Emerson Automation Experts
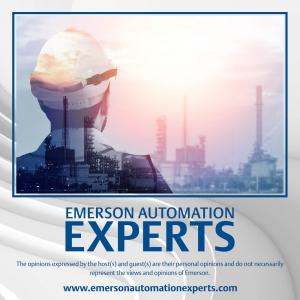
Boosting Efficiency and Safety: The Power of Digitalization in Greenfield LNG Projects Podcast
The liquefied natural gas industry is active in building new greenfield facilities. These new facilities have the opportunity to take advantage of technological advances in automation and the digitalization of work processes. Valves, actuators, and regulators play a crucial role in this challenging cryogenic process’s overall safety, efficiency, and reliability.
In this podcast, Emerson’s Riyaz Ali and Tom Mullins share the story of an LNG producer and how they applied digitalization in their project design and installation to deliver integrated solutions to improve the project schedule and ongoing operational performance. Digitalization enables predictive maintenance practices to avoid unplanned downtime and optimize maintenance budgets.
Give the podcast a listen and visit the Valves, Actuators and Regulators for the Entire LNG Value Chain section on Emerson.com for more information on the broadest portfolio of valves, actuators, and regulators with critical isolation and control technologies.
Also, visit the LNG Success Podcast page to listen to other podcasts in this series.
TranscriptJim: Hi, everyone. I’m Jim Cahill with another “Emerson Automation Experts” podcast. Today we’re on another episode in our four-part series that explores the role of control technologies in helping drive efficient and reliable LNG production. Emerson’s valves, regulators, and actuators empower the entire LNG value chain, from the liquefaction process to transport and terminals, and from project startup and commissioning to long-term facility operations and maintenance. Today we’re talking about digitalization, enhanced efficiency, and safety in an LNG project. And we’ll look at the very compelling customer success story. Our guests today are Riyaz Ali and Tom Mullins from Emerson. Riyaz is a senior director for FIELDVUE Business Development and a subject matter expert for Digital Solutions for Basic Process Control Systems and Safety Instrumented Systems. Tom is the director of Projects and Strategic Accounts with Emerson’s Actuation Technologies business. Welcome, gentlemen.
Tom: Hey, Jim. Good to be here.
Riyaz: Thank you, Jim. Pleasure to be here.
Jim: Well, it’s great having you both with us. So, Tom, I’m going to pick on you to start with. Can you give us an overview of how digitalization is transforming the LNG industry? I guess particularly in Greenfield projects, what role does it play in enhancing efficiency and safety, for example?
Tom: Sure, Jim. Today we’re going to be talking more about isolation valves and actuation on top of those valves. And specifically to that point, over the last 10 to 15 years, what’s really changed is our customers are starting to ask for more stringent closure times and opening times around these big valves. That’s derived from the safety instrument loop there that’s being required. So every data sheet now has a specific safe closure time. And now every actuator on every valve needs to meet, or exceed, or do better than what that time is. So 15 years ago, you didn’t see closing times on every valve actuator assembly or data sheet. Now you do. So with that and the use of some of our equipment, like the DVC SIS we’re going to talk about today, we’re able to not only meet and exceed the closing times but also track the fact that the customer, you know, met those times, which is very important to test the safety instrument loop. So that’s some of the ways we’re starting to see just simple on/off valve actuation now gets much more complicated, but not only complicated, the ability to track with our equipment on top.
Jim: Oh, that’s interesting about how that’s changing in that way. So, Riyaz, we said we want to talk about a particular success story here. Can you give us a little more information about the customer?
Riyaz: It’s a Greenfield Energy project. It’s in North America. It has got two liquefaction trains, two storage tanks, and associated facilities.
Jim: Oh, okay. So that’s a pretty good-sized facility. So given their setup and what they had, what were some of the main customer challenges that they faced?
Riyaz: As we know that the plant has got a lot of on/off assets and those assets traditionally are non-communicating and the customer are really facing issues because it cannot be integrated closely with the control whole system. Second thing, they would like to have the digitalization diagnostic because the field diagnostic is very key. Like, all we see right now and currently all the digitalization impacts on our regular life, how the digitalization is making those differences. And similarly, they would like to have those kind of information coming out with the field assets directly to the control system to make the operation easy, quick action by button and the better decision-making for them to get the plant highest availability.
Jim: Okay. So one of those challenges was the lack of visibility for on/off valves in traditional systems. So how did digitalization help solve this issue in this particular Greenfield LNG project?
Riyaz: Yeah, as these devices earlier were non-communicating type, with the digitalization, what we need to, the customer, what they want to manage now is not only the on/off valve body and actuator, plus the associated instrumentation. Now traditionally, the on/off valve and actuators are mechanical item, so they need to have a special skill set for the instrumentation. So their challenges right now is how do we manage multiple vendors with valve body, actuator, accessories, instrumentation and have the skill set so that the package is completely integrated perfectly with the seamless functioning of all the objective they would like to gain through the digitalization. Plus, they would like to standardize and make sure that the plant is uniformly working across all the units with the same kind of instrumentation, same kind of pneumatic schematics, and they get full benefits out of these field assets.
One more problem came out was the expertise in the instrumentation required a lot of setting of the parameters and other stuff. And the challenge was how do we make all those things where they can copy-paste all those configuration and parameters across the plant. And the biggest requirement was that how do we get this whole complete integrated package with one reliability assessment report. It means that whosoever supplies me the components of the valve body, actuator, everything, we need to have one complete reliability assessment report coming for the whole final element. And at the same time, they would like to meet the project specs, which means if there is certain guidelines with the project required, is there any way then when they hand over the plan, can they have a kind of a performance certificate for the whole element and single source, single component, single reliability, single guarantee? So that is how they are looking one point of contact with expertise for the whole package.
Jim: Yeah, it sounds like that standardization of it was very important, and that single source that you mentioned there at the end, very important to this project. I guess diving a little bit into the technology, what was the impact of the digital valve controllers, the Fisher FIELDVUE DVC6200? Can you explain how their predictive capabilities contributed to the plant’s operational efficiency and safety?
Riyaz: Absolutely. The DVC6200 digital valve controller is exactly like what you have your iPhone, and handheld, and other stuff, where you have your visibility of the information 24/7. And that’s what the digitalization for the field asset is offered through the DVC. The information which you can get from the movement of the valve, every time the valve moves, anything goes, movement into the control valve, or safety valves, or on a valve, the digital valve controllers are completely alive and provide all this information. At the same time, you are able to now get the diagnostic of the device online by reducing the maintenance budget, because everything online through the operating screen can be known, and at the same time it will reduce the field trips because now the operator have more better visibility and then decision power has been given.
So before the valve trips, the operator has a better decision power to make whatever the necessary correction or adjustment to make the plant availability highest. And one of the major achievement of digitalization is the mechanical X-ray of the valve, which means which particular part of the valve is having a problem. It’s a part in the mechanical movement in the plug side, in the actual size, in the shaft area, in the instrumentation area, in the pneumatic area or supply area. So it is very clear X-ray which will provide you pinpoint where exactly is the problem. That makes easier to keep the things running into a plant availability rather than taking the valve out of the line for finding out where exactly problem is, taking it to the workshop, opening the valve, checking each and every component, and then determining where exactly is the fault. So this particular mechanical X-ray is a great added help for the digitalization of these on/off assets.
Jim: Yeah, that seems really critical because a cryogenic process is such a difficult process and the valves really have to take a lot of that. So having that digitalization to really know what’s going on inside them is, yeah, that seems just critical. Well, Tom, let me turn to you. I guess with valves often in a static or dormant state, what specific performance issues do these digital controllers help monitor and how does that enhance overall reliability?
Tom: Yeah, I think for the most part, the hardest service for an on/off valve is I’ll call it the sitting service, right? Where the valve actually stays in the fully open position, the spring’s compressed in the actuator for a long period of time. And this is most of these valves, right? Most valves in an on/off service don’t stroke very often. That can be the hardest service, right? You have the actuator that’s been sitting in one position. You’ve had the valve sitting in one position for a long period of time. And what the customer is trying to determine, is it going to work when we trip, right? When something bad happens, is this valve gonna close? What these smart devices do, the DVC6200, is it allows you to perform a partial stroke test easily and on a schedule and it won’t stroke the whole way. It strokes 15%, let’s say. During that process, it allows you to give diagnostics on was it the timing to go from fully open to this 15%.
Did it take longer than it should have, right? We’ll tell the device, hey, this should take 25 seconds. And if it takes 40 seconds, we’ll make some determinations. Hey, this is not performing the right way. So the fact that these online devices now can give you, like Riyaz said, the ability to use some preventative maintenance. I see a problem. It’s still closed. Just not the right period of time. Let’s go check it out. So those are some of the things. But that is the hardest part is the dormant state. We’ve used this device on control valves for many, many years, right, with a lot of success. But that service is a lot easier when things are just moving all the time. You know, we kind of know that it’s working. So that’s the big point. The static state build up in the valve. You could have, you know, seizing in bearings. You could have a build-up of process inside of the valves that could cause the valve to not work right.
Jim: Yeah, I know. If I sit here at the desk too long, I can get being static for too long. Isn’t too good for me either. So I can appreciate that. So having a single supplier for the valve operating system or VOS is a key factor. So how does this streamline safety, reliability, and the maintenance processes?
Tom: Yeah, that’s the same thing, right? Emerson’s in a unique position in the fact that we have valve actuators and the control device. But as Riyaz mentioned before, these devices require some higher level of instrument engineers and instrument techs to understand how they work. So in the end of the day, if you order from Emerson with Emerson equipment, it goes to ultimately the actuator manufacturing location. A Bettis or Biffi location would take the 6200 DVC, mount it to the actuator, perform the test, upload how you want the device actually set, okay, with software, and then ultimately ship to where the valve’s done or, and this really adds. I mean, for example, Riyaz and I just were on a phone call this morning with a customer about the fact that, hey, we want to make sure all the HART tags are on every DVC so that when you crank up your control system, it automatically reads the fact that that’s the right tag. Those are the simple things we do with an Emerson actuation package with the DVC6200 that are simple to us because we have a process. So it allows it very simple to be able to integrate to be able to commission very simply is set up properly when it gets to the field. So those are just a few of the ways that that one package helps.
Jim: Yeah, that sounds like that that just will simplify the process once it gets there on site, all that work that’s been done in advance. So that’s, yeah, I think a real big benefit right there. Riyaz, let me turn to you. So what role did proper valve assembly configuration and instrumentation play in reducing commissioning time and accelerating the plant startup?
Riyaz: Absolutely. Since the digitalization word itself has been given and it’s playing important role right now in not only your home front or day-to-day life, but the same expectation has been set by end user that when they get these kind of devices, can it reduce their workload? Can the smart digital instrumentation can do remote configuration and calibration? Can it do copy and paste the configuration from one device to other device saving them considerable time during the startup of the plant? Can the auto set of wizard allows easy calibration and make the process intuitive. At the same time, as earlier Thomas mentioned that these digitalization can allow you to run a concurrent batch, which means that you just give a one command and a batch of complete set of valves with the digital solution mounted on them can do an auto-calibration, all those kind of diagnostic, the valve signature test, everything in one click of start. It means the 15 or 20 valves which is being combined in one batch to do this job simultaneously each valve is doing on its own rather than doing one by one valve saving a considerable time for the commissioning as well as bringing the plant startup quickly much more than waiting for so long to go through each and every individual items.
Jim: Wow, that sounds like being able to batch it would really accelerate that whole process. That’s really good. How do the microprocessor-based digital controllers provide predictive maintenance capabilities? Can you share any specific examples of how this prevents equipment failures and reduces downtime?
Riyaz: Yeah, I’ll just provide one example and then certainly Tom can provide you. Since these digital valve controller has got inbuilt travel, pressure, velocity, and all those sensors which provides a predictive capability for the complete valve assembly. So I’ll give you an example. One of the refinery had a critical 24-inch size ball valve for safety application and that mandated them to check the integrity of the mechanical movement of that particular valve. So the customer was using a traditional approach which was recording the valve travel to check the rotary motion of the actuator. Now this traditional approach because these valves are rotary lying horizontally the output shaft has got an indicator and that’s how the customer concluded that the valve is mechanically moving. But all of a sudden an accident occurred and what they found that valve did not close during the safety demand.
The reason being what happened that the output shaft was moving but the plug shaft integral to the output shaft was not connected. So that’s how they came back to us and this is, is digital valve controller smart enough or does it have a sensor which can provide a friction value or the torque value. If the output shaft and inbuilt shafts are not connected the torque value will be very small. So for a mechanical valve the yardstick of the health indication is a friction or torque and that’s how the diagnostic algorithm within the digital valve controller can provide easy description and the statement and the cause of the problem and what is a possible solution to act while the valve is still in operation. So all these tests, what we have been doing for critical valves are online in service and having identified right corrective action by digital valve controller it can avoid any unnecessary valve trips, at the same time, it can increase the plant uptime and make the reduced maintenance costs and saving a lot of man hours.
Tom: Yeah, absolutely, Riyaz. I mean, there’s another example in an LNG facility that we just went through with a customer and they had some 72-inch valves. Jim, these are big valves, which means the big, that means they’re huge actuators, but they were not getting the performance they wanted out of our competitor’s actuator. Okay? And ultimately, the first step they did was actually buy the DVCs, put them on the valve to look at the performance. Once they saw that they weren’t getting the performance out of those valves, they said, “Hey, well, what’s going on?” So we helped them start to troubleshoot based off of what came out of the ValveLink software and determine that really the valve operating system, which is the things on top of the actuator that make the pneumatic actuator go, you know, that’s solenoids, boosters, and time.
We determined A, number one, they don’t have enough air, right, a couple of different things, and ultimately they ended up replacing the actuation assemblies in the valves. Ultimately, say, “Look, this is such critical nature. Here’s what we got to do. We had our engineers look at it.” But it all went back to the fact we had the diagnostics to say we know it’s not performing and here’s why. Yeah, it took people with some knowledge to take a look at that, right? But the reality is once you print that out and send it to the right people at Emerson, we can look at it and probably tell you here’s why you’re not getting what you want out of the valve.
Jim: Yeah, without those, you know, diagnostics to be able, it just seems like even trying to troubleshoot it, find it, you’re just shrinking the time, especially as you say, you get it in the hands of someone that really understands the diagnostics and can pinpoint the things that need to be done. Well, those are great examples. I guess, Riyaz, in terms of plant safety, how does continuous monitoring of on/off mechanical valves enhance the ability to respond to potential issues as they escalate?
Riyaz: Yes, digital valve controller, as I said, it’s a communicating device and it’s continuously monitoring. So immediate attention is drawn to the operator should anything deviate from the normal operating condition. So that’s one of the biggest takeaway. The second thing, these valves, on/off valves, and specifically if these are on critical app safety application, because of the dormant state and because of the process build-up because that is one of the biggest concern for the customer whether these valves will be available during the immediate need when a safety demand occurs. So for that, we have already partial stroke test which assures that valve will be available should a safety demand occurs.
So you can see there is a small movement of valve but there is a big leap in the safety of the complete safety instrument function loop. But at the same time, the partial stroke test, once you have conducted, it will provide you the capability to store and compare in future. So now suppose if there is any deviation from the normal state of providing any…if there is a deviation from the normal state of valve operating condition it will provide a big clue for maintenance team for corrective action before the safety event occurs. So that can improve your plant safety considerably, plant safety & reliability.
Jim: Okay, and Tom, what can you tell us about the actuators involved in the project? I know we touched on them briefly here. How did they harmonize with the Fisher digital valve controllers?
Tom: Yeah. I kind of mentioned this earlier, Jim, but Emerson’s on/off actuation brands are primarily Bettis and Biffi for this space. These are 50, 60-year-old products that have been in the market for a long time, and we’ve sold hundreds of millions of dollars of actuators in the LNG space. You know, it’s one of our largest markets. But the reality is as we’ve done this over that period, the last 30 years or 40 years of selling into LNG, we’ve gotten that much better of integrating the stuff on top of the actuator which includes the DVC. So, when you buy an Emerson actuator from Bettis or Biffi and say, “Hey, I want this integrated with the DVC6200 SIS,” we have a plan, we have a strategy to… And we know exactly what we’re doing when we mount these all together.
Jim: Yeah, putting the whole integrated space especially in that for a safety instrument function, it just seems such a critical thing to do just to make sure it’s all in there and you’re getting the right diagnostics that you need out of them. So I guess turning a little bit to, you know, the costs and labor efficiency, remote commissioning and access are mentioned as benefits of digitalization. How do these features reduce labor costs and improve operational efficiency for an LNG plant?
Riyaz: Certainly, Jim, as you know, the digitalization, the expectation of the customer is to reduce the workload whether it’s the home front or whether we are doing on our day-to-day process, or any manufacturing process, or any plus, wherever you are bringing the digitalization, the purpose is to reduce not only the work documentation, not only the time plus the manpower plus at the same time can these kind of things copy-paste for the multiple operations. So, configuration template is one of the biggest takeaway from the digital valve controller, which allows you to completely take the same configuration and make it for the same, for other valves, reducing time and man hours.
At the same time, digital valve controllers can store the complete specification sheet for future reference and that will be stored in the non-volatile memory of the microprocessor that can reduce the documentation and improve the plant efficiency. Meeting the project space complies because all the Greenfield project, they have certain compliance, so when you hand over the plant, the digital valve controller signature provides as a benchmark for the mechanical performance of that complete assembly with a graph and assurance report for the plant making plant commissioning faster through the…make the plant start up quickly. And as we already discussed, the auto-calibration, the auto-scheduling, all those kind of thing can reduce considerable time and at the same time, provide efficiency and more time for more other fruitful work in the plant.
Jim: Yeah, it sounds like if you can really automate, bring that data together and you free up time to do more valuable activities than some of that.
Riyaz: Okay, the biggest takeaway is taking away the human error because by digitalization, you’re removing the human error and that is one of biggest takeaway for digitalization by elimination of the need of technicians. We are not trying to completely eliminate, but we are trying to make sure the technician is allowed during that time to do other major work of the plant startup.
Jim: Yeah, that’s a really important point. Human error can be, you know, a large part of the bad things that happen in there, so whatever you can do to reduce that that’s a great thing. I guess looking ahead, what do you see as the next steps for digitalization in LNG projects, and how might emerging technologies further enhance efficiency, safety, and reliability?
Riyaz: So digitalization offers us mechanical on/off asset which is one of the biggest plant asset in any operating plan, the digitalization is just a baby step towards future automation technology moving towards data mining. So with future, the customer or end users would like to have some kind of mechanism where all these data can be utilized through some kind of machine learning or some kind of a program which can allow them to predict or prognostic of the life of the mechanical item by crunching the data through the defined algorithm and retune it mechanic, make it more better, recalibrate for the prediction purpose. And that way, they can accurately determine what is the mechanical SIS life and that how the robot’s artificial intelligence, all those kind of thing is anticipated in their minds.
So in the future, the customer would like to have only one of physical body in the field whereas all the work should be done by artificial intelligence, machine learning, and everything. And if there is any problem, it commands will be sent either robots or human being can go and just replace without any expertise required in the field. And at the same time, it makes sense to digitalize one of the largest field assets which is on a valve to take advantages of upcoming developments in the robotics AI driven technology for the increased efficiency and improved product quality as well as plant uptime and safety reliability.
Jim: Yeah, it seems like turning AI loose on all this data created in there to be able to really pinpoint problems and send out the people, or the robots, or whatever we’re going to have there in the future, that’s an exciting future. So let’s wind it all down, and maybe can you all share some of the key takeaways for our listeners from what we’ve talked about today?
Tom: Yeah, I think I could do that, Jim, I mean, me and Riyaz. But I mean, I think the summary is, like I said, these smart devices, they’re here and coming, right? You’re going to see more and more of them. And you know, as we begin to track the health of these valves, and as Riyaz says, if you have one versus now you’ve got 1000, you can really start to pinpoint what the difference is between the 2. And so that’s kind of what I see. The key takeaway is when you work with Emerson, it’s going to be a fully integrated package, right, and it’s going to make it much easier to commission and we’re going to help the end user get really what they want out of the project. So, and that starts with communicating and talking up front and getting, you know, and understanding the requirements and what they want out of it.
Riyaz: So digitalization, as Tom said, is becoming as a need rather than a choice. And each automation industries are looking for streamlining the process whether it’s installation, commissioning, documentation, compliance to the project specs, certification, auditing, and storage of data. So you can name any of those kind of an activity, they just would like to have a click of button to reduce the cost and manpower using the digital power of the microprocessor-based smart instrumentation. And at the same time, the digitalization reduces maintenance cost, increases plant productivity, and it has got less load on the workforce, and at the same time better future integration to the developments in the technology as the technology is moving exponentially in microprocessor.
And these kind of technology movement, they have to start having them now on the ground so in the future it will be easily upgraded or it can be easily migrated to the new ways how the digitalization takes shape. And as Tom said, the one integrated package from the complete Emerson digital solution can solve multiple angles of project including the reduced procurement cost because now you have one vendor versus multiple vendors to coordinate, there will be only single certificate for the complete assembly. And then there’s a one vendor to contact for future any support, and the biggest thing is a single warranty certificate for the whole product.
Jim: Yeah, I don’t think we can stress that enough that integrated from the valve through the actuator to the digital valve controller, riding on top, making sure it’s all working seamlessly and providing the diagnostics for it running over time, that’s a really critical point there. And for listeners, you can go to Emerson’s LNG Valve Solutions page, and that’s at Emerson.com/LNGvalves, and we’ll add some hyperlinks into the transcript that we put with the post. Well, Riyaz and Tom, I want to thank you both so much for spending some time with us and sharing your expertise with our listeners. Thank you.
Tom: Thanks, Jim, enjoyed it.
Riyaz: Thank you, Jim, and you’re very welcome. Appreciate taking us through the journey of digitalization and LNG specifically for the on/off assets.
-End of transcript-