The Downstream Column Podcast
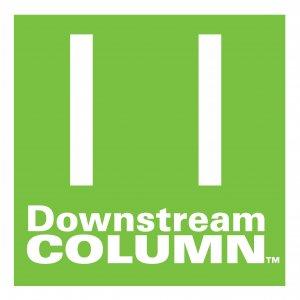
Manufacturing high concentration mAbs challenges and solutions
In this podcast, we spoke to Tom Watson, Group Leader, Product Management – Biotech Division, Gregor Kalinowski, Manager SLS Purification Consultants Europe, and Aude Iwaniec, R&D Bioprocessing Team Leader, all from Pall Corporation, about why high concentration mAbs are an increasingly important part of the biotech landscape, current manufacturing challenges and solutions, and future trends.
High concentration drugs offer benefits for patients
I began the discussion by asking why high concentration mAbs are an important topic in today’s biotech landscape. Tom explained that high concentration drugs are an important innovation because when a biotech drug can be prepared at high concentration that is administrable, it is usually self-administered in a subcutaneous mode. This method of delivery brings lifestyle benefits to patients and reduces health care costs because it negates the need for an intravenous treatment. Subcutaneous biotech drugs have been available for a while, but recently more companies are developing new drugs or formulating existing ones at high concentration.
High concentration mAb manufacturing vs. more traditional mAb production
I followed up by asking what some of the differences in terms of manufacturing high concentration mAbs versus more traditional mAb production are. Tom described that a mAb or recombinant protein for subcutaneous delivery is going to be prepared at a high concentration. Starting with the final concentration steps, it is common to have a highly viscous fluid of 10 to 30 centipoise, with a concentration of greater than 100 grams per liter and often higher than 250 grams per liter.
He went on to say that the concentration step reduces the volume of the fluid processed across the subsequent unit operations that are typical of a biotech process. What happens then is a reduction in the dosage volume, since you only need 1 to 2 milliliters of a highly concentrated biotech drug for therapeutic effect. So, typically there are small dosage volumes, or in some cases dosage volumes can be several milliliters to permit a slightly longer-term infusion of a subcutaneous drug.
However, viscosity makes processing the fluid more challenging across the unit operations including the concentration step itself, but also through filtration, mixing, freeze/thaw, formulation, and dispensing. In addition, the smaller batch volumes that correspond with the increased concentration of the drug raises the cost of the Active Pharmaceutical Ingredient (API) per unit volume and this results in more significant impact with any product loss.
Manufacturing challenges with high concentration drugs
Next, we discussed some of the main challenges that exist in manufacturing workflows for high concentration mAbs. Tom said that he repeatedly hears from customers about challenges relating to product loss in hold up volume, aggregation of the molecules, limitations with analytical equipment and sampling procedures, and destabilization of filtered fluid due to the stripping out of formulation components.
Achieving high product concentrations
I then asked Gregor about the specific challenges to achieving high product concentrations. He explained that product viscosity is increasing with increasing product concentration. So, for a given crossflow, the pressures are also increasing with increasing product concentration. He went on to say that the permeate flux is decreasing with increasing product concentrations and therefore the processing times become longer, and the number of pump passes are much higher compared to low concentration processes. This combination of extended recirculation time and the increased concentration carries a significant risk of shear related damage that may impact the product quality. Finally, the high viscosity of the final retentate pools typically results in a poor recovery from TFF systems because of limited drainability.
I followed up by asking him which solutions can be app...