The Turf Zone Podcast
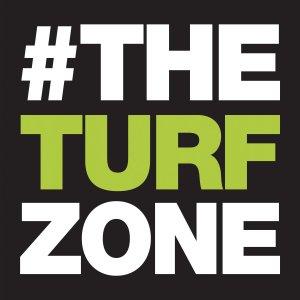
Alabama Turfgrass Association – “Looking To the Future – Where Will the Turfgrass Industry Be in Ten Years” Equipment and Technology of the Future PART 3
Battery Powered Equipment
One of the most dynamic features of new turfgrass equipment of the future involves battery power. This part of the market is moving at lightning speed. There are several reasons for this move toward battery powered equipment and away from conventional gas and diesel. Legislation in several states and municipalities are phasing out the use and in some instances the sale of new gas-powered lawn equipment. California’s governor signed a bill to phase out the sale of all new gas-powered lawn equipment in that state by 2024. These new laws cite the need for reducing air and noise pollution. Many subdivisions, nursing homes, hospitals, and schools here in Alabama have restrictions on noise pollution during certain hours of the day and days of the week. Seeing these trends, some companies have decided this is the wave of the future that they want to ride. As an example, in its Sustainability Report for fiscal 2021, The Toro Company stated that one of its goals was to increase battery and hybrid product sales to at least 20% of total adjusted net sales (motorized product sales) by fiscal 2025.
Even though battery powered equipment offers reduced noise and environmental impact, the initial purchase price as compared to its gas/diesel counterparts could turn some buyers away. However, there are other considerations that turfgrass managers should consider that might cause them to take a second look at battery power equipment. The newer batteries are lighter, more powerful, longer lasting, and charge faster; and the technology is only getting better each year. Battery powered equipment now covers the full spectrum of maintenance equipment including mowers, blowers, weedeaters, pruners, chainsaws and more. Many times, the equipment is built on the same frames as the gas/diesel models, so they are just as tough and then there’s the reduced operational and time saving feature of reduced maintenance costs. Some say that operational costs for battery powered equipment could be 35% less than conventional gas/diesel powered equipment. Remember, the batteries are powering electric motors turning wheels, operating steering, and driving the blades or other attachments. There’s no fuel, oil, belts, or filters; and no coolant or hydraulic fluid on the bigger equipment.
Another area of research to watch involves the type of new batteries being developed. Currently, most batteries being used across all industries, including the turfgrass industry, are Lithium ion (Li-ion). However, the next generation of batteries being developed include:
- Lithium-sulfur (Li-s) – have up to 3 times the energy density of Li-ion
- Sodium – larger than Li-ion batteries but cheaper to produce
- Lithium- air (Li-air) – hold over 40 times the charge of Li-ion batteries. These batteries are still quite some time from being ready for mass production.
Also, Hydrogen Fuel Cells are getting a look for small equipment. So, what is a hydrogen fuel cell? In the simplest terms, a hydrogen fuel cell combines hydrogen and oxygen to produce heat, electricity, and water – they are very similar to a battery, but they can keep producing power as long as hydrogen is supplied. Tech companies are reportedly already experimenting with hydrogen fuel cell powered mowers, so expect to see these in the next decade.
- Solar Power panels are currently available to charge Lithium batteries, but as a power source to power commercial equipment, it’s not there yet. However, solar panels supplying electrical power to charging stations has real possibilities. Many in the turf industry will have crews working away from a convenient power source to recharge their equipment. This poses a new challenge/opportunity for innovation. Battery-recharging setups will be a focus in the future, especially as more landscape companies opt for electric equipment.
Stihl has debuted a prototype cabinet in a standard trailer with multiple charging units for repowering equipment on the go. At some point, don’t be surprised to see more box trailers and trucks with solar panels on roofs and sides, supplying power to their mobile charging station. As manufactures of battery equipment continue to improve the efficiency while working toward keeping the purchase price competitive, it looks like the future of battery powered equipment will “charge forward.”
Mowers
Without question the number one category of turfgrass equipment is the mower; after all, it was the first mechanical piece of lawn equipment invented due to the overwhelming need. Manufacturers continue to meet that need by providing a range of rugged, strong, dependable equipment for the turfgrass industry. In recent years, we have seen vast improvement in maneuverability of mowers, especially with the bigger units. Today, many of the improvements made in the design of mowers involve the use of new technology to make mowing even more efficient, faster, and safer. Two of the biggest mower advancements that technology is providing today involve steering and power source.
Steering options, such as Autonomous, Autosteer and Remote Control have arrived on the scene just as the turfgrass industry has seen a reduction in the workforce and skilled labor willing to work agricultural related jobs. These new steering options can help attract and retain new employees, while improving productivity and quality of work. However, the terminology around these steering options is sometimes misused and can be confusing, even in some advertising. As Dr. McCall stated, “There is a lot of overlap in terminology of steering options, so most people aren’t alone in not being completely clear about differentiating between the different options.” The following statements explain the difference in terminology.
Autonomous mowers can be considered robotic mowers. They are programmed by humans to perform the necessary functions of mowing by following a programmed set of instructions, under defined conditions, without a human driver. The program establishes the mowing route, sets the boundaries, and in some cases, the start times. Once the initial programming has taken place, the equipment’s internal computer does everything from there, totally unassisted and driverless. Autonomous mowers have built-in detection sensors that ensure obstacle avoidance. It can make decisions based on sensor input, technically allowing the mower to have “a mind of its own,” without human direction or guidance.
Autosteer (AS) equipped mowers are operated with a human in the driver’s seat; they engage the AS feature when needed. This technology relies heavily on GPS to know where the unit is and where it needs to go when engaged. To begin the process, the operator will program the initial pass, either straight and/or curved, and once AS is engaged, the equipment will make parallel lines off the first pass until programmed differently. Autosteer equipment will travel the predetermined path, hands-free with a level of accuracy that was impossible to reach before. It reduces overlap and missed areas, saves time and fuel, reduces operator fatigue and increases production and quality. Some of the older AS equipment still require manual functions, such as turning around for a new pass or getting from the shop to the fairway or field, etc.; newer versions can make pass turn-arounds on their own.
Remote Control mowers operate without a human in the driver’s seating; instead, a person standing at a safe distance away operates the equipment using a wireless, hand-held remote-control device. The equipment isn’t moving autonomously. Rather, the real-time maneuvering is controlled by the human operator watching the unit mow within line-of-sight distance or further away by viewing a monitor that can be attached to the remote control. A live video from the mower mounted camera is fed to the monitor, giving the operator a view of what the mower is seeing in real-time.
Remote Control steering has been possible for many years in a variety of industries, but it is especially functional when maintaining turfgrass and vegetation on steep banks. Depending on the slope, mowing banks has always been a very hazardous operation, but today, remotely operated mowers are making this task much safer. Take for instance the slope mowers offered by RC Mowers that were discussed in Part 1 of this article. Their mowers are equipped to maintain slopes up to 50°, remotely by the operator hundreds of feet away. This clearly places the operator out of harm’s way of the many dangers that could be encountered. Their remote-controlled mowers with track systems are also capable of mowing in several inches of water in low, boggy areas, or along the edges of ponds. RC Mowers have plans to develop an autonomous slope mower in the future.
Autosteer has been used for almost 25 years in row crop agriculture. It has been used on tractors to till, plant, fertilize, spray and harvest very efficiently. This technology has reached the turfgrass industry and is seen on sprayers, spreaders, and more recently, mowers. John Deere offers Autosteer on sprayers and mowers, providing users with increased productivity and efficiency. Cub Cadet offers a zero-turn mower with Autosteer that consistently mows straight lines and can make turns without operator assistance. Autosteer technology on mowers delivers many advantages such as less operator fatigue; more precise and consistent cut with less overlap; prevents gaps and missed areas; all while reducing the inputs of time, labor and fuel. Autosteer mowers cut more grass per hour, more acres per day and complete more work each week.
Autonomous equipment has been under development for years in agriculture, with several manufacturers releasing their autonomous tractors only within the last 10 years. John Deere released their version of an autonomous farm tractor in early 2022, stating that three dimensions had come together in the last five years to make this technology possible: 1). Significant Connectivity; 2). Increased Computational Capability; 3). Advanced Machine Learning Algorithms. This announcement is not surprising to those in Information Technology (IT). Mankind is currently in the 4th Industrial Revolution (4IR), described as the convergence of digital, physical and bio technologies driving an unrelenting acceleration of human progress. According to the July 2020 “Global Poll: Impact of the 4th Industrial Revolution” by Quadrant Strategies*, four in five senior IT decision makers worldwide say a century’s worth of technological advancements will take place in the next five years. This advancement in technology is also helping companies develop equipment for the turfgrass industry.
After investing more than 20 years of research and development, The Toro Company has also begun field testing their GeoLink Solutions Autonomous Fairway Mower at several sites across the U.S. this year. The Toro press release stated, “This type of innovation aims to alleviate the issues of labor shortages and budget constraints, while increasing productivity and getting more consistent results. With the implementation of GeoLink Solutions technology, mowing will become more time and cost effective. When operating autonomously, the built-in detection capability ensures avoidance of obstacles. After defining the mowing boundary, a variety of mowing patterns can be selected. The mowers operate consistently for perfectly straight lines, even in conditions with poor visibility, and during the cleanup pass. Even more efficiency is achieved by utilizing the entire width of the mower, reducing overlap, and self-transport between mowing areas.”
While discussing autonomous equipment, Dr. McCall was asked, “In the future, there’s a real possibility that we’ll relinquish more control of equipment to artificial intelligence. Should we trust technology to safely operate autonomous equipment driverless?” Dr. McCall had an interesting reply. He said, “There are times when things may go wrong with autonomous equipment. Generally speaking, it won’t go wrong as often as human error. Autonomous equipment has fewer accidents compared to humans operating the same equipment.” While he thinks autonomous equipment has the technology to ensure that it’s operating safely, Dr. McCall said, “It’s understandable that turfgrass managers will be nervous until they have tested and experienced this equipment for themselves, at their facilities. And this will take time.”
Another big mower advancement driven by need and provided by technology, is battery power. This was covered earlier, but since we’re already seeing manufacturers offering battery powered mowers, and in some cases hybrid mowers and other equipment for commercial use, it’s worth mentioning here.
John Deere has released the E-Cut Series Hybrid Fairway Mower with diesel engine and a 48-V, 180-amp alternator that powers brushless electric reel drive motors, requiring no additional batteries. The electric reel drive system eliminates all potential hydraulic leak points in the reel circuit. The Hybrid System offers reduced fuel consumption, noise reduction and hydraulic leak points.
The Toro Company has released battery and hybrid mowers including Toro’s Greensmaster® eTriFlex® riding greens mower, Greensmaster® e1021 Series walk greens mowers and Reelmaster® 5010-H hybrid fairway mowers. Toro also offers an electric version of the Workman® GTX utility vehicles. In addition, Toro has introduced the Revolution series of commercial-grade mowers designed for professional use, that is powered with a lithium battery system – HyperCellTM. This series includes a stand-on mower (The Grandstand®), a zero turn mower (Z Master®) and a walk behind (HD21).
GPS Sprayers and GPS Spreaders
Dr. Chase Straw says it is quite possible that within 10 years the use of GPS sprayers and spreaders will be commonplace across the turfgrass industry. This equipment has been in use in row crop agriculture for years, but only more recently in turfgrass, with most of that centered in the northern states.
GPS Sprayers (tractor or golf cart mounted) are used in the following manner: the turfgrass manager drives the spray unit over the turf area, while marking the perimeter of the area to be sprayed using the onboard computer. The computer program controlling the spray application then shows a digital map of the turf area on a monitor. The spray unit begins spraying just inside the known perimeter and continues spraying the first swath till it crosses the digital perimeter at the end of the pass. Once there, it stops spraying while the unit is turned around. The unit repeats the procedure once it crosses inside the perimeter and makes the next pass.
Some GPS sprayers are equipped with Autosteer for more precise steering. Each pass shows up as a color-coded rectangle on the monitor, indicating the width of the spread swath. Missed areas show up clearly as having no color, and overlaps show up as darker strips indicating the area had been sprayed twice. It’s just that simple. Some GPS sprayers have the added feature of Variable Rate Application (VRA). VRA comes into play when the data supporting the spray application can provide the onboard computer the coordinates of specific zone (SSMU) requirements within the field of treatment. For this to work, each nozzle on the spray boom is individually controlled by the computer, with the VRA technology controlling the rate of application to match the GIS rate-of-application map. “The precision of GPS Sprayers with VRA technology can make applications within 12 inches of target while on the move.” according to Dr. David McCall, Virginia Tech. This is quite impressive and accomplishes the goals of PA and PTM quite well.
Dr. McCall sees the future of GPS sprayers as limitless when combined with the use of various sensors and GIS technology. Dr. McCall envisions over the next 10 years having mobile ground or aerial sensors capable of collecting large amounts of data from one pass over the turf area being maintained. All the data would be analyzed using GIS technology, separating all the problems and pests (such as dry spots, brown patch, dollar spot, green kyllinga, white clover, etc.) into individual layers of information. Detailed digital maps would be created for each specific problem or pest (such as brown patch). Each specific map would contain all the GPS coordinates of each location for that particular problem or pest across the entire area being maintained. All the different layers of information would be transferred to the GPS sprayer. With technology that exists today, rather than having one tank filled with whatever product to make a single blanket application, there would be one tank filled with water, and smaller tanks carrying various pesticides and chemicals in concentrate form. The goal would be to make multiple applications during the ‘one trip’ across the area being treated. To accomplish this, as the GPS sprayer approaches coordinates identifying specific problems, or pests, water would be mixed with the appropriate fungicide, herbicide, insecticide wetting agent, etc. as the GIS information and GPS coordinates dictate. Dr. McCall thinks that’s the direction turfgrass research will take in order to make “one pass-multiple apps” possible for practical application.
As for GPS sprayers being more mainstream today, Dr. Straw has golf course superintendents telling him they have a 5-10% savings using their GPS sprayer. Others say they save 20%. Dr. Straw stated, “It’s possible to retrofit a sprayer with GPS equipment anywhere from $20K-$30K, which will pay for itself in 3 to 4 years depending on use. Turfgrass managers that first adopted this type of technology at its inception 5-7 years ago, are now ‘dialed-in’. They know the problems with making traditional spray applications and now, they couldn’t imagine not having that GPS feature, because it benefits them so much. They have peace of mind knowing the application was made on time, with the proper amount applied, overlap minimized, and everything got treated. In addition, they have the added benefit of being able to schedule and plan daily operations more precisely. More research is definitely needed, but if turfgrass managers gave this option serious consideration and more testimonies were given by those already using this technology, the use of GPS sprayers and spreaders would definitely increase.”
GPS Spreaders work the same way as GPS Sprayers. Dr. McCall stated, “GPS Spreaders will have great use in making application in site specific management zones. For example, a GPS spreader could be used on athletic fields, such as a soccer field, where additional fertilizer might be needed at the goalmouth or other areas of heavy traffic. The turfgrass manager could use the GPS spreader to deliver the fertilizer product at a set rate in just those high traffic zones.” However, Dr. McCall doesn’t believe this equipment will be precise enough to make the on and off adjustments within 12 inches of the target like GPS Sprayers.
As for VRA applications being used with GPS Spreaders, more research will be needed for that feature to be effective in turfgrass maintenance. Interestingly, Dr. Straw has just started a 3-year USGA grant to study slow-release nitrogen application on golf fairways using a GPS spreader with VRA technology. Similar research is what will be needed to make this equipment more mainstream, allowing PTM goals to be achieved.Dr. Chase Straw foresees ride-on sprayers and spreaders being equipped with GPS guidance in the future to track applications and reduce waste. He said, “I would not be surprised to see even push spreaders equipped with GPS guidance for greens, with the same benefits (reduce overlaps and prevent missed areas). If a person is guessing where they’re making application by following tire tracks, they could have overlap of 30-40% which is extremely wasteful and potentially harmful. If you can cut it to 10 to 15% that would be ideal. However, if you can get it dialed-in closer than that, you could reduce overlap to 10%.”
GPS Aerators
Using a core aerator with GPS technology would be very straightforward to operate. The process would start by first having some type of sensor take soil compaction readings using a penetrometer to measure resistance to identify soil compaction. Other sensor readings measuring soil moisture and turf health/stress could also be useful. The sensor(s) would travel over the entire surface of any turf area, to measure compaction and provide GPS coordinates of all areas having a compaction reading meeting the criteria established for aerification. A digital map of the turf area could be generated along with the square footage of the area to be aerated. As the aerator crossed any GPS coordinate identified as having compaction within the established perimeter of the turf area, the aerator would engage and start aerating. It would stop aerating once it reached the preset boundary identifying the limits of aeration. This GPS technology could be applied to tractor mounted, tow behind or walk behind units. Any aerification method from spiking, solid tines, core tines, drill and fill, air or water injection could use GPS technology with more precision.
Another possible method for collecting soil compaction measurements in the future, was mentioned by Dr. Chase Straw. He recounted conversations with a few people about how medical researchers who studied sports related injuries had outfitted players with special shoes containing sensors that measured the force and stress their feet had with the surface of the playing field when exerting the pressures of the sport. During the conversation, the researchers discussed the possibility of equipping shoes with special soles that could measure the hardness of the playing field. That information could possibly be correlated to soil compaction given enough research study. Another interesting idea that will be answered by the future!
Irrigation
With all the advancements in irrigation over the last 20 years, one might wonder what could be improved. As we’ve seen, one of the biggest advancements for irrigation in recent years has been individual head control using valve-in-head technology controlled by cell phone, tablet, or computer. This was developed for golf courses, but sports fields are using this now as well. It is quite impressive! This is really becoming more common as more manufacturers are offering this type of head, so don’t be surprised if more affordable heads of this type are developed in the future for use outside the world of golf and sports.
There’s no doubt we’ll see even more irrigation products being developed in the future and older ones being improved. When asked his thoughts about what the future holds for irrigation, Dr. Straw thinks the next big advancement for irrigation in the future may be with artificial intelligence (AI) assisted control systems. Currently, many turfgrass managers may set an irrigation controller to certain days and runtimes based on what they think the turfgrass will need, taking into account weather, work being performed or scheduled events. Some systems have the added feature of soil moisture sensors, rain gauges or weather stations that assist with limiting, or stopping, the operational runtimes of the system. However, Dr. Straw sees a much different picture of the future, with the goal being a predictive model that can establish runtimes for irrigation systems. The runtimes will be based on real time data being collected and fed into a computer once a baseline of information has been established. He said, “It’s all about setting up the model, and that’s the one thing we don’t have right now. The procedure of deciding when to irrigate could turn into machine learning with artificial intelligence using algorithms taking over for the turfgrass manager. It’s not there yet, but currently that technology is being developed at places like Texas A&M.”
Turf managers today that use the valve-in-head technology may try to measure soil moisture along with visual observations to decide when to program runtimes manually. In the future, various sensors will be used to map soil moisture and then classify irrigation heads based on the surrounding soil moisture of each individual head. Then run times can be scheduled for those heads based on plant available water and the soil conditions around each. All that individual testing can be done now, but separately, with the final decision being made by the turfgrass manager. Irrigation research is working toward taking the human element out of the decision-making process and letting artificial intelligence (AI) do that for the turfgrass manager. For AI to fully automate decision making for the turfgrass manager, the process would start by building a computer model that would reflect all the conditions (factors) such as turfgrass species, soil, and the history of inputs such as weather, irrigation, and cultural practices.
The process of building a computer model to predict irrigation runtimes involves the following factors:
- Establish an initial baseline or benchmark for soil moisture, using a variety of soil moisture sensors such as stationary, ground mobile, or aerial.
- Establish an initial plant response index (NDVI or similar) taken at the same time as the soil moisture baseline, that could measure turf quality correlated to the established soil moisture baseline. The plant response index could be collected using a sensor mounted to a drone or mowing unit.
- The next step involves the initial work of ground truthing the soil conditions and plant responses.
- From that point in time, all future data collected on soil moisture and plant response would be added to the computer model, providing a better understanding of how soil moisture influences turf quality. It’s important to note that there are a variety of sensor platforms available. Dr. David McCall, Virginia Tech, doesn’t see one sensor platform (stationary, ground mobile or aerial) necessarily leading the way, but all three working together for best result.
- Building this model will give the turfgrass manager a clear picture of the wet and dry spots across their turf area. This would be especially true using GPS/GIS technology, which could map different soil moisture conditions.
- Historically, we know water holding capacity of the soil (wet and dry spots), will not change rapidly over time. In fact, these soil conditions aren’t going to change very much unless there is major construction. So, once you have that baseline of soil characteristics, that remains stable over time. The only other thing that will influence water holding capacity will be rainfall or use of irrigation. Therefore, during the model building process, all irrigation runtimes would be entered as well as weather conditions (rainfall, temperature, wind, humidity, etc.) as factors in building this complex model.
- Any cultural practices would also be added as factors such as mowing, fertilizing, aerating, etc.
- The goal in collecting all this data over time is to establish a computer model that can run algorithms to make correlations between the different factors and then calculate the turfgrass response, so irrigation runtimes can be generated automatically – thus creating the “predictive model.” Straw stated, “It’s all about setting up the model, and that’s the one thing we don’t have right now, but we’re working in that direction.”
Conclusion
The next 10 years will be extremely exciting and possibly astonishing to witness. We may be seeing the beginning of a paradigm shift allowing the technology of machine learning and artificial intelligence to make decisions and operate equipment for the turfgrass manager. With that said, Dr. Straw had one final comment about a study that discussed all the advancements (sensor technology, machine learning, artificial intelligence, predictive models etc.) as being important. However, when it came down to the final analysis, the observations, actions, and merits of the turf manager were just as important and should not be discounted. Fortunately, many university and manufacturer researchers with “innovation imagination” are listening to turfgrass managers and developing the next generation of equipment and technology needed for the turfgrass industry to succeed in a world of growing uncertainty. The researchers are working hard to meet user demand and governmental regulations. The issues being addressed remain roughly the same: improve product quality, increase uniformity and consistency, improve playability, reduce operational cost, promote eco-friendly outcomes, increase operational maneuverability, safety, and efficiency, and improve the public perception of the turfgrass industry. The advancements will be nothing short of amazing in all phases of turfgrass equipment and technology. In total, the ultimate goal of their innovations will be the creation of a better future. And that’s good for us all!
The post Alabama Turfgrass Association – “Looking To the Future – Where Will the Turfgrass Industry Be in Ten Years” Equipment and Technology of the Future PART 3 appeared first on The Turf Zone.