to provide long service life and reduced maintenance intervals.
Jim: Yeah, that sounds like a really tough kind of fluid going through the pipes, that slurry of it being very abrasive and maybe corrosive and everything else. So, that’s definitely a challenging application. So, how do environmental considerations shape the practices and technologies used in tailings disposal?
Steve: Right. Well, everybody in every industry is very focused on environmental safety anymore, and especially in the mining industry. But for Emerson, you know, we’re always seeking new technology to reduce the negative impact of the mining practices on the environment.
So, recently, Emerson introduced a new line of what we call severe service knife gate valves, designed specifically for very difficult tailings applications, again, abrasion-resistant, erosion-resistant products, and, again, products that can be repaired in the field at the customer site.
So, again, trying to provide that long service life and reduced maintenance intervals, at the same time maintaining environmental safety.
So, one of the things we’ll talk about a little bit later is the two different types of products that we typically provide for tailings isolation, and that is our new severe service valves and our traditional Clarkson sleeve valves, as we call them, push-through valves or slurry gate valves. We’ll talk a little bit about that in just a moment. But we do offer two different products, and, again, the new severe service valves are designed specifically to be a little more environmentally friendly, I would say.
Jim: Well, that’s great, responding to the challenges the mining industry faces. Now, I understand that the International Council of Mining and Metals, ICMM, implemented the global standard on tailings management in 2020. Can you elaborate on what the standard entails?
Steve: You bet. So, the ICMM is a group of mining companies that got together, trying to create and drive an industry standard to protect the environment, human safety, and all of this kind of revolves around reducing tailings production. I mean, their idea is to reduce tailings and, eventually, eliminate tailings all together. We have a lot of work to do before we get there.
But this basic drive is going to improve tailings management design, and that is tailing storage facilities, you know, all the way from the, you know, the civil work and also the pipelines and transportation of the tailings themselves.
But there’s a lot that goes into this. You know, we’re trying to reduce the environmental footprint and help companies be more environmentally sound. A lot of what they’re trying to do, like I said, where they’re trying to reduce or eliminate tailings, and they start by looking at the ore.
And so, they talk about precision geology, for example, and precision mining and precision segregation. So, the precision geology, for example, is trying to identify not only where a particular mineral is, but how do we find, or locate, or identify the higher-grade ores, because the higher-grade ore, you know, the more product you’re going to be able to recover, and, obviously, lowers the amount of tailings you generate.
The mining part, precision mining, if we can extract ore that is effective, not extracting the waste part of the ore in the first place, that doesn’t have to go to the mill, that, too, reduces your tailings.
And then the other part is segregation ore recovery. You know, the more mineral we can recover from the ore, the less tailings you’re going to have. So, like I said, it’s just one of those things that they’re trying to do a lot, and a lot of this revolves around reducing tailings all together.
Jim: Yeah. And I can just imagine that, you know, it’s not just reducing the tailings, but just increase energy efficiency, less digging for that ore, if you’re more precise somewhere to get it. And then, on the processing side, all that energy that’s in the processing side. So, yeah, that’s driving sustainability to much higher levels.
So what are the key design changes in new tailings parameters?
Steve: Well, right off the bat, you know, one of the, again, we’re very focused on the recovery of the mineral we’re looking for and obviously generating less waste. That’s good. But we also try to recover as much water out of the process as we can. And when you recover, or when you reclaim more and more water from what would be your tailings, the more water you reclaim, the higher the solids content of the tailings media becomes.
So, we used to see tailings at about 45% solids, and then 55% solids. And now we see tailings applications up to 65% solids just by reducing the amount of water in the tailings. That’s a big part of it.
We also talk about liquor recovery or efficiency. You know, we’re more trying to be more efficient in recovering the mineral we want, but again, reducing water, not only in the process and in tailings, but reductions in water evaporation or groundwater seepage, because the less water you send to tailings, the less water there is for evaporation, for example.
Also, we’re looking at changes in the tailing storage facility and the pipeline. So one of the things we see is that, over time, we’re moving tailings further and further away from the mill to basically dispose of that waste material. But where they’re basically dumping or placing that material into a tailing storage facility, we’re adding more, what we call, spigot lines.
So you’ll have a long tailings line moving towards the tailing storage facility, but you have discharge spigots where you’re dumping that material into the tailing storage, right? And you want to, in this new system, have more spigots, so you’re discharging more material across this tailing storage facility. Basically, a more even distribution of material, which is, again, good for the environment, good for human safety, just overall better practices for tailings.
Jim: Well, that makes sense. And again, it seems like driving greater efficiencies there. Now, I know that valves are critical components in any tailings management system. What does the standard mean for valves?
Steve: Well, right off the bat, I mean, we’re processing more solids at higher pressures and higher velocities. And again, these valves, you know, we use these in abrasive erosive process media. So we know we’re anticipating wear, with not only the valves, but pumps and piping, and pretty much everything involved. But we’re basically increasing the solids content that sometimes requires higher pressure and higher velocity to push that media down the pipeline.
We’re also looking at customers wanting longer lifecycles and reduced maintenance intervals. So, basically, they’re increasing the wear rates, if you will, and asking for longer service life.
So that, for valve manufacturers, that means that we have to really step up and provide better and better product as we go on with this new innovation. You know, not just for the tailings systems themselves, but for the individual components in the process.
So things we work on, longer lifecycles for our products. Again, ease of field repairability for our products is really important.
And also, you get, like I said, the turbulent flows. You get higher pressures, higher velocities, but we need to maintain somewhat of a turbulent flow to keep the solid suspension in the pipeline. Anytime you have solids and water in a pipeline and you’re moving it, you don’t want the solids to settle to the bottom of the pipeline. So you have to maintain a certain velocity through the pipeline for that.
And then, the other thing for valves, we offer two different types of products. The original Clarkson slurry gate valves, or push-through valves, that we introduced almost 50 years ago. And then, our newer severe service valves, which are designed for the same exact applications, just a little bit different in how they operate.
Last, I mentioned this before, but there are more valves required in the typical system now, as we add spigots for discharging waste material into the tailing storage facility. So again, increased piping layout, longer pipelines, higher pressures, there’s a lot that goes into it for valves in general.
Jim: Yeah. Given all these challenges that you just described there, what innovations in technological advancements are being made in tailings valve designs to address these challenges?
Steve: Right. So, as I mentioned, we developed and recently introduced a new line of severe service valves. So, severe service knife gate valves are designed, like I said, for high solids content, abrasive slurries like tailings. And these valves are typically higher-pressure valves.
So these valves are rated for ANSI class 150, class 300, and class 600 for Emerson. And these are kind of a departure from the original valves we developed almost 50 years ago, the Clarkson slurry gate valves. The slurry gate valves are what we call a push-through or discharging-style valve. And so, these valves are designed for, you know, the most, I guess, arduous slurry applications we have. But these valves are designed to self-purge or self-clean when they cycle. So when they do cycle, they discharge a small amount of process media onto the ground.
So, if these valves are located in the tailing storage facility or near a tailings thickener, that’s typically not going to be a big problem. But you have other areas where, in these longer pipelines, for example, that you might have transportation of slurry across environmentally sensitive areas, and there, you would not want a discharging valve.
So that’s the new innovation, and the reason, one of the reasons, anyway, for the new severe service valves. And again, these higher-pressure valves, severe service valves, are rated for ANSI class 150, ANSI class 300, and 600, whereas the original Clarkson valves, when we developed those back in 1977, we designed those valves for low-pressure tailing systems at basically 100 PSI cold working pressure. You know, they’re not an ANSI class-rated valve.
So we had the original Clarkson valves, we had those designed for 100 PSI, and then we moved that up to 200 PSI, and then 300 PSI. But we are seeing more and more high-pressure applications and a combination of both discharging and non-discharging valves.
Jim: Yeah, it sounds like, one, you had to design for those higher pressures to deal with some of those challenges. And given the fact that it may cross environmentally sensitive areas, to have them be non-discharging. So those are some great innovations there.
Steve: And again, as the, you know, this new standard for these tailing storage facilities, we’re seeing, you know, tailing storage moving further and further away from the mill. And when we do that, we need higher pressures to push that tailings media further away from the mill. And that’s one of the reasons for the higher pressures. But again, going from the mid-’70s to today, we’re seeing, you know, a great increase in pressures to move that tailings media.
Jim: Well, that’s great news that our technologies have kept up with what’s required by the industry there. So, what advice would you offer to mining companies looking to improve their tailings management systems?
Steve: You know, the first thing, we do travel around, and we go to the mine sites and offer, you know, maintenance training, for example. And we do these maintenance training events at mines all over the place.
But one of the things I always start with is proper installation of valves, and this could be a new system, a new installation entirely, or, you know, replacement valves over time. But I always say that the first thing you want to do is make sure you install the valve correctly, as noted in the manufacturer’s instruction manuals.
And the reason for that, if you install the valve correctly, you’re going to get the longest service life. You’re going to get the best wear out of your wear components and the valves, and you’re going to reduce your maintenance intervals. So, you know, for maintenance training, I always tell them, install the valves correctly in the first place. They will last longer. And that’s kind of the whole point of this.
Other than that, you can maintain the valves per the manufacturer’s standards, and also, we recommend they use OEM, you know, normal OEM parts. We do run into, you know, pumps and valves run into this, that there are people that make non-OEM parts, and sometimes they work well, sometimes they’re maybe not up to par, but we do recommend following the manufacturer’s recommendations for maintaining the product and using those parts.
And then train your people, and this is part of the training, but train your people to help them learn how to extend the life and reduce maintenance intervals.
The other thing is, and I’ve mentioned this already, but we do manufacture a combination of slurry gate valves, which are what we call discharging valves, and severe service valves, which are non-discharging. And we do manufacture both, so we can offer a combination of those to best fit the applications required.
Jim: Yeah, it seems like if you’re in the tailings area already, discharging valves are fine. So, having both those work. And I think that’s real important given that if the valve fails and you’re using non-OEM parts, you know, you’re basically stopping mining operations, which is not what you want and is quite costly in that case.
Steve: Yeah, using non-OEM parts does not help extend the lifecycle and definitely doesn’t reduce maintenance intervals. So, just a basic recommendation from us.
Jim: Yeah. And finally, if listeners want to learn more about this subject or implement best practices, where can they find more information?
Steve: Well, I believe we’ll have some information in the show notes below that the customer can look at. But we also have a number of helpful resources on the Emerson website, Emerson.com. We do have, you know, product data sheets. We have drawings, instruction manuals, a lot of other information. We also have some toolkits that we can make available to people working with our products that help with the selection of valves and application of valves, and also sourcing product.
Jim: And you’re absolutely right. I’ll add hyperlinks to where we discuss some of the different things throughout the transcript here and make it easy for people to get to the right area of Emerson.com to learn more.
Steve: Got it. And then, of course, if you have any questions or immediate needs, reach out to your local Emerson representative, and we can get you in contact with the people, whether it’s tailings or application in the mill, or pretty much anything mining-related. We should have somebody to help.
Jim: Well, that’s great. Steve, I want to thank you so much for joining me today and sharing your expertise with our listeners.
Steve: Yeah, thank you for hosting, Jim. I do appreciate the opportunity.
-End of transcript-